
The semi-auto pallet wrapping machine stands as a cornerstone of efficiency in many industries. Its ability to streamline packaging operations while ensuring product safety has made it indispensable in warehouses, distribution centers, and manufacturing plants. However, like any other machine, it’s not immune to failures. Addressing these failures is essential for maintaining productivity and minimizing operational costs.
When a semi-auto pallet wrapping machine malfunctions, the consequences can cascade across the supply chain. Downtime leads to delayed shipments, customer dissatisfaction, and increased costs. Understanding the common causes and solutions is not just an operational need but a strategic advantage.
While these machines are generally reliable, their complexity means even minor issues can snowball into larger problems if left unaddressed. To mitigate these risks, it’s crucial to know what can go wrong, why it happens, and how to fix it. This knowledge empowers businesses to act swiftly and ensure smooth operations.
.
Claim: Regular maintenance and proactive troubleshooting are key to preventing and resolving semi-auto pallet wrapping machine failures.
1. Common Failures in Semi-Auto Pallet Wrapping Machines: What Causes Them?
1.1 Insufficient Stretch Film Tension Adjustment
One of the most common issues is improper stretch film tension. When the tension is too loose, the load isn’t secured properly. If it’s too tight, the film may tear, leading to waste and inefficiency.
1.2 Mechanical Wear and Tear
Mechanical components like rollers, bearings, and belts are subject to wear and tear over time. A 2023 industry report found that 45% of machine failures in packaging systems result from worn-out components.
Component | Average Lifespan | Replacement Frequency |
---|---|---|
Rollers | 18 months | Every 12-18 months |
Belts | 24 months | Every 18-24 months |
Bearings | 36 months | Every 24-36 months |
These parts should be regularly inspected and replaced as part of a preventive maintenance schedule.
1.3 Electrical Issues
Electrical problems, such as faulty sensors or wiring failures, can halt operations unexpectedly. This is especially common in machines that operate in high-humidity environments. Proper insulation and regular testing are essential to prevent such issues.
1.4 Sensor Calibration Problems
Sensors play a critical role in ensuring that the wrapping process runs smoothly. Misaligned or dirty sensors can lead to miswraps or incomplete wrapping cycles. Cleaning and recalibrating the sensors can resolve most of these issues.
1.5 Two Fact Statement
- True: Regular cleaning of sensors can extend their lifespan by up to 30%.
- False: Using generic lubricants improves the performance of all mechanical parts.

2. How Do Operational Errors Contribute to Machine Failures?
2.1 Lack of Proper Operator Training
Operator error is one of the leading causes of machine failures. Semi-auto pallet wrapping machines require precision, especially in settings such as film tension, speed, and load positioning. Inexperienced operators often skip calibration steps or use incorrect settings, leading to inefficiencies and damage. Investing in comprehensive training programs can significantly reduce these risks.
2.2 Inconsistent Load Placement
Misaligned loads can strain the wrapping machine, leading to mechanical damage over time. A 2022 study revealed that 25% of machine repairs are linked to improper load placement. Implementing load alignment guides can prevent recurring issues.
Issue | Impact | Preventive Measure |
---|---|---|
Uneven load weight | Machine imbalance | Use weight distribution tools |
Overhanging edges | Tearing of film | Align load within pallet size |
Irregular load height | Miswrapping | Calibrate wrapping settings |
2.3 Mishandling During Repairs
When issues arise, untrained personnel attempting repairs can exacerbate problems. For example, using incorrect tools or applying excessive force can damage components such as rollers or motors. Clear guidelines for handling repairs should be established, and repairs should ideally be performed by trained technicians.
2.4 Conclusion
Operational errors often stem from a lack of training or established protocols. While semi-auto pallet wrapping machines are designed to be user-friendly, their efficiency relies on proper handling. By creating standard operating procedures and offering ongoing training, businesses can minimize these errors.
2.5 Two Fact Statement
- True: Regular operator training can reduce machine failure incidents by up to 30%.
