I see many people struggle with flipping different coil materials. They worry about safety or damage. This causes hesitation and higher handling costs. A coil upender addresses these pains.
A coil upender can handle a range of materials, including ferrous metals, non-ferrous metals, and even coated coils. The key is to match the coil’s weight, size, and physical characteristics with the upender’s capacity. Operators should check load limits and adjust settings for each material type.
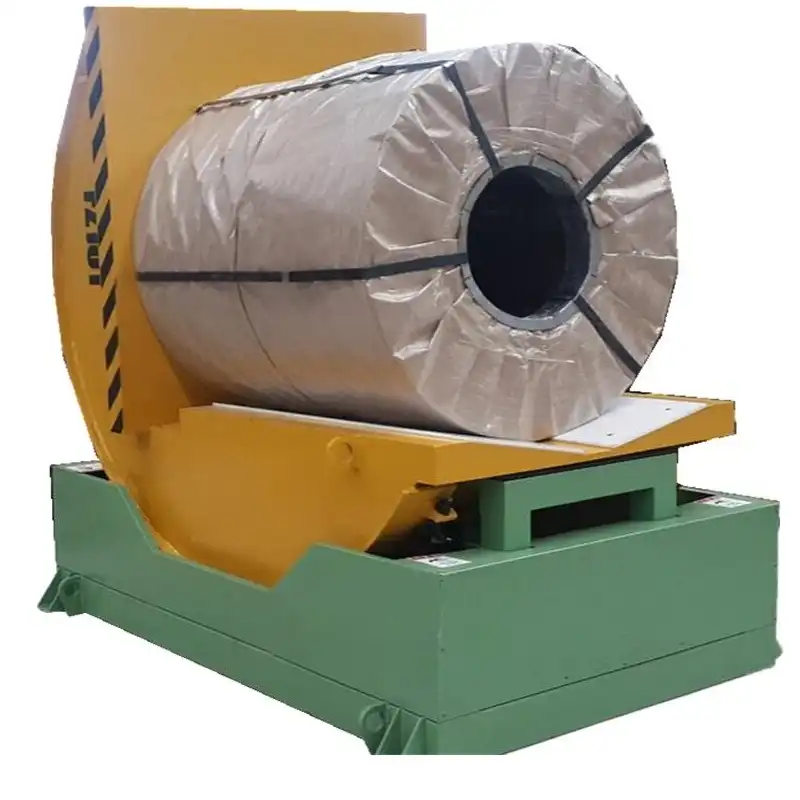
I know you want to optimize productivity and ensure smooth workflows. Let us see how coil upenders support various materials so your plant can stay safe and efficient.
Can Steel Coils Be Used with a Coil Upender?
I see many people question if steel coils are too heavy for a coil upender. They get worried about structural stress or mechanical breakdowns. This leads them to avoid upgrades and stick to manual flipping.
Yes, a coil upender is ideal for steel coils. It manages heavy weights with a strong frame and powered rotation. Steel coils rest on a stable cradle that prevents shifting or drops during tilting. The motor, hydraulics, and clamps work together to ensure safe flipping for steel coils.
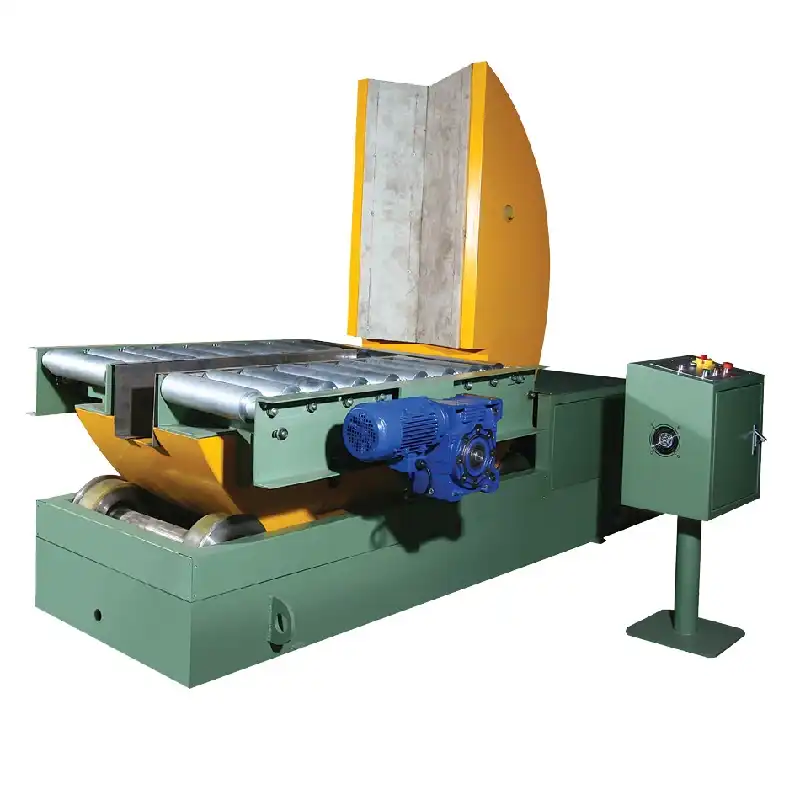
I want to share details on how steel coils work well with an upender. If you handle steel coils daily, keep reading.
