I see many people worry about handling massive coils. They feel uncertain about the limits of coil upenders.
A coil upender can handle coils from a few tons to well over 50 tons, based on its design, motor capacity, and structural strength.
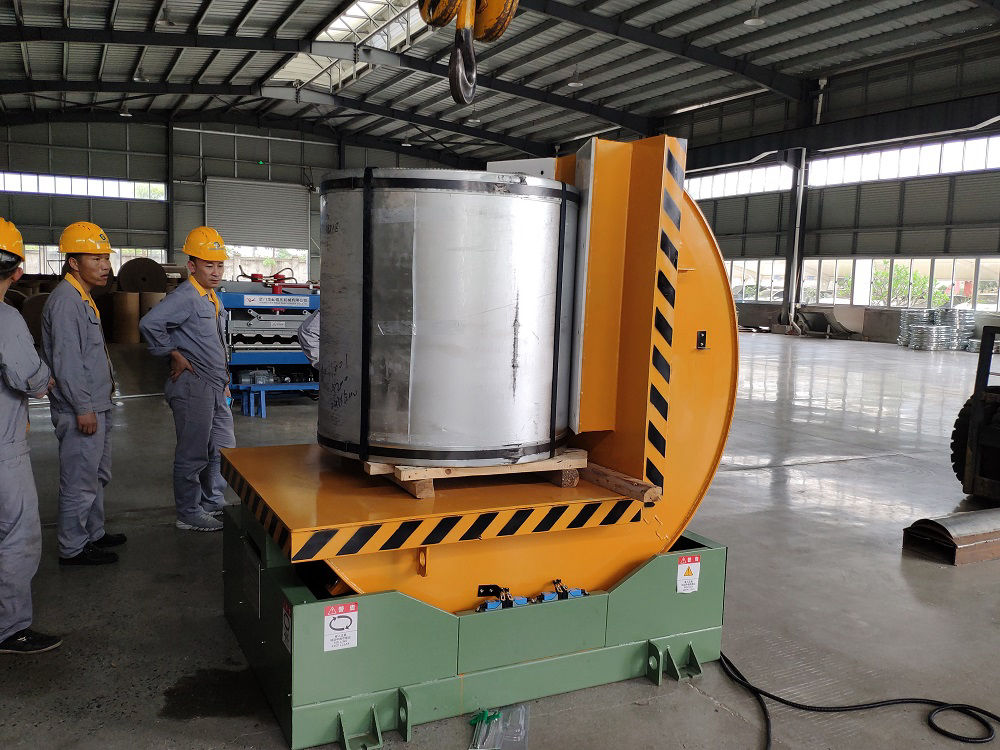
I know that coil upenders vary by manufacturer. We should look at load capacity, diameter range, and overall machine design. Then we pick the right upender for our needs.
How Do Manufacturers Determine Maximum Coil Capacity?
I notice many who are new to coil handling wonder if capacity comes from guesswork or strict testing.
I think manufacturers test coil upenders using real loads. They also rely on structural calculations. This way, they can decide the safe maximum weight a coil upender can rotate.
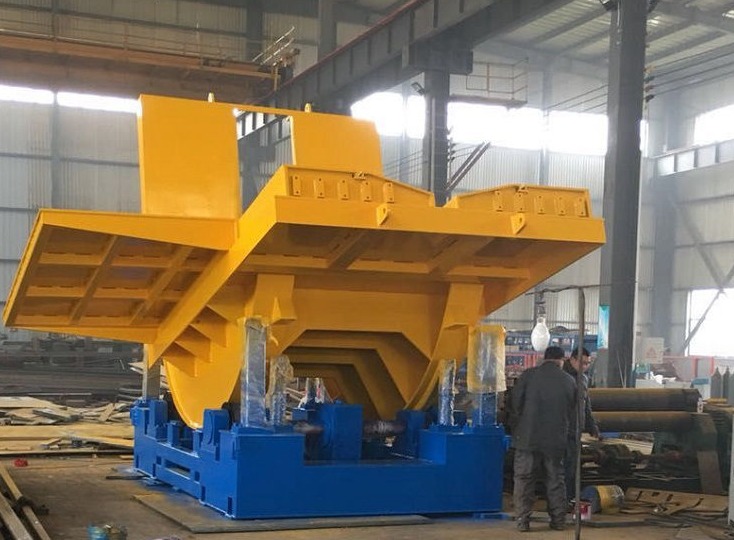
Maximum Coil Capacity
I want to break down the process. Coil upenders have frames that must withstand high stress. Manufacturers look at steel thickness, weld quality, and the geometry of support arms. They run simulations that analyze potential stress points under full load. Then they perform real-world tests to confirm the simulation results.
