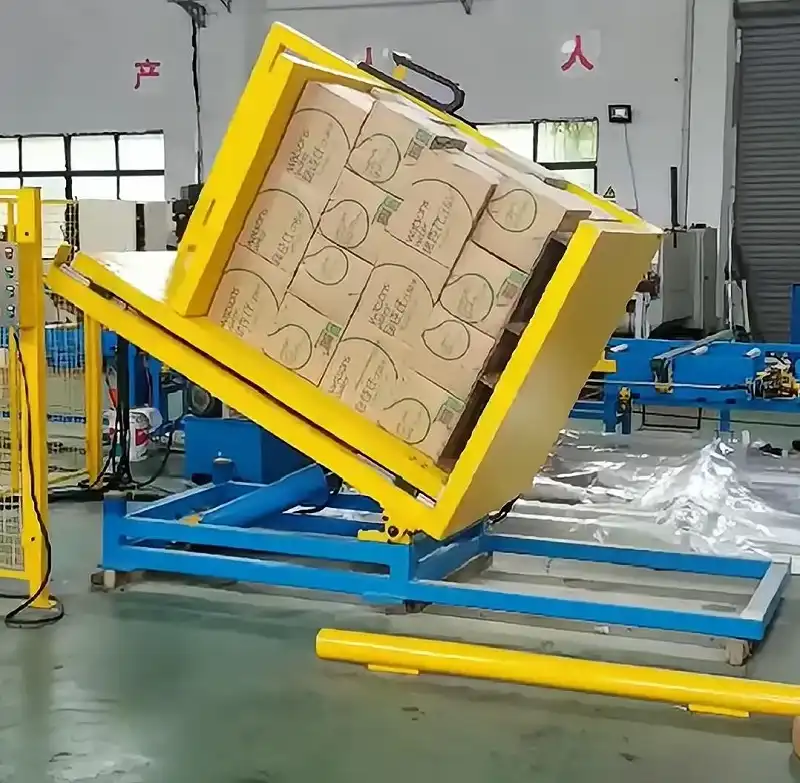
Pallet inverters are crucial in modern logistics and manufacturing, ensuring efficiency, safety, and cost-effectiveness when handling heavy goods. However, even the most reliable machines can fail if not properly maintained or operated. These failures can disrupt operations, increase costs, and compromise safety, leading to frustration for businesses and employees alike.
Failures often arise from overlooked issues—minor mechanical wear, improper use, or neglected routine maintenance. Understanding the causes of these failures is the first step toward minimizing downtime and safeguarding productivity. So, why do pallet inverters fail, and how can you address these issues proactively?
Whether you're a warehouse manager or a manufacturer, recognizing the early signs of pallet inverter issues is essential. It could mean the difference between smooth operations and costly downtime. Let's dive into the key factors contributing to pallet inverter failures and how to prevent them.
[Claim]
Regular maintenance, proper operator training, and early identification of issues are the backbone of avoiding pallet inverter failures. Neglecting these aspects can lead to frequent breakdowns, increased repair costs, and reduced operational efficiency.
1. Why Do Pallet Inverters Fail?
1.1 Causes of Mechanical Wear and Tear
Pallet inverters are heavy-duty machines designed for rigorous use. However, daily operation under high stress can lead to mechanical wear over time. Friction, impact, and prolonged use weaken key components such as hydraulic pumps, hinges, and safety guards.
Neglecting regular maintenance accelerates wear, turning minor issues into major malfunctions. Regular inspections are essential to prevent breakdowns. Checking for unusual sounds, hydraulic leaks, or reduced performance can help catch problems early.
1.2 Overloading and Stress on Key Components
Overloading pallet inverters is a common mistake. Each machine is designed to handle a specific weight limit, yet operators sometimes push beyond these boundaries. Overloading not only causes immediate strain on hydraulic systems but also reduces the machine’s lifespan.
