Coil wrapping machine also name coil packing machine that are a vital asset in industries requiring secure, efficient packaging solutions. While the initial purchase of these machines is often carefully planned, the after-sales service provided by the manufacturer is equally critical. An efficient after-service program not only ensures the machine’s longevity but also minimizes downtime, enhances productivity, and builds trust between the buyer and the supplier.
Imagine investing in a sophisticated coil wrapping machine that promises top-notch performance, only to face unexpected malfunctions shortly after installation. Without robust after-service, troubleshooting such issues can quickly spiral into frustration, financial losses, and operational inefficiencies. This is why understanding the scope and quality of after-service is crucial when selecting a supplier.
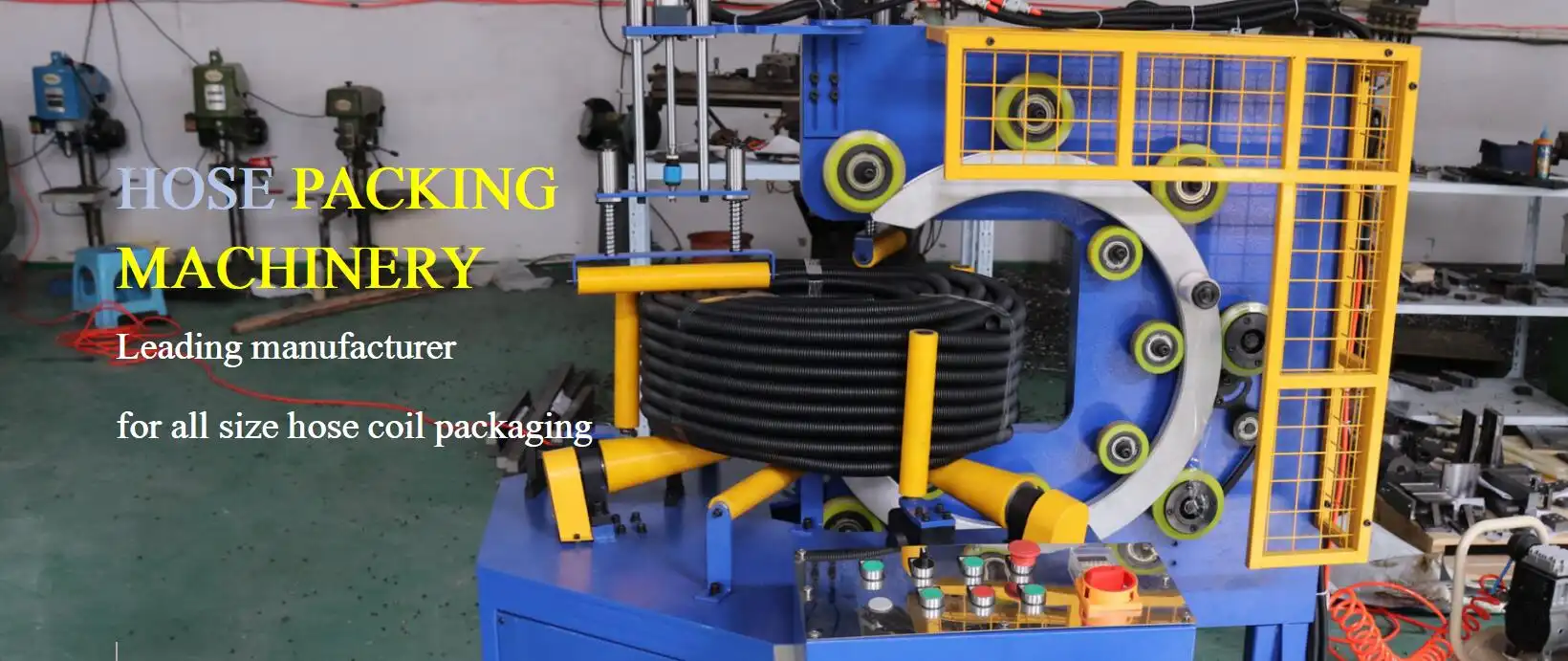
After-service encompasses a wide range of support activities provided after the machine’s installation. It includes training, maintenance, technical support, replacement of parts, and warranty coverage. The question is, how do manufacturers differentiate their after-service programs, and what should buyers expect?
1. What Should You Expect from Installation and Training Services?
1.1 Installation Process and Ensuring Smooth Operations
The installation process for a coil wrapping machine is more than just assembling parts. It involves aligning the machine with existing workflows, calibrating for precision, and running initial test cycles. Manufacturers typically dispatch skilled technicians to oversee the installation, ensuring every detail is fine-tuned.
When installation is handled professionally, it minimizes the risk of errors and prepares the machine for optimal performance. A key aspect of this phase is clear communication between the supplier and the buyer, as it ensures that both operational goals and technical requirements are met.
