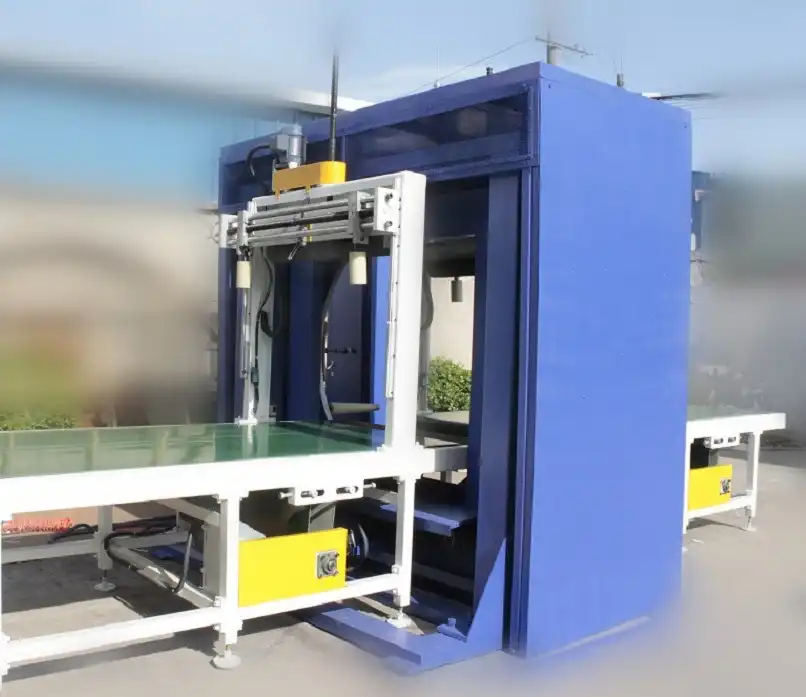
Failure is a natural part of using machinery, but when it comes to semiauto horizontal wrapping machines, understanding the why and how can save significant downtime and costs. These machines, essential for efficient and secure packaging, often face predictable and avoidable issues when properly maintained or operated within guidelines. By exploring the common causes of failure, you can ensure smoother operations and prevent unexpected expenses.
Issues in semiauto horizontal wrapping machines typically arise from a blend of human errors, environmental factors, and mechanical wear and tear. Each element plays a distinct role, contributing to disruptions that can halt production lines and affect overall efficiency. However, by identifying patterns and taking proactive measures, many of these failures can be avoided entirely.
Understanding these challenges requires delving into the operational principles of these machines. From recognizing signs of wear to knowing the critical parts prone to malfunction, this knowledge equips you to address issues effectively. Below, we’ll explore key insights, actionable tips, and detailed strategies to help you maintain operational consistency.
[Claim]:Semiauto horizontal wrapping machine failures stem primarily from preventable causes like poor maintenance, operator errors, and environmental factors.
1. Why Do Semiauto Horizontal Wrapping Machines Fail?
1.1 Understanding Machine Vulnerabilities
Machines, especially those handling repetitive tasks like wrapping, have inherent vulnerabilities. Components like motors, tension belts, and sensors are designed to withstand high use but are not immune to degradation over time. For example, a wrapping belt under continuous tension without routine checks can fail unexpectedly. Addressing such weak points starts with recognizing the operational limits of each part.
1.2 Common Machine Errors and Statistical Breakdown
A study on packaging machinery revealed that 45% of failures stem from mechanical issues, followed by 30% due to operator mishandling, and 25% attributed to environmental conditions such as temperature or debris. Here's a simplified breakdown:
Failure Cause | Percentage |
---|---|
Mechanical Wear | 45% |
Operator Mishandling | 30% |
Environmental Factors | 25% |
Routine inspections help identify signs of strain on the machine’s components, preventing these issues from escalating into costly repairs.
1.3 Critical Components That Require Monitoring
Key parts of a semiauto horizontal wrapping machine that demand consistent monitoring include:
- Motors and Gear Systems: Often the first to show signs of wear.