Below is a summary of weight-related stress points:
Component | Stress Effect | Failure Outcome |
---|---|---|
Hydraulic Cylinder | Reduced pressure efficiency | Inconsistent load flipping |
Bearings | Excessive heat build-up | Risk of seizing or deformation |
Frame Integrity | High stress fractures | Structural collapse during use |
Exceeding the recommended load limit creates a ripple effect, causing secondary components to deteriorate faster.
A labeled diagram showcasing the impact of overloading on a pallet inverter's hydraulic system.
1.3 Lack of Routine Maintenance
Routine maintenance ensures longevity and optimal performance of pallet inverters. Without a consistent schedule, minor faults like loose bolts or oil contamination in the hydraulic fluid can escalate into larger issues.
Maintenance Task | Frequency | Outcome of Neglect |
---|---|---|
Inspecting hydraulic seals | Weekly | Fluid leaks, reduced efficiency |
Lubricating moving parts | Monthly | Increased friction, wear |
Checking safety systems | Monthly | Compromised operator safety |
Scheduling regular tune-ups and adhering to manufacturer recommendations can reduce breakdown risks significantly.
1.4 Two Fact Statements
- True: Regularly replacing hydraulic oil in pallet inverters prevents contamination and maintains efficiency.
- False: Increasing the load capacity beyond manufacturer recommendations will extend the lifespan of the machine.
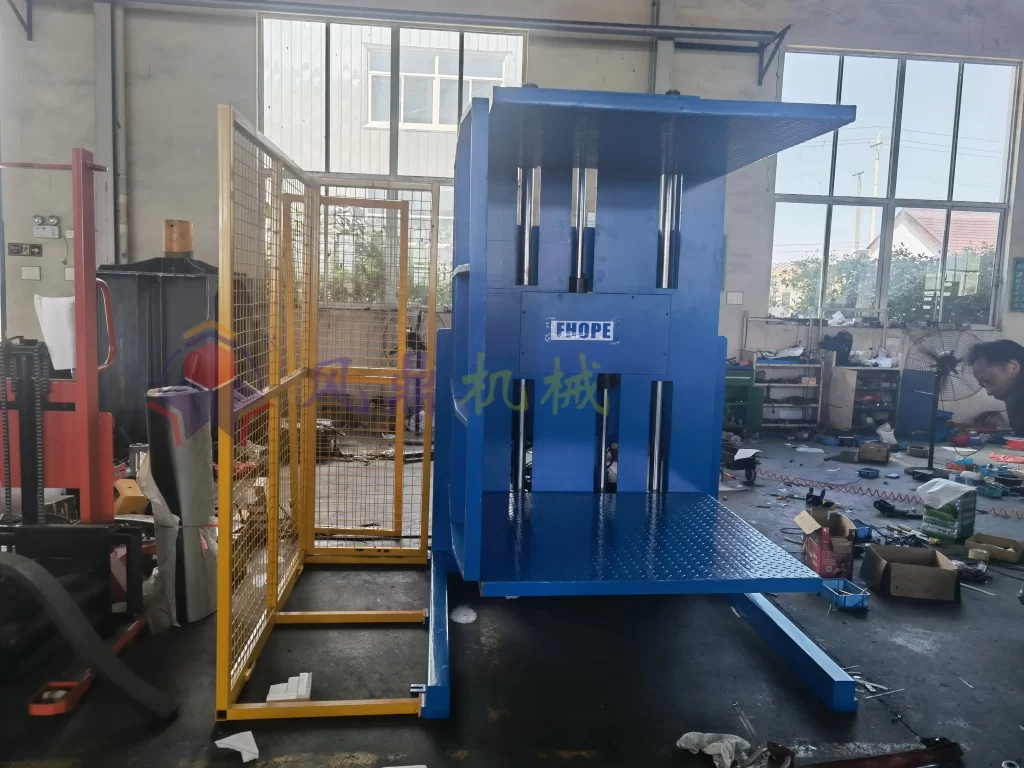
2. What Are the Common Mechanical Issues?
2.1 Signs of Hydraulic System Failures
The hydraulic system is the heart of a pallet inverter. Any malfunction here can halt operations. Common signs include slow response times, jerky movements, or complete failure to lift or rotate. These symptoms often point to issues such as air trapped in the system, worn-out seals, or low hydraulic fluid levels.
