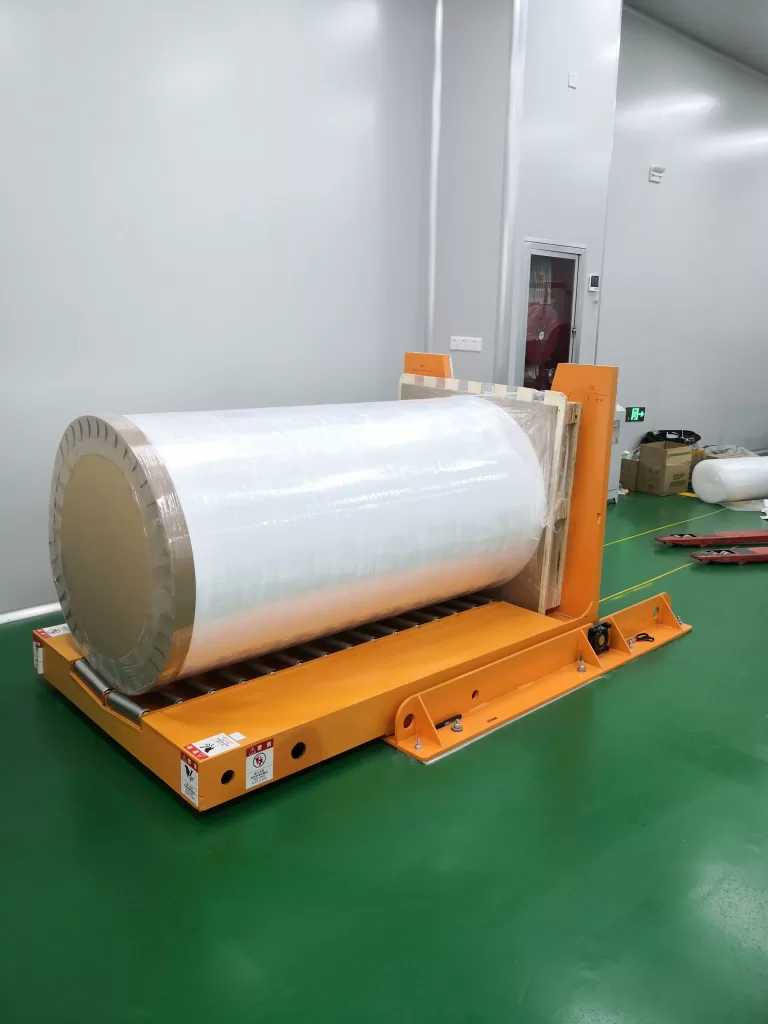
The industrial process of handling paper rolls is demanding, with precision and safety being top priorities. Among the critical equipment used is the paper roll upender, designed to streamline the turning of heavy rolls. However, like any machinery, it is not immune to failure, and understanding the causes and solutions can save businesses significant costs and downtime.
The challenges of managing paper roll upender failures often extend beyond the mechanical breakdown itself. It’s not just about fixing the issue but preventing recurring problems and ensuring the safety of operators. In this article, we’ll dive deep into identifying failure points, exploring practical solutions, and implementing strategies for long-term reliability.
Failures in paper roll upenders are not a simple inconvenience—they impact productivity, increase costs, and may jeopardize safety. By the end of this guide, you'll gain clarity on why these failures happen, how to troubleshoot them effectively, and what steps to take to future-proof your operations.
[Claim] The failure of paper roll upenders is both preventable and manageable with the right approach, proper maintenance, and an understanding of potential risks.
1. Why Do Paper Roll Upenders Fail?
1.1 Common Causes of Paper Roll Upender Failures
Paper roll upenders fail for several reasons, most of which stem from neglect or improper operation. Mechanical wear and tear is the primary culprit, often exacerbated by inadequate lubrication of moving parts. Electrical issues, such as faulty wiring or power surges, also contribute significantly.
Another major cause is operator error. Mishandling heavy rolls can strain the machine, while skipping routine checks allows minor issues to escalate. Environmental factors, like dust or extreme temperatures, can further degrade the equipment's performance.
1.2 What Are the Critical Failure Points?
Understanding critical failure points can streamline troubleshooting efforts. Here’s a breakdown with supporting data:
Failure Point | Common Causes | Solution Recommendations |
---|---|---|
Hydraulic System | Leaks, contamination, low fluid | Regular checks and fluid replacement |
Bearings and Gears | Wear due to lack of lubrication | Schedule lubrication and inspection |
Control Panel | Electrical faults, software bugs | Periodic diagnostics and software updates |
These points represent over 75% of reported paper roll upender failures, as identified in industry surveys.