- Sensors: Responsible for precision, prone to misalignment.
- Belts and Tensioners: Regular lubrication and adjustments prevent snapping.
A lack of regular inspections and updates for these components can lead to unplanned downtimes, often during peak operational periods.
1.4 Preventative Maintenance and Operational Efficiency
Preventative maintenance involves actions like cleaning, lubrication, and systematic testing of components before failure occurs. For example, scheduling belt replacements every 6 months based on usage intensity ensures no sudden halts. Machines serviced on a proactive schedule report a 30% reduction in downtime compared to those repaired reactively.
Maintenance Type | Downtime Reduction |
---|---|
Preventative | 30% |
Reactive | - |
1.5 True or False: Factors Contributing to Failures
- True: Improper tension in wrapping belts accelerates wear and tear.
Explanation: Overly tight belts strain the motor and reduce the machine's lifespan. - False: Dust accumulation has no impact on machine performance.
Explanation: Dust interferes with sensors and motor cooling, leading to overheating or misaligned wrapping.
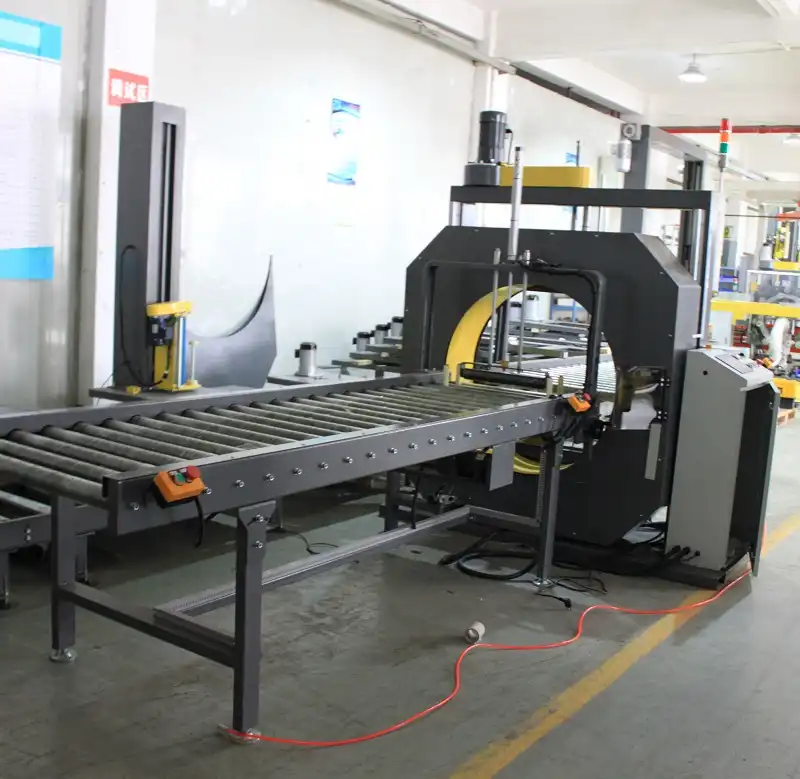
2. What Are the Most Common Causes of Downtime?
2.1 External Environmental Impacts
External factors, such as the operational environment, significantly impact the performance of semiauto horizontal wrapping machines. Humidity, temperature variations, and dust buildup can compromise components like motors and sensors. For example, a factory with poor ventilation may see a 15% increase in motor overheating incidents, causing unplanned halts in production.
Maintaining a controlled environment is crucial. Installing dust barriers or temperature regulators minimizes these risks, ensuring stable performance over extended periods.
2.2 Operator Errors: A Statistical Perspective
A survey of industrial packaging facilities revealed that 30% of downtime is attributed to operator mistakes. Key examples include:
- Incorrect calibration of machine settings, leading to misaligned wrapping.
- Neglecting routine checks before starting operations.
- Improper loading techniques that strain the motor and belts.
