An orbital wrapping machine represents a significant investment in automating and optimizing packaging lines. These machines boost efficiency and throughput while ensuring product protection during handling and transit. However, acquiring the equipment is just the first step. To truly maximize the operational lifespan and return on investment (ROI) of an orbital wrapper, businesses must carefully consider the essential support structures and service levels provided by the manufacturer. Comprehensive support encompasses far more than initial setup; it includes critical elements like technical assistance responsiveness, spare parts logistics, operator training, and robust warranty terms, all of which directly influence machine uptime and long-term performance.
This guide delves into the crucial support and service components necessary for effective orbital wrapping machine operation. We will explore key areas including technical support response times, spare part accessibility, personnel training programs, warranty coverage details, and the necessity of clear, comprehensive documentation. Understanding these requirements enables informed decision-making when selecting a supplier and ensures your orbital wrapper functions reliably, minimizing costly downtime and maximizing operational efficiency.
1. Recovery Speed: Minimizing Operational Downtime
In any production or logistics environment, equipment downtime translates directly to lost productivity and revenue. Recovery speed—the time it takes to diagnose and resolve an issue, returning the machine to full operational status—is therefore a critical performance indicator. When evaluating orbital wrapping machine suppliers, scrutinize the technical support responsiveness and recovery protocols they offer.
A. Rapid Technical Support Access
Immediate access to knowledgeable technical support is paramount. Look for manufacturers offering readily available support channels (phone, email, chat) with qualified technicians capable of providing swift troubleshooting assistance. Service Level Agreements (SLAs) defining response times can offer valuable assurance.
B. On-Site Service and Remote Diagnostics
While remote assistance can resolve many issues, complex problems may necessitate on-site technician deployment. Verify the manufacturer's field service capabilities, including technician availability and geographical coverage. Increasingly, remote diagnostic capabilities allow technicians to access machine data remotely, enabling faster problem identification and sometimes even resolution without a site visit, significantly shortening recovery times.
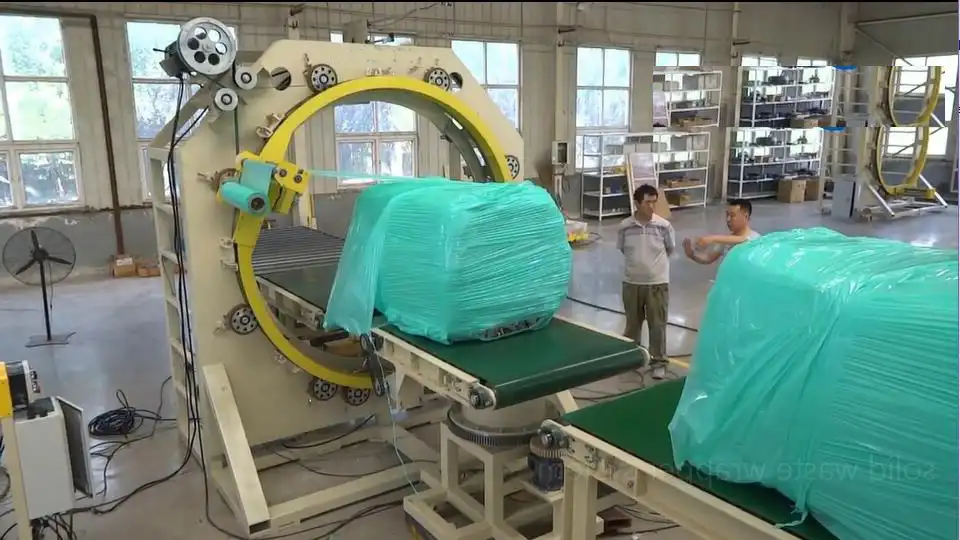
2. Availability of Spare Parts: Ensuring Continuous Operations
Even the most robustly built machinery experiences component wear over its operational life. Consistent and predictable access to replacement spare parts is fundamental to maintaining workflow continuity and avoiding prolonged shutdowns. Consider the logistics for both common wear parts and specialized components.
A. Common Wear Parts Stocking
High-wear components such as belts, rollers, sensors, and cutting blades require periodic replacement. The manufacturer or their local service partner should maintain adequate stock levels of these common parts for immediate dispatch. Inquire about recommended on-site spare parts kits for critical components to further reduce potential delays.
B. Special or Custom Parts Logistics
Parts unique to specific machine models or custom configurations might require special ordering. Evaluate the manufacturer's supply chain efficiency for these non-standard components. Understand the typical lead times and ensure they have reliable processes for sourcing and delivering these parts promptly.
C. Accessible Customer Service for Parts Ordering
A responsive customer service department is essential for efficient parts identification and ordering. Support should be available during your operational hours, staffed by personnel who can quickly assist with part identification using serial numbers or machine documentation, process orders, and provide tracking information.
D. Expedited Delivery Options
When a critical part fails, speed is crucial. Confirm the manufacturer utilizes expedited shipping methods (e.g., overnight courier, priority freight) to minimize transit time for essential spares. Regional parts depots can also significantly reduce delivery times compared to international shipping.
