
Why Automatic Steel Coil Palletizing Is Safer Than Palletizing Manually By Hand
Efficient palletizing is crucial for packaging lines. Companies use manual or automatic methods to stack steel coils and other products onto pallets. In manual palletizing, workers handle coils by hand with conveyors or lift tables. Automatic palletizers instead rely on palletizer machines.
Automatic palletizers offer clear safety advantages. Steel coils can weigh tons, presenting significant ergonomic hazards if lifted manually. However, automatic palletizers equipped with mechanical forks, vacuum pads or magnetic grippers precisely arrange coils.
These technologies allow palletizers to safely grasp coils regardless of size or weight, minimizing risk of injury from heavy lifting.
By automating coil palletizing tasks, workers are removed from potential dangers. Automatic processes contain hazards from moving or dropped coils within safety enclosures. Integrated controls ensure motions follow protocols, preventing accidents from human errors. Consistent, high-speed palletizing alleviates risks compared to fatigue-prone manual labor.
Automatic palletizing creates a safer working environment for handling heavy steel coils at scale. The benefits of robotics outweigh continuing manual methods for operations handling bulky coil packaging.
Remove Operators From Potential Dangers
Automated palletizers significantly reduce the risk to workers by keeping them away from potential safety hazards associated with manual palletizing. Handling products manually exposes workers to various dangers, including injuries from dropped cases, bumps, scrapes, broken products, sharp corners, and mishandled tools. These risks can result in cuts, puncture wounds, and other workplace accidents, leading to potential injuries.
In contrast, automatic palletizers ensure employee safety by incorporating features like safety enclosures and controlled entry systems that contain hazards related to gravity and voltage. By keeping workers out of harm's way, these machines optimize safety in the workplace.
When it comes to steel coil palletizing, using machinery offers numerous advantages over manual handling. Not only are the mechanical costs lower, but it is also safer. With machinery, handling a pallet may only require one person, whereas manual handling typically necessitates the effort of two individuals.
Additionally, automated equipment can be integrated into packaging lines, enabling a single operator to manage a more significant number of pallet packaging processes efficiently.
Reduced Physical Strain
Automated palletizing systems offer a solution to eliminate the physical strain associated with manual labor. Heavy lifting and repetitive movements involved in manual palletizing can lead to back strain and various injuries over time, impacting worker health and productivity.
These physical stresses can result in increased insurance costs, higher turnover rates, and decreased efficiency in the long run.
Automatic palletizing, especially in the context of steel coil handling, provides a safer alternative by transferring the heavy lifting tasks to machines capable of handling them without the risk of injury.
These mechanical systems operate efficiently in harsh environments, tirelessly and with high stability. In contrast, manual labor may lead to fatigue and discomfort, necessitating rest breaks or job rotation strategies to mitigate the risk of injuries due to overexertion.
By leveraging automated palletizing technology for steel coils, companies can ensure a consistent and safe handling process that minimizes physical strain on workers, enhances operational efficiency, and reduces the likelihood of workplace injuries associated with manual labor.
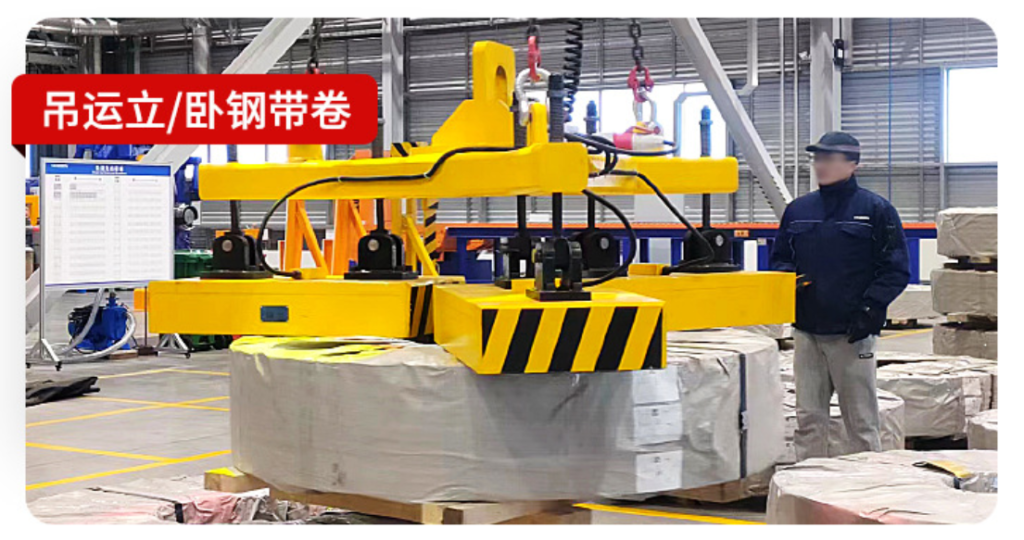
Packing Integrity Enhance Safety
Consistent and accurate packing processes are crucial for eliminating accidents and ensuring workplace safety. Manual packing can be prone to errors, which may result in unstable pallets, falling products, and safety hazards.
