Optimizing Coil Handling: Selecting the Best Steel Coil Upender for Your Metal Processing Plant
Introduction to Coil Handling in Metal Processing
In the demanding environment of metal processing, maximizing operational efficiency and ensuring workplace safety are non-negotiable priorities. A key piece of equipment enabling both is the steel coil upender, also known as a coil tilter. These robust machines are engineered to safely rotate heavy steel coils between horizontal and vertical orientations (eye-to-sky and eye-to-wall). This facilitates easier storage, transport, and integration into processing lines like slitting or stamping. Given the variety of upenders available, selecting the optimal model for a specific metal processing plant requires careful consideration of capacity, automation, safety protocols, and application versatility. This guide provides insights into choosing the right coil handling equipment.
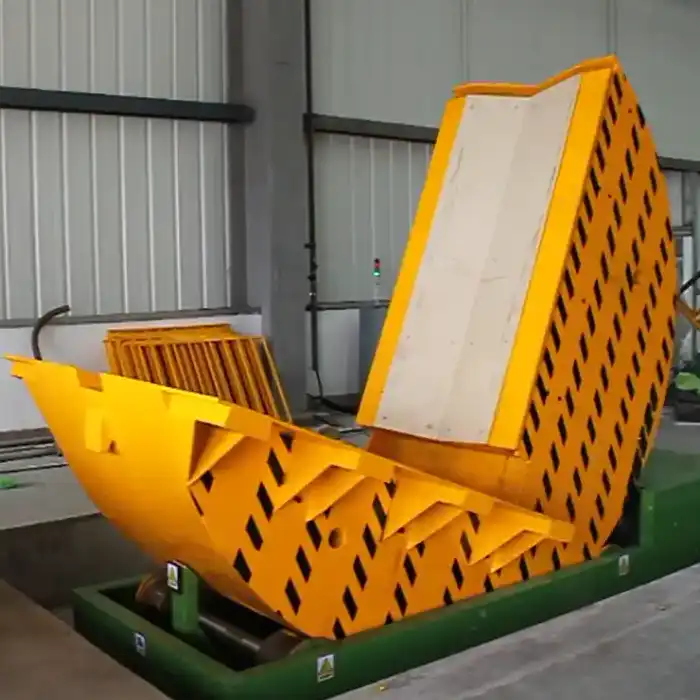
Understanding the Function and Importance of Steel Coil Upenders
A steel coil upender is fundamentally a material handling device designed to reorient large, heavy coils of metal (primarily steel, but also aluminum, copper, etc.). In metal processing plants, coils arrive, are stored, and are fed into machinery in specific orientations. Manually repositioning these coils is impractical and hazardous. An upender automates this process, ensuring coils are handled:
- Safely: Minimizing risks to personnel associated with handling multi-ton loads.
- Efficiently: Speeding up the transition between storage, transport (e.g., by crane or forklift), and processing.
- Without Damage: Preventing deformation, telescoping, or edge damage to valuable coil stock.
Choosing an upender that matches the plant's specific workflow and coil characteristics is crucial for maintaining productivity and safety standards.
Key Factors for Selecting the Right Steel Coil Upender
Evaluating potential steel coil upenders involves assessing several critical parameters to ensure the chosen equipment meets the operational demands of your metal processing plant.
1. Load Capacity and Coil Dimensions
- Parameter: Maximum Load Weight
- Consideration: The primary specification is the upender's maximum load capacity. This must exceed the weight of the heaviest coils processed in your facility. Capacities typically range widely, often from 1 ton to over 50 tons. Always select a capacity rating that includes a safety margin above your maximum coil weight.
- Parameter: Coil Size Compatibility
- Consideration: Beyond weight, consider the physical dimensions:
- Maximum Coil Outer Diameter (OD)
- Minimum Coil Inner Diameter (ID)
- Maximum Coil Width
The upender's platform or cradle must securely accommodate the full range of coil sizes handled in your plant.
