Enhancing Workshop Efficiency: The Role of Wire Coil Compactors in Metal Fabrication
Managing wire coils effectively is a common challenge in metal fabrication and related industries. Disorganized or loose coils can consume valuable floor space, hinder workflow, and even pose safety risks. Wire coil compactors are specialized machines designed to address these issues by efficiently compressing and bundling wire coils for easier storage, handling, and transportation. Understanding the operational benefits of this equipment can help businesses optimize their material handling processes.
Key Benefits of Utilizing Wire Coil Compactors
Implementing a wire coil compactor offers several tangible advantages for operations dealing with significant volumes of wire.
Improved Organization and Space Optimization
Loose wire coils naturally occupy a large footprint. A wire coil compactor significantly reduces the volume of stored wire by compressing coils into dense, uniform bundles. This densification allows for more efficient use of warehouse or shop floor space, potentially freeing up areas for production or other critical activities. Furthermore, compacted coils are easier to stack, inventory, and retrieve, leading to better overall organization and workflow efficiency.
Reduced Material Handling and Transportation Costs
The logistics of moving wire, whether within a facility or shipping to customers or recycling centers, involves costs related to space and weight. Compacted coils occupy less volume, meaning more material can fit onto a pallet, into a truck, or within a shipping container. This can lead to fewer required transport runs, reducing fuel consumption, labor hours associated with loading/unloading, and overall shipping expenses. Efficient wire coil handling translates directly to cost savings.

Enhanced Workplace Safety
Unsecured wire coils present potential hazards. They can unravel unexpectedly, create tripping hazards, or shift unstablely during movement. Compacting wire into tight, secured bundles minimizes these risks. Properly compacted coils are more stable, easier to handle with forklifts or other equipment, and less likely to cause accidents, contributing to a safer working environment which aligns with OSHA guidelines and best practices. (Consider adding an external link to relevant OSHA guidelines here if appropriate).
Streamlined Scrap Wire Management
For businesses generating scrap wire, compactors play a crucial role in preparing this material for recycling. Compacted scrap wire is denser and easier for recyclers to handle and process, potentially increasing its value. Efficient scrap management is not only cost-effective but also supports environmental sustainability efforts.
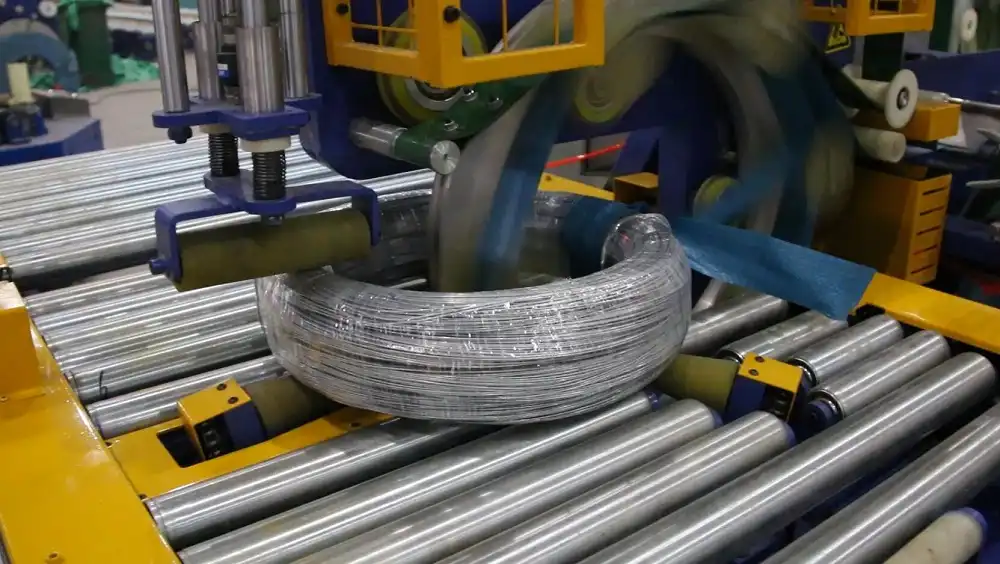
Evaluating the Investment
While the initial acquisition of a wire coil compactor represents a capital expenditure, the return on investment (ROI) should be evaluated based on long-term operational gains. Factors contributing to ROI include:
- Space Savings: Quantifying the value of reclaimed floor space.
- Labor Efficiency: Reduced time spent handling, organizing, and moving wire.
- Transportation Cost Reduction: Lower freight and shipping expenses.
- Safety Improvements: Reduced costs associated with workplace accidents.
- Scrap Value: Potentially higher returns from recycled materials.
Different types of compactors (e.g., hydraulic, pneumatic) offer varying levels of force and throughput. Selecting the appropriate machine depends on the volume, type, and diameter of the wire being processed. (Consider adding an internal link to an article comparing compactor types if available).
Conclusion
In conclusion, a wire coil compactor is a practical tool for any operation managing significant quantities of wire coils or scrap wire. By improving spatial organization, reducing transportation and handling costs, enhancing workplace safety, and streamlining scrap processing, these machines contribute directly to operational efficiency and profitability. Evaluating the specific needs of your facility against the capabilities of available compacting equipment can reveal significant opportunities for process improvement in wire coil management.
Further information on wire coil compactor and strapping machine specifications can be found here: http://www.fhopepack.com/Wire-coil-compactor-strapping_machine.html