The Key Factors in Steel Coil Upending
I want to break down why steel coils fit coil upenders so well. First, steel coils are often dense and heavy. A coil upender typically has a robust frame with thick steel components. That structure resists bending or twisting under large loads. If you compare the load rating of an upender to the typical weight of a steel coil, you will see a comfortable margin of safety.
Second, the cradle design matters. Many upenders include adjustable support arms or V-shaped cradles. These hold steel coils without letting them roll. The motor or hydraulic system provides a steady rotation. As the cradle tilts, the coil stays in place. You do not need extra manpower. This reduces back injuries or coil mishaps.
Third, there is the factor of friction. A steel coil might have an oiled surface or rust-prevention layer. That can make the coil slippery. I see coil upenders use textured grips or rubber-lined edges on the cradle. This friction keeps the coil from sliding. Operators can upend the coil without fear of it skidding off. If the upender lacks these grips, you can add friction pads to improve stability.
Fourth, steel coils sometimes come in massive diameters. The upender must accommodate that diameter in its flipping arc. Factories often measure the widest coil they expect to handle, then pick an upender with enough clearance. This ensures the coil does not bump into any guards or components. If the upender is too small, the coil could jam midway, risking damage. Checking coil size against machine specs is vital.
Fifth, many steel coils have a tension that can unwind if not secured. Some coil upenders offer optional banding or clamp systems to hold the coil’s outer wrap. That prevents unwinding during the tilt. In my experience, this is helpful for narrower strips or tightly wound steel. By stabilizing the coil’s outer layer, you cut down on the risk of tangles or surface damage.
Below is a table summarizing key points for using a coil upender with steel coils:
Consideration | Why It Matters | Suggested Approach |
---|---|---|
Load Capacity | Steel coils can be extremely heavy | Pick an upender with matching tonnage |
Cradle Design | Prevents coil rolling or slippage | Use V-shaped or adjustable cradle |
Friction Grips | Oily surfaces can slip easily | Add rubber pads or textured surfaces |
Diameter Clearance | Large coils need enough room | Check max coil diameter vs upender specs |
Coil Stabilization | Outer layer might unwind | Use optional clamps or banding devices |
I recall when I introduced a new coil upender for steel. Operators were skeptical at first. They worried the coil might not stay put. But after a few trials, they saw how stable the cradle was. The upender handled the weight with no strain. That saved time that we had spent moving coils by overhead crane. It also improved safety and speed. Steel coils are indeed a perfect match for a well-designed upender.
I also suggest routine checks on the upender. Heavy steel coils can place consistent stress on bearings, gears, or hydraulic cylinders. Lubricate them frequently. Inspect for signs of fatigue or misalignment. If you see unusual vibrations or noises, investigate right away. A well-maintained machine will keep flipping steel coils for many years.
Lastly, I note that steel coil edges can be sharp. The upender’s cradle surfaces should resist cuts or scuffing. Some upenders have special guards that prevent contact with operators. Combined with proper safety training, these guards reduce the risk of hand injuries. This synergy of mechanical design and operator skill ensures steel coil flipping is both efficient and safe.
Are Non-Ferrous Metals Safe for Coil Upending?
I see people doubt if lighter metals, like aluminum or copper, need special treatment. They fear that an upender designed for steel might be too rough for softer metals. This causes hesitation in adopting automation.
Yes, coil upenders handle non-ferrous metals well. The same stability and rotation controls apply. You may add softer liners or reduce clamp force for delicate coils. An upender’s adjustable settings allow safe flipping of aluminum, copper, and other non-ferrous coils.
