The journey doesn’t end with the installation of your orbital stretch wrapper. In fact, it’s just the beginning of a long-term partnership focused on operational excellence, equipment optimization, and ensuring your investment delivers the value you expect. Post-installation support plays a pivotal role in keeping your machine running smoothly, reducing downtime, and adapting to evolving business needs.
From technical troubleshooting to operator training, post-installation support encompasses a wide range of services designed to maximize the performance and lifespan of your orbital stretch wrapper. When you choose us, you’re not just purchasing a machine—you’re gaining access to an ecosystem of expert care and innovation.
Whether you’re navigating operational hiccups, upgrading features, or simply looking to maintain peak efficiency, our comprehensive support ensures that you’re never left on your own. Here’s what you can expect from our post-installation services.
[featured image: A technical support engineer assisting with an orbital stretch wrapper in a manufacturing facility]
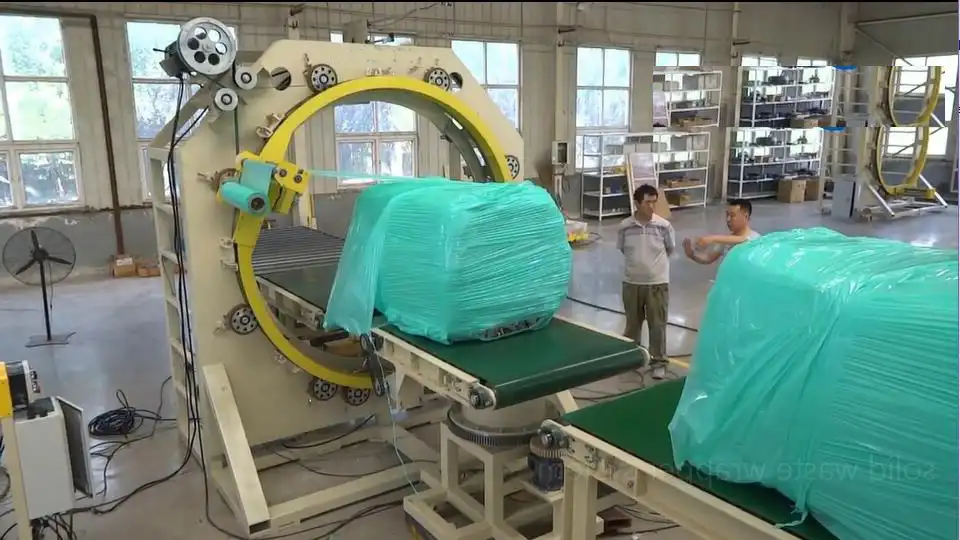
How Do We Ensure a Smooth Transition After Installation?
Immediate On-Site Assistance
One of the first steps after installation is ensuring that your new orbital stretch wrapper integrates seamlessly into your existing operations. Our team provides immediate on-site support to fine-tune machine settings, optimize workflows, and address any potential issues that arise during initial use.
For example, during a recent installation at a packaging facility, we identified a misalignment in the conveyor feeding system. By recalibrating the wrapper’s alignment in real-time, we prevented potential film wastage and ensured that the machine operated at peak efficiency from day one.
Calibration and Customization
No two operations are the same, which is why customization is key. Our post-installation team configures the machine to align with your specific requirements, adjusting parameters like wrapping tension, rotation speed, and film type.
A food packaging company required their orbital wrapper to handle both small trays and larger bulk shipments. By customizing the machine’s programmable settings, we enabled seamless transitions between product types, ensuring operational flexibility and efficiency.
![featured image: A technician calibrating an orbital stretch wrapper for customized product requirements]
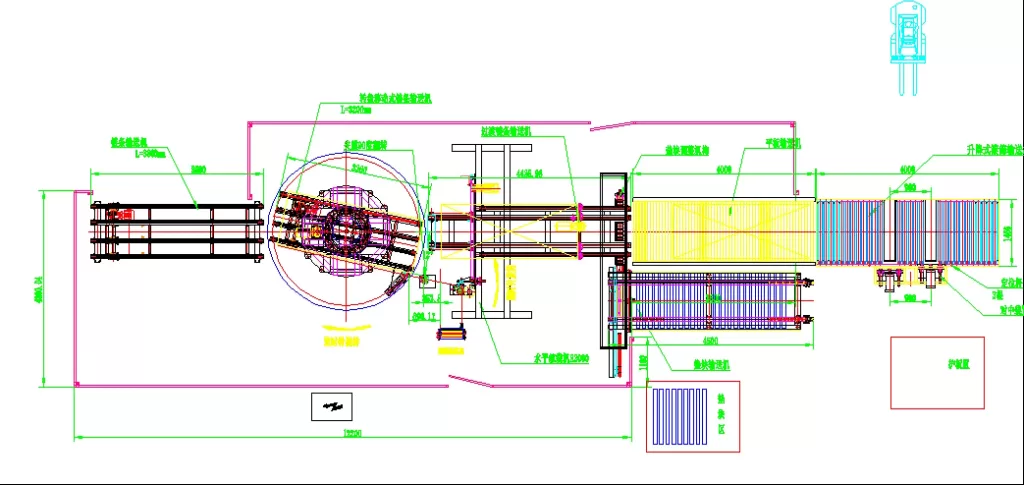
Testing for Operational Readiness
Before we leave your site, we rigorously test the machine to ensure it operates as expected under real-world conditions. This involves running sample loads, evaluating packaging quality, and verifying system reliability.
