What Kind of Maintenance Do Steel Coil Packing Lines Require?
- What Kind of Maintenance Do Steel Coil Packing Lines Require?
- 1. The Importance of Regular Maintenance for Steel Coil Packing Lines
- 2. Daily Maintenance Tasks
- 3. Weekly and Monthly Preventive Maintenance
- 4. The Role of Predictive Maintenance in Modern Packing Lines
- 5. The Impact of Regular Maintenance on Safety
- 6. Developing a Maintenance Schedule for Steel Coil Packing Lines
- 7. Best Practices for Maintenance Record-Keeping
- Conclusion
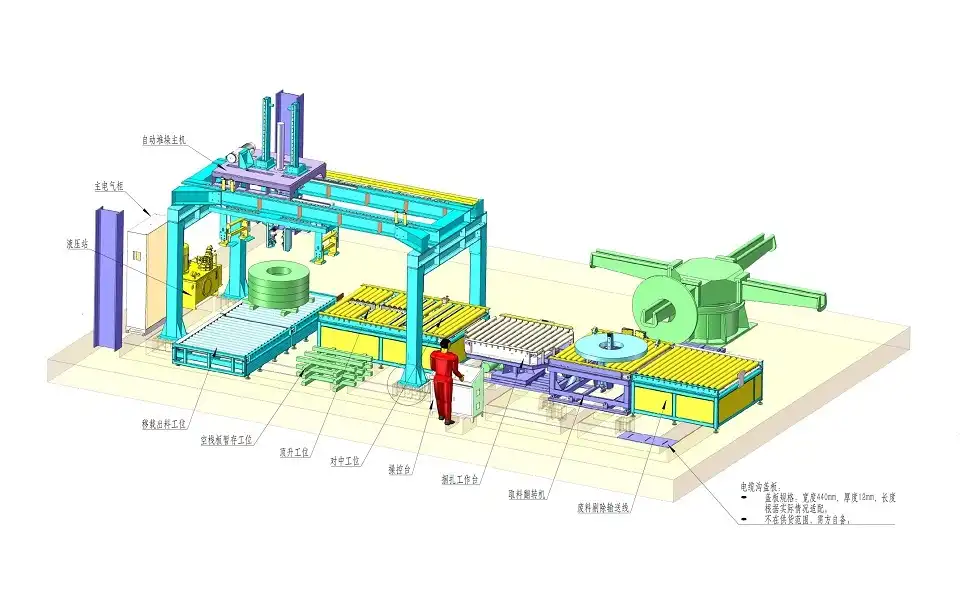
Steel coil packing lines are crucial for protecting high-value materials during transport and storage. These complex machines automate the packaging process, ensuring that steel coils are securely wrapped, strapped, and labeled for shipping. However, like any advanced machinery, steel coil packing lines require regular maintenance to ensure optimal performance, minimize downtime, and extend the life of the equipment.
In this article, we’ll explore the different types of maintenance tasks required for steel coil packing lines, the importance of preventive measures, and best practices to follow. We’ll also discuss how effective maintenance contributes to operational efficiency, safety, and overall profitability.
1. The Importance of Regular Maintenance for Steel Coil Packing Lines
Steel coil packing lines are intricate systems composed of several interconnected components such as conveyors, wrapping units, strapping machines, and coil upenders. Neglecting maintenance can lead to reduced efficiency, equipment failure, and safety hazards. Consistent maintenance not only ensures smooth operations but also helps prevent costly breakdowns and emergency repairs.
Regular maintenance offers several key benefits:
- Increased equipment lifespan: Well-maintained machines experience less wear and tear, which extends their usable life.
- Reduced downtime: Preventive maintenance prevents unexpected breakdowns, ensuring that operations run without interruption.
- Safety: Regular inspections and repairs reduce the risk of accidents caused by malfunctioning equipment.
- Cost savings: A proactive approach to maintenance helps avoid expensive repairs and replacements.
Now that we understand the importance of maintenance, let’s break down the specific tasks involved in keeping your steel coil packing line in top shape.
2. Daily Maintenance Tasks
Daily maintenance tasks are quick and easy to perform but are essential for ensuring the equipment remains in good working order. These tasks focus on cleanliness, visual inspections, and basic lubrication.
Key Daily Maintenance Tasks:
- Cleaning: Dust, dirt, and debris can accumulate on the moving parts of the machine. These contaminants may cause friction, leading to premature wear. Operators should clean the machine daily, particularly focusing on conveyors, sensors, and wrapping units.
- Inspecting sensors and controls: Steel coil packing lines rely on sensors to detect coil dimensions and ensure the proper application of packaging materials. Daily inspection ensures these sensors are clean and functioning properly.
- Lubricating moving parts: Friction between moving parts can wear them down over time. Applying lubrication to chains, bearings, and gear mechanisms prevents this wear and ensures smooth operation.
By incorporating these daily maintenance tasks, operators can catch potential issues early and ensure their steel coil packing line runs efficiently.
3. Weekly and Monthly Preventive Maintenance
While daily maintenance focuses on immediate concerns, weekly and monthly preventive maintenance dives deeper into the mechanical and electrical aspects of the packing line. These tasks are more comprehensive and require more time, but they are crucial for ensuring the longevity of the system.