- False: Overloading the machine is an acceptable way to maximize its capacity.
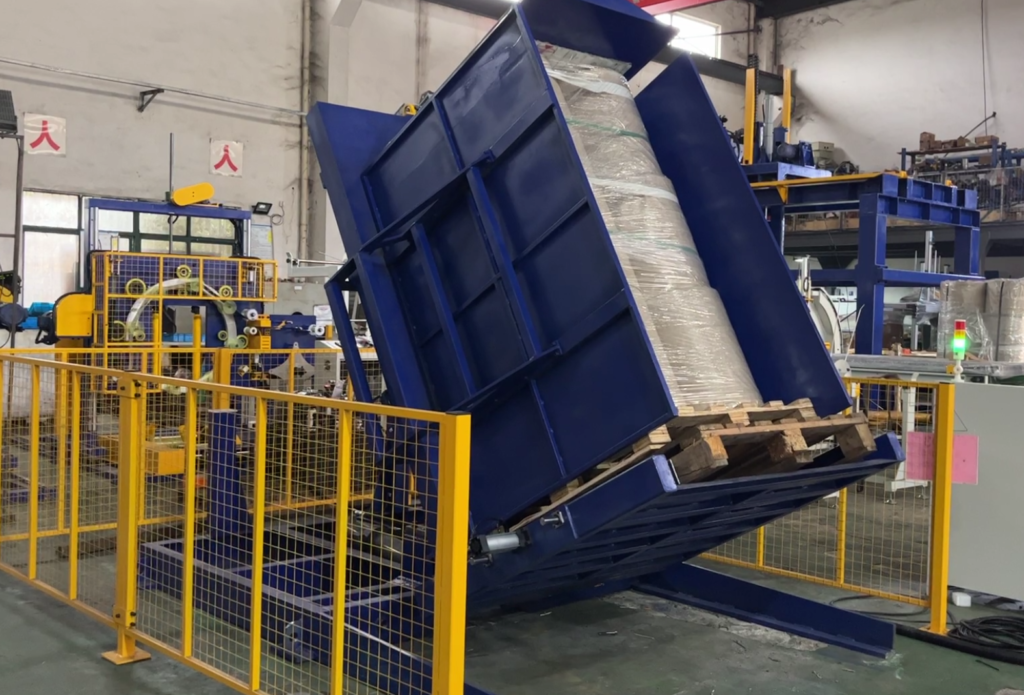
3. Why Is Maintenance Planning Vital for Machine Longevity?
3.1 Routine Maintenance Prevents Sudden Breakdowns
Semi-auto pallet wrapping machines require regular maintenance to operate efficiently. Neglecting maintenance schedules often leads to unexpected failures, resulting in costly downtime. Establishing a clear maintenance plan that includes cleaning, lubrication, and part inspections is crucial for keeping the machine in optimal condition.
Task | Frequency | Outcome |
---|---|---|
Clean sensors | Weekly | Avoid miswraps |
Inspect belts | Monthly | Prevent slippage |
Lubricate bearings | Quarterly | Reduce wear and overheating |
3.2 Ignoring Small Issues Can Escalate
A minor issue, such as a noisy bearing or a misaligned roller, might seem negligible at first. However, these small problems often escalate into larger, costlier repairs. Research shows that addressing minor issues promptly can reduce repair costs by 40% annually.
3.3 Dive Deeper into Predictive Maintenance
Predictive maintenance uses data from machine sensors to detect potential issues before they cause failures. Temperature monitoring, vibration analysis, and software alerts can help identify wear or misalignments. This approach not only reduces downtime but also extends the machine’s lifespan.
Sensor Type | Monitored Metric | Prevented Failure |
---|---|---|
Vibration Sensor | Bearing misalignment | Motor damage |
Temperature Sensor | Overheating components | Circuit board failure |
Film Tension Sensor | Improper tension | Film tearing |
3.4 Conclusion
Maintenance planning is more than a checklist; it’s a strategy to ensure consistent machine performance. By adopting a proactive approach and leveraging predictive technologies, businesses can maximize machine uptime and operational efficiency.
