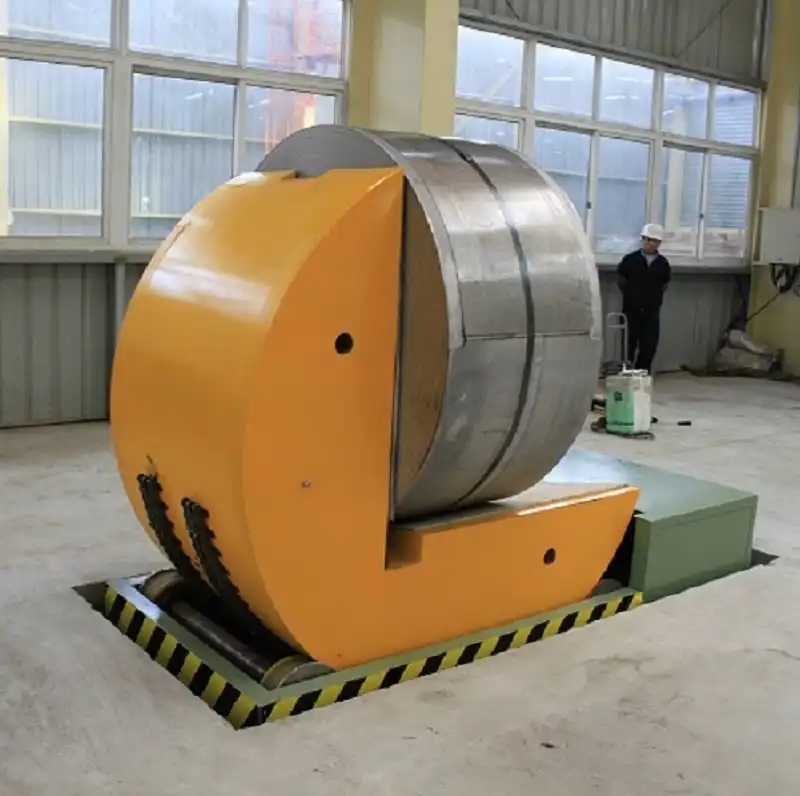
In the realm of heavy industry, coil turnstiles play an essential role, seamlessly facilitating the handling and storage of steel coils. Their precision, reliability, and durability directly influence operational efficiency and safety. However, what happens when these machines fail? Many businesses overlook the warning signs until it’s too late, leading to costly downtime and safety hazards that could have been prevented.
It’s easy to take these machines for granted when they’re functioning well, but the reality is that coil turnstile failure is a significant risk factor for businesses. Whether due to wear and tear, improper maintenance, or misaligned system designs, these failures can spiral into larger operational and financial issues. To mitigate these risks, it’s crucial to understand the causes, preventative measures, and solutions when failures occur.
Failures don’t just disrupt operations—they jeopardize worker safety, inflate maintenance costs, and weaken your supply chain reliability. But by adopting a proactive approach, supported by accurate diagnostics and maintenance protocols, you can turn potential failures into opportunities to enhance your processes.
[Claim] Coil turnstile failure is preventable with the right mix of knowledge, planning, and preventative measures, and addressing it effectively can significantly reduce downtime and operational costs.
1. How Do Coil Turnstiles Fail and Why Does It Matter?
1.1 Common Causes of Coil Turnstile Failures
Coil turnstile failures rarely occur out of the blue. They are often the result of gradual degradation caused by factors like mechanical wear, improper lubrication, and overloading. Many operators unknowingly push their turnstiles beyond their designed capacity, causing unnecessary stress on critical components like bearings and axles. Environmental factors, such as exposure to extreme temperatures or corrosive materials, further exacerbate these vulnerabilities.
1.2 How Maintenance Gaps Impact Performance
A study analyzing industrial turnstile failures found that over 60% of breakdowns could be traced back to inconsistent or incomplete maintenance schedules. Inadequate lubrication, skipped inspections, and the use of substandard replacement parts are recurring issues. These lapses not only reduce performance but also increase the likelihood of sudden, catastrophic failures that halt production entirely.
Maintenance Gap | Impact |
---|---|
Skipped Lubrication Cycles | Increased friction and wear |
Infrequent Inspections | Missed early signs of component failure |
Use of Substandard Components | Reduced lifespan of turnstile parts |
1.3 Top Indicators of Imminent Failure
Recognizing early warning signs can make a difference between minor downtime and major losses. Look out for unusual vibrations, erratic movement, or grinding noises during operation. These often signal wear in internal components. Additionally, inconsistent handling speeds or unexpected system lags indicate that the turnstile is struggling to perform under its current workload.