They also consider the drive system. Some coil upenders use hydraulic cylinders, while others use gear-driven systems. These power mechanisms produce torque. If the torque is too low, the upender will struggle to rotate heavier coils. If the system is too weak, it may stall or overheat, leading to breakdowns. So manufacturers run load tests to see if the drive can handle peak loads without failing.
I have seen engineers use strain gauges attached to critical stress points on the frame. They rotate large coils and measure how the steel structure flexes. If the flex is within safe limits, they confirm that the upender can operate at that capacity. If not, they adjust the design or use thicker materials. This iterative approach finds the highest coil weight the machine can handle while still meeting safety standards.
Manufacturers also factor in duty cycles. A facility might flip hundreds of coils a day. The upender must keep working under repeated loads. If a machine is rated for 30 tons but flips coils all day, wear can accumulate. So the manufacturer might suggest a safety margin. In practice, you might not run the upender at full capacity every time. Instead, you stay a bit below the maximum for prolonged service life.
Another point is that some upenders feature adjustable cradles that support different coil sizes. The design must hold a range of coil diameters without losing stability. Manufacturers do final inspections for each model. Then they share recommended load limits. If your coil is heavier than their recommendation, you risk equipment damage or operator harm.
Below is a simple table that shows typical steps in determining maximum capacity:
Step | Action | Outcome |
---|---|---|
Structural Design | Engineers pick materials | Ensure rigid frame |
Simulation | Use stress analysis software | Identify weak points |
Real-World Tests | Test with actual coils | Confirm load rating |
Safety Margin | Apply extra capacity buffer | Reduce breakdown risk |
When I first discovered coil upenders, I was surprised at the detailed checks. I assumed that the manufacturer just labeled a number and sold it. Now I see how much math and testing go into it. This gives me confidence that when a machine says it can handle 50 tons, it truly can, provided we follow the instructions.
I also notice that buyer feedback helps refine these capacity ratings. If a customer frequently loads a machine near its limit, the manufacturer might get data on wear rates. This data can prompt design updates, such as thicker steel channels or improved bearings. That ongoing improvement process often leads to upgraded models with better performance.
I have learned that maximum capacity is not just about weight. It is about safe rotation, stable support, and mechanical durability. Manufacturers aim for a consistent flipping motion under maximum load. They do not want the coil to jerk or shift unpredictably. That can pose hazards for operators and equipment. A stable, controlled rotation is a sign that the upender is well within its safe limits.
Manufacturers also clarify the difference between rated capacity and absolute maximum capacity. Rated capacity is the best practice limit. Absolute maximum might be slightly higher but not recommended for regular use. If you need to push beyond that, you should ask for a custom design. In my experience, going beyond the rated capacity can shorten the machine’s lifespan and risk operator safety.
Why Does Coil Diameter Matter?
I notice that some people only focus on coil weight. They overlook coil diameter. That can lead to an upender mismatch and wasted money.
Coil diameter affects the cradle design and the machine’s turning radius. A larger coil diameter often requires stronger support structures.
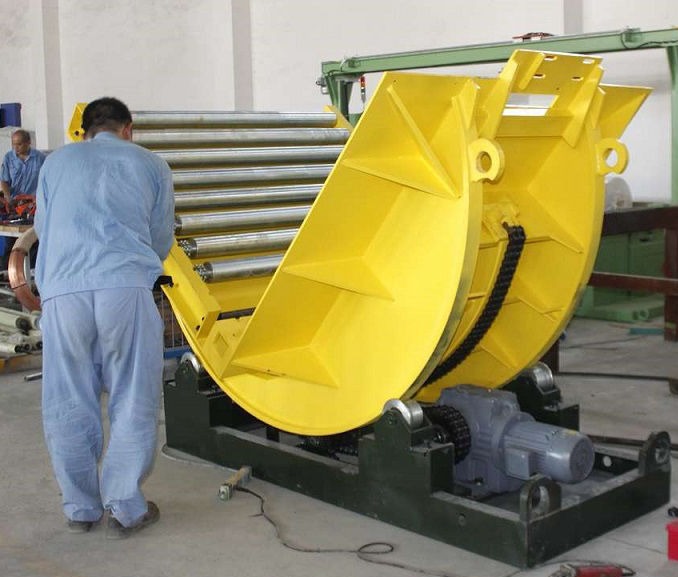
Dive Deeper into the Importance of Coil Diameter
I want to explain coil diameter in more detail. When a coil is larger, it can shift the center of gravity during rotation. Manufacturers consider the cradle’s shape and how the coil sits. If the coil is too wide or too tall, it might tip or not fit securely. This could damage the coil or strain the upender’s frame.