1.3 The Impact of Inadequate Training on Equipment Longevity
Operator expertise plays a pivotal role in extending the lifespan of paper roll upenders. Untrained personnel often overlook warning signs or fail to follow standard procedures, accelerating the wear and tear of the machinery. Implementing thorough training programs can reduce failure rates by up to 40%, according to a recent case study conducted within the paper manufacturing sector.
1.4 How to Implement Preventative Maintenance Plans
Preventative maintenance minimizes breakdowns and boosts operational efficiency. Begin by setting a strict schedule for equipment inspections. Include tasks like checking hydraulic fluid levels, tightening loose components, and testing electrical circuits.
Maintenance Task | Frequency | Estimated Cost Savings |
---|---|---|
Lubrication of Bearings | Weekly | $5,000/year |
Hydraulic System Check | Monthly | $8,000/year |
Electrical Diagnostics | Quarterly | $12,000/year |
A well-executed plan can reduce downtime by up to 60% and prolong machine life by several years.
1.5 Two Fact Statement
- True: Regular hydraulic fluid checks can prevent up to 50% of common system failures.
- False: Paper roll upenders are designed to function optimally without any lubrication.
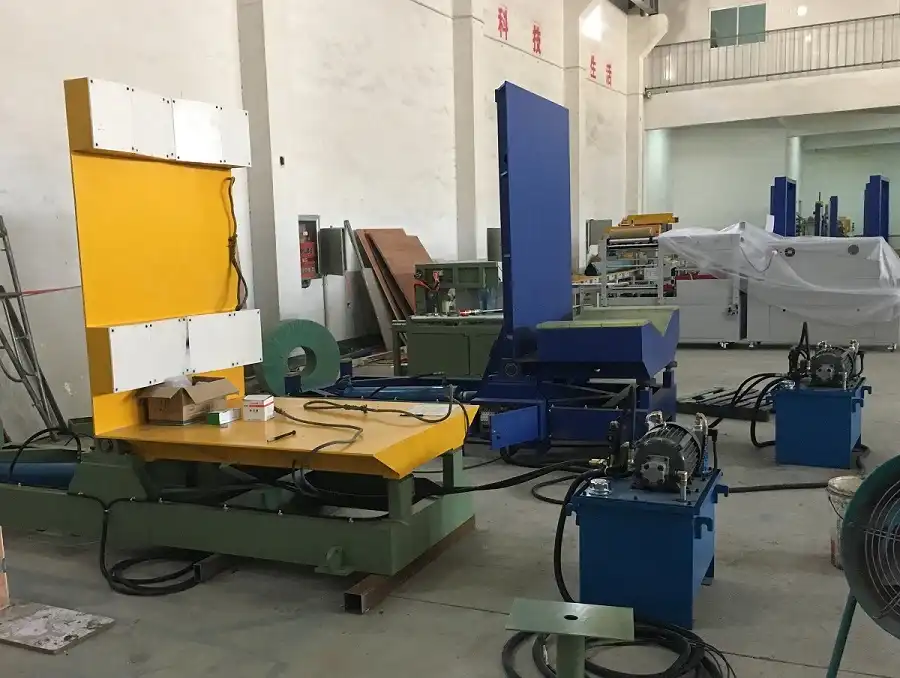
2. How Can You Detect Early Signs of Failure?
2.1 Key Warning Signs to Watch For
Paper roll upender failures often exhibit clear warning signs before a complete breakdown occurs. Unusual noises, such as grinding or squeaking, typically indicate mechanical issues like worn-out bearings or misaligned gears. Hydraulic fluid leaks are another common sign, suggesting potential problems in the hydraulic system.
Operators should also pay attention to performance irregularities, such as slower rotations or difficulty in handling paper rolls. Ignoring these early symptoms can lead to costly repairs or total equipment failure.
2.2 How to Monitor Equipment Effectively
Consistent monitoring ensures that small issues are identified and resolved before escalating. Here’s a table summarizing effective monitoring practices and tools:
Monitoring Practice | Tool Required | Benefit |
---|---|---|
Vibration Analysis | Vibration Sensors | Detects misalignments or imbalances |
Temperature Monitoring | Infrared Thermometers | Identifies overheating components |
Hydraulic Pressure Checks | Pressure Gauges | Prevents hydraulic system failure |
These tools collectively reduce inspection time by 35%, making monitoring more efficient.