At a logistics hub, our team conducted a stress test using varying product sizes and weights to ensure the wrapper maintained consistent performance. The testing phase eliminated potential performance issues, giving the client confidence in their new system.
What Ongoing Maintenance Services Are Provided?
Preventative Maintenance Plans
Regular maintenance is essential to prevent wear and tear and avoid unexpected breakdowns. We offer tailored preventative maintenance plans that include routine inspections, lubrication of critical components, and software updates.
A manufacturer utilizing their orbital wrapper in a high-volume setting enrolled in our bi-annual maintenance plan. This proactive approach significantly reduced unplanned downtime and extended the lifespan of key components, keeping their operations running without interruption.
Real-Time Diagnostics and Remote Support
Modern orbital stretch wrappers often include IoT-enabled features that allow for real-time diagnostics. Through these systems, our support team can remotely monitor your machine’s performance, identify issues early, and provide solutions without the need for on-site visits.
One client experienced an unexpected drop in wrapping consistency. By accessing the wrapper’s diagnostic data remotely, our team quickly identified a film tension issue and guided their operator through the adjustment process, resolving the problem in minutes.
![featured image: Dashboard showing IoT-enabled diagnostic tools for an orbital stretch wrapper]
Emergency Repairs and Spare Parts Availability
Despite preventative measures, emergencies can happen. Our team is always on standby to provide rapid on-site repairs when needed. Additionally, we maintain a stock of spare parts to minimize downtime during urgent situations.
A steel coil manufacturer faced an unexpected motor failure during peak production. Within 24 hours, our technician arrived with the necessary replacement part, restored functionality, and ensured the production line was back up with minimal disruption.
How Does Our Training Program Empower Your Team?
Comprehensive Operator Training
A well-trained team is essential for maximizing the performance of your orbital stretch wrapper. Our post-installation support includes comprehensive operator training sessions, ensuring your staff is equipped with the knowledge and skills to handle the machine effectively.
At a large manufacturing facility, we conducted hands-on training workshops for their operators. These sessions covered everything from basic operations to troubleshooting techniques. The result was a confident team capable of resolving minor issues independently, reducing their reliance on external support and minimizing downtime.
Customized Learning Modules
Different teams have different needs. That’s why our training programs are tailored to your specific operational requirements. Whether it’s advanced programming for technical staff or simplified operation guides for warehouse personnel, we ensure everyone gains the knowledge they need.
For instance, a packaging company with a rotating staff required simplified yet effective training for their operators. We provided modular training materials, including videos and step-by-step guides, which allowed new hires to quickly learn the basics without disrupting ongoing operations.
![featured image: Operator training session for an orbital stretch wrapper in a factory setting]
Ongoing Support for Skill Development
Training doesn’t end after the initial session. Our team offers periodic refresher courses and advanced training for long-term skill development. This ensures your team stays updated with any new features or technologies introduced to your orbital stretch wrapper.
One logistics company opted for annual training updates. As new software features became available, their team learned how to utilize advanced diagnostics and adjust machine parameters, keeping their operations at the forefront of efficiency and innovation.
What Advanced Features Can Be Added Post-Installation?
Integration of IoT Capabilities
If your orbital stretch wrapper doesn’t initially include IoT functionality, we offer upgrades that integrate these advanced capabilities. IoT-enabled features allow for real-time performance monitoring, data collection, and predictive maintenance, which significantly enhance operational efficiency.
A distribution center upgraded their orbital wrapper with IoT sensors, enabling them to track film usage and monitor wear on key components. This data-driven approach helped them predict maintenance needs, avoid downtime, and optimize resource allocation.
Enhanced Wrapping Patterns
As your business evolves, your packaging requirements may change. We provide software upgrades that expand the machine’s wrapping patterns, allowing you to handle new product types or meet specific client demands.
A furniture manufacturer added a spiral wrapping feature to accommodate larger, irregularly shaped products. This upgrade improved packaging consistency and reduced the need for manual adjustments, streamlining their operations.
![featured image: Orbital stretch wrapper interface showing expanded wrapping pattern options]
Energy-Efficiency Upgrades
With growing emphasis on sustainability, energy-efficient features are becoming a priority for many businesses. We offer retrofitting options, such as energy-saving motors and advanced power management systems, to reduce the environmental impact of your equipment.
A beverage company aiming to meet their carbon reduction targets upgraded their orbital wrapper with energy-efficient drives. This change reduced energy consumption by 20% and contributed to their sustainability certifications, enhancing their reputation as an eco-conscious brand.
Conclusion
Post-installation support for your orbital stretch wrapper is not just about solving problems—it’s about ensuring long-term success, operational efficiency, and adapting to changing business needs. From seamless integration and proactive maintenance to empowering your team and upgrading features, our support services are designed to deliver maximum value at every stage of the machine’s lifecycle.
[claim] With comprehensive training, cutting-edge upgrades, and dedicated maintenance plans, our post-installation support transforms your orbital stretch wrapper from a standalone machine into a vital component of your operational success. When you choose us, you’re choosing a partner committed to your growth and efficiency.