There is a geometric aspect to flipping a large-diameter coil. The rotation arc becomes wider, so the upender must have enough clearance to rotate the coil freely. If the facility has limited floor space, a big coil might collide with nearby equipment. That is another reason coil diameter specifications matter.
I have seen some operators assume that if the coil is within the upender’s weight limit, they can flip it. They forget to check diameter. The coil might physically fit on the cradle but not allow enough room for a safe rotation. The manufacturer usually provides maximum coil width and outer diameter guidelines. These guidelines are as important as the weight rating.
Let me break it down into smaller points:
- Cradle Width: The cradle must fit the coil’s width so it remains stable and does not overhang.
- Coil Height: A taller coil can shift the center of gravity higher, making it harder to rotate smoothly.
- Rotation Radius: A bigger coil needs more room to swing while flipping. This can influence upender design and placement.
- Load Distribution: A wide coil may spread load differently than a narrow one, impacting how the frame handles stress.
Manufacturers sometimes offer multiple cradle sizes or adjustable designs to accommodate different coil diameters. They may include features like adjustable guide rollers or removable sidewalls. That flexibility helps if you flip coils of varying sizes on the same machine. However, if you handle extremely large diameters, you might opt for a custom cradle.
In addition, coil diameter can affect the torque needed from the motor or hydraulic system. A heavier coil with a modest diameter might be easier to flip than a large-diameter coil with the same weight. The farther the load’s mass extends from the pivot point, the more torque is required. Manufacturers account for these torque calculations when determining the machine’s drive components.
Below is a table that outlines diameter-related factors:
Diameter Factor | Effect on Upender | Possible Outcome |
---|---|---|
Center of Gravity | Shifts with larger diameter | May cause imbalance if not designed |
Cradle Fit | Requires correct width & depth | Prevents coil tipping |
Torque Demand | Increases with larger radius | May need stronger drive motor |
Clearance Space | Wider arc for rotation | Influences factory floor layout |
I recall a situation where a colleague installed an upender rated for 30 tons. They had coils that weighed under that limit. But the coils were unusually large in diameter. During rotation, the coils grazed nearby equipment because the clearance was not accounted for. This taught me the importance of diameter, not just weight.
When deciding on an upender, I ask about both weight capacity and coil dimension limits. I also consider the path the coil will travel once flipped. I want to avoid collisions with walls or machines. I remind people that space planning is as important as picking the right capacity. A coil might technically fit on the cradle, but if you do not have enough open floor area for the coil to rotate, you have a problem.
In my experience, diameter issues often surface when operators try to push the machine’s boundaries. They might think a few extra centimeters will not matter. But a slight increase can shift the coil’s geometry enough to stress the cradle. Over time, that leads to wear or mechanical failure. I always advise a safe margin. If your coil diameter is near the machine’s upper limit, ask the manufacturer for confirmation.
Are There Other Factors That Influence a Coil Upender’s Limits?
I notice many questions about weight and diameter. People sometimes forget about other constraints like coil material or special configurations.
An upender’s maximum coil size also depends on the cradle’s design, power supply, and how the coil’s edges or shape might affect handling.
