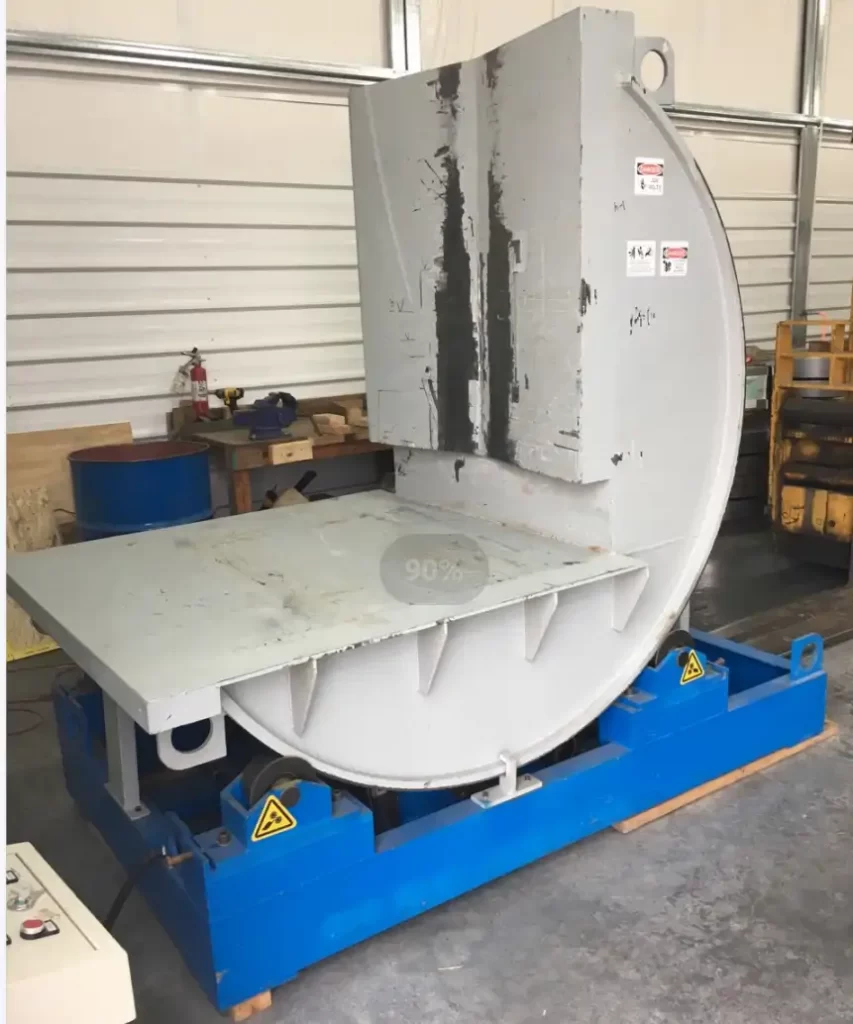
Mechanical upenders are indispensable in industrial operations, ensuring the safe and efficient rotation of heavy loads. However, like any machine, they are not immune to failures. These disruptions can have serious consequences, including production delays, costly repairs, and safety hazards. Understanding the causes and potential solutions for mechanical upender failures is essential for maintaining optimal operational efficiency and safety standards.
When mechanical upenders fail, the issue often stems from a combination of wear and tear, improper usage, and inadequate maintenance. In industries where downtime equates to financial loss, learning to anticipate and mitigate these failures becomes a strategic priority.
The failures of mechanical upenders are more than mere technical issues; they reflect how well a facility integrates equipment management into its operations. By delving into the root causes, identifying warning signs, and implementing preventive measures, businesses can protect their investments and enhance their workflow reliability.
Claim:Identifying the common failures and addressing them proactively ensures extended operational life and reduced maintenance costs for mechanical upenders.
1. What Are the Common Causes of Mechanical Upender Failure?
1.1 Component Wear and Tear
Mechanical upenders are subjected to constant pressure and load handling, leading to inevitable wear and tear. This degradation primarily affects critical parts such as hydraulic systems, pivot bearings, and control mechanisms. If unchecked, minor deterioration can escalate into significant malfunctions, compromising safety and functionality. For example, a study indicated that 45% of upender failures are directly related to overused bearings and seals, which often operate under extreme pressure.
