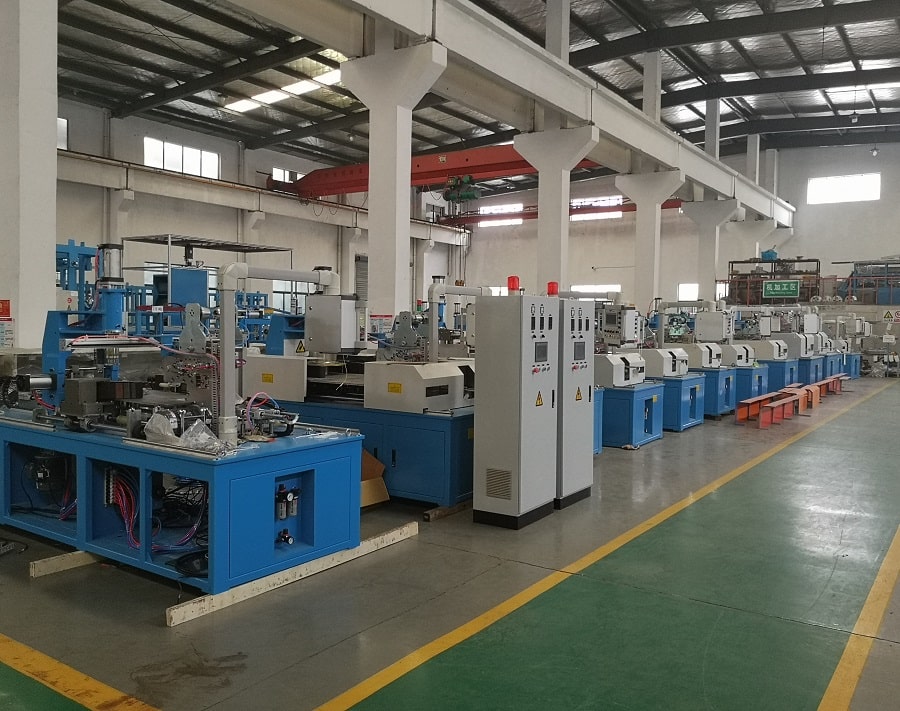
Cable packing machines are pivotal in modern manufacturing, ensuring that products are securely wrapped and ready for distribution. But what happens when these systems falter? Downtime caused by cable packing machine failures not only disrupts production schedules but also has ripple effects across supply chains. Understanding the causes, impact, and preventative measures of these failures is crucial for maintaining operational efficiency.
Failures in cable packing machines often appear sudden, but they usually result from long-term neglect of minor issues. A misaligned conveyor belt, overlooked sensor malfunction, or improper machine calibration can quickly escalate into significant problems. By proactively identifying potential weak points, businesses can prevent costly breakdowns and keep production lines running smoothly.
To navigate this challenge, you must be equipped with the knowledge to diagnose, address, and prevent these failures. This article provides a comprehensive overview of the common causes of machine failure, how to mitigate risks, and strategies to maximize equipment lifespan.
[Claim] Understanding the root causes of cable packing machine failures empowers manufacturers to implement effective solutions, ultimately enhancing productivity and profitability.
1. Why Do Cable Packing Machines Fail?
1.1 Misalignment of Mechanical Components
Even the smallest misalignment in a cable packing machine can lead to operational inefficiencies. Misaligned conveyor belts or rollers often cause irregular cable wrapping, leading to inconsistent packaging. Over time, this strain results in wear and tear on critical machine components, increasing the likelihood of complete system failure.
Proper calibration and alignment checks during routine maintenance can address these issues before they escalate. By ensuring that every part of the machine operates in harmony, manufacturers can improve reliability and extend the machine’s service life.
1.2 Electrical Failures: A Silent Disruptor
Electrical issues are one of the most common culprits behind cable packing machine failures. Sensors may fail to detect cables properly, or control panels might experience short circuits due to power surges.
Common Electrical Failures | Impact |
---|---|
Sensor malfunctions | Incorrect packaging output |
Short circuits | Machine shutdown |
Voltage fluctuations | Component damage |
To minimize these risks, manufacturers should install surge protectors and conduct regular inspections of electrical connections.