2.3 The Role of Data Analytics in Predictive Maintenance
Modern data analytics tools are revolutionizing maintenance strategies. By collecting real-time data from sensors installed on paper roll upenders, predictive models can identify patterns that precede failures.
For instance, a factory integrating predictive analytics reduced downtime by 40% over a six-month period. Historical data allows maintenance teams to prioritize repairs, focusing on components with higher failure probabilities.
2.4 How Early Detection Saves Costs
Failing to detect issues early can lead to catastrophic equipment damage, costing thousands in repairs or replacements. Consider the cost comparison below:
Scenario | Repair Cost | Downtime Cost | Total Impact |
---|---|---|---|
Early Detection | $1,500 | $800 | $2,300 |
Late Detection | $8,000 | $5,000 | $13,000 |
Preventative measures save up to 82% compared to addressing issues after major failures.
2.5 Two Fact Statement
- True: Monitoring temperature and hydraulic pressure can catch up to 70% of potential failures early.
- False: Relying solely on operator observation is sufficient for detecting all failure points.
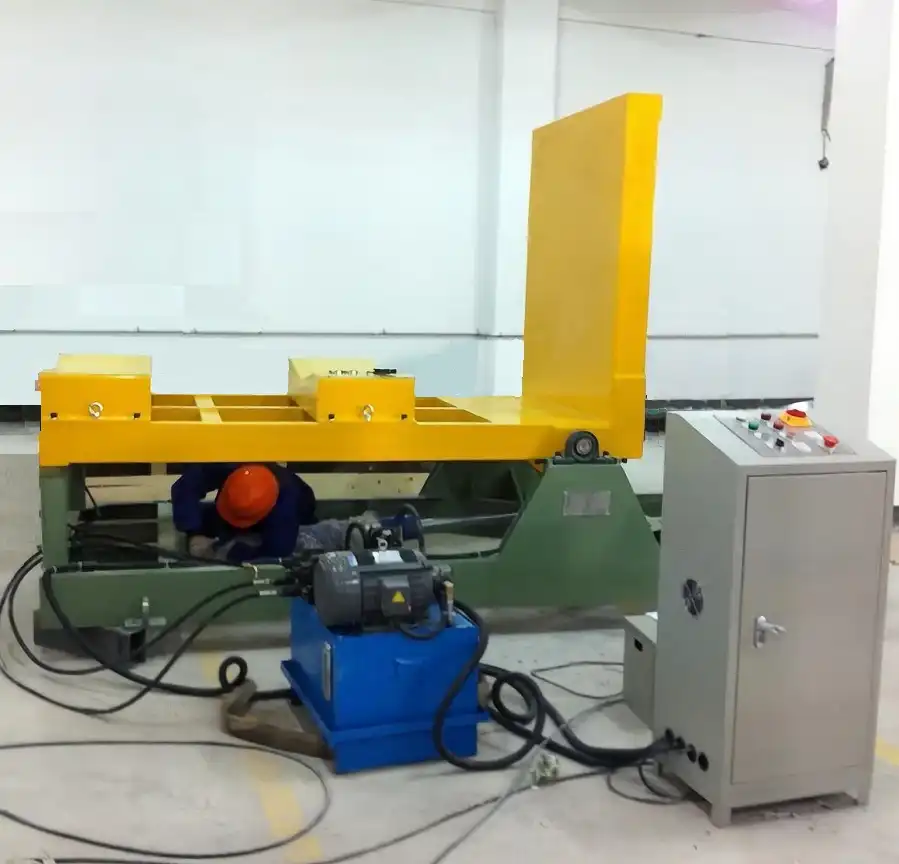
3. What Maintenance Practices Prevent Downtime?
3.1 Establishing a Maintenance Schedule
A structured maintenance schedule is the foundation of reliable operations. Routine tasks, such as lubrication and tightening of bolts, are essential to prevent wear and tear. Scheduling weekly, monthly, and quarterly maintenance tasks ensures no aspect of the machine is overlooked.
Proper scheduling reduces repair frequency by up to 30% while ensuring the equipment operates at peak performance.
