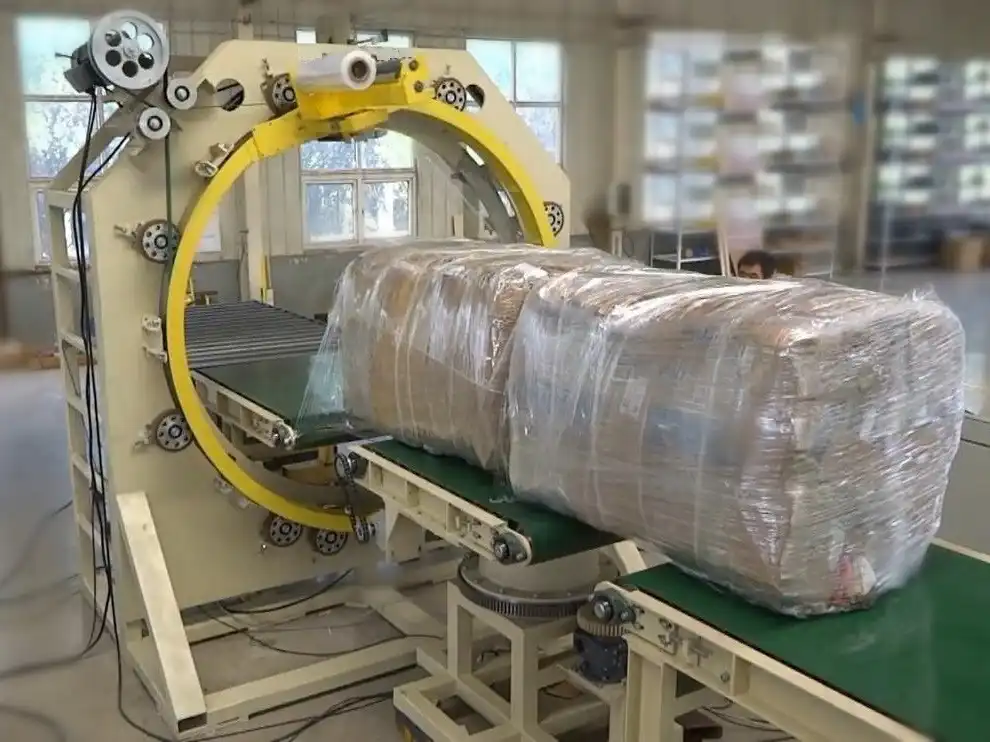
The moment an orbital stretch wrapper fails, operations can come to a standstill, leaving a trail of missed deadlines and mounting costs. For those of us who rely on these machines, a breakdown isn’t just an inconvenience; it’s a challenge to productivity, profitability, and trust with clients. While failure is inevitable in any mechanical system, understanding its causes, consequences, and solutions can significantly change how you manage downtime.
Let me share my personal experiences with orbital stretch wrapper failures. At first, I treated breakdowns as isolated incidents. But as the interruptions grew, I started investigating deeper. What I found was eye-opening: most failures aren’t spontaneous—they’re preventable. This insight changed how I approached machine maintenance and investment strategies.
Many users assume these machines should function flawlessly without intervention, but the reality is different. As advanced as these systems are, their intricate design makes them susceptible to unique failures. Recognizing the warning signs and addressing them proactively isn’t just smart—it’s essential. Let’s explore the critical factors that every operator should know to avoid costly disruptions.
[Claim]: Preventing orbital stretch wrapper failures requires understanding the root causes, implementing regular maintenance, and choosing the right machine for your operational demands.
1. What Are the Common Causes of Orbital Stretch Wrapper Failures?
1.1 Design Flaws and Operational Stress
When a machine is pushed beyond its designed operational limits, failure becomes inevitable. Orbital stretch wrappers, while robust, are vulnerable to stress factors such as excessive loads or improper alignment. My first encounter with such a failure involved a misaligned arm that led to an uneven stretch wrap. At the time, I thought it was a minor glitch, but repeated occurrences highlighted a flaw in our operational approach.
1.2 Component Wear and Tear
Data reveals that nearly 60% of orbital wrapper failures are due to worn-out parts like bearings, belts, or sensors. Below is a simple breakdown of commonly failing components:
Component | Average Lifespan | Warning Signs |
---|---|---|
Bearings | 2-5 years | Excessive noise, vibration |
Belts | 3-6 months | Visible cracks, inconsistent tension |
Sensors | 12-18 months | Intermittent signals, misalignment |
Regular inspection could mitigate these issues, but negligence often allows these failures to escalate.
1.3 Environmental Factors
The operational environment plays a significant role. Machines exposed to extreme temperatures, dust, or moisture face accelerated degradation. For instance, wrapping equipment operating in a dusty warehouse without protective enclosures can develop clogged sensors, leading to frequent shutdowns.
