What Is the Coil Upender?
I once faced a real struggle when I tried to flip a massive steel coil in a cramped space. My team looked at me with uncertainty, and we realized we needed a safer and more reliable solution.
A coil upender is a device that helps rotate large coils from a horizontal to a vertical position, or vice versa, without manual lifting or pushing. It uses sturdy frames and a powered mechanism to reduce hazards, save effort, and improve productivity by maintaining steady control over the coil during the flipping process.
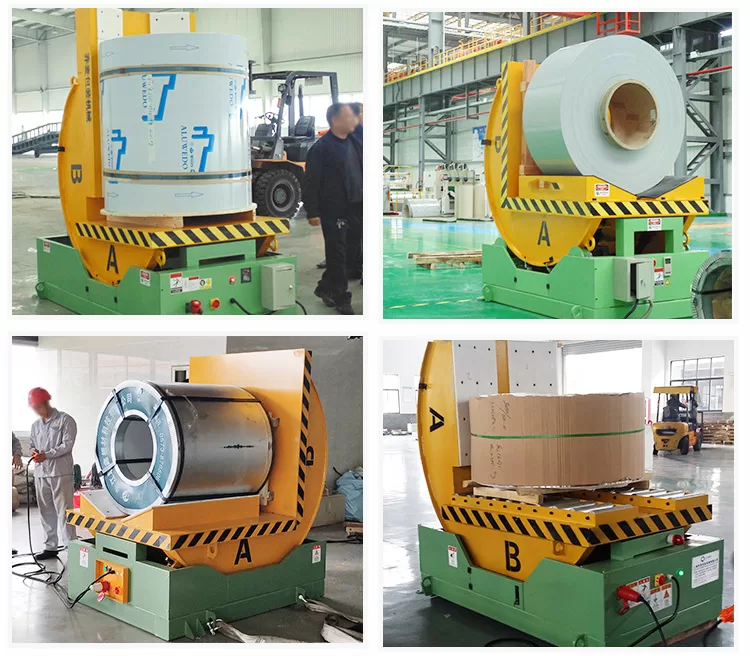
I discovered how much time and frustration a coil upender can save. I also learned that it reduces the chances of accidents caused by makeshift flipping methods. Now, I will share what I know about coil upenders and how they can make industrial handling more efficient.
Which Materials Are Compatible with a Coil Upender?
I remember when I managed a range of materials, including steel, aluminum, copper, and even specialty alloys. I wanted to know if a single upender could handle them all without compromising safety or efficiency.
A coil upender can handle steel coils, aluminum coils, copper coils, and other wound materials like wire or cable spools. It supports different coil widths, diameters, and weights. This adaptability allows one device to serve multiple material types, streamlining many industrial processes by reducing the need for separate handling systems.
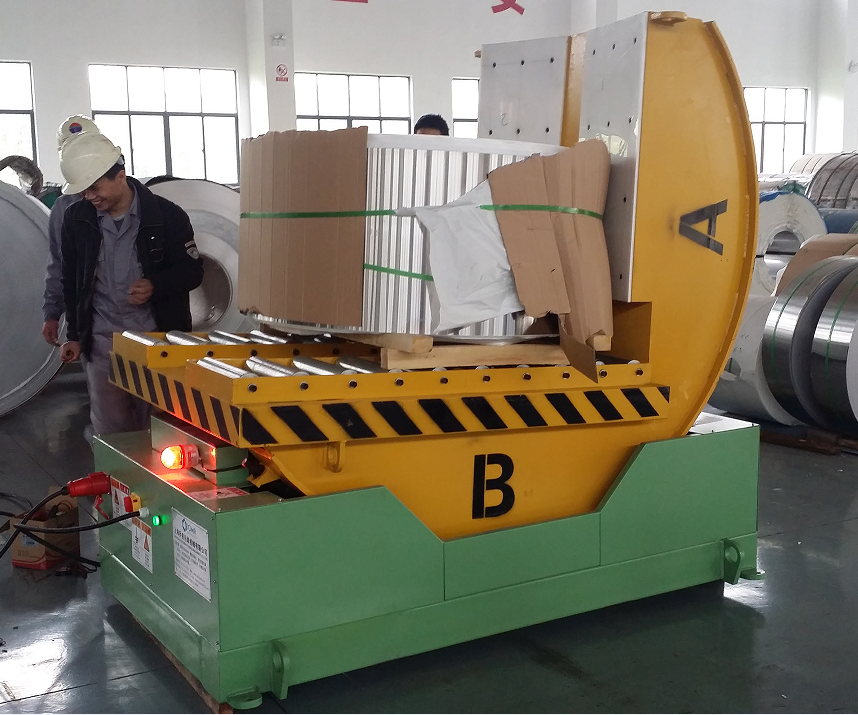
Understanding Material Compatibility in Detail
I want to go deeper into how a coil upender deals with different materials. I have seen heavy steel coils demand more robust frames and higher torque capabilities. I have also seen lighter materials, such as aluminum or copper, need a gentler approach, where padding and even speed controls become crucial. In my experience at FHOPEPACK, we place special attention on designing coil upenders that handle various materials with care. We know that every coil has a distinct density, diameter, and surface finish.