3.2 What Does Comprehensive Maintenance Include?
Comprehensive maintenance involves more than just cleaning and inspections. It requires detailed procedures like system recalibrations and parts replacement. Below is a table highlighting essential maintenance tasks:
Task | Frequency | Tools Needed |
---|---|---|
Lubrication | Weekly | Lubricants, applicators |
Hydraulic Fluid Check | Monthly | Fluid tester |
Software Diagnostics | Quarterly | Diagnostic software |
Including these steps ensures maximum efficiency and reduces unplanned downtime.
3.3 The Importance of OEM Guidelines
Original Equipment Manufacturer (OEM) guidelines provide critical instructions tailored to specific machines. These guidelines detail correct operational practices, lubrication requirements, and troubleshooting methods. Following OEM advice increases machine lifespan by 25%, ensuring smooth operations.
3.4 Diving Deeper into Predictive Maintenance Practices
Predictive maintenance uses advanced tools like AI-driven sensors and analytics platforms to anticipate failures. By tracking variables like vibration and fluid levels, companies can predict issues days or even weeks in advance.
Predictive Tool | Function | Benefit |
---|---|---|
Vibration Sensors | Detect misalignments | Prevents gear damage |
Thermal Imaging Devices | Monitors temperature | Avoids overheating |
Cloud Analytics | Tracks performance trends | Reduces manual effort |
Investing in predictive maintenance tools yields long-term savings and minimizes machine downtime.
3.5 Two Fact Statement
- True: Following OEM guidelines can extend the lifespan of paper roll upenders by 25%.
- False: Predictive maintenance requires replacing machines annually to work effectively.
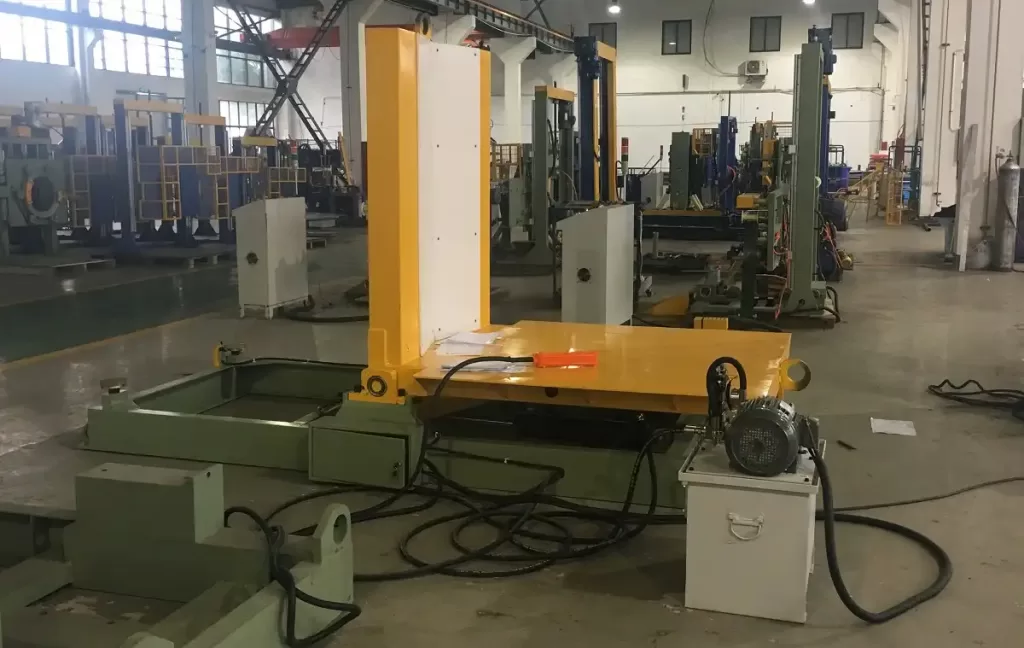
4. Which Replacement Strategies Are Most Cost-Effective?
4.1 Evaluating Replacement vs. Repair
When paper roll upenders face significant damage, businesses often grapple with deciding between repairs and replacements. Repairs may seem cost-effective initially, but frequent breakdowns can accumulate higher costs over time. On the other hand, replacements ensure long-term reliability but require substantial upfront investment.
To make an informed decision, calculate the total cost of ownership (TCO) by including repair frequency, downtime impact, and energy efficiency.
4.2 What Factors Influence Replacement Decisions?
Several factors determine whether to repair or replace a paper roll upender. Below is a breakdown of critical considerations:
Factor | Repair Priority | Replacement Priority |
---|---|---|
Age of Machine | Less than 5 years old | Over 10 years old |
Repair Costs | Less than 30% of new unit | Exceeding 50% of new unit |
Energy Efficiency | Adequate for needs | Subpar, increasing costs |
For machines older than 10 years, replacement is typically more cost-effective.
