
When investing in automated steel coil packing lines, the importance of post-sale service and support cannot be overstated. These systems are often critical to operational efficiency and represent a significant capital investment. Ensuring you know what to expect in terms of service, troubleshooting, and long-term support can make the difference between smooth operations and costly downtime.
Every piece of machinery, no matter how advanced, requires ongoing care. Automated steel coil packing lines are no exception. From installation to maintenance, and from training to upgrades, the service package associated with your machinery is as crucial as the machine itself. In this guide, we’ll explore what a robust service and support framework should look like when purchasing or operating these systems.
Understanding the full scope of post-sale support is essential for maximizing the efficiency and longevity of your investment. A good provider will offer comprehensive assistance covering installation, preventive maintenance, emergency troubleshooting, and more. Let’s delve into the specifics of what to expect.
Service and support for automated steel coil packing lines can be categorized into key areas: installation, training, maintenance, spare parts management, and technical assistance. Ensuring these components are part of your service agreement is essential for sustainable operations.
1. Why is Service and Support Critical for Automated Packing Lines?
1.1 Understanding the Importance of Post-Sale Support
Investing in an automated steel coil packing line is more than just a purchase—it’s a long-term commitment to operational excellence. However, the true value of this investment lies in how effectively the system is supported after installation. Machines can malfunction, technologies can evolve, and staff may require ongoing guidance. Without robust post-sale support, these challenges can quickly escalate, leading to unplanned downtime or reduced efficiency.
1.2 What Should a Reliable Support Framework Include?
A strong service framework encompasses more than just technical assistance during emergencies. It should include proactive measures such as regular system audits, software updates, and operator training refreshers. Additionally, service providers should offer warranties that cover both parts and labor for an extended period. The objective is to provide peace of mind while ensuring optimal system performance throughout its lifecycle.

1.3 How Support Affects ROI
Inadequate service not only disrupts operations but also diminishes the return on your investment. Consider this: a well-supported packing line can significantly reduce operational costs by minimizing breakdowns and maintaining production speed. Conversely, frequent downtime due to poor service erodes profitability, negating the initial cost savings of choosing a lower-priced system. Therefore, the quality of service should be as much a priority as the equipment itself.
2. How Should Installation and Training Be Handled?
2.1 Why Professional Installation is Non-Negotiable
The installation phase is the foundation for how well your automated steel coil packing line will perform. A professional installation team ensures that every component is calibrated correctly, safety protocols are followed, and the system integrates seamlessly with your existing production lines. Skimping on professional installation can lead to recurring errors and reduced efficiency.
2.2 How to Evaluate Training Programs
After installation, the next critical step is operator training. A comprehensive training program should not only teach staff how to operate the system but also cover basic troubleshooting and maintenance tasks. This empowers your team to handle minor issues independently, reducing reliance on external technicians. Additionally, periodic training updates are vital as systems are upgraded or when new staff members join the team.

2.3 Installation and Training as an Ongoing Process
Installation and training are not one-time events. As production demands change, modifications to the system may be required, necessitating additional training. Likewise, after several years of operation, the system may require upgrades to maintain compatibility with new technologies. Choosing a provider that offers ongoing installation support and retraining services is crucial for adapting to these changes.
3. What Role Does Preventive Maintenance Play?
3.1 Why is Preventive Maintenance a Must-Have?
Preventive maintenance is the backbone of reliability for any automated system, including steel coil packing lines. By addressing potential issues before they escalate into full-blown problems, you can minimize unexpected downtime and extend the lifespan of your equipment. Think of it as the difference between regular health checkups and waiting for a medical emergency.
3.2 Key Components of a Preventive Maintenance Plan
A solid preventive maintenance plan should include regular inspections, calibration checks, software updates, and lubrication schedules. Providers that offer remote monitoring services can further enhance the effectiveness of these plans by identifying anomalies in real-time. Predictive analytics tools are increasingly being integrated, allowing systems to notify operators about upcoming maintenance needs before a fault occurs.