When I first explored coil upenders, I talked to experts who explained why design features matter for material compatibility. They said that controlling movement is essential. Many upenders come with adjustable clamping mechanisms. These adjustments help avoid coil damage. It also helps prevent dents, scratches, or shifting during rotation. That can be vital for sensitive materials like thin aluminum or finely finished copper. The last thing I want is a coil that has a damaged edge or a distorted shape, which leads to extra costs.
Over time, I made a chart to compare how different materials interact with coil upenders. I realized it was important to note weight ranges, tension, and thickness. Coil upenders often have a maximum capacity, and it must match my plant’s heaviest coils. The key is to avoid overloading the system, which could lead to mechanical failure or uneven flipping.
Below is a simple table that shows some typical materials and the related handling aspects:
Material | Key Considerations | Example Industries |
---|---|---|
Steel | High capacity, stronger hold | Automotive, Construction |
Aluminum | Lighter weight, gentle handling | Aerospace, Packaging |
Copper | Surface protection, smooth rotation | Electrical, Plumbing |
Wire/Cable | Narrow coils, speed control | Electronics, Communications |
I remember one project with David, a specialist who manages steel coils in the automotive sector. He stressed that his steel coils are often heavier than others, which meant we needed an upender with robust gearing and frames. We ended up selecting an upender from our facility in Northern China. It was designed for steel coils that weighed well over the standard limit. That project taught me that understanding each material’s characteristics is the key to choosing the right coil upender.
For aluminum coils, I recall how important it was to add some protective materials and adjust the machine’s flipping speed to prevent dents. I learned that controlling each stage of the flip matters more for lightweight coils because they can shift out of place more easily. The coil upender’s hydraulic or mechanical motion must be smooth and consistent to avoid sudden jolts.
I also saw how crucial it is for the upender to accommodate various coil diameters. Some facilities handle coils of many sizes. The same upender should adapt to these differences. That means either an adjustable platform or a design that accommodates a wide diameter range. This feature helps me reduce downtime because I do not have to switch equipment for each coil size.
In summary, different materials come with different demands. A coil upender with the correct specifications, adjustable clamping, and protective surfaces helps me handle multiple coil types without major modifications. It saves money because I do not have to buy separate equipment for each type of material. It also gives me peace of mind because I know my team can handle different coils with minimal risk of damage. A well-designed coil upender is a flexible tool in diverse manufacturing environments.
How Much Time Does It Take to Upend a Coil with a Coil Upender?
There was a period when my team tried to flip coils manually, and it was a slow and cautious process. We lost productivity and worried about safety. I started investigating how fast a coil upender can handle flipping times.
Most coil upenders complete a full flip in a short time, often under a minute, depending on weight and size. This speed is usually consistent because of powered hydraulics or mechanical systems, which allow fast flipping with steady control. Operators can save many hours each shift by reducing manual flipping.