1.4 Misalignment in Design: A Hidden Culprit
Design flaws, while less obvious, play a critical role in turnstile failure. Misaligned frames or improperly balanced coils can stress the machine unevenly, causing premature damage to structural components. This is particularly common when machines are retrofitted without considering the original specifications. Proper alignment during setup and regular recalibration can help mitigate this issue.
1.5 Fact Check: Which Failure Scenarios Are True?
True: Overloading a coil turnstile consistently shortens its lifespan by causing undue stress on its mechanical components.
False: Regular lubrication alone is enough to prevent failures. While it’s essential, lubrication must be combined with comprehensive inspections and proper component handling.
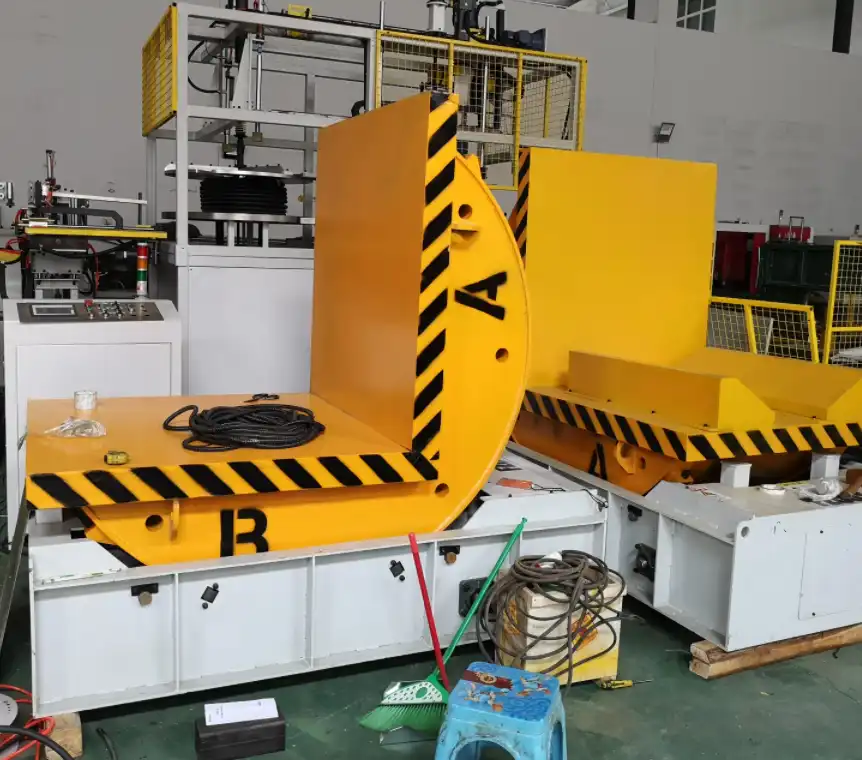
2. Can Predictive Maintenance Prevent Coil Turnstile Failures?
2.1 Benefits of Predictive Technologies
Predictive maintenance leverages advanced technologies like IoT sensors and machine learning algorithms to monitor equipment performance in real time. These tools detect anomalies and provide early warnings before a failure occurs. For instance, vibration sensors can pinpoint unusual patterns in bearing movement, signaling the need for maintenance. By implementing predictive systems, companies can reduce unplanned downtime by up to 40% and maintenance costs by 30%.
2.2 How IoT Sensors Detect Early Signs of Failure
IoT sensors collect vast amounts of data from coil turnstiles, tracking key performance indicators such as temperature, vibration, and load distribution. These sensors provide actionable insights, enabling technicians to address minor issues before they escalate into major failures.
Sensor Type | Function | Early Warning Sign Detected |
---|---|---|
Vibration Sensors | Measure mechanical oscillations | Bearing misalignment or wear |
Thermal Sensors | Monitor heat levels | Overheating due to friction or stress |
Load Sensors | Track coil weight distribution | Uneven loading causing structural stress |
2.3 A Cost-Benefit Analysis of Predictive vs. Reactive Maintenance
The financial advantages of predictive maintenance far outweigh its initial investment costs. A study by Deloitte reveals that for every dollar spent on predictive tools, industries save $5 in maintenance and downtime costs. Reactive maintenance, on the other hand, often leads to inflated expenses due to emergency repairs and prolonged production delays.
2.4 What Happens When Maintenance Protocols Are Ignored?
Ignoring maintenance protocols not only increases the risk of failures but also exposes businesses to safety liabilities and operational inefficiencies. For example, failing to address warning signs such as abnormal vibrations can result in component breakdowns that shut down operations for days. Moreover, neglected systems often operate inefficiently, consuming more energy and reducing overall productivity.
2.5 Fact Check: Are Predictive Systems 100% Reliable?
True: Predictive maintenance significantly reduces the likelihood of unplanned downtime by identifying potential failures in advance.