To ensure smooth operation, regular hydraulic inspections are critical. Look for oil leaks, unusual noises, or reduced pressure, as these can indicate an impending failure.
2.2 Frequent Faults in Moving Components
Mechanical components like hinges, bearings, and clamps endure constant stress. Over time, improper lubrication or debris buildup can lead to reduced efficiency or part failure. Below is an overview of frequently affected parts:
Component | Common Issue | Impact on Functionality |
---|---|---|
Hinges | Rust, wear | Restricted movement |
Bearings | Lack of lubrication | Increased friction, overheating |
Clamps | Misalignment, cracks | Uneven gripping, load instability |
Addressing these issues early can prevent costly repairs and reduce downtime.
A close-up image of a corroded hinge on a pallet inverter, illustrating the importance of preventative maintenance.
2.3 Preventing Overheating in Hydraulic Systems
Overheating is a silent killer for hydraulic systems. Excessive heat can degrade hydraulic fluid, reduce lubrication, and increase the likelihood of part failures. To combat this, maintain proper ventilation around the machine and ensure the cooling system is functioning effectively.
Below is a comparison of optimal versus overheated systems:
Factor | Optimal | Overheated |
---|---|---|
Hydraulic Fluid Temp. | 50–60°C | 80°C+ |
Response Time | Immediate | Delayed |
Risk of Seal Damage | Minimal | High |
Routine checks for signs of overheating, such as discoloration of hydraulic fluid or hot surfaces, are crucial.
2.4 Conclusion
Understanding and addressing mechanical issues in their early stages is key to maintaining a reliable pallet inverter. By identifying signs of wear and tear or hydraulic failures before they escalate, businesses can prevent costly disruptions.
2.5 Two Fact Statements
- True: Ensuring proper lubrication of bearings significantly reduces wear and extends the lifespan of moving components.
- False: Hydraulic systems can function optimally without regular fluid replacement as long as there are no visible leaks.