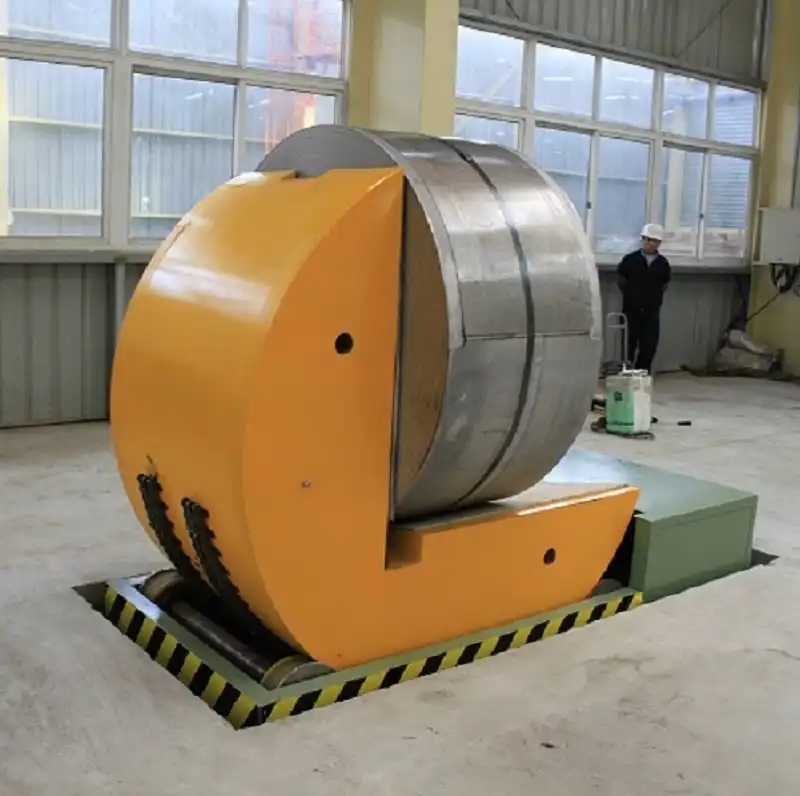
2. Drive System: Mechanical vs. Hydraulic
- Type: Mechanical Upenders
- Mechanism: Typically use electromechanical drives (motors, gearboxes, chains, or screw jacks).
- Pros: Often offer precise control, potentially lower maintenance complexity in some designs.
- Cons: May have limitations on very high load capacities compared to hydraulics; moving parts require regular inspection and lubrication.
- Type: Hydraulic Upenders
- Mechanism: Utilize hydraulic cylinders powered by a hydraulic power unit (HPU).
- Pros: Excellent for heavy loads, provide smooth and powerful motion, inherently robust.
- Cons: Require hydraulic fluid maintenance, potential for leaks if not properly maintained.
- Consideration: The choice depends on load requirements, environmental factors, maintenance capabilities, and budget. Hydraulic systems are very common for heavy-duty steel coil handling.
3. Rotation Angle and Speed
- Parameter: Rotation Angle
- Consideration: Most standard upenders rotate 90 degrees (horizontal to vertical or vice versa). Some applications might require 180-degree rotation (inverting the coil). Ensure the model provides the necessary angle for your process.
- Parameter: Rotation Speed
- Consideration: Cycle time is critical for efficiency. The upender's rotation speed should align with your production tempo. Faster speeds improve throughput but must be balanced with smooth, controlled movement to prevent coil damage. Typical rotation cycles range from 30 seconds to several minutes depending on size and type.
4. Automation Level and Control Systems
- Level: Manual/Semi-Automatic
- Control: Pendant controls or push-button stations requiring direct operator interaction. Suitable for lower volume operations.
- Level: Fully Automated
- Control: Integrated with plant control systems (PLCs), potentially using sensors for automatic loading/unloading sequences. Often includes remote control options.
- Consideration: High-volume metal processing plants benefit significantly from fully automated upenders. Automation enhances speed, consistency, reduces labor dependency for this task, and allows operators to manage the process from a safe distance.
5. Safety Features and Compliance
Safety is paramount when handling heavy coils. Look for upenders equipped with comprehensive safety features:
Essential Features:
- Emergency stop buttons (easily accessible)
- Overload protection systems
- Stable base frame and secure clamping/support mechanisms
- Limit switches to control rotation range
Enhanced Features:
- Safety barriers or light curtains to prevent personnel entry during operation
- Sensors to detect proper coil positioning before rotation
- Audible and visual operating alarms
- Controlled descent/fail-safe mechanisms in case of power loss (especially important for hydraulic systems)
Compliance: Ensure the equipment meets relevant safety standards (e.g., ANSI, CE markings). Consult resources like OSHA guidelines on material handling for broader context.
rotating coil upender 6. Footprint and Integration
Parameter: Machine Dimensions & Layout
Consideration: Evaluate the upender's physical size and required operating clearance. Choose a model that fits efficiently within your plant layout. Options include:
- Floor-mounted: Standard configuration.
- Pit-mounted: Allows the loading platform to be flush with the floor, potentially simplifying loading/unloading with certain equipment.
Integration: Consider how the upender integrates with existing material flow – crane access, forklift paths, conveyor systems, or AGVs (Automated Guided Vehicles). Some upenders feature modular designs for easier integration.