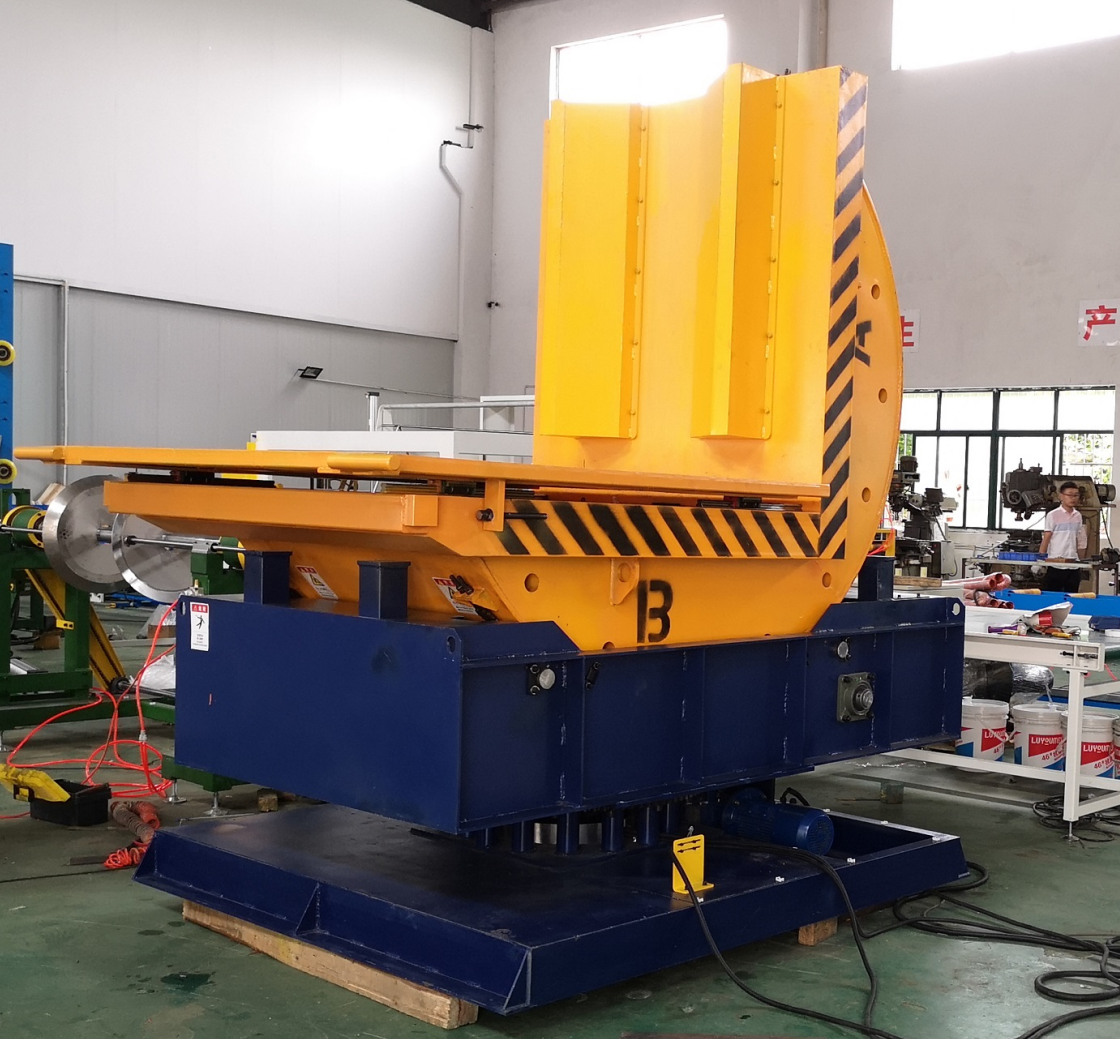
I think it is crucial to explore the subtle differences. Keep reading to see how an upender manages non-ferrous metal coils.
Special Adjustments for Non-Ferrous Coils
I want to examine the considerations for flipping non-ferrous coils. Aluminum, copper, or brass coils can be lighter, but they often need gentler handling. The surfaces might be more prone to scratches or dents. Some coils have protective coatings or finished surfaces that must remain flawless for further processing. That means the cradle should have gentle contact areas. Many upenders offer padded surfaces or adjustable clamp force to avoid pressing too hard on the coil edges.
Next, non-ferrous coils can be bigger in diameter while weighing less. Aluminum is less dense than steel, so the coil might be physically larger. This shift in geometry affects how the coil sits in the cradle. The upender should have enough space for the coil’s width and diameter. Even if the weight is within capacity, the machine must accommodate the coil’s footprint. This is important in a smaller facility or tight production area.