1.3 Overloading: The Hidden Enemy
Machines are designed to handle specific loads. Overloading the cable packing machine—whether by exceeding its weight capacity or operating it for prolonged periods without rest—can significantly reduce its lifespan.
This overuse leads to overheating, motor failures, and even structural damage. Regularly monitoring machine loads and scheduling appropriate downtime is essential to avoid these scenarios.
1.4 Operator Errors: A Human Factor
No matter how advanced a machine is, human error remains a critical risk factor. Incorrect settings, improper loading, and failure to follow operational guidelines can lead to accidents and malfunctions.
Training programs that educate operators about machine limitations and best practices can drastically reduce such errors. Ensuring that only certified personnel handle complex machinery adds an extra layer of safety and reliability.
1.5 Fact Statements
- True: Regular maintenance reduces the likelihood of cable packing machine failure by up to 70%, according to industry studies.
- False: Using a higher voltage than recommended can enhance the speed and efficiency of cable packing machines. (Higher voltage often leads to component damage and operational risks.)
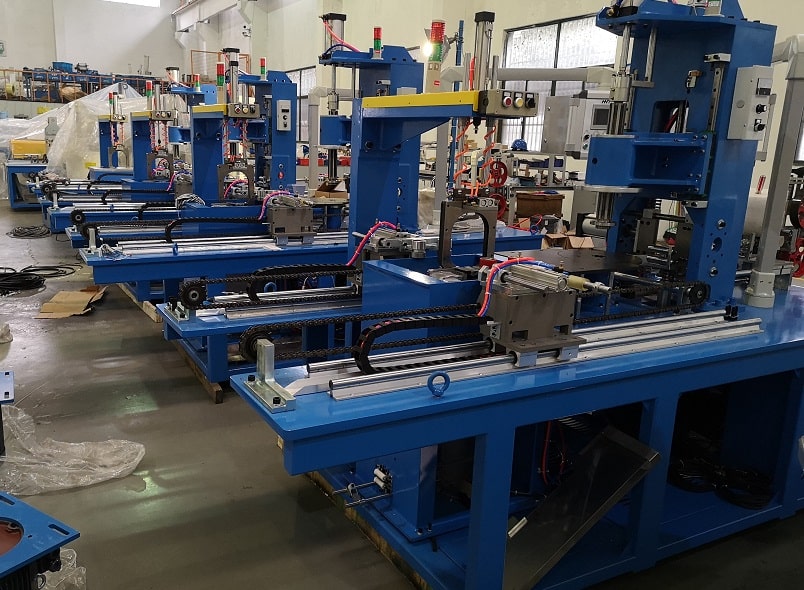
2. How Can Routine Maintenance Prevent Catastrophic Breakdowns?
2.1 Importance of Scheduled Inspections
Regular inspections are the backbone of an effective maintenance strategy. Identifying minor issues such as worn belts, loose bolts, or degraded lubricants during scheduled checks can prevent significant breakdowns.
A consistent maintenance schedule also ensures compliance with manufacturer guidelines, which often recommend inspections after specific operational hours. This practice not only improves machine reliability but also extends its operational lifespan.
2.2 Lubrication and Calibration: Key Maintenance Practices
Neglecting lubrication can lead to increased friction and eventual damage to the machine’s moving parts. Additionally, improper calibration can result in uneven cable packaging, wasting materials and compromising quality.
Maintenance Task | Frequency | Impact |
---|---|---|
Lubrication of moving parts | Every 200 hours | Reduces wear and tear |
Calibration checks | Monthly | Ensures packaging consistency |
Sensor testing | Quarterly | Detects early electrical issues |
By adhering to these practices, manufacturers can mitigate risks associated with routine wear and tear.
2.3 Common Missteps in Maintenance
Many operators underestimate the importance of using manufacturer-approved parts and consumables. Substituting cheaper alternatives may save costs initially, but it often results in compatibility issues and premature failure.
Another common mistake is skipping minor repairs, assuming they won’t impact overall performance. Over time, these small issues accumulate, leading to a complete system breakdown.
Manufacturers should implement a comprehensive maintenance plan that prioritizes long-term reliability over short-term savings.