3. Training: Empowering Your Workforce for Efficiency and Safety
Properly trained personnel are key to operating and maintaining an orbital wrapping machine safely and effectively. Inadequate training can lead to operational errors, reduced efficiency, equipment damage, and safety incidents. Therefore, comprehensive operator and maintenance training is a non-negotiable service requirement.
A. Structured Professional Training Programs
Manufacturers should provide well-designed training programs delivered by experienced instructors. Curriculums should cover:
- Machine operation principles
- Control panel navigation and settings adjustment
- Film loading and threading procedures
- Routine maintenance tasks (cleaning, lubrication)
- Basic troubleshooting for common faults
- Critical safety procedures and lockout/tagout (LOTO) protocols
B. Tailored Training for Customizations
If your machine includes custom features or integrations, the training must specifically address these elements. Ensure operators understand the unique operational parameters and maintenance needs associated with any modifications.
C. Ongoing Support and Refresher Training
Personnel changes and evolving operational needs necessitate ongoing learning. Inquire about the availability of refresher courses, updated documentation, or advanced training modules. Continuous learning ensures your team remains proficient and adheres to best practices throughout the machine's lifecycle.
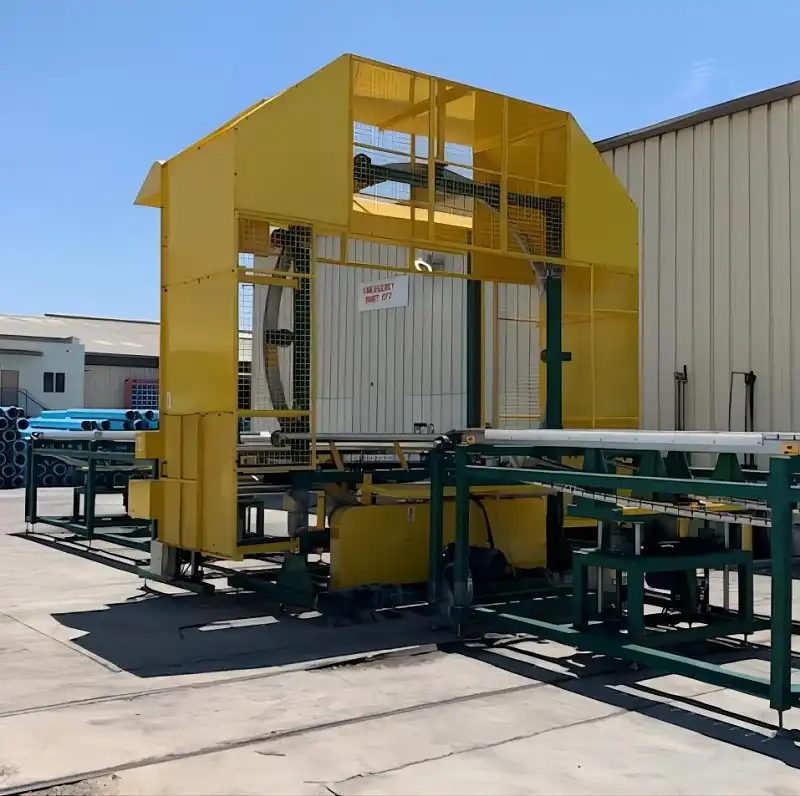
4. Warranty Specifics: Protecting Your Equipment Investment
A clear and comprehensive warranty provides crucial protection for your capital investment. It offers financial security against premature component failures and demonstrates the manufacturer's confidence in their product quality.
A. Component Coverage Details
The warranty should explicitly state which components are covered (e.g., motors, drives, PLCs, sensors) and for what duration. Understand any exclusions or limitations, particularly regarding wear parts versus defects in materials or workmanship.
B. Service Labor and Technician Travel
Clarify whether warranty service includes labor costs and technician travel expenses for on-site repairs. Unexpected service labor bills can significantly impact maintenance budgets if not covered.
C. Electrical and Control System Components
Failures in electrical systems or control components can be complex and costly. Ensure the warranty provides adequate coverage for these critical parts, including replacement and programming if required.
D. Defined Resolution Timeframes
Ideally, the warranty or associated service agreement should outline target timeframes for acknowledging service requests and initiating technical resolution, demonstrating a commitment to minimizing customer downtime.
5. Warranty Extensions: Securing Long-Term Protection
Standard warranties eventually expire, yet the need for reliable machine operation persists. Extended warranty options offer continued protection against unexpected repair costs as the machine ages and components naturally wear.
A. Benefits of Extended Coverage
Extended warranties provide budget predictability by covering major repairs beyond the initial period. They offer long-term peace of mind and can ensure continued access to manufacturer-certified technicians and genuine spare parts, preserving machine integrity.
B. Evaluating Extension Options
Compare different extended warranty plans offered by the manufacturer. Assess the duration, scope of coverage (parts, labor, travel), cost, and any included preventative maintenance services. Ensure the plan aligns with the machine's criticality and your risk tolerance.
