Understanding Combined Wire Drawing and Wrapping Machines: Process and Applications
A wire coil drawing and wrapping machine integrates two critical processes in wire manufacturing: reducing the wire's diameter through drawing and subsequently wrapping the finished coil for protection and handling. This type of equipment is frequently utilized in industries such as electrical component manufacturing, construction, and general manufacturing where wire serves as a fundamental raw material or finished product.
The Wire Drawing Process Explained
Wire drawing involves pulling a metal rod or thicker wire through a sequence of hardened dies, each with a slightly smaller aperture than the previous one. This process achieves several key outcomes:
- Diameter Reduction: The primary goal is to decrease the wire's cross-sectional area to meet specific dimensional requirements.
- Elongation: As the diameter reduces, the wire's length increases proportionally.
- Enhanced Tensile Strength: The cold working involved in drawing increases the material's hardness and tensile strength.
- Surface Finish: Drawing can improve the surface smoothness and uniformity of the wire.
Effective drawing often requires lubrication to reduce friction between the wire and the die, minimize wear, and manage the heat generated during deformation. Integrated cooling systems are essential to maintain the wire's metallurgical properties and prevent overheating.
The Wire Wrapping Process Explained
Following the drawing stage, the wire is typically coiled onto a spool or former. The wrapping mechanism then applies a protective layer around the finished coil. Common wrapping materials include:
- Polyethylene (PE) film
- Polyvinyl Chloride (PVC) film
- Stretch wrap
- Paper or other specified materials
The wrapping process ensures the wire coil maintains its shape, protects it from environmental factors like moisture and dust during transport and storage, and facilitates easier handling. Precise tension control during both coiling and wrapping is crucial for producing neat, stable coils.
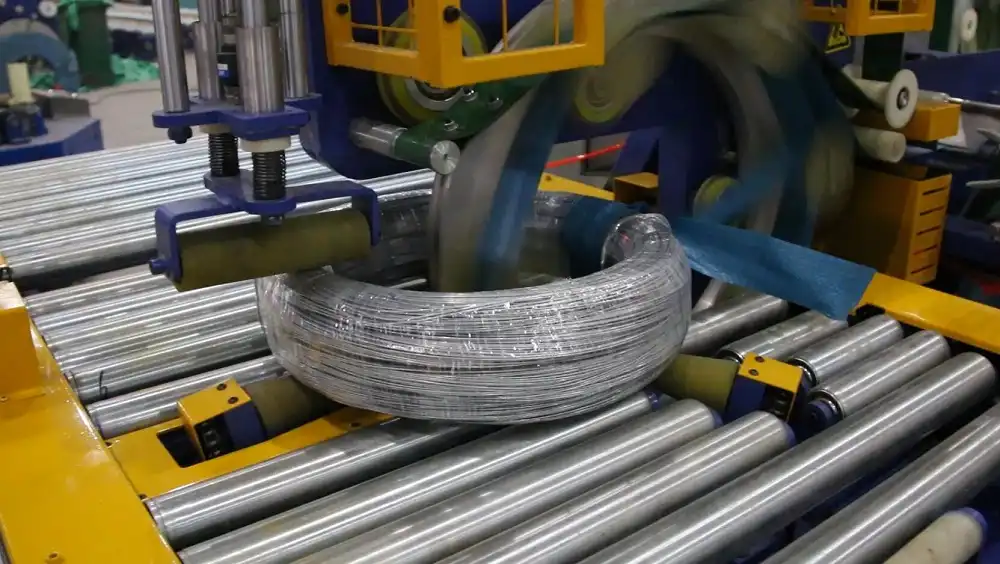
Key Components and Features
A combined wire drawing and wrapping machine typically incorporates:
- Pay-off Stand: Holds the initial wire rod or coil.
- Drawing Section: Consists of multiple capstans (driven drums) and die holders. Dies are often made from durable materials like tungsten carbide or polycrystalline diamond (PCD).
- Cooling System: Usually involves water or specialized coolants circulating around the capstans and dies.