False: Predictive systems eliminate the need for routine manual inspections. While highly effective, these systems should complement, not replace, traditional maintenance practices.
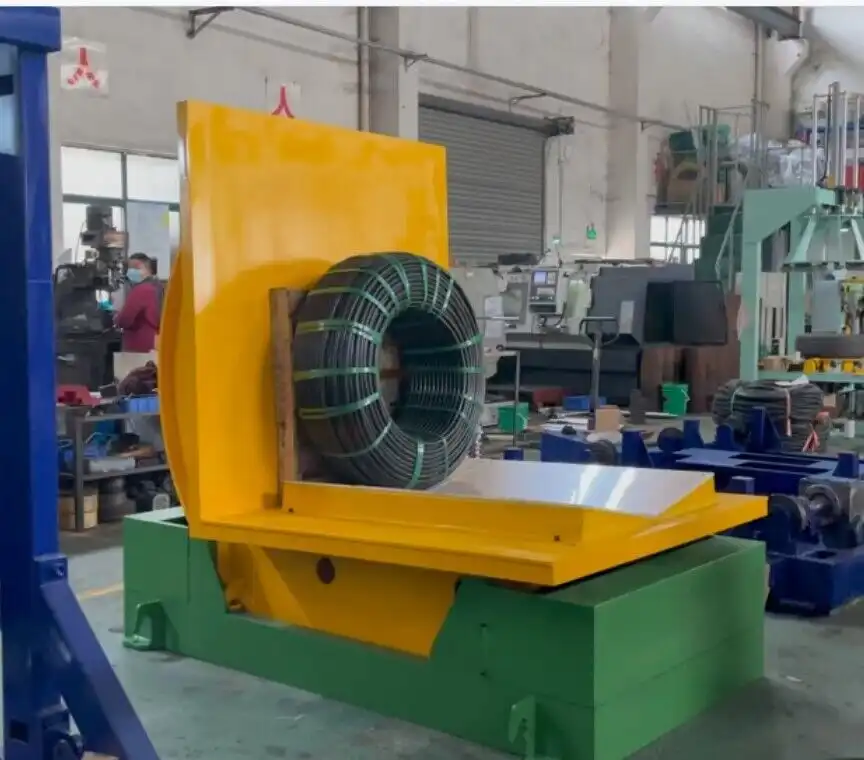
3. What’s the Cost of Ignoring Turnstile Maintenance?
3.1 Hidden Costs of Downtime in Steel Manufacturing
The financial impact of downtime extends far beyond immediate repair costs. When a coil turnstile fails, production schedules are disrupted, resulting in delayed shipments and dissatisfied customers. A 2023 study showed that downtime in steel manufacturing costs an average of $22,000 per hour, excluding the potential reputational damage from unmet client deadlines.
Impact | Cost Per Incident |
---|---|
Delayed Production | $15,000-$50,000 |
Emergency Repairs | $5,000-$20,000 |
Customer Penalties | $10,000-$30,000 |
3.2 How Neglected Maintenance Inflates Operational Costs
Neglected maintenance doesn’t just increase repair bills; it affects energy efficiency and equipment lifespan. When turnstiles operate under suboptimal conditions, they consume up to 20% more energy, raising utility bills. Additionally, recurring breakdowns shorten the overall lifecycle of the equipment, leading to premature replacement costs.
3.3 The Role of Training in Minimizing Failures
Proper training for operators is essential to minimize the risk of coil turnstile failures. Misuse or improper handling often stems from a lack of understanding of the machine’s capabilities and limitations. Training sessions should focus on operational guidelines, troubleshooting basics, and recognizing early warning signs of failure. Companies that prioritize training see a 25% reduction in equipment-related accidents and breakdowns.
3.4 When to Upgrade: Balancing Cost vs. Efficiency Gains
Older coil turnstiles, while seemingly functional, may lack the efficiency and reliability of modern systems. Upgrading to advanced models equipped with predictive maintenance capabilities can save businesses money in the long term. However, the decision to upgrade should weigh the upfront cost against the potential savings in energy, labor, and downtime.
3.5 Fact Check: Can Downtime Be Fully Eliminated?
True: Proactive maintenance and predictive technologies can significantly reduce downtime and operational interruptions.
False: It’s possible to achieve zero downtime. While it can be minimized, unforeseen events such as power outages or natural disasters may still disrupt operations.