1.2 Hydraulic System Leaks and Performance Issues
Leaking hydraulic systems are a prevalent problem in mechanical upenders. Factors like incorrect oil levels, contamination, or damaged seals can cause a decline in hydraulic efficiency. Below is a table showcasing common hydraulic issues and their frequency:
Hydraulic Issue | Frequency (%) |
---|---|
Seal Damage | 30 |
Fluid Contamination | 25 |
Incorrect Oil Viscosity | 20 |
Improper Hydraulic Pressure | 25 |
Such issues demand immediate attention, as reduced hydraulic pressure directly affects the lifting capacity of the upender. Ignoring these problems could result in operational breakdowns.
1.3 Control System Malfunctions
Electrical and control system malfunctions are another common cause of mechanical upender failure. Poorly calibrated sensors or wiring faults often lead to erratic performance. As automation becomes integral in industrial systems, the complexity of control units increases, amplifying the risk of breakdowns. A sudden error in the control system could halt operations and potentially damage both the equipment and the load.
1.4 Load Mismanagement and Dive Deeper
Mismanagement of loads, such as exceeding the upender’s capacity or improper positioning, significantly increases the likelihood of mechanical failures. The strain on structural components grows exponentially when loads are unevenly distributed, resulting in mechanical stress and damage over time.
Data Table: Load Handling Issues
Mismanagement Issue | Failure Rate Impact (%) |
---|---|
Exceeding Capacity | 40 |
Uneven Load Distribution | 35 |
Insufficient Operator Training | 25 |
This table emphasizes the importance of proper operator training and adherence to the machine’s capacity limits.
1.5 Two Fact Statement
- True: Regular inspections of hydraulic systems can extend an upender’s lifespan by up to 30%.
- False: Overloading mechanical upenders by 10% does not affect their performance.
The truth lies in proactive maintenance, while overloading always exacerbates mechanical stress and reduces operational reliability.