1.2 Comprehensive Training Programs
Training programs are the cornerstone of effective machine utilization. Operators, maintenance personnel, and supervisors should all be educated on various aspects of the machine. This includes proper operation, basic troubleshooting, and safety protocols.
Training Program Features | Benefits |
---|---|
Hands-on Operational Training | Reduces errors and increases efficiency |
Safety Protocol Workshops | Ensures workplace safety and compliance |
Maintenance Best Practices | Extends machine lifespan and reliability |
Studies indicate that companies offering structured training reduce machine-related downtime by up to 30% compared to those without. Such programs empower the team to handle minor issues, leaving only complex problems for technical support.
1.3 Addressing Common Post-Installation Concerns
A recurring issue in post-installation phases is a lack of understanding of machine settings, particularly in custom configurations. Manufacturers who offer prompt support during this stage stand out. By addressing questions or fine-tuning adjustments, they build confidence and trust with their clients.
1.4 Ensuring Continuous Support During Initial Operations
Support during the early stages of operation is non-negotiable. Buyers should expect real-time technical assistance to address unexpected scenarios. This often includes remote diagnostics or on-site support to ensure seamless functionality.
The true test of after-service lies in the supplier’s willingness to resolve issues swiftly. It’s not just about selling a machine; it’s about nurturing a long-term partnership.
1.5 Two Fact Statements with Explanations
- True: Comprehensive training programs significantly reduce operational errors and improve machine performance.
Explanation: Well-trained staff can manage machine operations more efficiently, preventing common errors that lead to downtime. - False: Manufacturers always provide unlimited free training sessions after installation.
Explanation: Most training programs are limited in duration or sessions and may require additional fees for extended services.