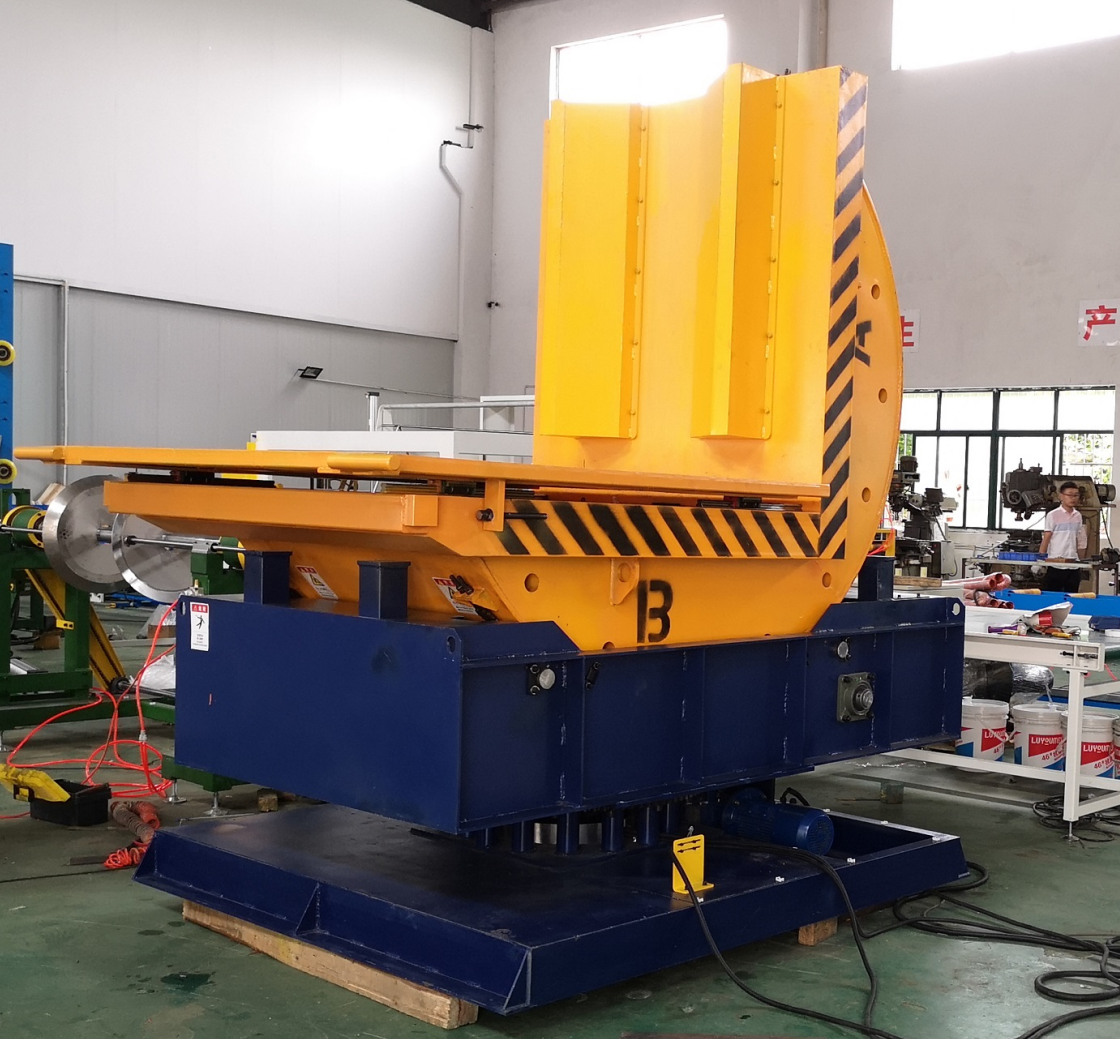
Delving into Flip Times and Efficiency
I began timing how long it took to rotate various coils in my facility. We had smaller coils that took barely 20 seconds to flip. Larger ones went closer to a minute. This difference happens because heavier coils need more careful rotation. Some upenders use variable speed drives. Others rely on fixed speeds. When we want consistent timing, a variable speed drive can be useful if we handle coils of different weights.
