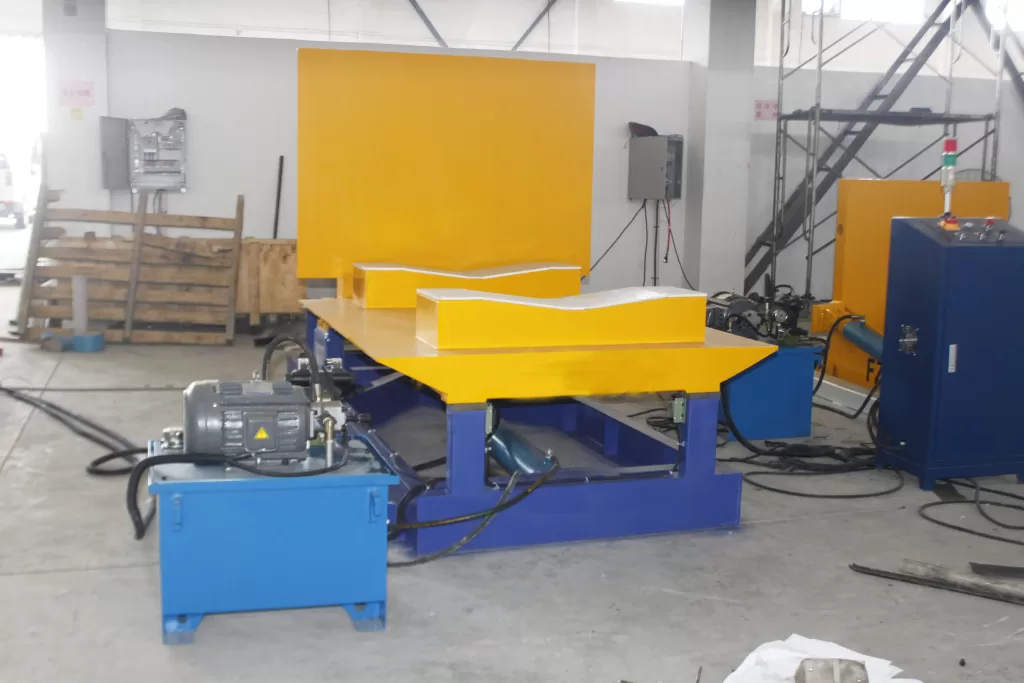
Hydraulic upenders are indispensable in industrial operations, seamlessly flipping heavy loads with efficiency and precision. However, even the most robust machines can encounter failures, and when they do, the consequences can disrupt workflows, increase downtime, and incur hefty costs. Understanding the causes and addressing the issues promptly can make a significant difference in operational efficiency.
Failures in hydraulic upenders don’t happen in isolation; they often signal underlying mechanical, hydraulic, or maintenance concerns. Without a proper diagnosis, repeated breakdowns can snowball into long-term reliability issues. This article aims to explore the common causes, effective solutions, and preventive strategies for hydraulic upender failures.
With a clear understanding of the challenges and solutions, you can keep your equipment running smoothly and ensure uninterrupted productivity. Let’s dive deeper into the factors that impact hydraulic upenders and how to safeguard against failures.
- 1. What Are the Common Causes of Hydraulic Upender Failure?
- 2. How Can Operational Stress Lead to Equipment Breakdowns?
- 3. What Preventive Maintenance Practices Can Reduce Hydraulic Upender Failures?
- 4. How Does Addressing Failures Improve Productivity and Reduce Costs?
- 5. What Are the Warning Signs to Address Before Complete Hydraulic Upender Failure?
- 6. How Can You Build a Failure-Resistant Maintenance Plan?
- Conclusion
1. What Are the Common Causes of Hydraulic Upender Failure?
Inadequate Maintenance Practices
Hydraulic upenders rely on precise movements, which demand regular upkeep. Over time, neglecting maintenance tasks such as lubrication, fluid checks, and filter replacements can lead to issues like overheating or hydraulic fluid contamination. Small lapses in these areas might seem insignificant, but they accumulate to create system-wide failures.
Early Signs of Deterioration
Equipment often gives subtle warnings before a breakdown. These include unusual noises, sluggish movements, or inconsistent hydraulic pressure. Paying attention to these early signs is key to addressing the problem before it worsens.