Here’s a snapshot of operator-related errors:
Operator Error | Impact | Frequency |
---|---|---|
Incorrect Calibration | Wrapping Misalign | 40% |
Neglected Routine Checks | Sensor Failure | 35% |
Improper Loading Techniques | Motor Strain | 25% |
2.3 Dive Deeper: Resolving Operator Challenges
Training programs tailored to machine-specific needs can drastically reduce operator errors. Facilities that implement quarterly training sessions report up to a 50% decrease in operator-related machine failures. Ensuring operators understand maintenance basics, such as cleaning dust-sensitive areas and identifying early signs of misalignment, makes a noticeable difference.
Training Frequency | Downtime Reduction |
---|---|
Quarterly | 50% |
Annual | 20% |
Developing checklists for daily operations and emergency responses further enhances efficiency. Standardizing procedures ensures consistency, reducing preventable errors.
2.4 True or False: Operator Error Myths
- True: Proper training reduces machine downtime by 50%.
Explanation: Knowledgeable operators are better equipped to handle calibration and preventive care. - False: Operator errors are inevitable and cannot be mitigated.
Explanation: Errors stem from a lack of training or unclear instructions, which can be corrected with proper measures.
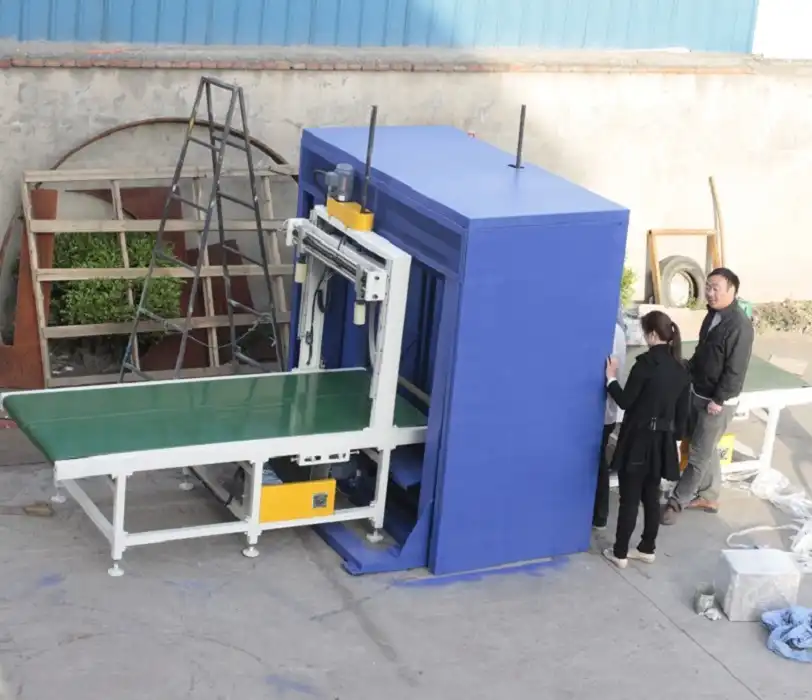
3. How Can Maintenance Strategies Mitigate Machine Failures?
3.1 Proactive Maintenance Programs
A robust maintenance schedule is the backbone of efficient machine operation. Facilities with proactive systems see a 30% boost in machine uptime compared to reactive models. Maintenance plans should focus on high-priority areas such as lubrication, sensor alignment, and belt tensioning.
For example, weekly checks on sensors reduce calibration-related downtime by 25%. Similarly, motor servicing every 6 months prevents overheating incidents, ensuring smooth operations.
3.2 Statistical Evidence Supporting Proactive Maintenance
Here’s how regular maintenance impacts uptime and costs:
Maintenance Type | Uptime Improvement | Cost Savings |
---|---|---|
Proactive Maintenance | 30% | 20% |
Reactive Maintenance | - | - |
3.3 Dive Deeper: Developing a Maintenance Blueprint
Creating a maintenance blueprint tailored to the specific needs of your wrapping machine ensures seamless functionality. For example:
- Daily Checks: Clean sensors and inspect belts for signs of wear.
