I notice that many production managers feel uneasy when they handle steel and aluminum coils. They worry about damage, workplace accidents, and increased costs. They want a clear plan to protect their products and ensure efficiency .
The best packaging solutions for steel and aluminum coils focus on robust wrapping, secure strapping, and reliable protective materials. I prioritize automated coil wrapping machines, sturdy edge protectors, and stable saddles or cradles. These steps minimize the risk of denting, corrosion, and scratching, and they lower the chance of costly reworks .
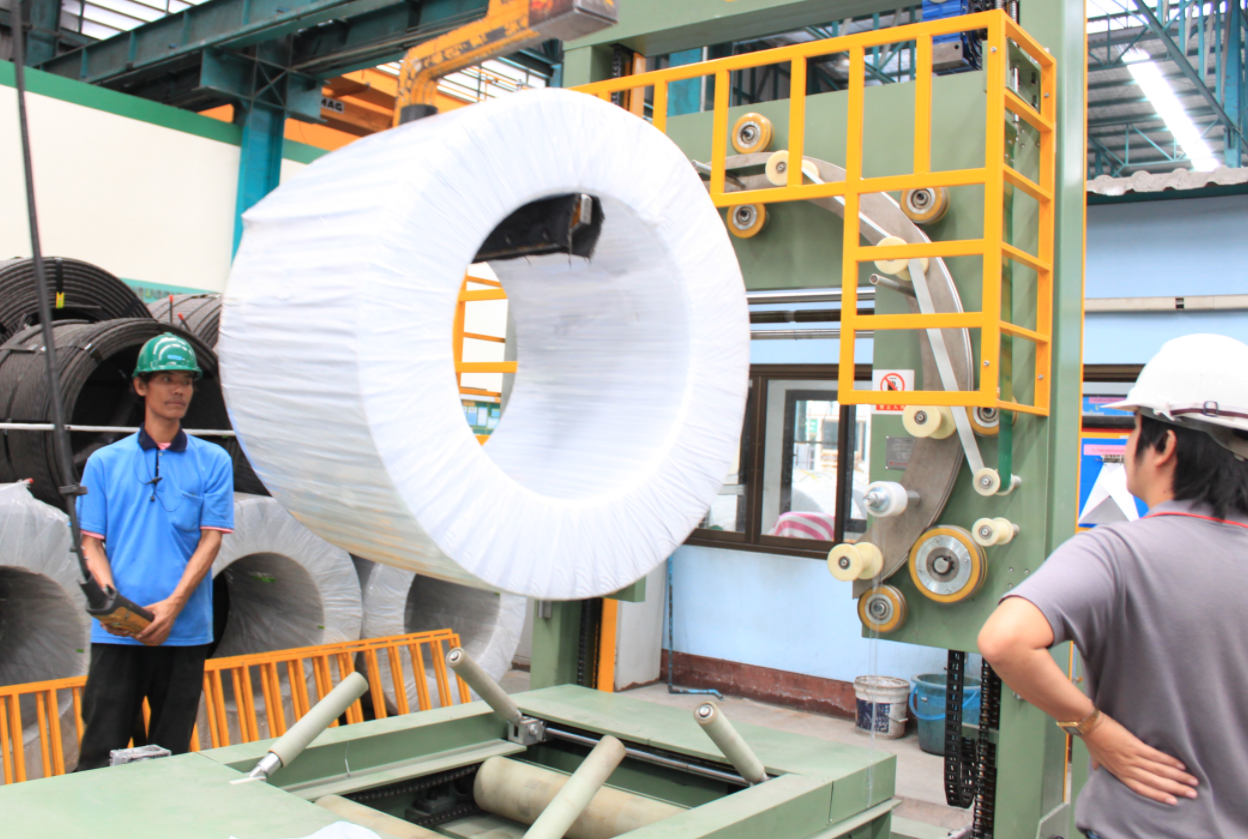
0 "Protective packaging for coils")
I have met many professionals who have similar questions. They want tools that improve coil packaging without complicating their workflows. I will share my insights on the best ways to package steel and aluminum coils safely. Let us explore the key points now.