I also see that non-ferrous coils may require less torque to rotate because they are lighter. That can let you run the upender at a faster tilt if needed. However, I suggest keeping a moderate speed for safety and consistent flipping. Even if the coil is lighter, an abrupt tilt can cause the coil to shift. A smooth, controlled motion is best for delicate surfaces.
Some upenders allow you to program clamp pressure and rotation angle. If you handle a variety of coils, from steel to aluminum, you can store presets for each type. That ensures the machine automatically adjusts clamp force or speed for each batch of coils. This adaptability is a big advantage in modern plants that handle multiple materials.
Another point is that non-ferrous metals can still get surface corrosion. Aluminum can develop oxide layers. Copper can tarnish. If the coil is stored for long, you might want to keep it wrapped until the flipping process begins. The coil upender can integrate with a packaging line that removes outer wrap before flipping, or re-wraps the coil after. That synergy maintains product integrity throughout the supply chain.
Below is a table comparing factors for non-ferrous coils vs. steel coils:
Aspect | Non-Ferrous Coil | Steel Coil |
---|---|---|
Weight to Size Ratio | Typically lighter, bigger | Heavier, more compact |
Surface Sensitivity | Higher chance of scratches | Usually more durable |
Cradle Padding | Recommended | Optional |
Clamp Force Settings | Lower force needed | Higher force for stability |
Rotation Speed | Often can be faster | Usually moderate |
Some people ask if they need a special upender just for aluminum. In most cases, a general coil upender with adjustable features works fine. The key is to set the parameters to suit the material. If you are flipping a soft coil, reduce clamp pressure and insert protective pads on contact points. If you are flipping a heavy steel coil next, revert to the steel preset. The best machine is flexible. That lowers the need for multiple upenders on the floor.
I recall when I first handled copper coils on an upender designed for steel. The operator worried about scuffing the edges. We swapped the cradle liners with softer rubber and turned down the clamp force. The coil flipped smoothly. No scratches or dents. That convinced me that a single upender can handle many coil types with minor adjustments. It saved money and floor space, which is vital for any efficient plant.
Non-ferrous coils also vary in shape. Some might be narrower, others wider. You can add lateral guides on the cradle to position the coil. This alignment helps the coil remain stable during rotation. As with steel, I suggest frequent maintenance. Check for wear in the pivot points, hydraulic lines, or motor gears. Even if the coil is lighter, repeated movements cause mechanical stress. Regular inspections and lubrication keep the upender running smoothly, no matter the material.
Does a Coil Upender Handle Coated or Wrapped Materials?
I see many ask if protective wraps or coatings affect upending. They worry that friction changes or that the machine might tear the wrap. This causes them to skip using a coil upender and revert to manual handling.
A coil upender can flip coated or wrapped coils without harm. Operators simply adjust cradle grips, ensure the wrap is secured, and manage tilt speeds. The upender’s clamp and rotation control prevent rips or slippage. This makes it safer for pre-coated or film-wrapped coils.
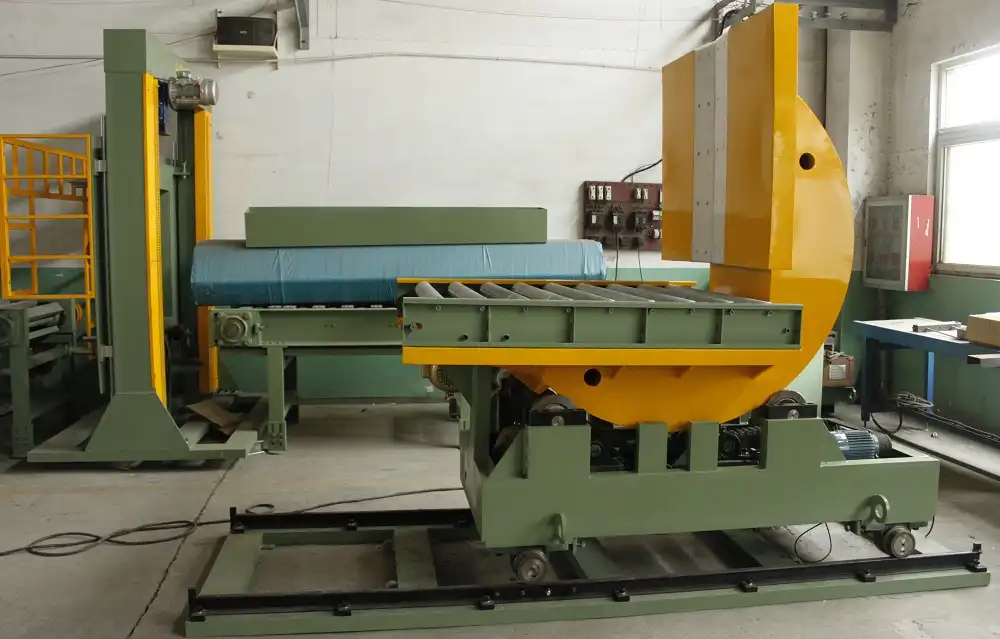
"coated or wrapped coils on upender")
I want to show how you can handle these specialty coils. Keep reading for tips on preventing damage to packaging or protective layers.