3.3 Benefits Beyond Reliability
Investing in preventive maintenance doesn’t just keep your system running—it also enhances operational efficiency. Regular upkeep ensures the machine operates at peak performance, leading to consistent production quality and reduced energy consumption. Additionally, a well-maintained machine holds its resale value better, which can be advantageous when upgrading to newer technology.
4. How Can Spare Parts Management Ensure Smooth Operations?
4.1 The Critical Role of Spare Parts Availability
Even the best-maintained systems occasionally require replacement parts. When a key component fails, the availability of spare parts can determine how quickly you get back online. Imagine a scenario where your packing line is idle for days due to a missing part—it’s an avoidable setback if your provider offers efficient spare parts management.
4.2 How to Ensure Timely Access to Spare Parts
Look for suppliers who maintain a robust inventory of critical spare parts and offer expedited shipping options. Some manufacturers even provide automated inventory management systems that track your usage and alert you when parts need reordering. This ensures that essential components are always on hand, minimizing downtime.
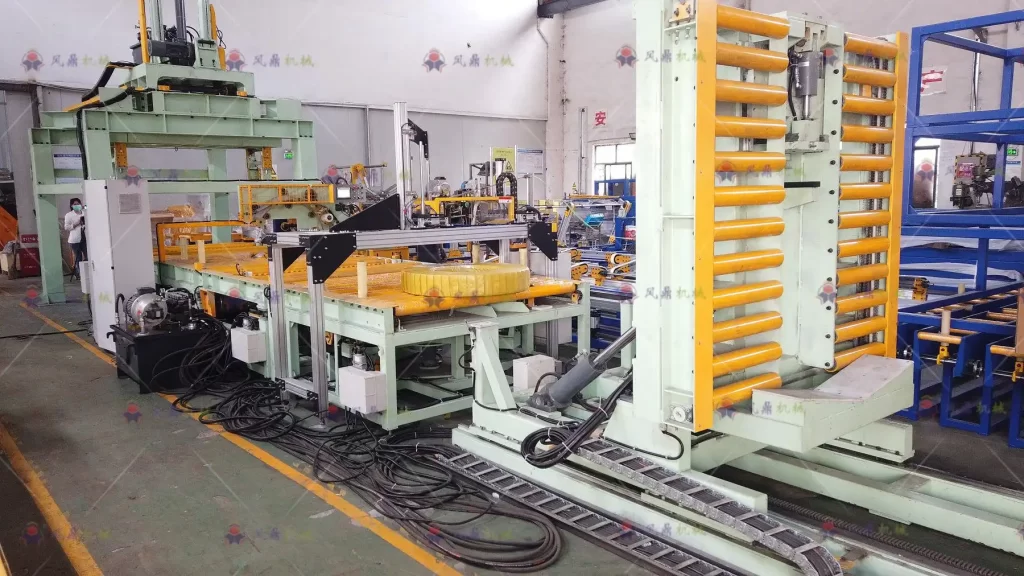
4.3 Long-Term Benefits of Strategic Spare Parts Management
A reliable spare parts program not only ensures continuity during emergencies but also reduces the overall cost of ownership. By negotiating bulk purchase agreements or opting for extended warranties that include parts, you can lower your long-term expenses. Moreover, consistent availability of high-quality parts enhances system performance, reducing wear and tear on other components.
Conclusion
Claim: Service and support are integral to the successful operation of automated steel coil packing lines.
The journey of owning and operating a steel coil packing line doesn’t end with the purchase—it begins there. From professional installation to continuous training, preventive maintenance, and spare parts management, every element of post-sale support plays a vital role in ensuring long-term efficiency and reliability.
Investing in a comprehensive service agreement not only safeguards your operations but also maximizes your return on investment. By partnering with a manufacturer that prioritizes service excellence, you’re not just buying equipment—you’re gaining a dependable ally in achieving operational success.

Get Your Best Solution !