6. Manuals and Documentation: Providing Essential Operational Guidance
Clear, comprehensive, and accessible operation and maintenance manuals are indispensable resources for your team. Effective documentation empowers operators and maintenance staff to use the machine correctly and perform routine upkeep.
A. Detailed Operating Procedures
The manual must provide clear, step-by-step instructions for all standard operating procedures, setup adjustments, and control panel functions. Diagrams and illustrations are crucial for clarity.
B. Maintenance Schedules and Troubleshooting Guides
A preventative maintenance schedule outlining daily, weekly, and monthly tasks is essential for machine longevity. A well-structured troubleshooting section, detailing common error codes or symptoms and their remedies, enables quick resolution of minor issues by operators.
C. Safety Information and Parts Lists
A dedicated section outlining all safety precautions, warnings, and procedures (including emergency stops and LOTO) is mandatory. An accurate spare parts list with part numbers and diagrams simplifies identification and ordering. Ensure manuals are available in the required language(s).
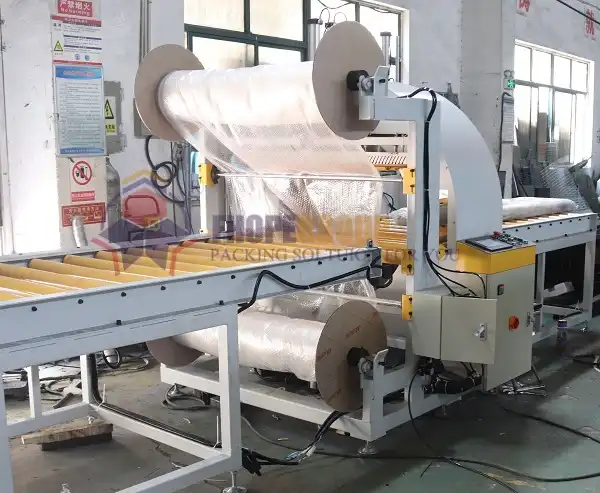
7. Customization Capabilities: Tailoring the Machine to Specific Needs
While standard orbital wrappers suit many applications, unique product dimensions, packaging requirements, or line integration challenges often necessitate customized machine solutions. The manufacturer should demonstrate the capability and willingness to tailor equipment design and functionality.
A. Modifications for Unique Products or Processes
If handling non-standard product sizes, shapes, or weights, or requiring specific wrapping patterns, machine modifications might be necessary. This could involve adjustments to the ring size, conveyor system, film delivery mechanism, or control logic.
B. Integration and Feature Flexibility
Effective integration with upstream and downstream equipment (conveyors, palletizers) is often critical. Manufacturers should offer flexibility in machine layout, control system handshaking, and optional features (e.g., top sheet dispensers, corner protectors, automatic film splicing) to create a seamless packaging line.
8. Continuous Improvement and Long-Term Support
The packaging industry and associated technologies are constantly evolving. A forward-thinking manufacturer provides ongoing support and potential upgrades to ensure your orbital wrapping machine remains efficient and effective throughout its extended service life.
A. Software Updates and Feature Enhancements
Modern orbital wrappers rely on sophisticated software for control and diagnostics. Manufacturers should offer periodic updates to improve performance, enhance security, add features, or address bugs. Inquire about the process and potential costs for software upgrades.
B. Lifecycle Support and Consultation
Beyond immediate technical issues, a good supplier acts as a long-term partner. This includes providing ongoing technical consultation, recommending potential hardware retrofits or upgrades as technology advances, and offering support as your production needs change over time.
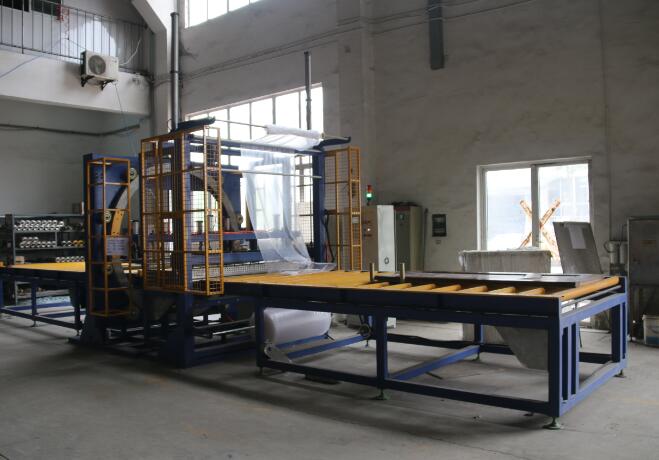
Conclusion: Prioritizing Comprehensive Support for Optimal Performance
Selecting the right orbital wrapping machine involves evaluating not only the equipment's specifications and price but also the robustness and responsiveness of the manufacturer's post-sale support infrastructure. Factors like rapid technical assistance, reliable spare parts availability, thorough training programs, clear warranty terms, and detailed documentation are critical determinants of the machine's long-term operational success.
By prioritizing these support elements during the procurement process, you ensure your investment is protected, downtime is minimized, and your packaging operations benefit from consistent, reliable performance for years to come. Comprehensive support is the foundation upon which efficient and productive orbital wrapping is built.