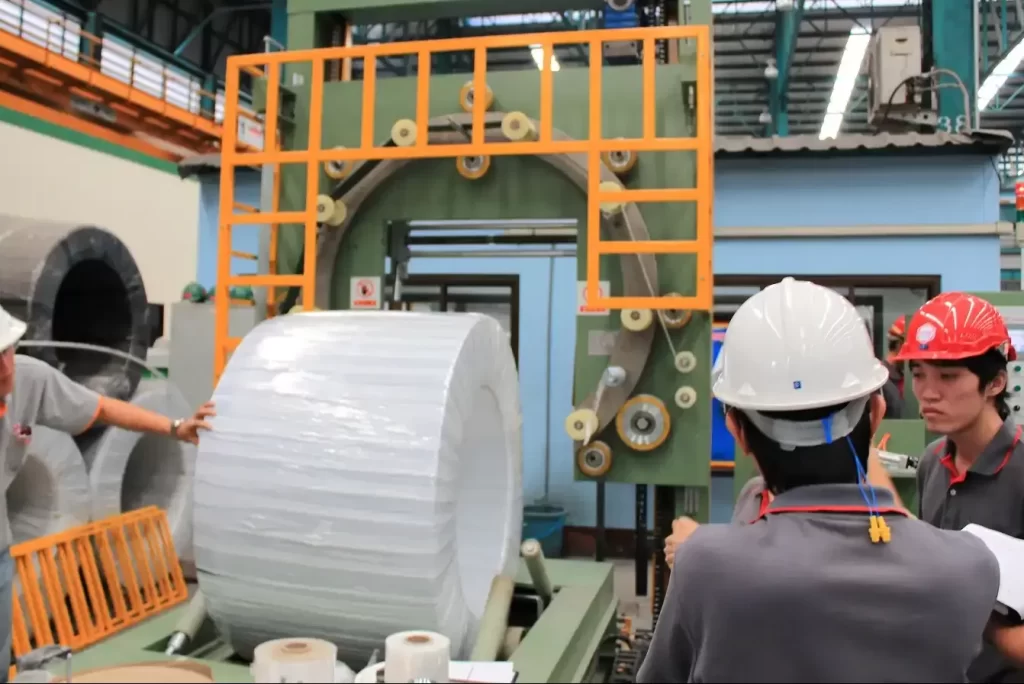
In demanding industrial environments, operational bottlenecks act as significant disruptors, leading to costly inefficiencies that impact productivity, labor allocation, and overall profitability. For facilities handling steel, wire, or metal coils, manual or outdated packaging methods often create these chokepoints. Implementing a modern coil wrapping machine offers a robust solution, introducing automation, consistency, and speed to overcome common obstacles in coil packaging workflows. **A modern coil wrapping machine can resolve key operational bottlenecks by enhancing speed, reducing material waste, improving consistency, and minimizing labor dependencies, thereby supporting a smoother, more efficient production line.**
Investing in an advanced coil wrapping system is not merely about convenience; it's a strategic approach to eliminate delays, optimize material handling, reduce operational costs, and boost throughput. These automated machines provide precision and speed unattainable through manual processes. Coupled with their durability and adaptability, they effectively address numerous issues that typically hinder packaging and distribution efficiency. The tangible value emerges when specific bottlenecks are identified and resolved, fundamentally transforming operational flow.
Within industrial packaging, consistency and efficiency are paramount. Addressing bottlenecks with targeted automation technology like coil wrappers unlocks significant gains in productivity, streamlines workflows, and ultimately enhances profitability.
1. How Does a Coil Wrapping Machine Improve Packaging Speed?
1.1. Increasing Throughput with Automated Wrapping
A primary benefit of a modern coil wrapping machine is the substantial increase in packaging speed compared to manual methods. Traditional manual wrapping is often slow and labor-intensive. Automated coil wrappers, designed for speed and efficiency, can complete the wrapping cycle significantly faster, often reducing wrapping time from many minutes to just a few per coil.
This acceleration translates directly to higher throughput, enabling a consistent and predictable flow of products through the packaging line. Key advantages include:
- Reduced Cycle Times: Faster wrapping per individual coil.
- Consistent Flow: Automated operation eliminates variability and delays common in manual processes.