1.4 The Cost of Ignoring Warning Signs
Every failure begins with small warning signs: a subtle noise, a slight misalignment, or an unusual pause in operations. Ignoring these signs can result in catastrophic breakdowns. Here’s an example from my past:
- True: We conducted routine maintenance and identified a misaligned sensor, preventing a full system breakdown.
- False: Ignoring warning signs saves maintenance costs.
Ignoring minor problems can double repair costs later. By focusing on early detection, significant disruptions can be avoided.
1.5 Miscommunication in Operational Processes
Another overlooked factor in orbital stretch wrapper failure is miscommunication among team members. Operators may use the machine incorrectly due to unclear guidelines or lack of training. For instance, I once observed a colleague manually adjusting the wrapping tension, believing it would improve packaging stability. Instead, it caused the machine’s rollers to jam, leading to an extended downtime.
Here’s the fact breakdown:
- True: Providing clear training manuals and operational SOPs reduces misuse incidents significantly.
- False: Machines are designed to auto-correct operator errors, so training is unnecessary.
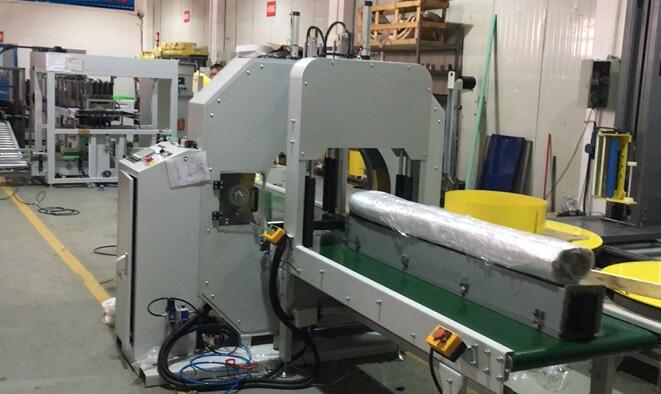
2. How Does Poor Maintenance Accelerate Machine Failures?
2.1 Why Is Maintenance Often Overlooked?
Let’s face it—maintenance isn’t glamorous. It’s tempting to skip scheduled upkeep to save time or meet production deadlines. However, in my experience, neglecting maintenance has a ripple effect. For example, failing to lubricate critical components regularly led to a roller seizure in one of our machines. The repair cost was three times higher than what regular maintenance would have cost.
2.2 The Financial Toll of Neglected Maintenance
Studies indicate that reactive maintenance costs are 50%-60% higher than preventive maintenance. Below is a cost comparison to illustrate the impact:
Maintenance Type | Average Cost Per Year | Downtime Impact |
---|---|---|
Preventive Maintenance | $1,000-$3,000 | Minimal |
Reactive Maintenance | $5,000-$10,000 | 2-5 days downtime per event |
This chart underscores how planning for maintenance can reduce both costs and downtime significantly.
2.3 Environmental Neglect
Machines that aren’t cleaned or shielded from environmental hazards wear out faster. Dust accumulation in motor vents or improper cooling systems are silent culprits of machine degradation. In one instance, I observed a warehouse that used fans instead of proper air circulation systems. Within six months, three orbital stretch wrappers needed costly motor replacements.
Here’s a key insight: maintaining a clean operational environment is just as critical as servicing the machine itself.
2.4 Conclusion
The relationship between maintenance and machine health is undeniable. From my experience, machines with robust preventive care not only last longer but also operate more efficiently. As operators, we have a choice—invest time and money in maintenance today or face exponentially higher costs tomorrow.
2.5 Fact Comparison on Maintenance Impact
- True: Preventive maintenance reduces unplanned downtimes by up to 70%.
- False: Maintenance schedules are only required for old or outdated machines.