![Image of a technician inspecting hydraulic components with a tool]
Component Wear and Tear
The constant handling of heavy loads places significant stress on the components, particularly the hydraulic cylinders, seals, and valves. Prolonged use without component replacements exacerbates wear and tear, leaving the machine vulnerable to sudden failures.
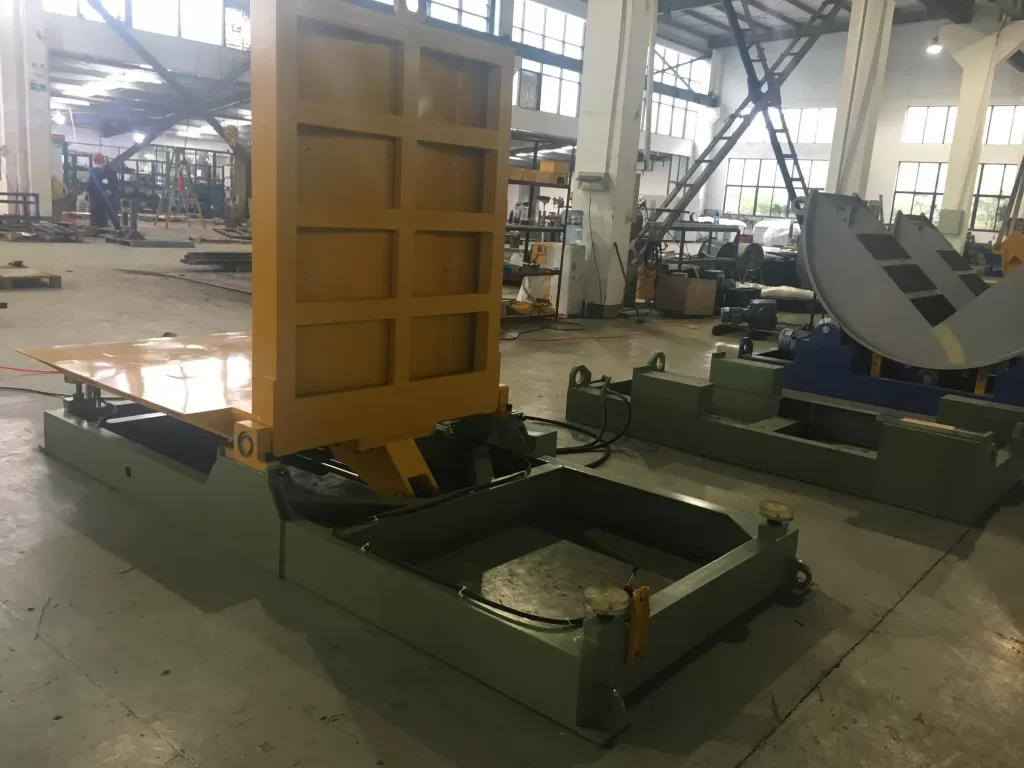
2. How Can Operational Stress Lead to Equipment Breakdowns?
Overloading the System
Exceeding the weight capacity of a hydraulic upender can cause permanent damage. Operators sometimes push equipment limits to maximize productivity, but this habit strains the motor and hydraulic system. A single instance of overloading may not lead to immediate failure, but repeated instances create a cumulative risk.
Environmental Factors
Operating conditions such as extreme temperatures, excessive dust, or corrosive environments play a significant role in hydraulic failure. These factors speed up material degradation, requiring more frequent inspections to maintain operational integrity.
Misalignment During Operations
Precise alignment is crucial for hydraulic upenders. If a load is not positioned correctly, it puts undue pressure on certain components, creating an imbalance that accelerates wear. This misalignment often results in jerky movements or uneven flipping, directly contributing to breakdowns.
![Image showing an example of misaligned loading on a hydraulic upender]
Long-Term Consequences of Operational Stress
Prolonged stress without intervention reduces the lifespan of hydraulic equipment, leading to escalating repair costs. Additionally, frequent failures disrupt productivity, creating cascading delays in operations that affect overall output.