2.4 How to Implement a Preventive Maintenance Plan
Preventive maintenance focuses on addressing issues before they occur. Start by creating a maintenance log that tracks inspection dates, performed tasks, and any observed issues.
Incorporating predictive analytics software into the maintenance routine can help anticipate potential failures. These systems use historical data to predict when components are likely to wear out, enabling timely replacements.
Investing in employee training programs is another critical step. Operators familiar with the machine’s intricacies are more likely to identify and report potential problems early.
2.5 Fact Statements
- True: Predictive maintenance reduces machine downtime by up to 50%, according to industry research.
- False: Using non-standard lubricants has no long-term impact on machine performance. (Non-standard lubricants often fail to meet manufacturer specifications, leading to increased wear and tear.)
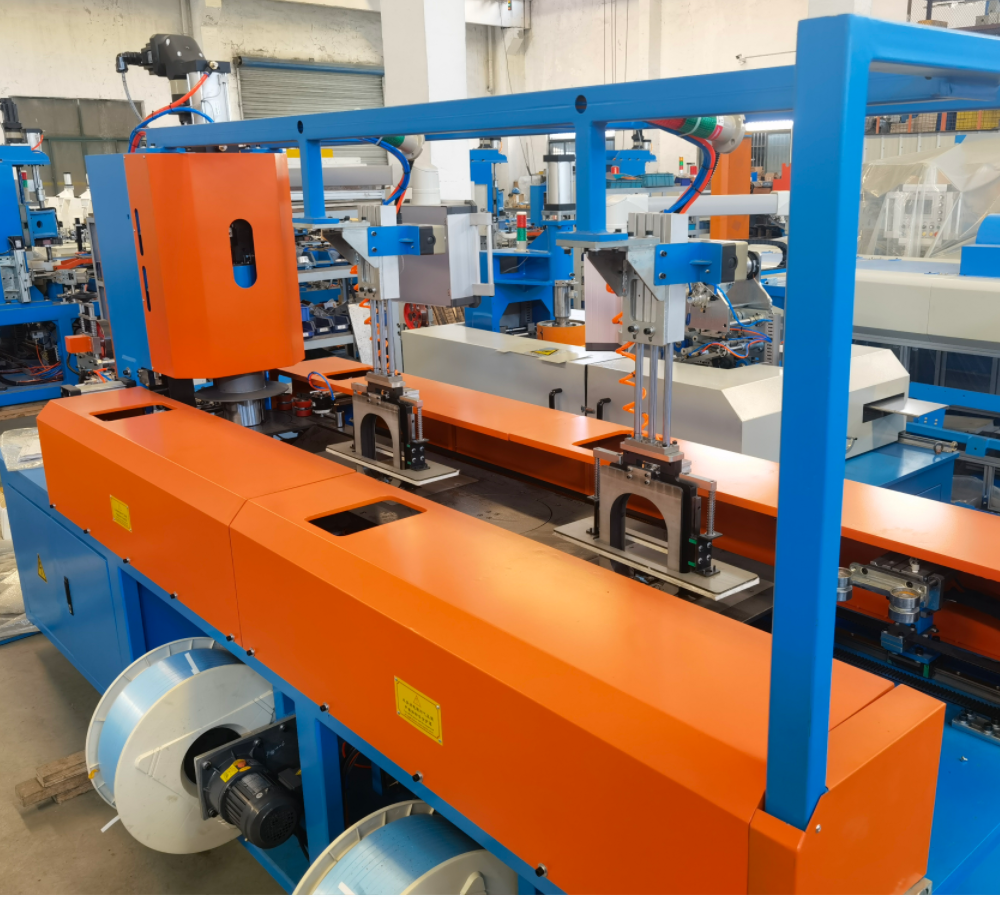
3. What Role Does Technology Play in Diagnosing Failures?
3.1 Advanced Diagnostics in Modern Machines
The latest cable packing machines come equipped with advanced diagnostic tools that monitor performance in real-time. Sensors track parameters such as temperature, pressure, and speed, flagging anomalies before they escalate into critical issues.