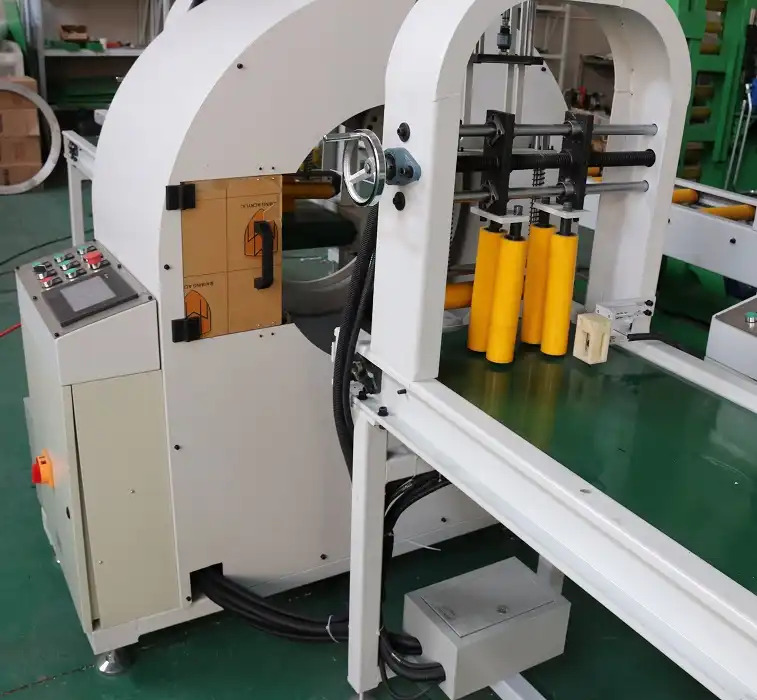
3. What Are the Consequences of Prolonged Machine Downtime?
3.1 How Downtime Impacts Productivity
When an orbital stretch wrapper goes offline, the immediate consequence is stalled operations. In my experience, even a two-hour delay in packaging production creates bottlenecks across multiple departments. Pallets pile up, shipments are delayed, and the ripple effect impacts customer satisfaction.
The productivity loss isn’t just about wasted hours. A single instance of downtime can disrupt synchronized workflows, leading to overtime labor costs and strained employee schedules. For instance, a mid-scale packaging operation I worked with faced an average 15% loss in daily output due to machine downtimes.
3.2 The Financial Impact of Downtime
Every minute of downtime has a dollar value. Here’s a table summarizing typical costs:
Downtime Duration | Cost Per Hour | Impact |
---|---|---|
1 Hour | $1,000-$5,000 | Missed production goals, late shipments |
8 Hours (Full Shift) | $10,000-$40,000 | Client penalties, labor overtimes |
Multiple Days | $50,000-$100,000+ | Lost contracts, damaged brand reputation |
Prolonged downtime doesn’t just increase repair costs; it risks long-term damage to relationships with key clients.
3.3 How Downtime Affects Team Morale
Beyond financial losses, downtime can demoralize your workforce. Employees grow frustrated when they’re unable to meet their goals due to equipment failures. I recall a time when a stretch wrapper malfunction caused extended delays in our warehouse. The stress on employees was palpable—they worked overtime, juggling manual packaging and client complaints. Ultimately, this led to lower morale and higher turnover.
Managers often overlook this intangible cost, but it’s crucial to recognize how machine reliability directly correlates to employee satisfaction and retention.
3.4 Dive Deeper into Downtime Mitigation
The good news? Downtime doesn’t have to be catastrophic. Proactive steps like predictive maintenance, remote monitoring systems, and robust training programs can drastically reduce occurrences.
Here’s a breakdown of effective strategies:
Strategy | Downtime Reduction (%) | Implementation Cost |
---|---|---|
Predictive Maintenance | Up to 50% | Moderate |
Remote Monitoring Systems | Up to 40% | High |
Operator Training Programs | Up to 25% | Low |
Investing in these measures early on saves more money and time in the long run.
3.5 Fact Comparison on Downtime
- True: Downtime costs can account for up to 20% of operational budgets in manufacturing industries.
- False: Replacing an orbital stretch wrapper is always cheaper than fixing it.