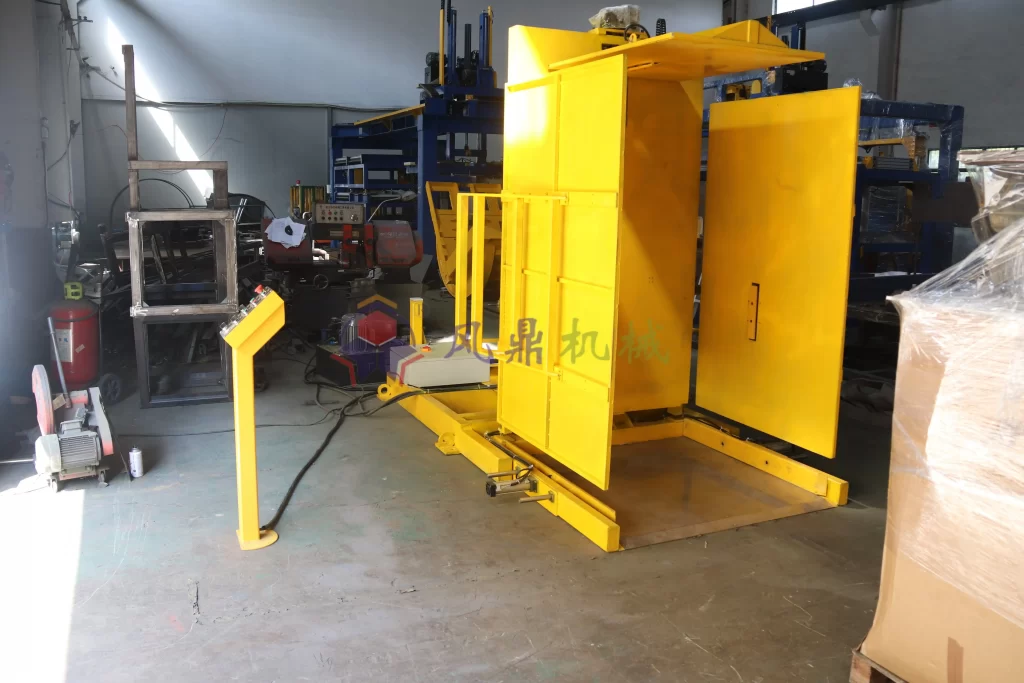
3. How Can Operator Errors Impact Performance?
3.1 Inadequate Training Among Operators
Operators lacking sufficient training often mishandle pallet inverters, leading to unnecessary wear or sudden breakdowns. For instance, improper load placement can strain components like clamps or frames, reducing efficiency and safety.
Proper training programs, emphasizing correct loading procedures and weight limitations, are critical to avoiding such issues. With skilled operators, the likelihood of damage significantly decreases.
3.2 Errors in Calibration and Adjustment
Incorrectly calibrated pallet inverters can result in uneven movements or load imbalances. Operators adjusting settings without understanding the equipment can worsen these issues. Below is a list of common operator errors and their consequences:
Error | Consequence | Resolution |
---|---|---|
Improper weight settings | Strain on hydraulic system | Use manufacturer-recommended settings |
Inaccurate clamp pressure | Damaged goods | Routine calibration checks |
An illustration of an improperly loaded pallet inverter, showing the risks of poor operator handling.
3.3 Consequences of Neglecting Safety Features
Ignoring built-in safety features is a major contributor to accidents and equipment failure. Operators who bypass safety interlocks or fail to use emergency stop mechanisms risk damaging both the machine and the goods being handled.
Ensuring all operators are familiar with these safety measures should be a standard practice. Regular training refreshers can reinforce their importance and promote safer operations.
3.4 Two Fact Statements
- True: Operators failing to use emergency stop mechanisms during malfunctions can exacerbate machine damage.
- False: Skipping daily operational checks will not impact the long-term performance of pallet inverters.