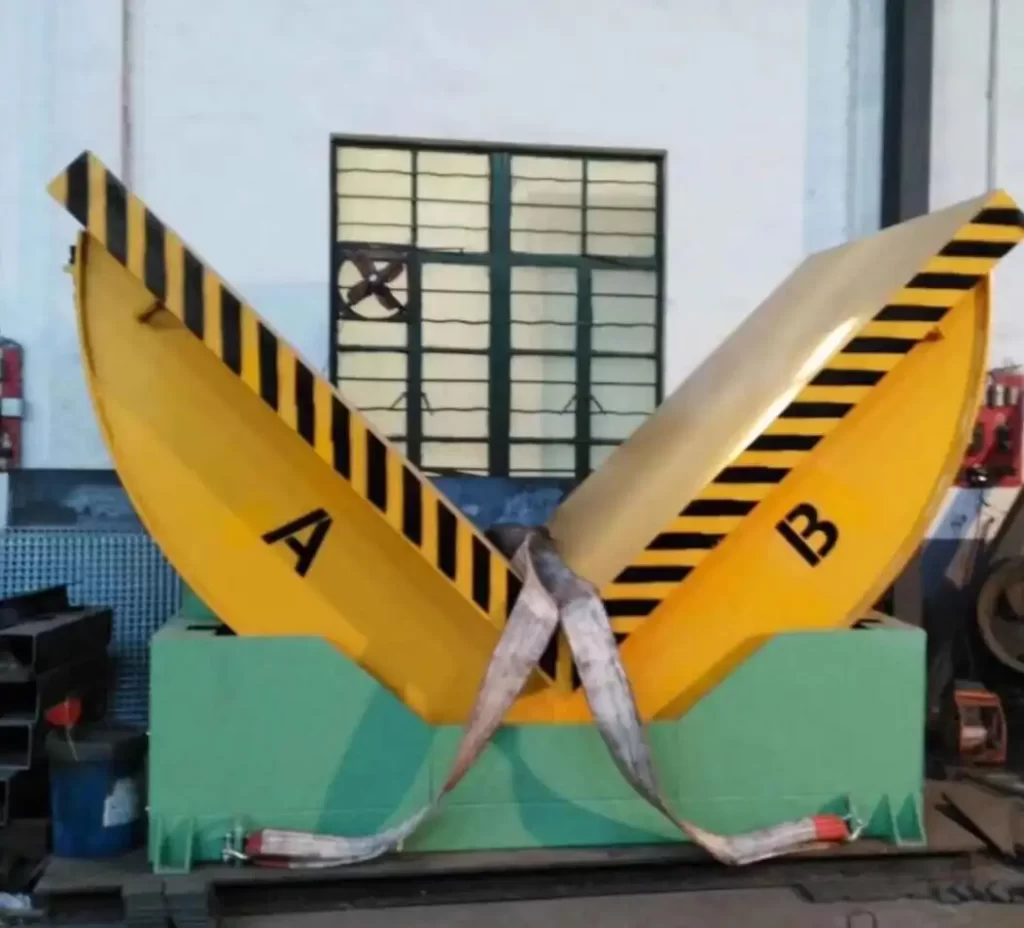
2. How Can Regular Maintenance Prevent Mechanical Failures?
2.1 Routine Inspection and Diagnostics
Routine inspections are a cornerstone of preventive maintenance, offering early detection of potential problems. By evaluating components like hydraulic systems, bearings, and control units, operators can identify wear before it causes significant downtime. Regular diagnostics also help track machine performance, ensuring that the equipment remains within operational parameters. For instance, companies that implement monthly maintenance schedules reduce unexpected failures by 35%, according to industry reports.
2.2 Lubrication and Replacement Schedules
One of the simplest yet most effective maintenance practices is proper lubrication. Insufficient or improper lubrication accelerates wear and tear, especially in bearings and moving parts. Below is a recommended lubrication schedule for mechanical upenders:
Component | Frequency | Lubricant Type |
---|---|---|
Bearings | Weekly | High-temperature grease |
Hydraulic Pistons | Monthly | Synthetic oil |
Pivot Points | Bi-weekly | Multipurpose grease |
Failing to adhere to these schedules results in increased friction, heat, and component degradation.
2.3 Dive Deeper: Predictive Maintenance Strategies
Predictive maintenance employs advanced tools like vibration analysis and thermal imaging to forecast potential failures. This proactive approach uses data analytics to pinpoint vulnerabilities, minimizing costly repairs.
Predictive Maintenance Benefits Table
Benefit | Average Savings (%) |
---|---|
Reduced Downtime | 50 |
Lower Maintenance Costs | 30 |
Extended Equipment Lifespan | 40 |
Implementing predictive strategies transforms maintenance from reactive to strategic, enhancing both efficiency and reliability.
2.4 Two Fact Statement
- True: Predictive maintenance can reduce downtime by half in industrial operations.
- False: Lubrication intervals can be skipped without affecting machine performance.
Skipping lubrication accelerates part failure, proving the importance of consistency in routine maintenance.