Why Is Automated Coil Wrapping Important?
I recall my first time encountering an automated coil wrapping machine. I was surprised to see how smoothly it worked and how it boosted productivity. The old manual methods felt slow and inconsistent (30 words).
Automated coil wrapping offers precise tension control, even coverage, and reduced worker fatigue. It prevents sharp edges from being exposed. I believe this technology lowers packaging errors. It also helps standardize coil appearances (50 words).
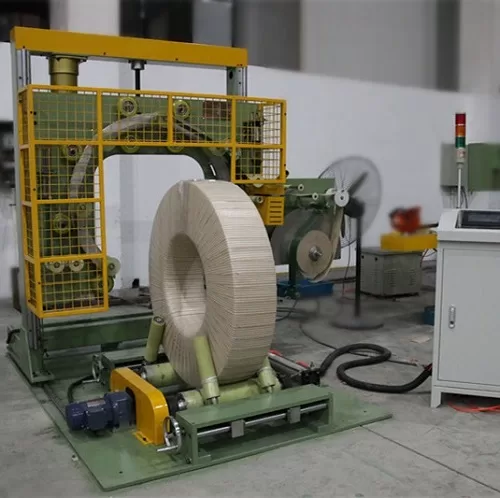
"Efficient wrapping equipment")
The Impact of Automation on Coil Packaging
I have witnessed how automation can transform entire production lines. Automated coil wrapping saves time and resources by removing the guesswork from manual wrapping. It removes the problem of uneven film layers or loose edges. It also helps me maintain a clean, consistent look that improves brand presentation.
Key Benefits of Automated Wrapping
Benefit | How It Helps |
---|---|
Consistent Tension | Keeps each coil firmly wrapped, reducing movement |
Faster Operations | Speeds up packaging, which is vital for tight schedules |
Lower Labor Costs | Reduces manual tasks and frees workers for other jobs |
Reduced Waste | Uses the correct amount of film or protective materials |
Better Safety | Lowers the chance of injuries from manual handling |
I also rely on automation to record data about each coil. That data includes coil size, wrapping speed, and number of wraps used. This data helps me spot trends or potential issues early. For instance, if I see an increase in film usage over time, I can investigate and make corrections. Automation simplifies troubleshooting by providing measurable insights.
I think about David, a purchaser in the steel coil sector. He manages tight production schedules. His team used to wrap coils by hand. They found that, during peak demand, operators rushed the process. That often led to coils not getting enough layers of film. This risked exposure to moisture, which caused rust or surface damage. Once David’s company implemented automated wrapping, these issues dropped drastically. Workers no longer had to guess how many times they needed to walk around the coil. The machine handled that part, delivering uniform coverage every time.
I also notice how some people fear that automated machines are too costly. However, I have seen that the return on investment quickly appears when we factor in lower rework rates, fewer damaged coils, and reduced labor expenses. Automated systems also help me keep pace with increased orders. If I rely only on manual labor, I may struggle to scale up effectively. Automation allows me to adjust wrapping parameters on the fly, using intuitive controls. That means less downtime for retooling or changing materials. Over time, the system pays for itself through consistent, error-free performance.
In my view, the real question is not whether automation is worth it. The question is whether I can afford to continue with manual processes that can cause subpar coil protection and waste. Automated coil wrapping is a direct path to better efficiency, improved quality, and stronger customer satisfaction. (261 words)
How Does Protective Strapping and Edge Guarding Help?
I remember one instance when I inspected a coil shipment that arrived with broken straps. The edges had cut into the strapping, creating a dangerous situation. That made me realize how vital proper straps and edge guards are (30 words).
Strapping secures the coil in place during transport or handling. I add edge guards to lessen pressure on coil corners and to safeguard strapping from fraying. This reduces accidents and preserves product integrity (50 words).