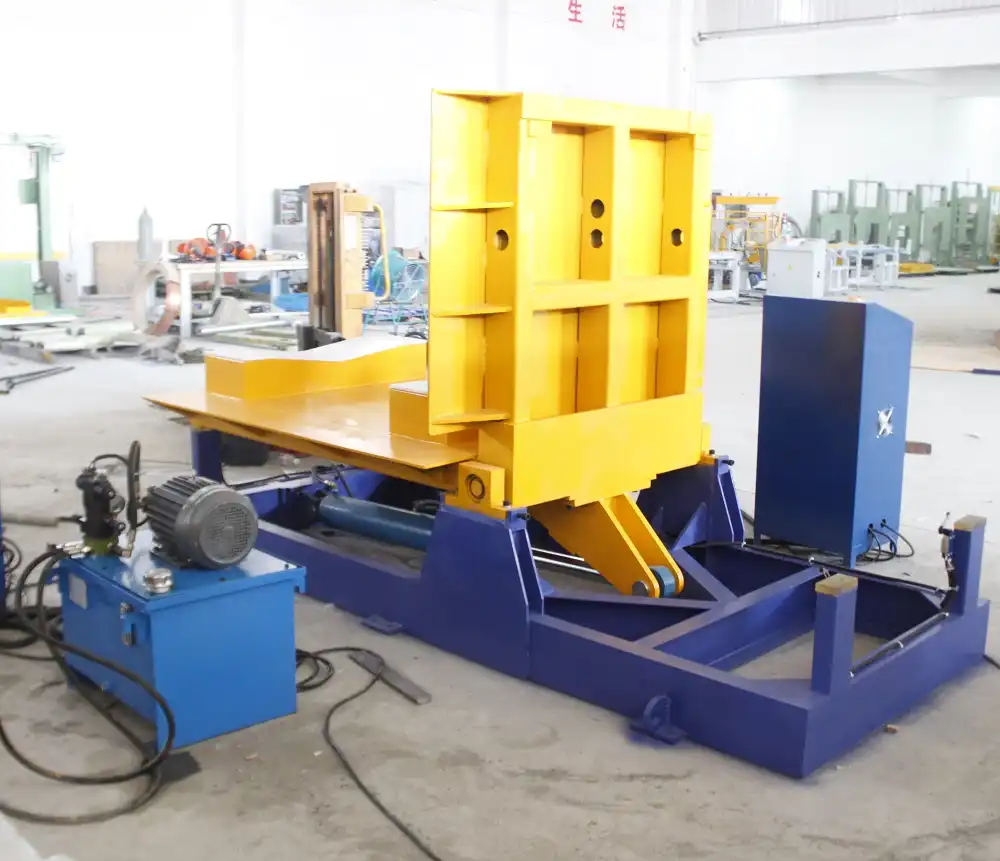
3. What Preventive Maintenance Practices Can Reduce Hydraulic Upender Failures?
Regular Inspection and Diagnostics
Consistent inspections are the cornerstone of preventive maintenance. Using diagnostic tools to monitor hydraulic fluid levels, pressure consistency, and the condition of mechanical parts can catch problems before they escalate. Scheduling routine checks ensures that minor issues are addressed promptly.
Fluid Quality Management
Hydraulic fluid plays a vital role in the smooth operation of upenders. Contaminated or degraded fluid can cause system inefficiencies and accelerate component wear. Regular fluid analysis, combined with timely replacement, ensures that the hydraulic system remains in optimal condition.
![Image of a technician testing hydraulic fluid for contaminants]
Training for Operators
Operator errors often lead to avoidable damage. Providing thorough training on load limits, operational protocols, and emergency response procedures reduces the likelihood of mistakes. Trained operators are better equipped to identify unusual machine behavior and take corrective action.
