I see confusion around coil shipments. People fear damage or wasted resources. This leads to stress. A structured coil packaging strategy helps solve these problems efficiently.
Coil packaging is the process of protecting coiled materials with secure wraps, covers, or pallets. This ensures safe handling and transport. It reduces damage risks. It also helps keep each coil in good shape. This method often uses specialized materials designed to cushion, protect, and stabilize coils.
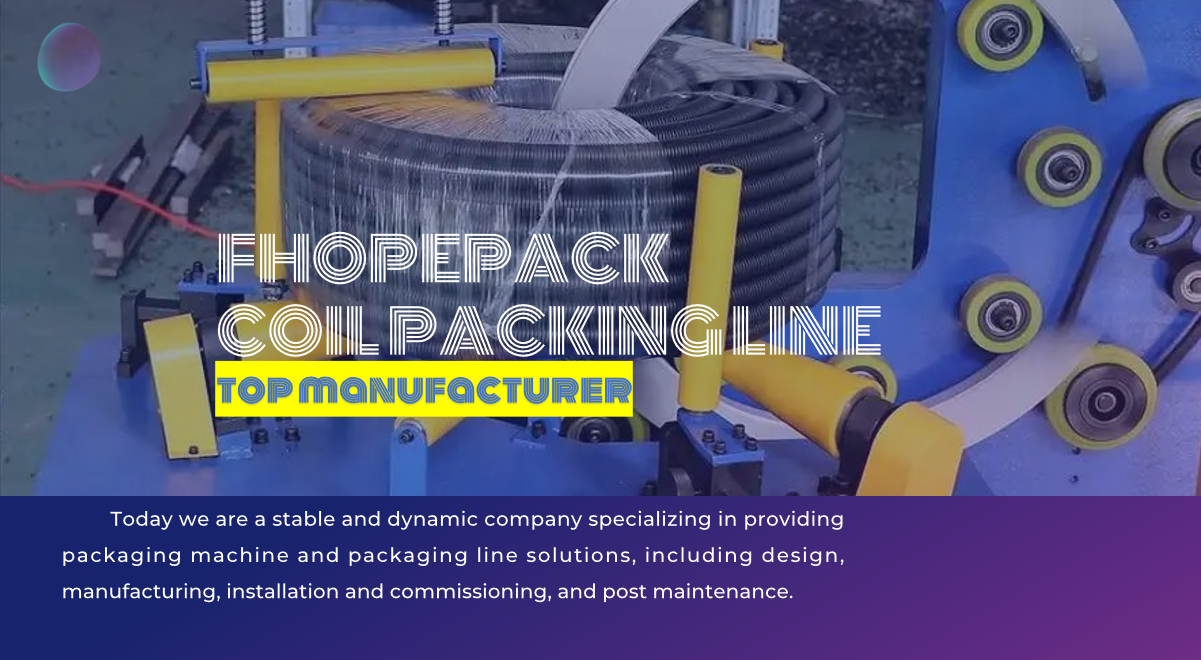
I want to share why coil packaging matters. Keep reading to find out how it prevents unwanted expenses and helps your operations run smoothly.
Why Is Coil Packaging Important?
I see factories struggle with coils. They worry about dents or corrosion. This sparks costly rework. A well-planned coil packaging solution addresses these challenges and ensures safe transport.
Coil packaging is important because it protects coils from moisture, impact, and handling errors. It reduces the chance of product damage. It also keeps quality consistent from the manufacturing site to the end user. By stabilizing each coil, it prevents costly downtime. It saves money through reduced reject rates.