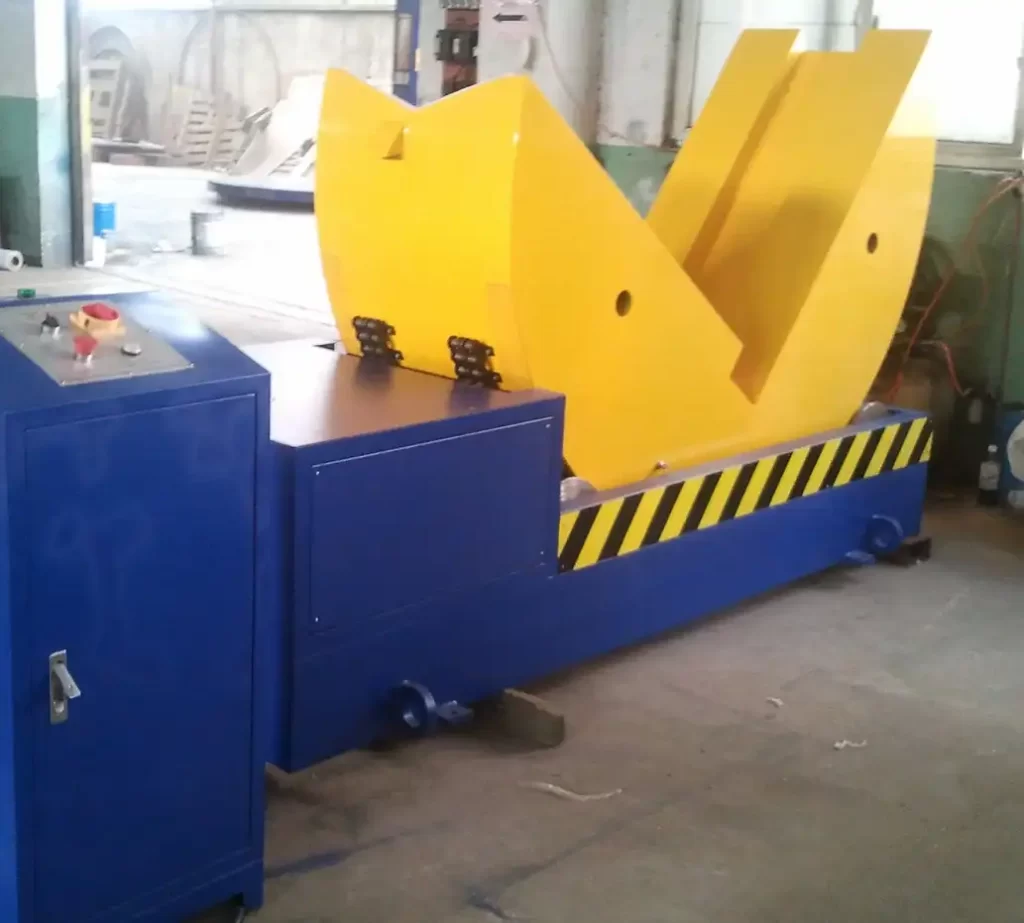
3. What Are the Long-Term Impacts of Neglecting Mechanical Upenders?
3.1 Escalating Repair Costs
Neglecting mechanical upenders often leads to cascading failures, where minor issues develop into costly repairs. For instance, replacing a single hydraulic seal may cost $200, but ignoring it can cause system-wide damage, leading to expenses upwards of $5,000. The financial burden grows exponentially when downtime and labor costs are factored in.
3.2 Declining Operational Efficiency
Equipment failures disrupt workflows, lowering overall efficiency. Below is a comparison of operational efficiency between facilities that implement regular maintenance and those that neglect it:
Maintenance Strategy | Average Downtime (%) | Efficiency (%) |
---|---|---|
Regular Maintenance | 5 | 95 |
Neglected Maintenance | 25 | 75 |
These statistics underline how neglected maintenance reduces productivity, creating bottlenecks across operations.
3.3 Dive Deeper: Safety Hazards and Liability Risks
Mechanical upender failures also pose significant safety risks. For example, a failed load rotation can cause equipment to collapse, endangering personnel and damaging property.
Key Safety Risks Table
Risk Type | Impact Level |
---|---|
Equipment Collapse | High |
Hydraulic Fluid Leaks | Moderate |
Load Mismanagement | Severe |
These risks not only threaten workers but also expose companies to liability claims, emphasizing the importance of proactive equipment management.
3.4 Two Fact Statement
- True: Neglecting maintenance can lead to liabilities costing up to $100,000 per incident.
- False: Regular inspections guarantee that no failures will ever occur.
While inspections minimize risks, no system is entirely immune to occasional breakdowns.
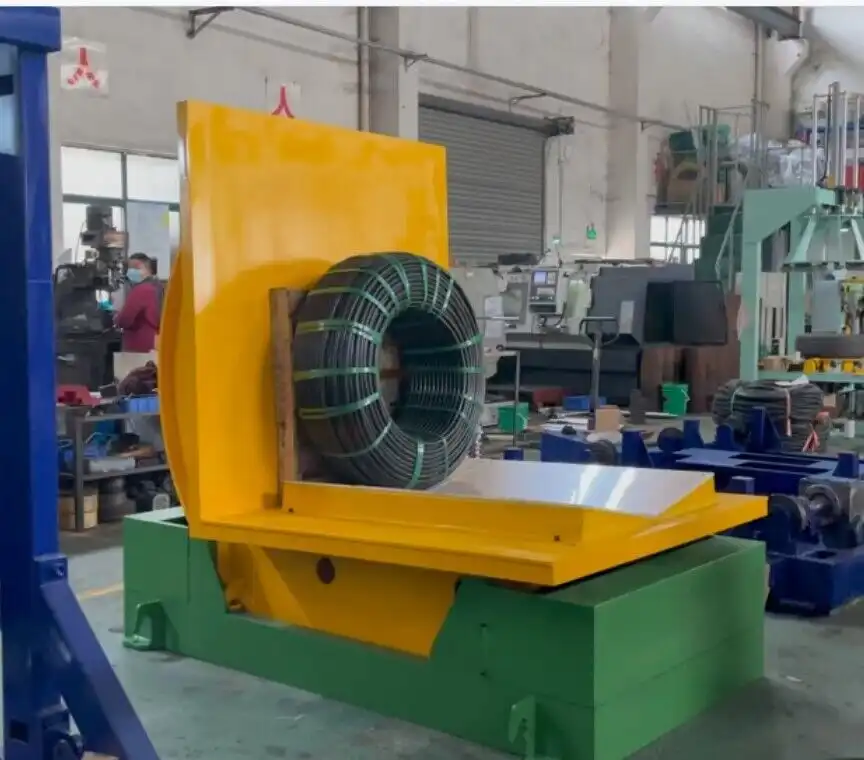
4. How to Build a Proactive Strategy Against Failure?
4.1 Operator Training and Competency
Training operators to handle mechanical upenders correctly is a critical first step in preventing failures. Skilled operators can identify early signs of malfunction and ensure that equipment is not overloaded or misused. For instance, facilities with certified operator training programs report a 20% reduction in operational errors. This underscores the value of investing in human capital as part of a broader failure-prevention strategy.