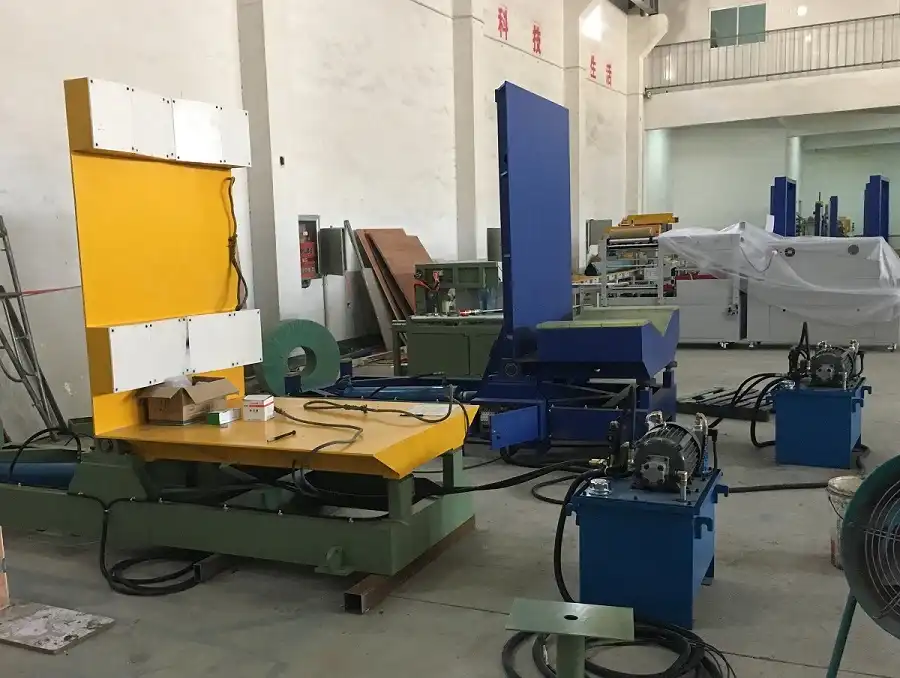
4. How Does Addressing Failures Improve Productivity and Reduce Costs?
Minimizing Downtime with Proactive Repairs
Addressing failures immediately prevents prolonged downtime. Quick identification and repair of issues ensure that operations resume without significant delays. Investing in spare parts and a well-equipped maintenance team can further expedite repairs.
Enhanced Equipment Lifespan
Preventive measures and timely interventions reduce the cumulative wear on hydraulic upenders. By extending the lifespan of the equipment, businesses avoid frequent replacements and maximize the return on their investment.
Lower Operational Costs
Failures are costly—not only due to repairs but also because of lost productivity and potential penalties for delayed deliveries. Regular maintenance and quick fixes reduce these expenses, leading to more predictable operational budgets.
![Image showing workers repairing hydraulic equipment in a factory setting]
Positive Ripple Effect on Operations
A reliable hydraulic upender contributes to smoother workflows across departments. With fewer interruptions, teams can maintain consistent productivity levels, fostering a culture of efficiency and reliability in the workplace.