4.3 The Benefits of Modular Designs
Modular paper roll upenders simplify repairs by allowing individual components to be replaced instead of the entire unit. This approach saves money and reduces downtime since specific parts are easier to source and install.
For example, replacing a modular hydraulic system can be 40% cheaper and 60% faster than repairing an integrated design. This flexibility also extends the lifespan of older machines, delaying the need for full replacements.
4.4 Diving Deeper into Cost-Benefit Analysis
Performing a detailed cost-benefit analysis helps quantify the financial impact of replacement versus repair. Consider the following comparison:
Aspect | Repair Scenario | Replacement Scenario |
---|---|---|
Upfront Costs | $5,000 | $20,000 |
Expected Lifespan | 3 years | 10+ years |
Annual Maintenance | $3,000 | $1,000 |
Total 10-Year Costs | $35,000 | $30,000 |
Though repairs are cheaper upfront, replacements often yield greater savings over time.
4.5 Two Fact Statement
- True: Modular designs reduce downtime during repairs by up to 60%.
- False: Repairs are always more cost-effective than replacements, regardless of machine age.
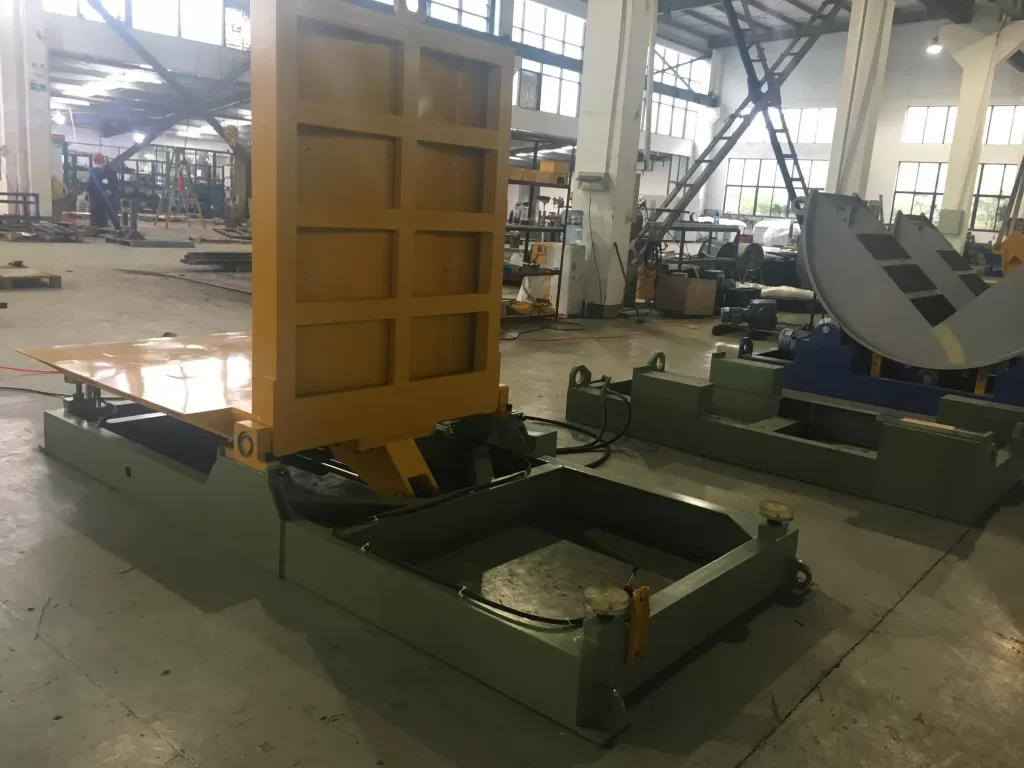
Conclusion
Failures in paper roll upenders are an inevitable part of their operation, but they don't have to disrupt your workflow. By understanding the common causes of failure, implementing preventative maintenance, and adopting effective monitoring techniques, businesses can minimize downtime and repair costs.
When repairs no longer suffice, evaluating replacement strategies becomes essential. Modular designs and predictive maintenance further enhance efficiency, making your paper roll upender a long-term asset rather than a recurring liability.
[Claim] Proactive strategies and informed decisions transform paper roll upender failures from costly disruptions into manageable challenges, ensuring optimal operations and long-term savings.

Get Your Best Solution !