- Increased Volume Handling: Facilities can manage larger production volumes without creating downstream congestion.
1.2. Minimizing Downtime with Reliable Machinery
Modern coil wrapping machines contribute to reduced bottlenecks by minimizing operational downtime. Manual wrapping is susceptible to interruptions from worker fatigue, human error, or process inefficiencies. In contrast, automated systems are engineered for continuous, reliable operation using durable components designed for extended industrial use. This reliability significantly reduces unplanned stops, maintaining a steady production rhythm.
Furthermore, many contemporary coil wrappers feature maintenance-friendly designs facilitating quick diagnostics, repairs, and preventative upkeep. This proactive approach ensures that even scheduled maintenance causes minimal disruption, supporting smoother workflows and enhancing overall equipment effectiveness (OEE).
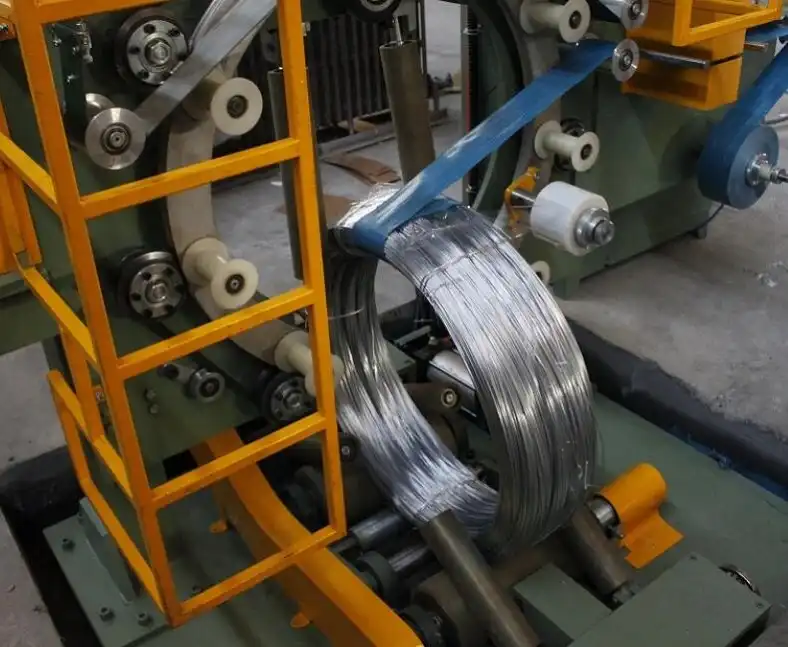
1.3. The Impact on Overall Production Capacity
The combined effect of increased speed and enhanced reliability directly boosts overall production capacity. An automated coil wrapping machine allows facilities to wrap substantially more coils per shift without requiring additional labor or floorspace. This increased capacity is crucial for scaling operations efficiently, particularly in industries facing fluctuating demand. The capability to increase output reliably and without compromising packaging quality provides a distinct competitive edge.
Modern coil wrapping solutions optimize the entire workflow by eliminating chokepoints in the packaging phase. This creates a seamless process capable of handling larger volumes without operational strain, contributing to a more robust and adaptable production line responsive to dynamic market needs.
2. What Role Does Consistency Play in Reducing Operational Delays?
2.1. Achieving Uniform Packaging with Precision Controls
Consistency is fundamental to minimizing operational delays, and modern coil wrapping machines excel in delivering uniform, high-quality results. Manual wrapping processes inherently suffer from variability – different operators may apply wrap material with varying tension or overlap, leading to inconsistencies that compromise coil protection and package appearance. Automated machines utilize precise controls to apply wrapping materials evenly and consistently to every coil, ensuring adherence to predefined quality standards.
This uniformity is vital for preventing downstream delays. Consistently packaged coils are less likely to require inspection failures, rework, or corrective handling, all of which disrupt process flow. By ensuring every coil is wrapped precisely to specification, automated systems reduce quality-control-related delays and maintain smooth production momentum.
2.2. The Role of Consistency in Inventory Management
Uniform packaging significantly streamlines inventory management and warehouse operations. Consistently wrapped coils are easier and safer to handle, stack, and store, optimizing valuable warehouse space. When each packaged coil occupies a predictable footprint and offers reliable protection, inventory organization becomes more efficient, reducing the time and effort required for stock management tasks.