- Tension Control System: Utilizes dancer arms or sensors to maintain consistent wire tension throughout the process.
- Coiling Unit: Forms the drawn wire into coils of specified dimensions.
- Wrapping Unit: Applies the protective wrapping material around the finished coil.
- Control System: Typically PLC-based with an HMI (Human-Machine Interface) touchscreen for setting parameters, monitoring operation, and diagnostics.
- Safety Features: Includes emergency stops, protective guarding, and sensors to detect wire breaks or other malfunctions.
Technical Parameters (Example Configuration)
Please Note: The parameters listed below are illustrative and may not precisely match the equipment shown in the video. For exact specifications tailored to your application, direct consultation is recommended.
- Machine Type: Combined Wire Drawing and Wrapping Machine
- Input Material Diameter: Up to 12mm
- Final Wire Diameter Range: 0.5mm to 5mm
- Maximum Drawing Speed: Up to 15 m/s (variable based on material and reduction)
- Common Wrapping Materials: Polyethylene, PVC, Stretch Film
- Typical Power Requirements: 410V, 50Hz, 3-Phase (can vary)
- Approximate Machine Dimensions: Length: 8000mm; Width: 3000mm; Height: 2200mm (footprint varies significantly by model)
- Standard Cooling System: Water-cooled capstans and dies
- Control Interface: PLC controlled with digital touchscreen
- Standard Safety Features: Auto-stop sensors, interlocked protective fencing
steel wire film wrapper4 Applications Across Industries
Combined wire drawing and wrapping machines are vital in various sectors:
1. Construction (Rebar and Structural Wire)
These machines produce steel wires used for reinforcing concrete (rebar) and other structural applications. Precise diameter control ensures compliance with building standards (e.g., ASTM standards), while wrapping protects the wire from corrosion and damage during transport and on the job site, preserving structural integrity.
2. Automotive (Wiring Harnesses and Components)
The automotive industry relies heavily on accurately sized copper and aluminum wires for complex electrical systems. This equipment efficiently produces and protects these wires, ensuring reliable conductivity and resistance to environmental factors within the vehicle. Consistent wire quality is critical for vehicle safety and performance.
3. Electronics (Fine Gauge and Specialty Wires)
Manufacturing electronic devices requires fine gauge wires for internal connections in appliances, computers, and communication hardware. The precise drawing capabilities produce wires with tight tolerances, while careful wrapping protects these often delicate wires from mechanical stress, ensuring the functionality and longevity of electronic components.
Benefits of Integrated Systems
Combining the drawing and wrapping processes into a single machine offers several advantages:
- Increased Efficiency: Streamlines the workflow by eliminating the need to transfer wire between separate machines.
- Reduced Handling: Minimizes manual intervention, lowering the risk of damage to the wire surface.
- Consistent Quality: Integrated controls ensure uniformity from drawing through to final packaging.
- Space Savings: Occupies a smaller footprint compared to two distinct machines.
- Improved Process Control: Centralized control allows for better synchronization between drawing speed, coiling, and wrapping.
Considerations for Selection and Operation
When selecting or operating a combined wire drawing and wrapping machine, factors to consider include:
- Material Type: The machine must be suitable for the specific metal or alloy being processed (e.g., steel, copper, aluminum).
- Diameter Range: Ensure the machine covers the required input and output wire diameters.
- Speed and Throughput: Match the machine's production capacity to operational needs.
- Level of Automation: Consider the desired degree of automation for setup, operation, and monitoring.
- Maintenance: Assess the ease of access for routine maintenance of dies, lubrication systems, and wrapping components.
Conclusion
Combined wire drawing and wrapping machines represent a significant advancement in wire manufacturing technology. By integrating diameter reduction and protective packaging into a continuous process, they offer enhanced efficiency, consistent quality, and streamlined production for essential wire products used across a multitude of critical industries. Understanding their operation and capabilities is key for manufacturers seeking to optimize their wire processing workflows.