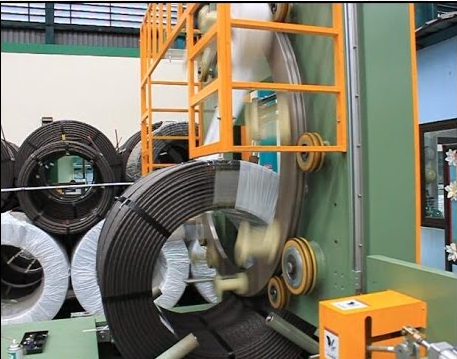
"Securing coil edges")
Securing Coils with the Right Tools
Strapping and edge guarding are not just add-ons. They are critical to protecting steel and aluminum coils, especially when these coils travel over long distances. I know that even a small shift during transit can lead to scratches, dents, or even full coil collapses. That can lead to rejections from customers or high repair costs.
Choosing Proper Strapping Materials
I usually choose materials like polyester or steel straps, depending on the coil’s weight and how far it must travel. Polyester straps offer good tension retention and flexibility. Steel straps provide high break strength for heavy coils. I like to weigh coil dimensions, overall mass, and shipping duration before making a choice.
Material | Strength | Ideal Application |
---|---|---|
Polyester | High elasticity | Medium to heavy coils, long distances |
Steel | Very high strength | Very heavy coils, short or rough handling |
Woven Straps | Good adaptability | Light to medium coils, less demanding routes |
Role of Edge Guards
Edge guards are small protective elements placed where straps make contact with the coil. They distribute pressure evenly and help the strap grip the coil without biting into the metal. I see this as a simple yet powerful step. Without edge guards, the strap can cut into the coil’s edges, causing paint chips, scuffs, or deeper damage. That can result in rust or performance issues later.
I use edge guards as part of a bigger protective setup. This might include stretch wrap, rust inhibitors, and corner protectors made from cardboard, plastic, or metal. When I follow a consistent routine of placing edge guards, I significantly reduce friction and wear on both the coil and the strapping.
During a recent project, I found that one of my clients shipped aluminum coils across multiple states. The route involved rough roads. Vibrations caused the coils to shift. By upgrading their strapping system and introducing edge guards, they dropped coil damages by a huge margin. The cost of the guards was minimal compared to the value they protected. They also saved on rework and improved their reputation for delivering perfect coils.
In my opinion, strapping and edge guarding are fundamental. They are like seat belts for the coil. They are not expensive, but they make a major difference in preventing accidents and damage. This is especially true if you pair them with an automated wrapping process. The synergy between these elements creates a robust packaging approach that can handle diverse transport or storage conditions. (263 words)
What Role Do Coil Saddles and Pallet Inverters Play?
I often see heavy steel coils roll or shift when placed on a flat surface. That creates safety concerns and can lead to permanent coil deformation. Coil saddles and pallet inverters solve these issues (30 words).
Coil saddles keep the coil stable by matching its circular shape. Pallet inverters handle load flipping and reorientation. I recommend both to protect coil edges and help workers handle products more easily (50 words).