Benefits for inventory handling include:
- Optimized Storage: Uniform packages allow for denser, more stable stacking.
- Easier Tracking: Consistent dimensions and appearance simplify inventory counts and location tracking.
- Faster Retrieval: Standardized packaging facilitates quicker access and movement of coils for shipment or further processing, preventing warehouse bottlenecks. (See Material Handling Institute resources on warehouse optimization)
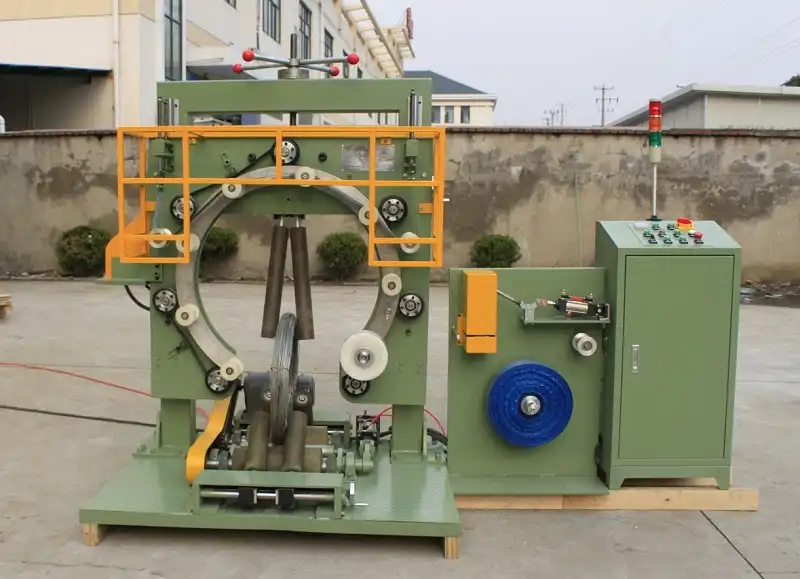
2.3. Enhanced Quality Control and Reduced Rework
A consistent wrapping process inherently improves quality control by minimizing defects that necessitate costly rework. Common issues in manual wrapping, such as uneven tension, poor film adhesion, or inadequate edge coverage, can lead to rejected coils that must be reprocessed, causing significant delays and disrupting production schedules.
Automated coil wrapping machines mitigate these risks by adhering to precise, repeatable wrapping programs. This reliability drastically reduces the incidence of errors and the associated need for rework, enabling smoother operations and minimizing time lost on corrective actions. Consequently, the final product quality is enhanced, ensuring coils leave the facility properly protected and presented.
3. How Does a Coil Wrapping Machine Minimize Material Waste?
3.1. Precision in Material Application for Cost Efficiency
Material waste represents a significant operational cost and potential bottleneck in packaging. During manual or semi-automatic wrapping, operators might apply excessive wrap film or other materials due to guesswork or variability, leading to unnecessary consumption. A modern coil wrapping machine addresses this by applying materials with high precision, using sophisticated controls to dispense only the optimal amount required for secure coil protection. This precision directly translates into substantial material savings and improved cost efficiency.
Reducing material waste offers benefits beyond direct cost savings:
- Lower Supply Costs: Reduced consumption of stretch film, VCI paper, or other wrapping materials.
- Improved Sustainability: Minimizing waste generation aligns with environmental responsibility goals. (Learn about waste reduction from EPA)
- Reduced Restocking Frequency: Less material usage simplifies supply chain management.
3.2. Reducing Packaging Variability with Automated Controls
Automated coil wrappers feature programmable settings for parameters like wrap tension, material overlap, film pre-stretch ratio, and layer count. This allows facilities to fine-tune the wrapping process for different coil types and ensure consistent material application across all units. By eliminating the variability inherent in manual wrapping, these machines prevent both material overuse and under-protection, major contributors to waste and potential product damage.
Consistent, optimized wrapping not only saves material but also guarantees that each coil meets packaging specifications, crucial for quality assurance and customer satisfaction. This controlled process allows for predictable cost management and helps streamline packaging expenses without compromising the integrity of the wrapped coil.