I discovered that flip times also depend on the type of power system. Hydraulic upenders might have a different rotation speed than mechanical or motor-driven upenders. When I looked into FHOPEPACK’s coil upenders, I found that many models let me tweak certain parameters. If I needed gentler flipping, I could set a slower speed. If I needed to hurry up, I could increase it a bit, as long as it stayed within safe limits.
During a busy production day, flipping efficiency has a big impact on overall workflow. If each coil takes too long to rotate, I risk delays that slow down packaging, shipping, and other parts of the process. Every second counts when I have a daily production target. My colleagues also told me that shorter flip times cut down the chance of worker fatigue. With a coil upender, workers do not need to wrestle with heavy loads, so they stay fresh and more engaged.
I also noted that training plays a role in flip time. A well-trained operator knows how to position the coil properly on the platform. They also know how to center it before flipping. If the coil is off-center, flipping might become unbalanced, and that may cause extra time or equipment stress. Taking a few seconds to place the coil correctly can lead to a smoother flip and less time wasted.
Here is a quick breakdown of factors that can affect flip time:
Factor | Impact on Flip Time |
---|---|
Coil Weight | Heavier coils may require slower rotation. |
Coil Diameter and Width | Larger coils might need more handling time. |
Upender Power Type | Hydraulic vs. mechanical can affect speed. |
Operator Skill Level | Proper placement can speed up flipping. |
Safety Settings | Additional braking or gradual movement may add a few seconds. |
From my experience, once everything is set up properly, the flipping itself is usually fast. What often takes more time is positioning the coil and making sure people follow safe procedures. But with a well-planned system and the right operator training, the flipping time becomes predictable and efficient. In a high-volume environment, this steady rhythm keeps the rest of the production line on track.
What Kind of Power Source Does a Coil Upender Require?
I used to assume that coil upenders only came in one configuration. Then I realized there are different ways to power them, and this affects maintenance, energy usage, and even noise levels.
Most coil upenders run on electric or hydraulic power sources, or a combination of both. Electric motors drive mechanical gears or pumps, while hydraulic systems use pressurized fluid to rotate the coil. The choice depends on capacity needs, usage environment, and available infrastructure.
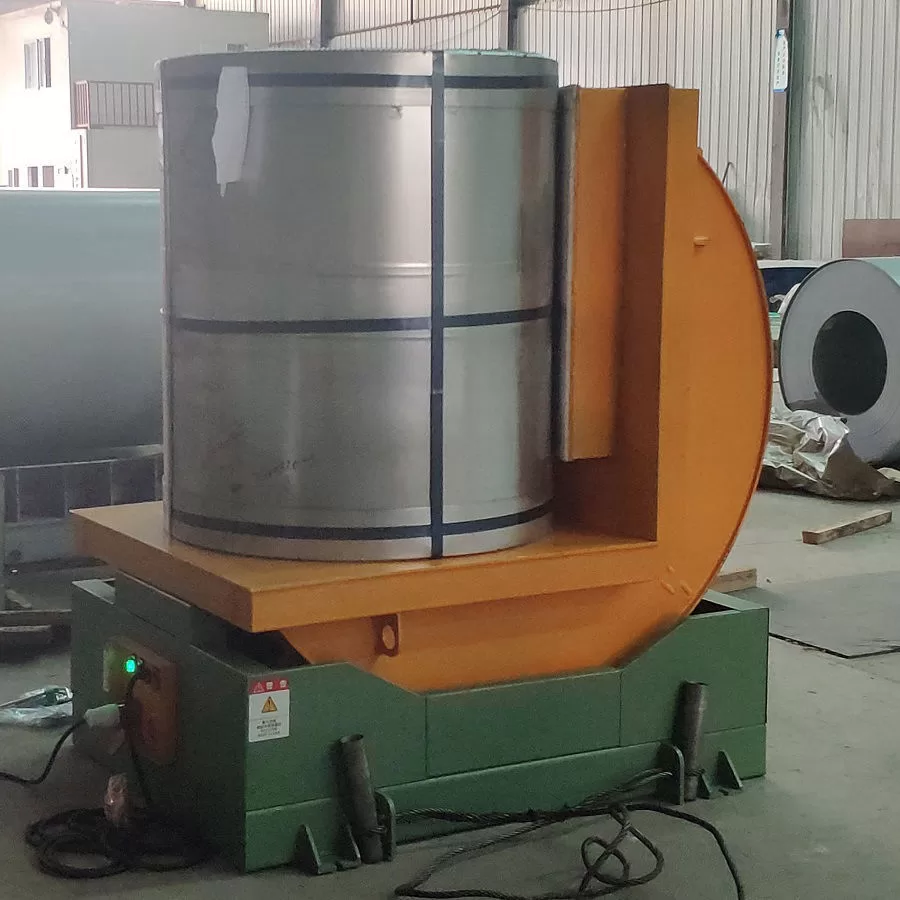
Exploring Power Options for Coil Upenders
I first encountered a purely hydraulic coil upender in an old facility. It used a hydraulic pump that powered a cylinder to lift and rotate the coil. It was strong and could handle very heavy loads. However, it came with routine maintenance requirements, like changing hydraulic oil, checking seals, and ensuring no leaks. Although I appreciated its power, I also had to deal with the costs of hydraulic fluid and the potential mess if a leak occurred.
Later, I saw a mechanical coil upender that worked with an electric motor and a gear system. It was simpler to maintain since I did not have to worry about fluid leaks. But it might not handle massive loads as easily as a hydraulic system. It was also somewhat louder when the gears engaged, though that was manageable in a typical factory setting.