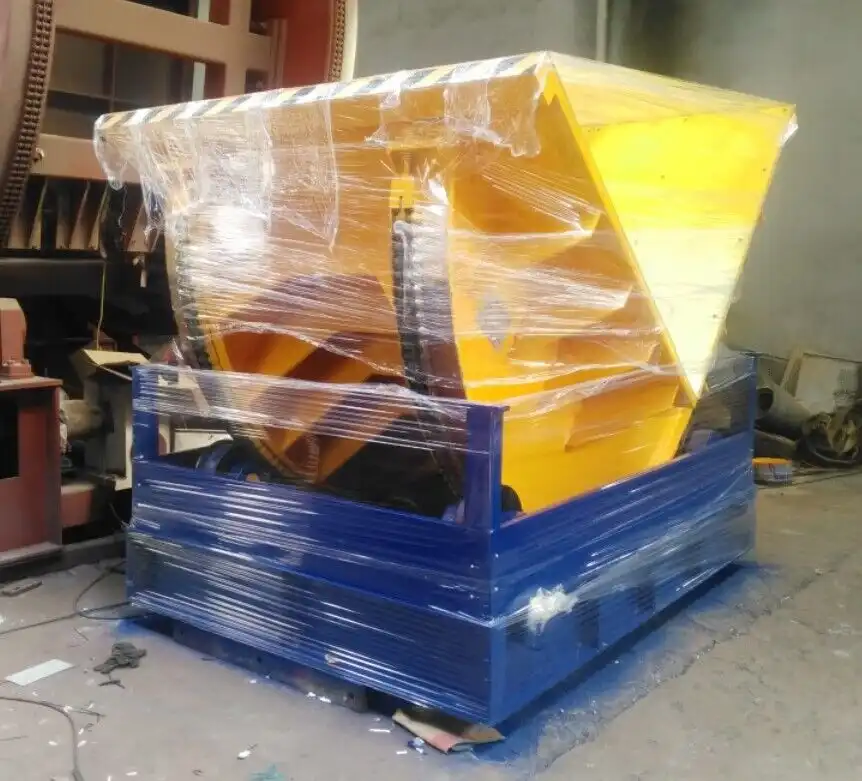
4. What Are the Best Practices for Coil Turnstile Longevity?
4.1 Routine Checks to Reduce Wear and Tear
Routine checks are the cornerstone of extending the lifespan of coil turnstiles. Regular inspections help identify early signs of wear, such as loosened bolts, degraded bearings, or misaligned frames. These small issues, if caught early, can be addressed with minimal downtime, saving significant costs over time. Scheduling daily visual checks and monthly deep inspections ensures the turnstile operates efficiently and safely.
4.2 How to Design a Fail-Proof Maintenance Schedule
A fail-proof maintenance schedule incorporates a mix of predictive and preventive measures. Start by analyzing the machine’s usage patterns and workload demands to create a customized maintenance calendar. For instance, high-capacity turnstiles may require weekly lubrication and bi-annual component replacements. Advanced scheduling software can automate reminders and track the performance metrics for better oversight.
Maintenance Task | Frequency | Action Required |
---|---|---|
Lubrication | Weekly | Apply manufacturer-recommended lubricant |
Component Inspection | Monthly | Check for wear or damage |
Calibration of Sensors | Quarterly | Ensure accurate data collection |
Full System Overhaul | Annually | Replace critical parts and recalibrate |
4.3 The Role of Technology in Extending Equipment Life
Technology has revolutionized maintenance practices, making it easier to extend the operational lifespan of equipment. IoT-enabled systems monitor performance parameters in real time, providing actionable insights to prevent wear and tear. For instance, automated alerts can notify technicians when the turnstile exceeds safe operating temperatures or vibration levels. Companies using these technologies report a 35% increase in equipment lifespan compared to traditional maintenance methods.
4.4 Strategies to Minimize Human Error in Equipment Handling
Human error remains one of the leading causes of coil turnstile failures. To address this, companies should invest in comprehensive operator training programs and intuitive user interfaces. Advanced systems with fail-safes, such as automatic shut-off mechanisms, can further reduce risks. Additionally, creating standardized operating procedures (SOPs) ensures that all operators follow consistent practices, minimizing handling errors.
4.5 Fact Check: Which Best Practices Are Most Effective?
True: Real-time monitoring systems significantly improve maintenance accuracy by providing precise performance data.
False: Routine visual inspections are unnecessary if predictive maintenance systems are installed. Both approaches are complementary and should be used together for optimal results.

Conclusion
Coil turnstile failures pose significant risks to industrial operations, from financial losses to safety hazards. However, with a proactive approach that combines routine maintenance, predictive technologies, and operator training, these risks can be effectively mitigated. By investing in advanced systems and fostering a culture of preventative care, companies can ensure their turnstiles operate reliably and efficiently for years to come.
[Claim] The key to preventing coil turnstile failures lies in integrating advanced maintenance strategies with consistent monitoring, empowering businesses to save time, reduce costs, and maintain operational excellence.

Get Your Best Solution !