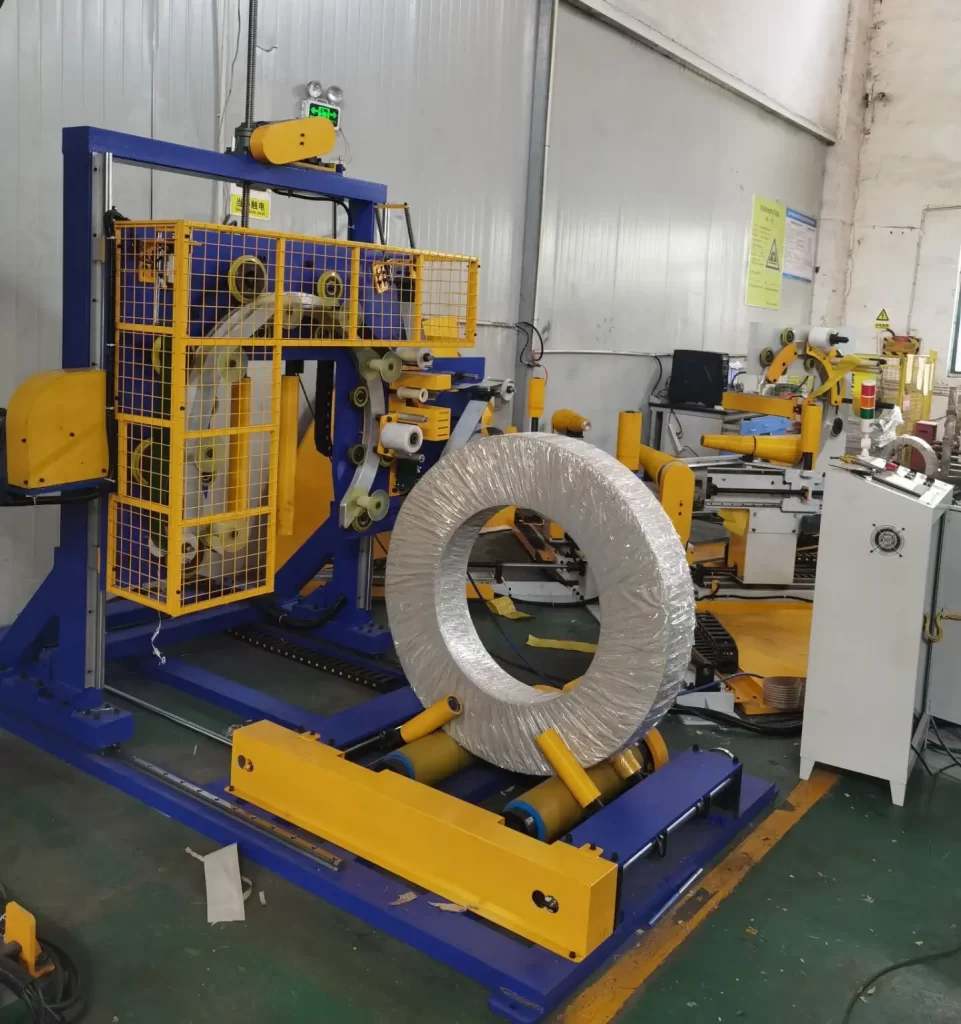
3.3. Supporting Sustainability Goals Through Reduced Waste
Minimizing material waste directly supports corporate sustainability objectives, an increasingly critical consideration for industrial operations facing pressure to adopt environmentally friendly practices. A modern coil wrapping machine, through optimized material usage, reduces the volume of disposable waste generated per coil. This efficiency helps achieve packaging goals with fewer resources, lessening the operation’s environmental footprint.
In today's market, demonstrating sustainable practices enhances brand reputation alongside cost reduction. Investing in efficient, automated wrapping systems provides both economic and ecological advantages, positioning the business for greater resilience and aligning with market expectations for environmental stewardship.
4. What Impact Does Reduced Labor Dependency Have on Efficiency?
4.1. Lowering Labor Costs with Automated Systems
One of the most compelling economic advantages of automated coil wrapping is the significant reduction in labor dependency. Traditional wrapping methods often require multiple operators for handling, wrapping, inspection, and adjustments – tasks that are both costly and time-consuming. By automating these repetitive functions, a modern machine allows for streamlined labor allocation, dramatically reducing hands-on involvement and lowering direct labor costs associated with packaging.