- Monthly Inspections: Calibrate sensors and tighten all bolts.
- Quarterly Servicing: Lubricate motors and replace tensioners if needed.
Maintenance Activity | Frequency | Key Benefit |
---|---|---|
Sensor Cleaning | Daily | Prevent Misalignment |
Belt Inspection | Weekly | Avoid Sudden Failures |
Motor Lubrication | Quarterly | Enhance Longevity |
3.4 True or False: Maintenance Best Practices
- True: Proactive maintenance reduces downtime by up to 30%.
Explanation: Regularly serviced machines face fewer unexpected breakdowns. - False: Cleaning sensors daily is unnecessary.
Explanation: Dust and debris interfere with sensor accuracy, leading to misaligned wrapping.
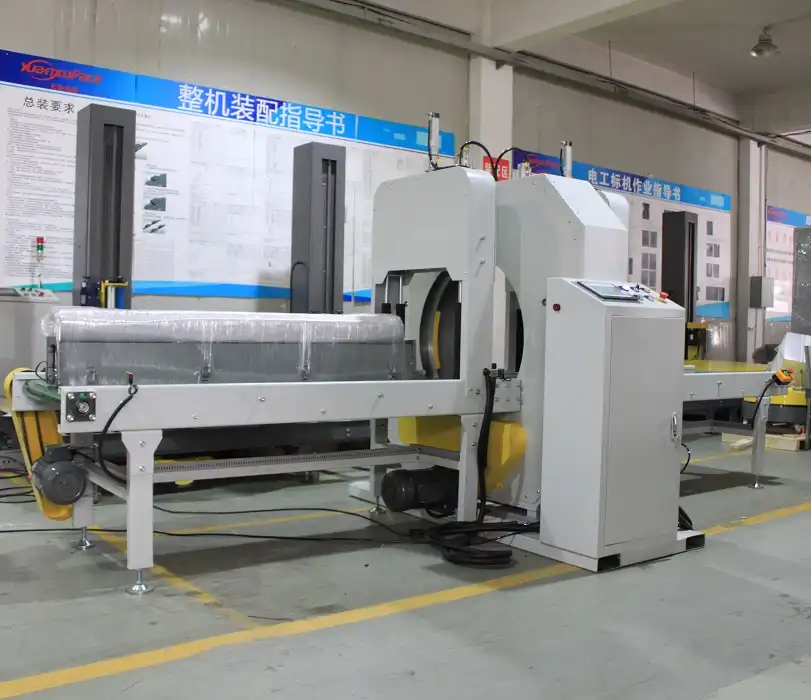
4. How Do Operator Training and Environmental Control Contribute to Machine Health?
4.1 Operator Expertise: A Key to Machine Longevity
Operators play a pivotal role in ensuring the seamless functioning of semiauto horizontal wrapping machines. Properly trained personnel can identify early warning signs of wear or malfunction, preventing minor issues from escalating into major failures. For instance, an operator adept at belt tension adjustments could save a motor from overheating due to excessive strain, significantly extending its lifespan.
Clear operating protocols paired with ongoing training sessions foster an environment where machines are used optimally, reducing downtime and repair costs.
4.2 Environmental Factors: Controlling the Uncontrollable
Environmental conditions within packaging facilities greatly influence machine reliability. Factors such as temperature, humidity, and air quality can accelerate component degradation. A study showed that facilities implementing environmental controls like dust barriers and temperature regulation experienced 20% fewer machine failures annually.
Environmental Factor | Failure Impact | Mitigation Strategy |
---|---|---|
Dust Accumulation | Sensor Misalignment | Install Dust Filters |
Temperature Variations | Motor Overheating | Maintain Ventilation |
Humidity | Corrosion of Components | Dehumidifiers |
4.3 Dive Deeper: Combining Training with Environmental Upgrades
The synergy between a skilled operator team and a controlled environment creates the ideal conditions for long-term machine efficiency. Operators who are well-trained can adapt quickly to environmental changes and implement necessary adjustments to the machine’s settings.