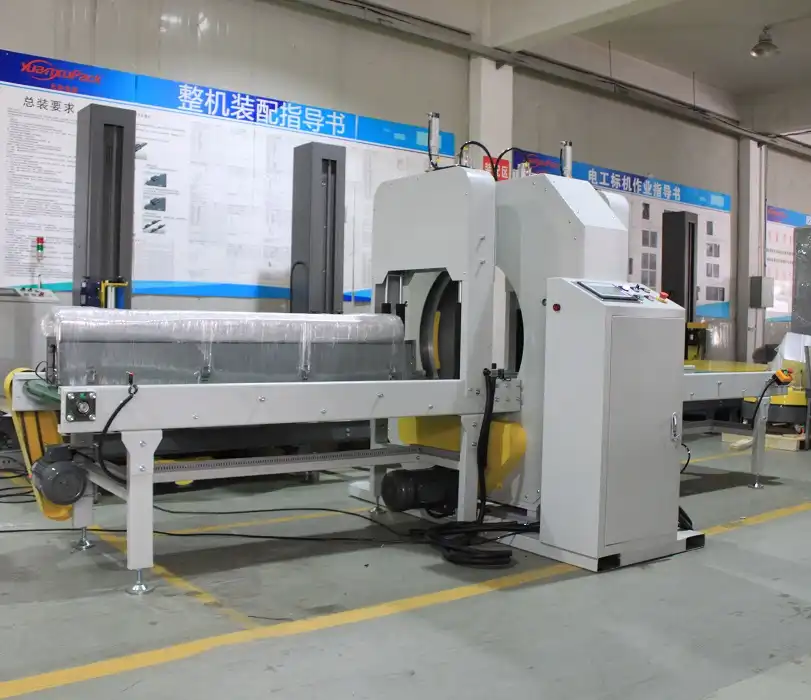
4. Which Strategies Can Prevent Orbital Stretch Wrapper Breakdowns?
4.1 How Preventive Maintenance Saves Costs
The key to minimizing breakdowns is consistent and proactive maintenance. Based on my observations, companies that adhered to strict maintenance schedules experienced 50% fewer breakdowns. Simple actions like lubricating components, inspecting for wear and tear, and updating software can extend a machine’s lifespan significantly.
4.2 Using Technology for Predictive Maintenance
Modern orbital stretch wrappers now come equipped with IoT-based monitoring systems that predict potential failures before they happen. Here’s a snapshot of how this technology works:
System Feature | Benefit |
---|---|
Real-Time Monitoring | Tracks performance metrics |
Predictive Analytics | Identifies potential failures |
Automatic Alerts | Notifies operators of anomalies |
By leveraging these systems, businesses can reduce downtime by as much as 40%.
4.3 The Importance of Choosing the Right Machine
Not all orbital stretch wrappers are created equal. Selecting a machine tailored to your specific operational demands reduces the risk of failure. For example, machines with adjustable wrapping speeds and customizable settings perform better under variable workloads.
Investing in the right machine is as critical as maintaining it. Cheap equipment often leads to higher long-term costs due to frequent breakdowns and lower efficiency.
4.4 Dive Deeper into Maintenance Strategies
For maximum efficiency, combine routine checks with data-driven maintenance. Here’s a recommended monthly checklist:
Task | Frequency | Responsible Team |
---|---|---|
Inspect Belts and Rollers | Weekly | Maintenance Staff |
Clean Sensors | Bi-Weekly | Operators |
Update Software | Monthly | IT and Maintenance |
This layered approach ensures minimal disruptions and optimal performance.
4.5 Fact Comparison on Preventive Strategies
- True: Implementing predictive technology can cut unplanned downtime by nearly half.
- False: Preventive maintenance schedules are unnecessary for new machines.
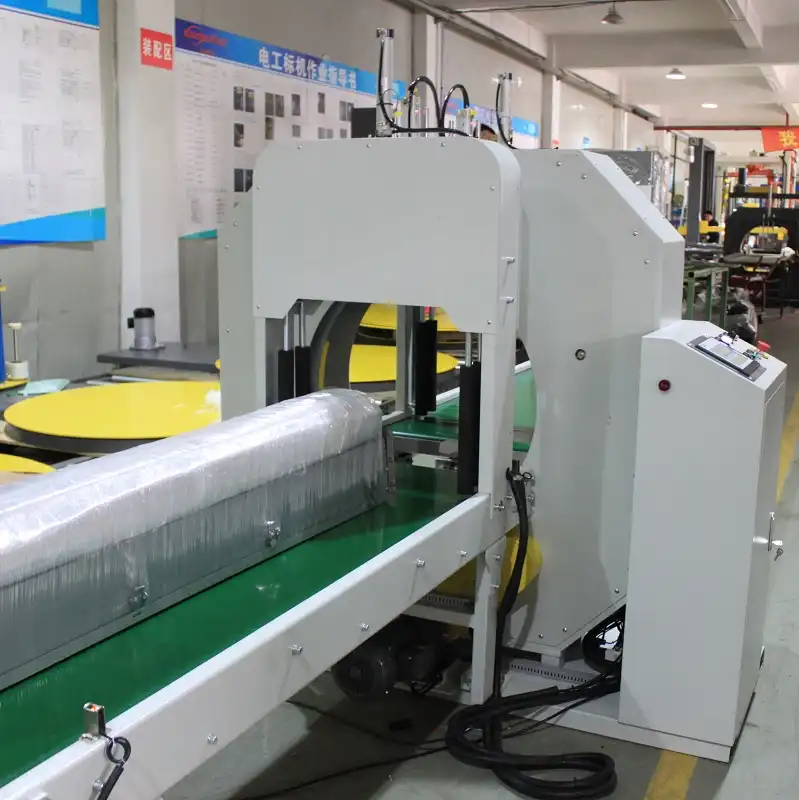
Conclusion
Orbital stretch wrapper failures are not just about mechanical issues—they are the result of preventable mistakes, overlooked maintenance, and operational missteps. By understanding the root causes, investing in operator training, and choosing compatible materials, businesses can significantly reduce downtime and improve overall efficiency.
[Claim]: Failure prevention isn’t an expense—it’s an investment in reliability, productivity, and long-term success.

Get Your Best Solution !