Best Practices for Coated or Wrapped Coils
I want to explore the challenges with coated or wrapped coils. These might be galvannealed steel with a delicate finish, or they could be plastic-wrapped aluminum. The first concern is surface friction. Some coatings, like paint or laminate, are smooth. The coil could slip if the cradle does not have enough grip. Many upenders have rubber pads, adjustable brackets, or friction liners. That helps keep the coil in place even if the surface is slick.
Second, pre-wrapped coils often have an outer film or paper to protect against scratches. When flipping, the wrap can shift if the coil is not clamped securely. I recommend checking that the wrap is tight around the coil. If it is loose or not taped well, the upender might cause it to bunch up or tear. By re-securing any loose edges or seams, you lower the chance of wrap damage.
Third, the machine’s rotation speed matters. If you rotate too quickly, the wrap experiences sudden stress at contact points. A slower tilt can reduce tension on the packaging. Most upenders let you set tilt speed or motor acceleration. I have found that starting gently, then gradually increasing speed, works best. This approach helps the coil’s protective layer adapt to movement without tearing.
Sometimes, coated coils have a protective plastic or paint that can chip if the coil bumps the cradle. Adding cushions to the cradle can help absorb shock. Some upenders feature foam or rubber surfaces that conform slightly to the coil’s contour. This spreads contact pressure over a wider area, lowering the chance of localized paint damage. If you have expensive coated coils, investing in these cushions or specialized cradles can save money by reducing rework.
I also see that some wraps include labels or barcodes. These must remain intact for tracking. If the clamp or cradle covers the label, it might smudge or tear it. Operators should place the coil so that the clamp or cradle does not crush important labels. Alternatively, they can add an extra label on an exposed area. If the coil’s identity is lost, you face confusion in shipping or inventory. Good labeling practices keep everything clear and traceable.
Below is a table covering key points for handling coated or wrapped coils on a coil upender:
Factor | Reason | Recommended Action |
---|---|---|
Surface Friction | Coated surfaces can be slippery | Use cradle grips or padded liners |
Wrap Security | Loose wraps can tear or fold | Check and secure wraps before flipping |
Speed Control | Quick tilts can stress coatings or wraps | Slow, steady rotation reduces damage |
Protective Cushion | Prevent localized pressure or scuffs | Add foam or rubber cradle surfaces |
Label Preservation | Wrap might hide or smudge labels | Position coil so labels remain visible |
I remember a scenario where a team handled pre-painted steel coils for an appliance manufacturer. They worried the upender’s metal cradle would scratch the glossy finish. We installed rubber pads on the contact points. Then we reduced the tilt speed. The flips went smoothly, and the paint stayed pristine. That success built trust that the upender could manage coated materials reliably.
In some cases, you might do partial wrapping. You might only wrap the coil’s edges, leaving the center exposed. This approach can reduce friction issues but still protect sensitive corners. If you see wear at certain spots, you can add extra wrap layers there. Each coil may need a slightly different approach. By experimenting with small adjustments, you find the best method for each coating type.
Maintenance remains vital. Coated or wrapped coils leave residue or dust on the cradle. Clean it regularly to maintain good grip. Check that no adhesive from the wrap is stuck to the cradle. If left unattended, these substances can build up and reduce friction. Also, if you handle multiple coil types, store presets for speed, clamp force, and cradle configuration. That way, you can switch from coated to uncoated coils quickly without manual changes.
Conclusion
I believe a coil upender can work with steel, non-ferrous metals, and coated or wrapped coils. By adjusting cradle features, clamp force, and tilt speed, you can safely flip almost any material. This keeps operations smooth and avoids product damage.