This technology not only minimizes downtime but also reduces the reliance on manual troubleshooting, allowing operators to focus on other tasks.
3.2 Data-Driven Insights for Predictive Maintenance
Leveraging data analytics is a game-changer for manufacturers. By analyzing historical performance data, operators can identify recurring patterns that indicate potential failures.
Diagnostic Tool | Functionality | Benefit |
---|---|---|
Vibration sensors | Detect mechanical wear | Early failure detection |
Thermal cameras | Monitor temperature levels | Prevent overheating |
AI-powered software | Analyze performance trends | Predict maintenance needs |
3.3 Challenges of Integrating New Technology
While advanced diagnostics offer undeniable advantages, their implementation is not without challenges. High upfront costs and the need for skilled operators to interpret data are significant barriers.
To overcome these hurdles, manufacturers should focus on gradual integration, starting with essential diagnostic tools and expanding capabilities as needed. Partnering with technology providers that offer training and support can also ease the transition.
3.4 Conclusion
Technology is transforming the way manufacturers approach machine maintenance. By investing in advanced diagnostics and predictive analytics, businesses can minimize downtime and enhance overall efficiency. These tools, when combined with traditional maintenance practices, create a robust system that ensures the long-term reliability of cable packing machines.
3.5 Fact Statements
- True: AI-powered diagnostics can detect up to 90% of potential machine failures before they occur.
- False: Advanced diagnostics eliminate the need for routine maintenance. (Regular maintenance remains essential to address issues that diagnostics might not catch.)
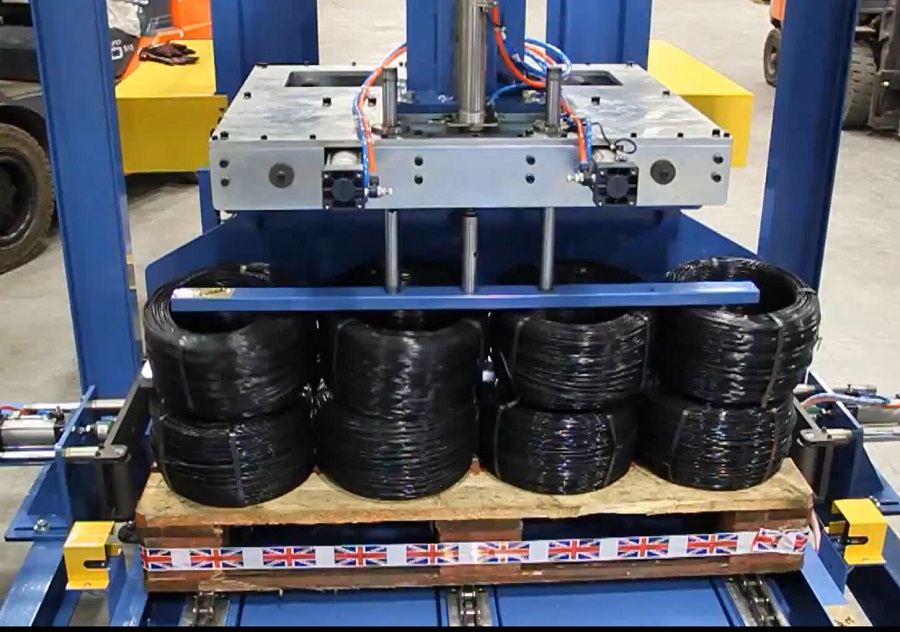
4. How Do You Select the Right Machine to Avoid Frequent Failures?
4.1 Evaluating Operational Requirements
Choosing the right cable packing machine begins with understanding your operational needs. Factors like production volume, packaging materials, and space constraints heavily influence machine selection.
For high-volume operations, a machine with automated features can significantly enhance efficiency. Conversely, smaller facilities may benefit from simpler, cost-effective models that prioritize reliability over advanced capabilities.
4.2 Key Specifications to Consider
When selecting a cable packing machine, evaluating technical specifications is critical. Elements such as machine speed, load capacity, and energy efficiency can impact both performance and long-term costs.