3.5 Two Fact Statement
- True: Predictive maintenance reduces downtime by an average of 20%.
- False: Routine cleaning has no impact on machine performance.
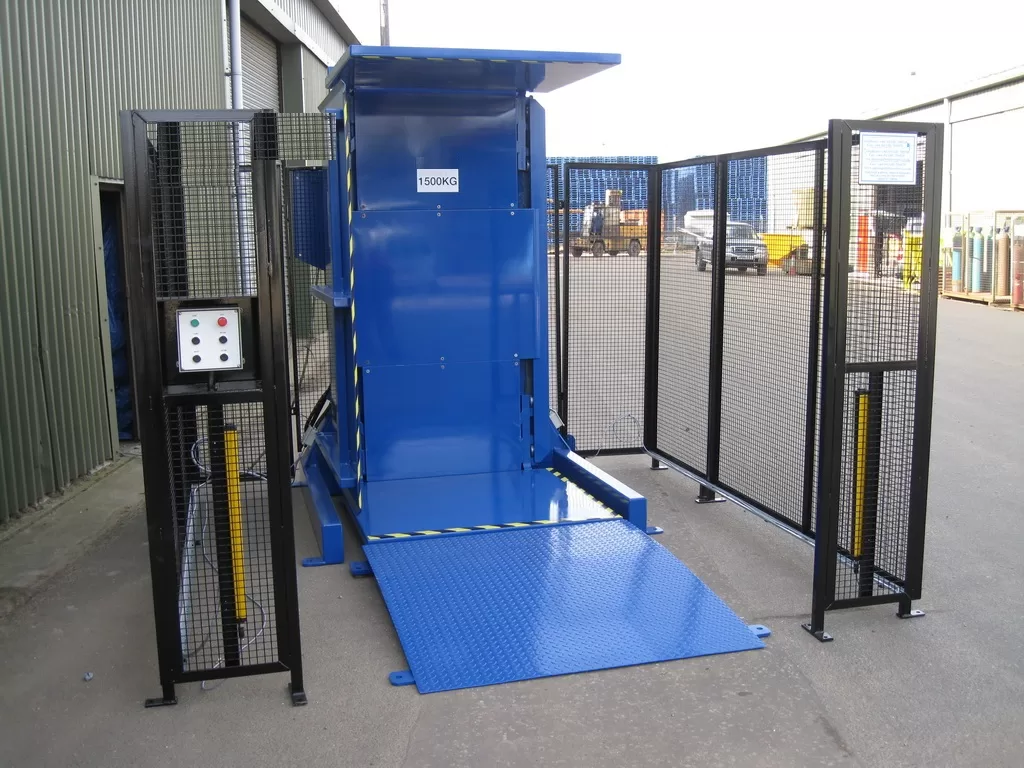
4. Can Upgrades Prevent Recurring Failures in Wrapping Machines?
4.1 Upgrading to Advanced Tension Control
One of the most effective upgrades for semi-auto pallet wrapping machines is an advanced tension control system. This technology adjusts film tension dynamically, ensuring consistent wrapping for loads of varying sizes and weights. By minimizing film breakage and improving load stability, businesses can significantly reduce operational disruptions.
4.2 Improved Sensor Technologies
Modern sensor technologies are designed to prevent common issues such as misalignment and incomplete wraps. For example, proximity sensors can detect irregular load shapes, while light sensors ensure proper wrapping coverage. A comparative analysis of sensor upgrades showed a 25% improvement in wrapping accuracy and efficiency.
Sensor Type | Benefit | Cost Savings |
---|---|---|
Proximity Sensor | Detects load irregularities | Reduces rework costs by 20% |
Light Sensor | Ensures wrapping coverage | Minimizes material wastage |
4.3 Dive Deeper into Automation Integration
Integrating automation into semi-auto pallet wrapping machines can dramatically reduce the frequency of failures. Features like automated diagnostics, load measurement, and programmable settings streamline operations and lower the margin for error. Automated diagnostics, for instance, can alert operators to potential problems before they disrupt workflows, increasing the machine’s reliability.