For example, when working in a high-humidity environment, operators can increase lubrication frequency to counteract rust formation. Training programs tailored to the specific challenges of each facility amplify these preventive measures, enhancing overall reliability.
Integration Strategy | Resultant Benefit |
---|---|
Operator Training + Dust Control | 15% Reduction in Sensor Errors |
Temperature Monitoring + Motor Care | 20% Decrease in Overheating |
4.4 True or False: Training and Environment Myths
- True: Dust barriers reduce sensor-related machine failures by 20%.
Explanation: Dust-free environments improve sensor accuracy and longevity. - False: Temperature control has no impact on machine efficiency.
Explanation: Unregulated temperatures lead to motor overheating and increased downtime.
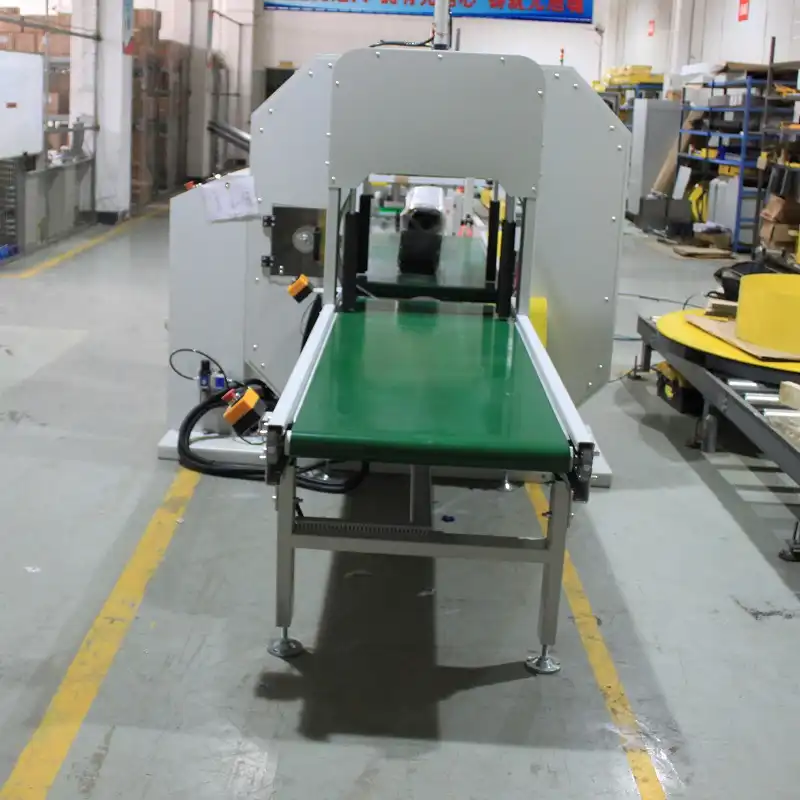
Conclusion: Maximizing Efficiency and Minimizing Failures
[Claim]
Semiauto horizontal wrapping machines are indispensable tools in industrial packaging, but their efficiency heavily relies on consistent maintenance, proper operator training, and environmental management. Failure to address these factors results in frequent breakdowns, increased downtime, and escalated repair costs.
To mitigate machine failures effectively, a combination of proactive measures is necessary. These include implementing routine maintenance schedules, training operators to handle machine-specific challenges, and optimizing the operating environment to prevent external damage to key components. Facilities that adopt these strategies report significant improvements in uptime and operational efficiency, ensuring long-term reliability.
By understanding and addressing the vulnerabilities of semiauto horizontal wrapping machines, industries can not only improve their packaging processes but also reduce the overall cost of ownership. Investing in proper systems today prevents costly interruptions tomorrow—ensuring your operations stay ahead in a competitive market.

Get Your Best Solution !