Then, I came across some hybrid systems that use an electric motor to drive a hydraulic pump. These systems combine the best of both worlds. They can deliver high torque and capacity while providing the ease of an electric interface. I liked that approach because it gave me the power I needed for heavier coils while relying on standard electricity. I did not have to set up a separate power line just for hydraulics. Instead, the electric motor drove the pump, and I only had to ensure I had enough electrical capacity in my facility.
Energy usage can be a factor too. If I run an upender many times a day, I need to consider operational costs. Some advanced models come with variable frequency drives that let me adjust speed and torque. This control can reduce power consumption when flipping lighter coils. It also helps with precise motion control, which is nice if I do not want sudden surges that could damage delicate materials.
Below is a small table that compares key points of these power options:
Power Source | Pros | Cons |
---|---|---|
Hydraulic | High capacity, strong torque | Possible fluid leaks, more maintenance |
Mechanical (Electric) | Simpler, less messy, easy to maintain | Might struggle with extra-heavy loads |
Hybrid | Combined benefits, good for varied loads | More complex system, higher cost |
In my own facility, I leaned toward a hybrid design because we handle steel coils of various weights. We needed the torque that hydraulic systems offer, but we liked the clean and direct control of an electric motor. The brand FHOPEPACK helped me understand how to optimize our power selection. They showed me how each model fits into a certain environment, and they guided me on power requirements. If I have a limited electrical infrastructure, I might need to work with local electricians to upgrade the supply. That ensures the coil upender runs smoothly without overloading the system.
David, my colleague, often shared how his company in the United States must follow strict safety standards. They prefer equipment that meets local electrical codes. He values designs that are easy to integrate into existing power grids. He said his team sometimes invests in coil upenders that come with built-in safety features, like emergency stops and limit switches. These features not only guard against power surges but also protect operators in case of unexpected motion.
From what I have seen, the right choice of power source depends on the load capacity, budget, and maintenance preferences. If I know that I will handle consistently heavy coils, a robust hydraulic system might be my best choice. If I prioritize simpler maintenance and smaller loads, a mechanical or electric upender could work. If I want a balance, a hybrid system is a good option. No matter what I choose, I believe a proper power source ensures smooth and stable performance, which is crucial for flipping large coils safely. That peace of mind is something I can truly appreciate.
Conclusion
I have found that a coil upender is a dependable tool for flipping large coils. It saves time and reduces risk. It also accommodates different materials, offers fast flipping speeds, and uses various power sources. I believe it is a worthwhile investment that boosts efficiency and safety.