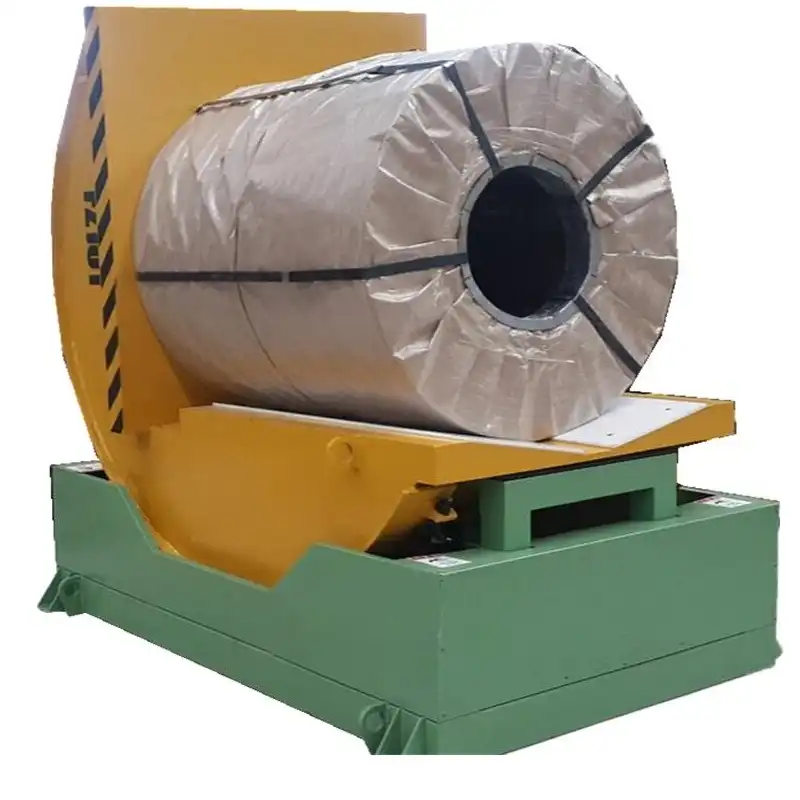
"Stable coil handling")
Enhancing Stability and Maneuverability
Stable handling forms the core of effective packaging. I often combine coil saddles with other systems, such as horizontal wrappers or upenders, to achieve a seamless process. This ensures that the coil is secure from the moment it arrives on the production floor to the time it ships out.
Coil Saddles and Their Advantages
Coil saddles, also referred to as coil cradles or V-shaped supports, hold the coil in a secure position. They prevent rolling, especially when the coil is in a horizontal orientation. I have found that using coil saddles also helps maintain the coil’s shape. This is crucial for thin-gauge aluminum coils that are prone to bending. Steel coils, being heavier, also need stable cradles to prevent sudden rolling.
Saddle Type | Suitable Coil Weight | Recommended Usage |
---|---|---|
Fixed V-Saddle | Medium to Heavy | Keeps larger coils from moving |
Adjustable Saddle | Varying Weights | Accommodates different coil sizes |
Modular Units | Custom Ranges | Flexible setup for mixed loads |
Pallet Inverters for Better Load Management
Pallet inverters flip or rotate a loaded pallet. I see them used in scenarios where workers need to switch the orientation of the product quickly without manual labor. With coils, a pallet inverter can make it simpler to handle the coil’s orientation. This is helpful if the coil needs to be turned for wrapping or loaded onto a new pallet. It reduces physical strain on operators and lowers the risk of dropping or damaging the coil.
I think about the times when I had to coordinate coil movements in a busy warehouse. Operators tried to maneuver heavy coils by tilting pallets with forklifts. This approach was risky. The coil could shift or slip, leading to injuries or product loss. When we introduced pallet inverters, we saw a drastic drop in mishaps. The machine made it easy to flip or tilt the load in a controlled manner. Operators felt safer, and we minimized coil scuffs.
Optimizing the Entire Workflow
Coil saddles and pallet inverters integrate well with automated wrapping machines. I like to set up a flow: the coil arrives, it is placed on a saddle, it may be flipped or rotated if needed, then it goes straight into the wrapper. This streamlined approach avoids unnecessary coil handling. That reduces the chance of forklift damage or collisions with other items. It also speeds up the packaging cycle because each machine is designed to handle a specific step.
I have realized that many packaging problems come from poor workflow design rather than a lack of technology. Even the best coil wrapper will not help if the coil is misaligned on a forklift or stored improperly. By investing in coil saddles and pallet inverters, I add important building blocks for a complete packaging line. These elements ensure the coil remains stable, easy to move, and ready for high-quality wrapping or strapping. A stable coil is a safe coil, which translates to fewer quality complaints and a smoother operation overall. (285 words)
Conclusion
Optimal coil packaging involves automated wrapping, sturdy strapping, edge guards, and proper support. I rely on coil saddles, pallet inverters, and reliable materials to protect steel and aluminum coils from damage, ensuring they arrive in prime condition (44 words).