7. Durability, Construction, and Maintenance
- Construction: Look for robust, heavy-duty steel construction (reinforced frames, high-strength welds) designed for industrial environments. The quality of components (motors, gearboxes, bearings, hydraulic cylinders) dictates longevity.
- Maintenance: Assess the maintenance requirements. Features like centralized lubrication points or easy access panels simplify upkeep. Consider the availability of spare parts and manufacturer support. A durable, low-maintenance upender minimizes downtime and total cost of ownership.
8. Versatility for Different Materials and Sizes
- Adaptability: If your plant handles coils of varying diameters, widths, or even different materials (e.g., steel and aluminum), select an upender with features like:
- Adjustable V-cradles or platforms
- Conveyorized platforms for easier loading/unloading
- Suitable clamping pressure that secures the coil without damaging softer materials.
- Benefit: A versatile upender provides operational flexibility and future-proofs your investment against changing production needs.
Common Types of Steel Coil Upenders in Metal Processing
While specific features vary, upenders generally fall into categories based on drive and design:
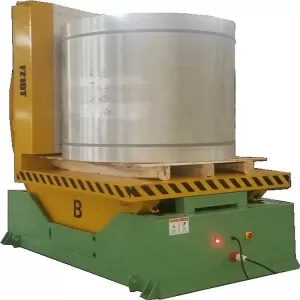
1. Heavy-Duty Hydraulic Upenders
- Characteristics: Typically designed for the highest load capacities (often 10 tons to 50+ tons). Utilize powerful hydraulic cylinders for rotation. Feature robust steel frames.
- Best For: Large-scale metal processing plants, steel service centers, and applications involving very heavy steel coils requiring reliable, powerful tilting. Often incorporate advanced automation and safety features.
2. Mechanical Upenders
- Characteristics: Employ electromechanical drive systems. Can range from light-duty to heavy-duty, though often dominant in lower to mid-range capacities. Known for potentially precise positioning.
- Best For: Applications where hydraulic fluids are undesirable, or where specific control precision offered by screw jacks or geared motors is preferred. Maintenance involves mechanical components.
3. Floor-Level vs. Pit-Mounted Upenders
- Floor-Level: Sits directly on the plant floor. Easiest installation but requires lifting coils onto the platform.
- Pit-Mounted: Installed in a floor recess, allowing the platform to be level with the surrounding floor. Facilitates roll-on/roll-off loading with floor conveyors or specific types of transfer cars. Requires civil work for installation.
4. Specialized Upenders (e.g., Coil Upender with Pallet Changing)
- Characteristics: Some upenders integrate additional functions. For instance, a pallet changer upender might tilt a coil and simultaneously allow for switching it from one pallet type to another (e.g., wooden to steel). These often operate at a 95-degree or 180-degree angle.
- Best For: Operations requiring integrated pallet handling or specific tilting angles beyond the standard 90 degrees. Suitable for lighter loads (e.g., up to 1-5 tons) where pallet management is part of the coil handling process.
Benefits of Optimizing Coil Handling with the Right Upender
Investing in the most suitable steel coil upender for your metal processing plant yields significant advantages:
- Enhanced Safety: Dramatically reduces risks associated with manual or inadequate coil handling methods, minimizing potential injuries and accidents.
- Increased Operational Efficiency: Streamlines the workflow by automating or simplifying coil repositioning, leading to faster cycle times, reduced bottlenecks, and less equipment downtime.
- Reduced Product Damage: Ensures smooth, controlled rotation, preventing costly damage to coils (e.g., edge damage, telescoping) that can occur with improper handling.
- Lower Labor Costs: Automation reduces the need for manual labor in the hazardous task of coil tilting, freeing up personnel for other value-added activities.
- Improved Ergonomics: Eliminates strenuous physical tasks associated with attempting to manually manipulate or assist in positioning heavy coils.
- Optimized Floor Space: While the upender itself occupies space, efficient handling can lead to better overall floor space utilization by streamlining material flow.
- Process Versatility: The right upender allows the plant to handle a wider range of coil sizes and potentially materials, adapting more easily to customer orders or production changes.
steel coil upender Conclusion: Making the Informed Choice
Choosing the best steel coil upender is a critical decision for any metal processing plant. It directly impacts safety, efficiency, product quality, and profitability. By carefully evaluating factors such as load capacity, dimensions, drive type (mechanical vs. hydraulic), rotation requirements, automation level, safety features, footprint, durability, and versatility, plant managers can select equipment that precisely matches their operational needs. Whether it's a heavy-duty hydraulic model for large coils or a specialized upender for integrated tasks, the right investment will significantly enhance coil handling capabilities, contributing to a safer, more productive, and cost-effective operation for years to come.