Specification | Importance | Optimal Range |
---|---|---|
Wrapping speed | Affects production output | 30–60 wraps per minute |
Cable diameter compatibility | Ensures versatility | 5mm to 60mm |
Energy consumption | Impacts operating costs | ≤1.5 kW per cycle |
4.3 Evaluating Manufacturer Support
The reliability of a cable packing machine also depends on the manufacturer’s post-sale support. Brands that offer comprehensive warranties, responsive customer service, and readily available spare parts often ensure higher machine uptime.
Look for manufacturers with a proven track record and positive customer reviews. Investing in equipment from a reputable brand might cost more initially but saves money by minimizing downtime and repair costs over time.
4.4 Balancing Cost and Long-Term Value
Price is often a deciding factor, but it should never overshadow quality and functionality. Opting for a low-cost machine may seem appealing, but frequent breakdowns and higher maintenance expenses can quickly negate the savings.
Instead, prioritize machines that offer a balance between cost-effectiveness and durability. Conducting a cost-benefit analysis to compare upfront costs with projected maintenance and energy expenses can guide better purchasing decisions.
4.5 Fact Statements
- True: Machines with higher energy efficiency ratings can reduce operational costs by up to 30% over their lifetime.
- False: All cable packing machines are compatible with every cable type. (Compatibility varies based on machine design and cable dimensions.)
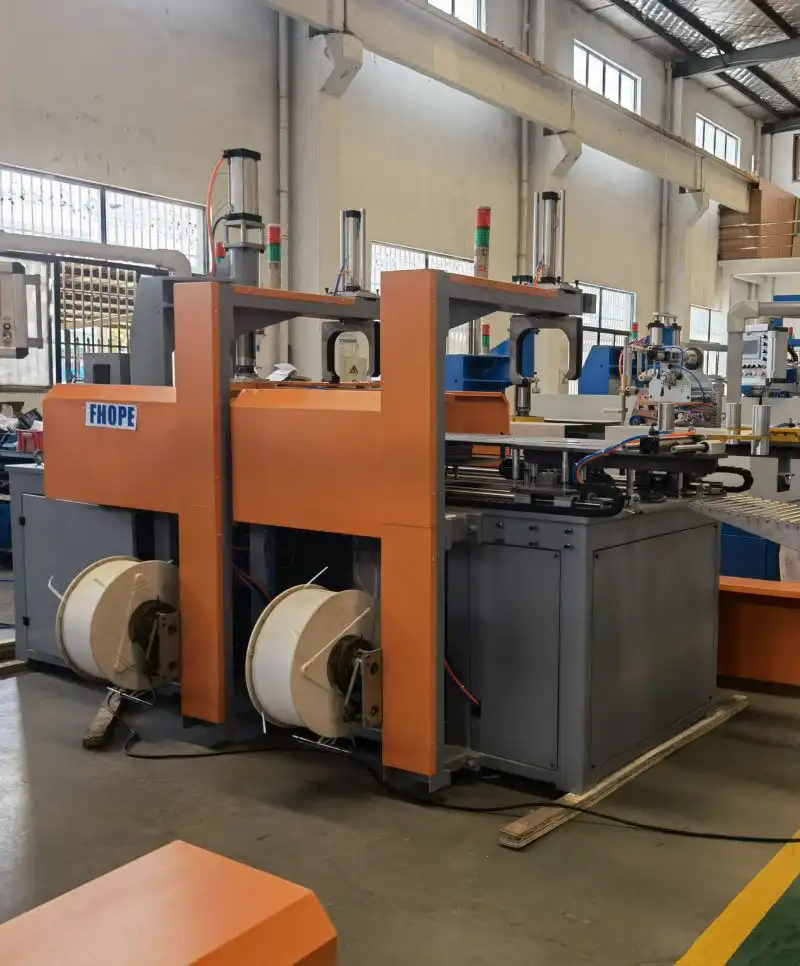
Conclusion
Understanding cable packing machine failures and their prevention is critical for maintaining smooth production workflows. From regular maintenance and advanced diagnostics to selecting the right equipment, every step contributes to reducing downtime and maximizing efficiency.
[Claim] By proactively addressing potential issues and investing in suitable solutions, manufacturers can create a reliable packaging process that supports long-term business growth.

Get Your Best Solution !