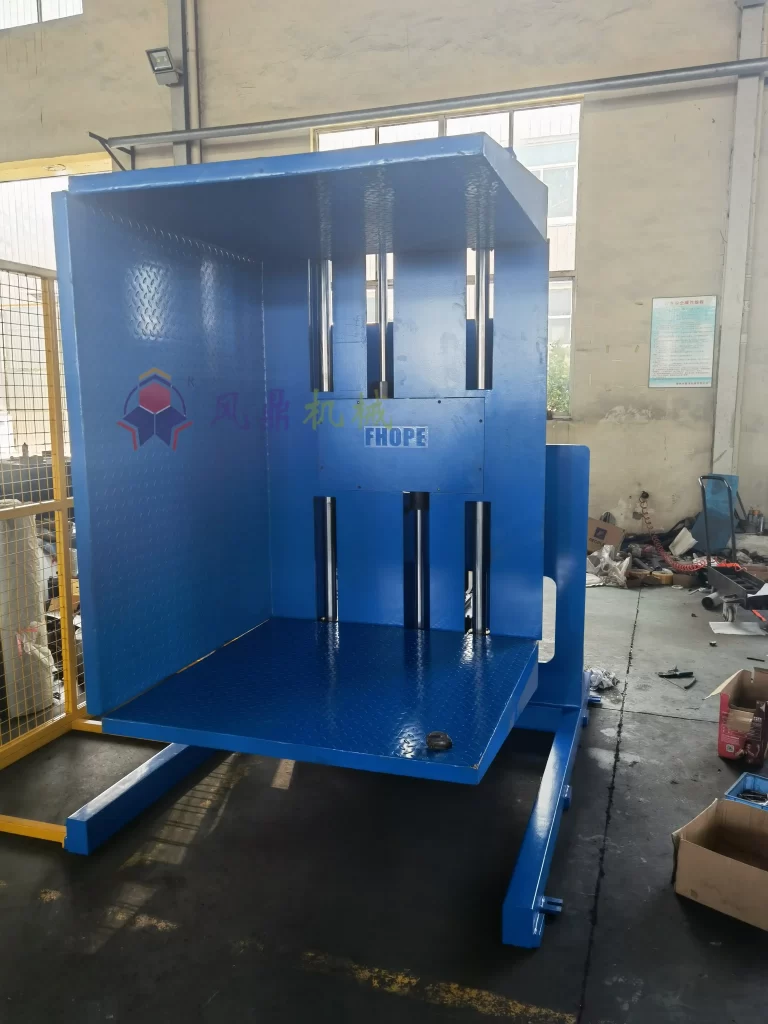
4. What Preventative Maintenance Practices Work Best?
4.1 Establishing a Maintenance Schedule
Consistency is key when it comes to preventative maintenance. Establishing a routine maintenance schedule ensures that minor issues are addressed before they escalate into costly failures. A well-planned schedule should cover daily inspections, monthly checks, and annual servicing.
Daily tasks include inspecting hydraulic lines for leaks and testing the controls for responsiveness. Monthly checks might involve tightening bolts and verifying clamp alignment. Annual servicing often requires professional support to assess the hydraulic system’s overall health and replace worn-out parts.
4.2 Common Preventative Tasks and Their Impact
Here’s a breakdown of essential maintenance tasks and their effects:
Maintenance Task | Frequency | Result |
---|---|---|
Hydraulic fluid replacement | Quarterly | Avoids contamination and overheating |
Inspecting electrical systems | Monthly | Prevents wiring faults |
Lubricating moving parts | Weekly | Reduces wear and ensures smooth motion |
Regular attention to these details not only reduces downtime but also extends the machine’s lifespan, delivering better returns on investment.
A step-by-step image guide for lubricating the moving parts of a pallet inverter.
4.3 Advanced Maintenance Strategies
Advanced strategies such as predictive maintenance use technology to monitor the condition of the machine in real-time. Sensors can detect anomalies in vibration, temperature, or pressure, alerting operators to potential issues before they cause failure.
This proactive approach minimizes unplanned downtime and enhances efficiency. While it may require an upfront investment, predictive maintenance often pays for itself through improved machine reliability and reduced repair costs.
4.4 Two Fact Statements
- True: Predictive maintenance technologies can reduce downtime by up to 30%, according to industry reports.
- False: Lubricating moving parts once a year is sufficient for optimal pallet inverter performance.
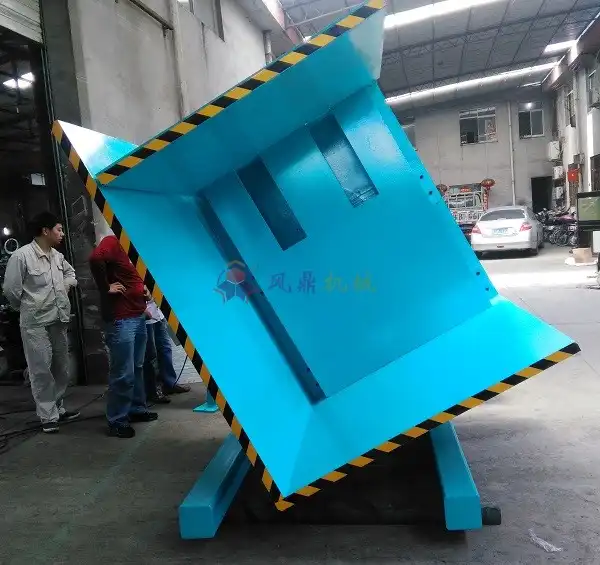
Conclusion
What You Should Know About Preventing Failures
Pallet inverters are indispensable tools in logistics, but their performance depends on regular care, proper handling, and strategic planning. By understanding common failure points, investing in operator training, and prioritizing preventative maintenance, businesses can avoid disruptions and maximize efficiency.
[Claim]
Proactive measures like routine maintenance and operator training not only prevent failures but also extend the lifespan of pallet inverters, delivering long-term savings and operational stability.

Get Your Best Solution !