This reduction offers several benefits:
- Lower Payroll Expenses: Fewer operators needed for the packaging task.
- Reduced Reliance on Skilled Labor: Frees up specialized workers from routine tasks.
- Mitigation of Labor Shortages: Provides a practical solution in tight labor markets.
4.2. Improving Safety and Reducing Workplace Injuries
Automating coil wrapping enhances workplace safety by minimizing the need for workers to perform physically demanding or potentially hazardous tasks, such as manually lifting, manipulating, and wrapping heavy coils. Reducing human interaction with large, heavy materials significantly lowers the risk of musculoskeletal injuries, strains, and other workplace accidents. (Refer to OSHA guidelines on material handling safety).
A safer working environment translates to fewer injury-related interruptions, reduced workers' compensation costs, and improved employee morale. Investing in automation is thus an investment in both operational efficiency and workforce well-being.
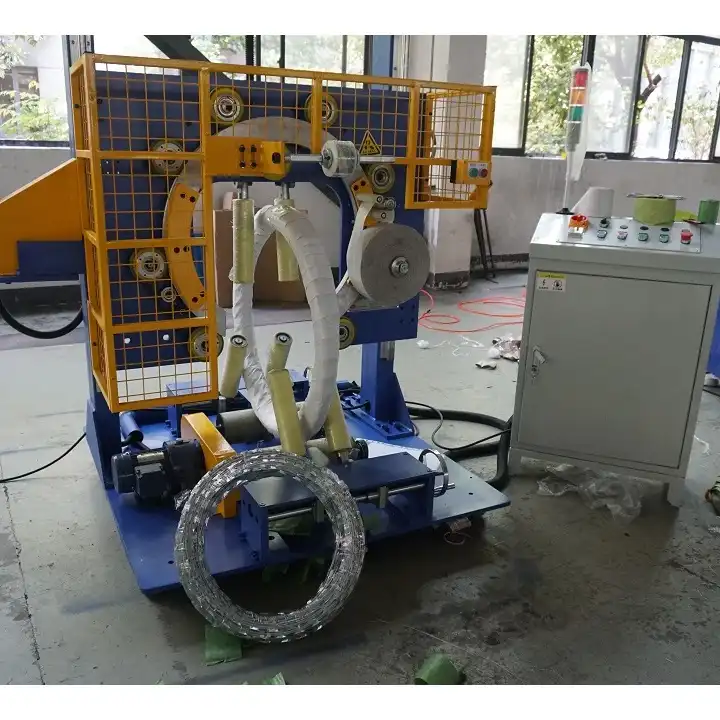
4.3. Allocating Workforce to Higher-Value Tasks
Automated coil wrapping frees up valuable human resources previously tied to repetitive manual labor. These employees can be strategically reassigned to higher-value tasks requiring critical thinking, problem-solving, quality oversight, or process improvement initiatives. This reallocation optimizes the workforce, allowing skilled personnel to focus on activities that directly enhance productivity, innovation, or overall operational quality.
By automating routine processes like coil wrapping, businesses can maximize the potential of their workforce, placing employees in roles where their skills contribute most effectively. This not only increases overall efficiency but can also boost job satisfaction and employee engagement, fostering a more dynamic and productive operational environment.
Conclusion: Automation as a Solution to Packaging Bottlenecks
Modern coil wrapping machines provide a powerful solution to persistent bottlenecks commonly found in industrial packaging operations. Through advanced automation, enhanced consistency, and operational precision, these systems fundamentally improve workflow efficiency. Key benefits—increased packaging speed, improved wrap consistency, reduced material waste, and lower labor dependency—combine to streamline processes, cut operational costs, and significantly boost overall productivity.
Investing in automated coil wrapping technology transcends a simple equipment upgrade; it represents a strategic move towards creating a more resilient, efficient, and scalable manufacturing or distribution operation. By automating coil wrapping, facilities can effectively resolve key bottlenecks, minimize operational delays, and enhance productivity, making it a vital investment for achieving long-term operational excellence and competitiveness in demanding industrial sectors.

Get Your Best Solution !