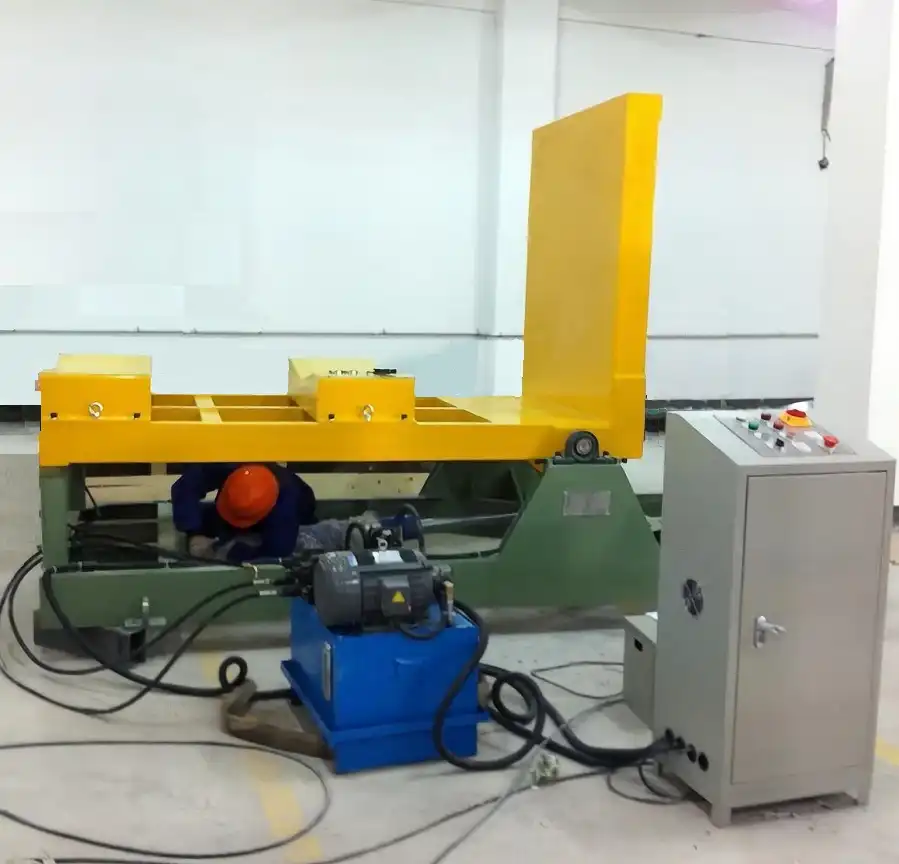
5. What Are the Warning Signs to Address Before Complete Hydraulic Upender Failure?
Unusual Noises During Operation
Hydraulic upenders often emit warning signs in the form of unusual noises. Clanking, hissing, or grinding sounds can indicate issues such as air in the hydraulic lines, worn-out bearings, or misaligned components. Addressing these noises early can prevent major failures.
Temperature Fluctuations in the System
Overheating is a common sign of stress in hydraulic systems. If the fluid temperature rises excessively, it can degrade hydraulic oil and damage internal components. Monitoring temperature variations and resolving overheating issues can save the equipment from long-term damage.
![Thermal image of overheating hydraulic components during operation]
Loss of Precision and Control
Difficulty in flipping loads accurately or experiencing irregular movements suggests hydraulic pressure inconsistencies. These signs often point to leaking seals or malfunctioning valves that require immediate attention to avoid operational hazards.
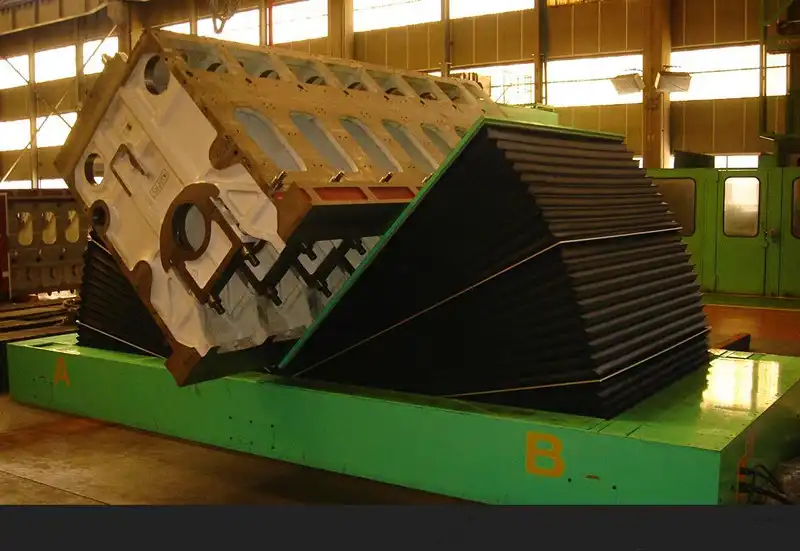
6. How Can You Build a Failure-Resistant Maintenance Plan?
Incorporating Predictive Maintenance Tools
Predictive maintenance relies on sensors and analytics to forecast potential issues. By monitoring hydraulic pressure, fluid quality, and component wear in real time, businesses can predict and address failures before they occur.
Partnering with Reliable Service Providers
Collaborating with trusted service providers ensures access to expertise and spare parts. Professional maintenance teams are better equipped to handle complex repairs, ensuring a swift resolution to issues.
Establishing a Comprehensive Log
Documenting all maintenance activities and failures helps track patterns and prevent repeat issues. A detailed log serves as a reference for both operators and technicians, streamlining troubleshooting and repair processes.
![Image of a technician updating a digital maintenance log on a tablet]
Long-Term Benefits of a Proactive Approach
A robust maintenance plan not only minimizes downtime but also improves equipment reliability, reducing overall operating costs. This proactive approach ensures that hydraulic upenders deliver consistent performance, even under demanding conditions.
Conclusion
Hydraulic upender failures can disrupt industrial operations, but they are not inevitable. By understanding the common causes, addressing warning signs early, and implementing preventive maintenance strategies, businesses can mitigate risks and enhance equipment reliability.
With informed maintenance practices and advanced diagnostic tools, hydraulic upenders can continue to support seamless workflows, safeguarding productivity and reducing costs.

Get Your Best Solution !