4.2 Establishing Maintenance Protocols
Well-defined maintenance protocols provide a structured approach to equipment care. These include checklists for daily inspections, monthly diagnostics, and quarterly overhauls. Below is an example of a maintenance protocol:
Maintenance Task | Frequency | Responsible Party |
---|---|---|
Inspect Hydraulic Fluid | Daily | Operator |
Test Control Systems | Monthly | Maintenance Team |
Replace Worn Bearings | Quarterly | Specialist |
Adopting such protocols ensures consistency in maintenance practices, reducing the likelihood of oversight.
4.3 Dive Deeper: Leveraging Technology for Preventive Maintenance
Technology can play a pivotal role in building a proactive strategy. Equipment sensors, IoT connectivity, and centralized maintenance software enable real-time monitoring and diagnostics. This allows operators to detect and address potential issues before they escalate.
Benefits of Technology Integration Table
Technology Used | Key Benefit |
---|---|
IoT Sensors | Real-time Data |
Centralized Maintenance Apps | Task Scheduling |
Predictive Analytics Tools | Early Failure Detection |
Implementing these tools transforms maintenance from reactive troubleshooting to intelligent prevention.
4.4 Two Fact Statement
- True: IoT-enabled sensors can reduce unexpected failures by 40%.
- False: Maintenance protocols do not impact overall equipment efficiency.
The efficiency of mechanical upenders significantly depends on adherence to systematic maintenance procedures.
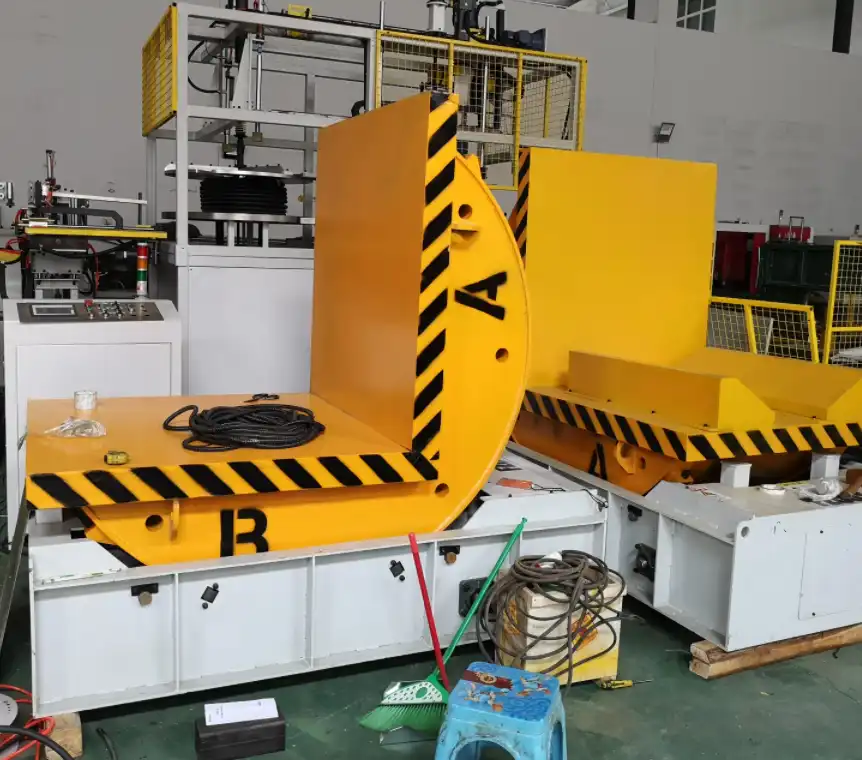
Conclusion
Understanding and addressing mechanical upender failures require a blend of proper maintenance, skilled operation, and the integration of modern technology. By identifying root causes, establishing consistent maintenance practices, and leveraging predictive tools, businesses can minimize downtime and enhance safety.
Claim:Proactive measures against mechanical upender failures not only extend the lifespan of equipment but also improve productivity and operational reliability.

Get Your Best Solution !