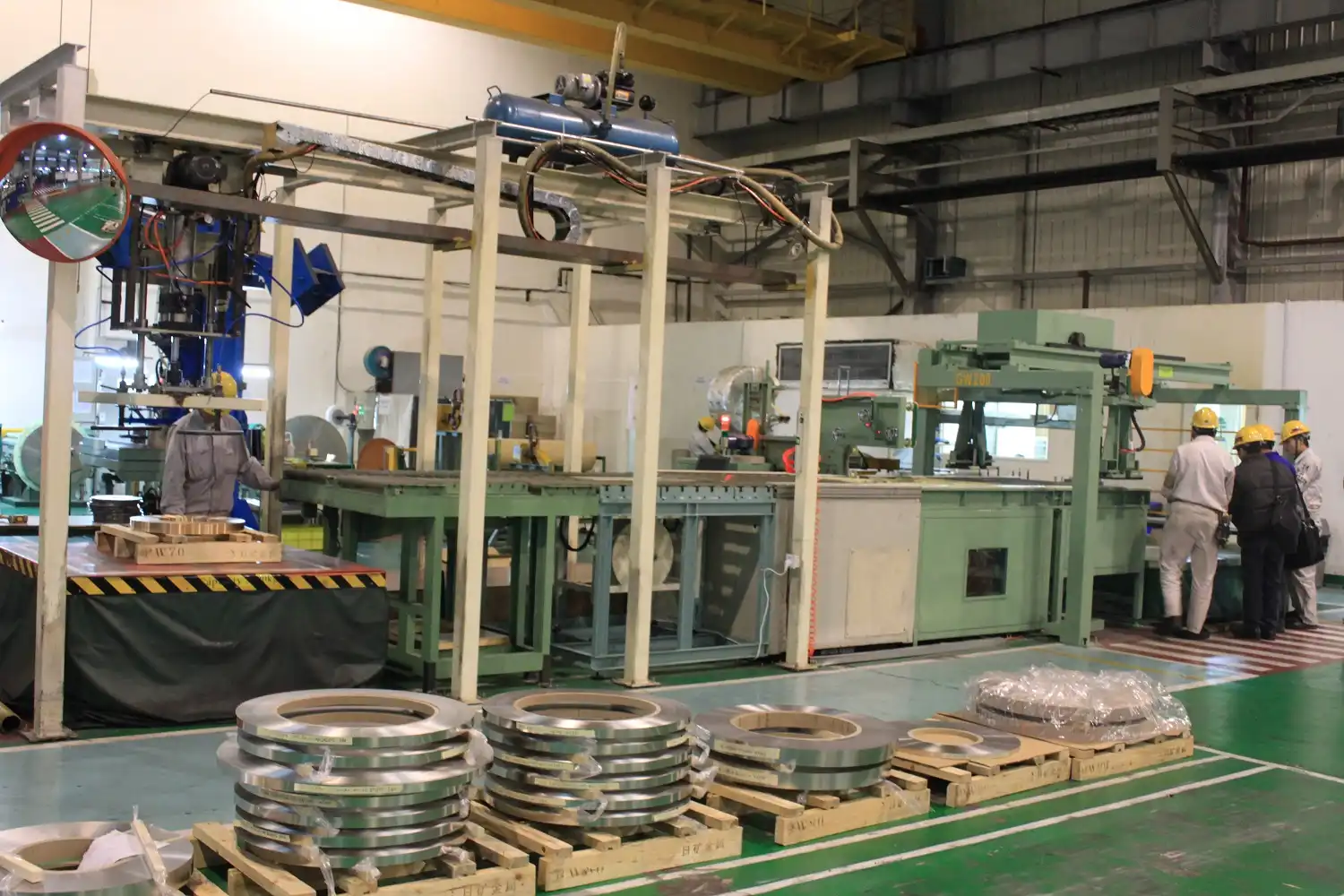
2. How Do Maintenance Plans Improve Machine Efficiency?
2.1 Routine Maintenance and Its Impact
Regular maintenance is critical for the long-term efficiency of a coil wrapping machine. Routine checks ensure that all components function optimally, identifying potential issues before they escalate into costly repairs. Manufacturers often provide detailed maintenance schedules tailored to the machine’s workload and operational environment.
Consider this scenario: a minor issue with the wrapping arm goes unnoticed during production. Over time, it could result in uneven packaging, increased material wastage, or even machine breakdown. Preventive maintenance programs address such problems proactively, saving both time and money.
2.2 What Maintenance Plans Include
Maintenance Plan Features | Description | Benefits |
---|---|---|
Scheduled Inspections | Periodic technical evaluations | Minimizes unexpected downtime |
Lubrication and Cleaning | Regular care for moving parts | Extends component lifespan |
Software Updates | Latest improvements for system functionality | Enhances machine performance |
Spare Part Replacement | Quick access to critical components | Reduces delays in production |
Statistics reveal that companies adhering to structured maintenance schedules experience 20% fewer breakdowns compared to those without. A well-maintained machine ensures consistent output and maintains product quality.
Featured Image: A detailed illustration of a technician inspecting a coil wrapping machine during routine maintenance.
2.3 Dive Deeper into Predictive Maintenance
Predictive maintenance goes beyond routine schedules by using advanced technologies to monitor the machine’s health. Sensors track real-time performance metrics, providing alerts when abnormalities arise. For instance, vibration analysis might reveal early signs of wear in critical components.
Predictive Maintenance Metric | Example Use Case | Benefit |
---|---|---|
Vibration Analysis | Detecting wear in motor bearings | Prevents sudden breakdowns |
Temperature Monitoring | Identifying overheating issues | Avoids major system failures |
Cycle Time Tracking | Monitoring wrapping cycle durations | Ensures consistent production speed |
Companies adopting predictive maintenance have seen a 25-30% reduction in unplanned downtime, making it a highly effective strategy for modern industries.
2.4 Conclusion
Maintenance plans are more than a safety net—they’re a commitment to operational excellence. By investing in both routine and predictive maintenance, businesses can maximize machine uptime, minimize costs, and maintain their competitive edge in the market.
2.5 Two Fact Statements with Explanations
- True: Predictive maintenance uses data-driven insights to prevent potential failures before they occur.
Explanation: This proactive approach allows manufacturers to address issues in advance, ensuring uninterrupted production. - False: All maintenance services are included in the initial purchase price.
Explanation: Many manufacturers offer maintenance plans as optional add-ons, often tailored to the buyer’s needs.
3. What Role Does Remote Monitoring Play in Modern After-Service?
3.1 Real-Time Monitoring and Diagnostics
Remote monitoring has revolutionized after-service by allowing manufacturers to oversee machine performance from afar. Using IoT sensors and cloud-based systems, technicians can diagnose issues without being physically present, reducing response times significantly.
For instance, if a machine exhibits abnormal cycle durations, the manufacturer can access performance logs and identify the root cause remotely. This capability not only minimizes downtime but also reduces the cost of on-site visits.
Key Features of Remote Monitoring | Benefits |
---|---|
Real-Time Alerts | Immediate notification of anomalies |
Performance Analytics | Comprehensive insights into machine efficiency |
Remote Adjustments | Instant corrections to minor settings |
3.2 Cost Benefits of Remote Service
Service Type | Average Cost Savings | Impact |
---|---|---|
Remote Diagnostics | 15-20% | Eliminates the need for travel |
Predictive Adjustments | 10-15% | Prevents potential machine downtimes |
Software Troubleshooting | 12-18% | Reduces physical repair needs |
With an increasing number of industries adopting remote monitoring, businesses report operational savings of up to 25%, alongside improved response times.
Featured Image: A visual representation of a dashboard displaying live data from a coil wrapping machine.
3.3 The Integration of Smart Technology
Smart technologies like AI and machine learning further enhance remote monitoring capabilities. These systems analyze vast amounts of data to predict trends, detect anomalies, and suggest corrective measures.