Automatic palletizers, such as those offered by FHOPE, provide a reliable solution by consistently creating stable pallets that reduce the risk of tipping or product spills during transportation within your facility.
FHOPE's palletizers incorporate concurrent stretch wrapping technology, which stabilizes and secures the load during the palletizing process, ensuring that each pallet is securely wrapped and safe.
In the context of steel coil palletizing, the impact of using automated machinery is significant. Beyond sustainable cost reductions, these systems contribute to the long-term strategic planning and benefits of a company.
The consistent and stable packaging achieved through automated palletizing ensures the reliable handling of steel coil pallets, enriching the diversity of orders and enhancing operational efficiency.
By investing in FHOPE's automatic palletizers for steel coils, businesses can improve safety, streamline packaging operations, and enhance overall workflow efficiency.
Contact FHOPE today to explore the right solution that aligns with your business goals, improves productivity, and delivers consistent results for your facility.
4 types Coil stacking and palletizing solution for the packing line.
In modern industrial packing lines, four primary technologies are used for coil stacking and palletizing: mechanical types, magnet lifters, vacuum lifters, and robotic systems.
Each method offers unique advantages tailored to handle different types of coils and weights, ranging from lightweight aluminum and copper coils to heavier steel coils up to 20 tons, ensuring efficiency, safety, and adaptability in various operational environments.
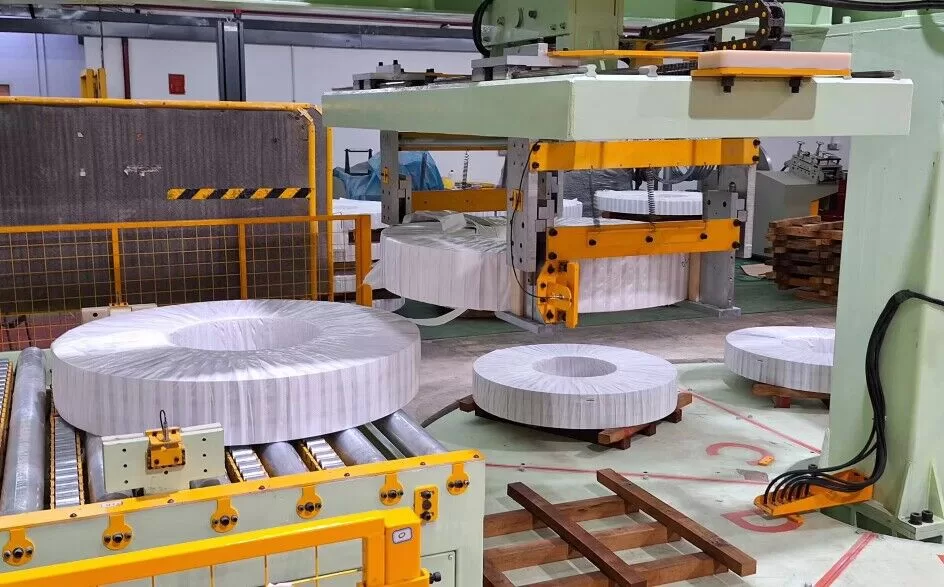
- Mechanical Type
The mechanical type is the most popular coil stacking method used in packing lines. It uses fork arms to securely hold and lift the coils from the bottom, ensuring stability during handling. Additionally, this system features a center expanding holder that grips the coil from the inside diameter, making it especially effective for lighter coils, and allows stacking without the use of timber. The mechanical system can handle coils up to 10 tons and is noted for its safety and reliability, making it a versatile choice for various industrial needs.
- Magnet Lifter
Magnet lifters utilize electric magnet suckers to handle coils, providing a secure grip without physical contact. This system includes power shutdown protection to ensure safety during unexpected power failures. Magnet lifters can handle steel coils up to 20 tons and are capable of stacking with or without timber. The process ensures minimal risk of magnetizing the coil, with efficient demagnetization after handling, thus maintaining the quality and integrity of the coils throughout
the process.
- Vacuum Lifter
Vacuum lifters are ideal for handling light coils, typically made from materials like copper or aluminum, with a maximum load capacity of 1000 kg. These lifters require that the coil surfaces be smooth and neat to ensure a strong vacuum grip. The vacuum technology provides a gentle touch, reducing the risk of damaging delicate materials. This method is particularly favored for its precision and the ability to maintain the aesthetic quality of sensitive surfaces.
- Robot
Robotic systems offer an advanced and automated solution for coil stacking, particularly suitable for light coils weighing around 1 ton. Robots are equipped with specialized work fixtures designed explicitly for coil handling, ensuring efficiency and precision in stacking operations. This method is highly adaptable and can be programmed for various tasks, making it an excellent choice for facilities aiming to increase automation and reduce labor-intensive processes. The robotic system also enhances safety by reducing human involvement in potentially hazardous tasks.