4.4 Conclusion
Upgrading semi-auto pallet wrapping machines with advanced technologies is an investment in long-term efficiency. By enhancing tension control, sensors, and automation capabilities, businesses can minimize failures, optimize productivity, and reduce operational costs.
4.5 Two Fact Statement
- True: Upgrading to automated tension control can reduce film waste by up to 30%.
- False: Advanced sensors are only beneficial for fully automatic machines.
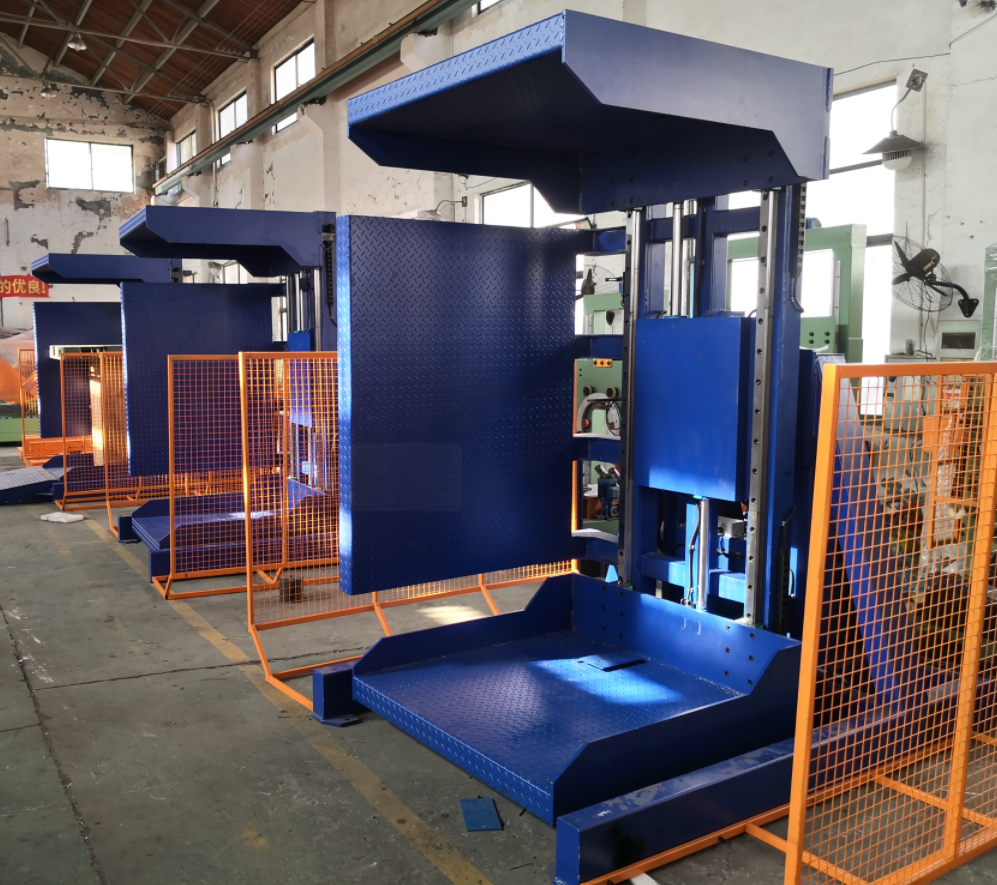
Conclusion
Semi-auto pallet wrapping machines are vital tools in modern supply chains, but their efficiency relies on proper usage, maintenance, and upgrades. From addressing common failures to investing in preventive measures and embracing new technologies, businesses can ensure these machines remain reliable assets. By prioritizing training, maintenance, and strategic upgrades, companies can achieve both operational excellence and cost savings.
Claim: A proactive approach to managing semi-auto pallet wrapping machine failures enhances performance, reduces downtime, and safeguards operational integrity.

Get Your Best Solution !