For example, an AI-enabled system might recommend adjustments to wrapping speed based on the weight and size of coils being packaged. Such insights improve overall machine efficiency and product quality.
3.4 Dive Deeper into the Benefits of Remote Support
Remote support extends beyond diagnostics. It facilitates software updates, operational guidance, and even virtual training sessions. These features eliminate geographic barriers, enabling manufacturers to provide world-class service regardless of location.
Remote Support Feature | Description | Example |
---|---|---|
Virtual Training | Online sessions for operator training | Step-by-step guidance on new features |
Software Patches | Updating machine software remotely | Fixing bugs or enhancing functionality |
Live Technical Assistance | Real-time troubleshooting via video or chat | Resolving operational issues instantly |
By leveraging these capabilities, businesses can enhance machine uptime by up to 35%, ensuring seamless operations.
3.5 Two Fact Statements with Explanations
- True: Remote monitoring reduces machine downtime by providing instant diagnostics and solutions.
Explanation: Remote systems can identify and address minor issues before they escalate, ensuring uninterrupted operations. - False: Remote support completely eliminates the need for on-site visits.
Explanation: While remote services handle many issues, complex mechanical problems may still require physical intervention.
4. Are Extended Warranties Worth Considering?
4.1 Understanding the Basics of Extended Warranties
Extended warranties provide additional coverage beyond the standard manufacturer warranty, ensuring long-term peace of mind. For coil wrapping machines, these warranties typically include protection against specific component failures, extended technical support, and discounted maintenance services.
Investing in an extended warranty is especially beneficial for businesses with high production volumes. The increased usage often leads to wear and tear, making extended coverage a cost-effective way to safeguard operations.
4.2 Analyzing the Costs and Benefits
Feature of Extended Warranty | Benefit | Cost Implication |
---|---|---|
Extended Coverage Duration | Reduces long-term repair costs | 10-15% of the machine’s cost |
Priority Technical Support | Minimizes downtime during emergencies | Included in premium packages |
Discounted Spare Parts | Lowers maintenance expenses | Savings of 20-30% on replacements |
A study of industrial equipment shows that businesses utilizing extended warranties reduce unexpected repair costs by an average of 35%, making them a sound investment for long-term efficiency.
Featured Image: A flowchart comparing standard and extended warranty coverage.
4.3 Evaluating Manufacturer vs. Third-Party Warranties
When considering an extended warranty, it’s essential to compare manufacturer-provided options with those from third-party providers. While manufacturers offer in-depth knowledge of the equipment, third-party warranties may provide broader coverage.
Warranty Provider | Key Advantage | Potential Limitation |
---|---|---|
Manufacturer Warranty | Specialized expertise on machine components | May have higher upfront costs |
Third-Party Warranty | Broad coverage across multiple brands | Limited familiarity with specific models |
Choosing the right warranty depends on your operational needs and budget constraints. For mission-critical equipment like coil wrapping machines, manufacturer-backed warranties often provide greater reliability.
4.4 Dive Deeper into Tailored Warranty Packages
Many manufacturers now offer customized warranty packages tailored to specific usage patterns. For instance, heavy-duty users might benefit from packages with shorter intervals for preventive maintenance and faster access to spare parts. Tailored packages allow businesses to align warranty terms with operational realities, maximizing value.
Warranty Feature | Heavy-Duty Use Benefits | Light-Use Benefits |
---|---|---|
Preventive Maintenance | More frequent servicing | Standard intervals |
Spare Part Availability | Immediate replacements | Lower stock levels |
Technical Support Response Time | Priority access | Standard access |
By opting for tailored warranties, businesses can reduce downtime by up to 40%, ensuring smooth operations even under demanding conditions.
4.5 Two Fact Statements with Explanations
- True: Extended warranties often include discounted spare parts and faster technical support.
Explanation: These benefits are designed to minimize long-term maintenance costs and ensure quick resolution of issues. - False: Extended warranties cover all forms of damage or malfunction.
Explanation: Warranties typically exclude damages caused by improper use or external factors, such as accidents or natural disasters.
Conclusion
Investing in a coil wrapping machine is not just about acquiring cutting-edge technology; it’s about ensuring sustained operational efficiency through robust after-service. From comprehensive training and maintenance programs to advanced remote monitoring and tailored warranty packages, after-service offerings form the backbone of long-term productivity.
Manufacturers that prioritize after-service demonstrate their commitment to customer satisfaction and operational excellence. By understanding the scope and quality of these services, businesses can make informed decisions, ensuring that their investment delivers maximum value over time.
Claim: After-service is not an optional add-on—it is an essential component of any successful industrial equipment purchase. By choosing a supplier that excels in after-service, you secure the performance, reliability, and longevity of your coil wrapping machine.