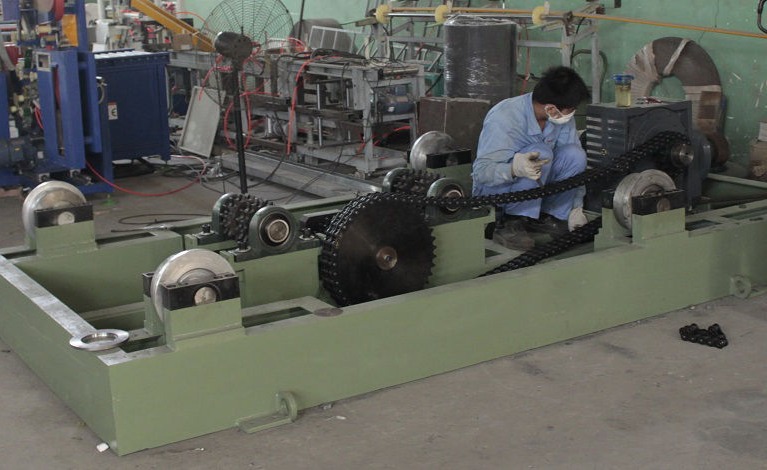
Dive Deeper into Additional Constraints
I want to focus on less obvious variables. First, coil material can play a role. A steel coil might weigh the same as an aluminum coil, but the steel coil could be denser and smaller in diameter. An aluminum coil might be bigger for the same weight. That can change how the upender clamps and rotates the load. Also, certain alloys might have sharper edges or more fragile surfaces, requiring specialized cradles or extra padding.
Second, coil width is important too. If a coil is very wide, it can shift the load distribution across the cradle. The upender might handle the total weight, but if the coil extends beyond the cradle’s sides, you risk instability. This could also lead to problems securing the coil. I believe it is essential to measure both coil width and diameter to ensure a proper fit.
Third, power supply can limit an upender’s performance. Some machines need higher voltage or a certain hydraulic pressure to flip heavier coils. If your plant does not have the right power infrastructure, the upender might not function at full capacity. This can be an unexpected bottleneck. I recommend checking the machine’s requirements and verifying your facility can support them.
Fourth, environmental factors matter. In dusty or humid environments, mechanical parts can wear faster. The upender’s capacity rating typically assumes normal working conditions. If you operate in extreme heat or near corrosive materials, you may have to adjust service intervals. If the environment is harsh, moving parts might degrade. That could lower the machine’s real-world limits over time.
Fifth, specialized coil shapes or packaging can introduce challenges. Some steel coils have paper wraps or plastic layers around them. These wraps might shift if the coil is not perfectly centered. That can cause slippage during rotation. A standard cradle may not hold a uniquely shaped coil without custom fixtures. When you buy an upender, you should mention any special coil wrapping or irregular shapes.
Sixth, operator experience can influence safe capacity. Even if the machine is rated for 30 tons, an inexperienced operator might fail to position the coil properly. This can lead to uneven load distribution or improper clamp pressure. Training ensures that staff place coils in the ideal position every time. That helps the upender work at its best without risk to people or products.
Here is a concise table covering these extra factors:
Factor | Why It Matters | Possible Impact |
---|---|---|
Material & Density | Affects coil size for same weight | Cradle design adjustments |
Coil Width & Shape | Influences load distribution and stability | May need special cradle features |
Power Supply | Determines if machine can run at full rating | Can reduce effective capacity |
Environment & Conditions | Causes faster wear under heat or dust | More frequent maintenance |
Operator Skill | Ensures correct placement and safe operation | Lowers risk of mishaps |
I recall a friend who used an upender for coated coils. The protective film on the coils was slippery. When the machine flipped them, the coils shifted slightly in the cradle. They had to add non-slip pads and adjust clamp pressures to keep everything aligned. That small tweak solved the issue, but it reminded me that coil wrapping can change how the coil behaves on the upender.
In another instance, I saw an upender installed in a plant that ran multiple shifts in a hot environment. The hydraulic fluid overheated on long shifts. Production slowed until they installed a cooling system. That was an example of the environment impacting the upender’s real capacity. The rated capacity was correct in normal conditions, but high temperatures changed performance. After adding a fluid cooler, they resolved the problem.
I want to stress that the largest coil size is not just about raw weight or diameter. There are details like coil shape, factory layout, and user experience. Each factor can limit or enhance the upender’s performance. If you talk to the manufacturer with all these details, they can give a more accurate assessment of how big a coil you can handle. I encourage open communication so you do not buy an upender that is either too big or too small.
Conclusion
I believe that a coil upender’s largest coil capacity depends on weight, diameter, and other factors. With the right design, it can safely handle huge loads.