Weekly Maintenance Tasks:
- Tightening bolts and connections: The vibrations caused by the movement of heavy coils can loosen bolts and connections. A weekly check ensures that all fastenings remain secure.
- Checking belts and conveyors: Belts and conveyors are under constant strain, transporting heavy steel coils. Inspect them for signs of wear or stretching, and replace any damaged components.
- Inspecting pneumatic and hydraulic systems: Many packing lines rely on pneumatic or hydraulic power for wrapping and strapping operations. Checking for leaks, pressure issues, and wear in hoses and seals is critical for maintaining optimal performance.
Monthly Maintenance Tasks:
- Deep cleaning: While daily cleaning focuses on visible surfaces, monthly maintenance should include a deep clean of harder-to-reach areas, such as inside electrical panels and underneath conveyors.
- Electrical inspection: Inspect the electrical wiring and control panels to ensure there are no frayed wires or loose connections. Faulty wiring can lead to shorts or malfunctions, which could cause dangerous accidents.
- Calibrating sensors: Ensure that all sensors are properly calibrated to measure and detect the dimensions and weights of coils accurately. Miscalibrated sensors can cause errors in wrapping or strapping, leading to product damage.
Both weekly and monthly maintenance contribute to long-term reliability and efficiency by addressing issues before they develop into significant problems.
4. The Role of Predictive Maintenance in Modern Packing Lines
With the advent of Industry 4.0 and IoT technology, predictive maintenance is becoming an integral part of managing steel coil packing lines. Predictive maintenance involves the use of sensors, data analytics, and machine learning to predict when components are likely to fail and take action before breakdowns occur.
How Predictive Maintenance Works:
- Sensors are embedded within critical machine components, such as motors, conveyors, and bearings. These sensors monitor variables like vibration, temperature, and wear in real-time.
- The data collected by these sensors is analyzed using machine learning algorithms to identify patterns and trends.
- The system alerts operators when a component is likely to fail, enabling preemptive repairs or replacements before the failure causes a disruption in the production line.
The advantage of predictive maintenance is that it allows operators to avoid unplanned downtime by addressing problems at their earliest stages. It also reduces the need for excessive preventive maintenance, as the system only intervenes when necessary.

Get Your Best Solution !
5. The Impact of Regular Maintenance on Safety
Safety is a top priority in any industrial setting, and steel coil packing lines are no exception. Neglecting maintenance can lead to hazardous conditions for workers, such as malfunctioning machinery or improperly strapped coils that could collapse or fall during transport.
Key safety concerns that can be mitigated through regular maintenance include:
- Strapping failures: Worn or malfunctioning strapping machines may apply straps incorrectly, resulting in coils that are not properly secured.
- Electrical issues: Faulty wiring or damaged control panels can cause short circuits or electrical fires.
- Hydraulic or pneumatic malfunctions: Leaks or pressure drops in hydraulic or pneumatic systems can cause sudden and dangerous failures, potentially leading to injuries or equipment damage.
A well-maintained steel coil packing line is not only more efficient but also significantly safer. Properly functioning equipment ensures that workers can operate in a secure environment, free from avoidable hazards.
6. Developing a Maintenance Schedule for Steel Coil Packing Lines
Developing a comprehensive maintenance schedule is essential to keep your steel coil packing line operating efficiently and safely. The schedule should be based on the specific needs of your machinery and should consider daily, weekly, monthly, and annual tasks.
A maintenance schedule should include:
- Daily tasks: As discussed earlier, these tasks focus on cleaning, lubrication, and basic inspections.
- Weekly tasks: Checking components for wear, tightening bolts, and inspecting pneumatic or hydraulic systems.
- Monthly tasks: Deep cleaning, electrical inspections, and sensor calibrations.
- Annual tasks: Annually, your packing line should undergo a comprehensive overhaul. This involves disassembling key components, replacing any parts that are nearing the end of their service life, and conducting a thorough inspection of the entire system.
Having a clear and consistent maintenance schedule ensures that no task is overlooked and that your machinery continues to perform at its best.
7. Best Practices for Maintenance Record-Keeping
One of the most overlooked aspects of machine maintenance is proper record-keeping. Keeping detailed records of all maintenance activities allows operators to track the condition of the machinery over time and identify trends that may indicate a potential failure.
Key Benefits of Maintenance Record-Keeping:
- Tracking performance: Maintenance records show how often components are replaced or repaired, helping you identify areas of concern.
- Compliance: In some industries, maintenance logs are required for regulatory compliance.
- Budgeting: Knowing the cost and frequency of repairs allows for better budgeting for future maintenance expenses.
A digital maintenance log is often the best option, as it provides easy access to information and can integrate with predictive maintenance systems.
Conclusion
Steel coil packing lines are a vital part of the steel production process, ensuring that coils are properly secured and ready for shipping. However, to ensure these machines continue to function optimally, regular maintenance is essential. Daily, weekly, monthly, and predictive maintenance tasks keep equipment in good working order, reduce downtime, and enhance safety. Furthermore, a well-planned maintenance schedule and good record-keeping can prevent costly breakdowns, extend the life of your machinery, and protect the health and safety of your workforce.
By investing in a robust maintenance program, businesses can ensure the long-term success of their steel coil packing operations and improve overall profitability.

Get Your Best Solution !