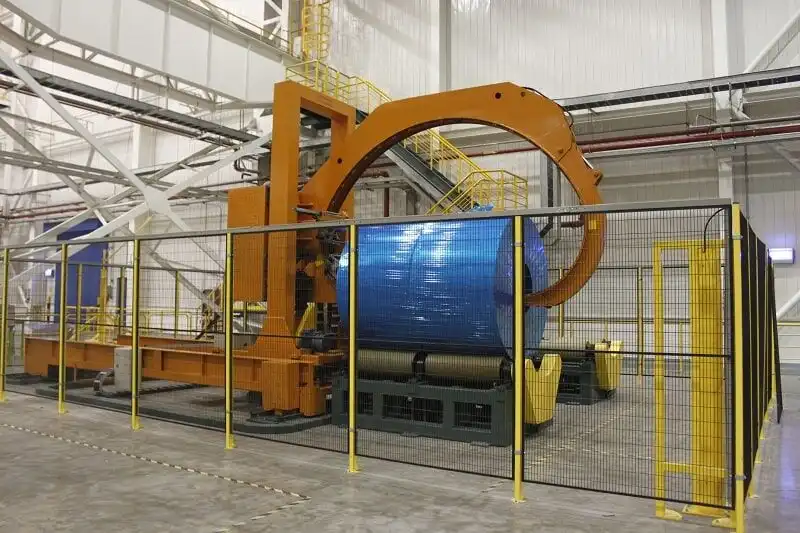
The Essential Role of Coil Packaging in Ensuring Quality and Safety
I want to explore the reasons coil packaging holds such value for manufacturers. First, the physical condition of a coil is crucial. Coils endure shifting, stacking, and shipping. Any weak spot can lead to scratches or dents. That lowers final product quality. Proper packaging stabilizes the coil and prevents unwanted friction. This method is especially important for steel coils, which are heavy and vulnerable to rust if moisture seeps through.
I notice that coil packaging also protects edges. Sharp coil edges can be damaged if workers move them without padding. A broken edge can render the coil useless for precise applications. By wrapping a coil in a tough protective layer, I see fewer scrapped sections and a more uniform appearance. This uniformity carries over to downstream processes like cutting or stamping, where consistent edges make production smoother.
Coil packaging also aids in standardizing shipping protocols. Each coil follows the same labeling, wrapping, and strapping approach. This uniform process saves time. Workers know exactly how to position a coil and which materials to use. This reduces human error and speeds up loading and unloading. It also builds trust with transport companies, since they see consistent, well-sealed packages. I have found that standardized coil packaging helps keep the supply chain predictable and efficient.
Another aspect is how coil packaging can reduce the chance of injuries. When coils are not secured, they might roll or shift suddenly. A stable coil is less likely to topple or shift. That leads to safer workplaces. It also lowers insurance risks. Companies that adopt thorough packaging strategies often discover that their employees face fewer accidents. This fosters a positive work environment.
Lastly, I like to mention the marketing angle. Well-packaged coils show professionalism. Buyers see that the supplier takes care of materials. That fosters confidence in product quality. Often, the final customers prefer suppliers who follow high packaging standards. It reflects a careful approach to everything from design to delivery. In competitive markets, that can be a key advantage. If your competitor ships coils with minimal wrapping and scuffed edges, customers might see that as negligence. Meanwhile, your company gains a good reputation for consistent quality.
Here is a simple table that shows how coil packaging brings benefits:
Benefit | Explanation | Result |
---|---|---|
Physical Protection | Prevents dents and scratches | Higher product quality |
Shipping Efficiency | Consistent wrapping speeds loading | Lower labor costs |
Safety Improvement | Stabilized coils reduce tipping hazards | Fewer worker accidents |
Brand Image | Professional packaging impresses clients | Strong reputation |
How to Choose the Right Materials for Coil Packaging?
I see people confused about material selection. They worry about cost or performance. This causes wasted spending. A step-by-step method helps pick the right coil packaging materials.
You should choose materials that handle weight, resist moisture, and protect edges. Popular materials include plastic film, VCI paper, steel strips, or wooden pallets. Match your coil’s weight and shape to the packaging material’s strength. Also, confirm compatibility with shipping guidelines and facility conditions.
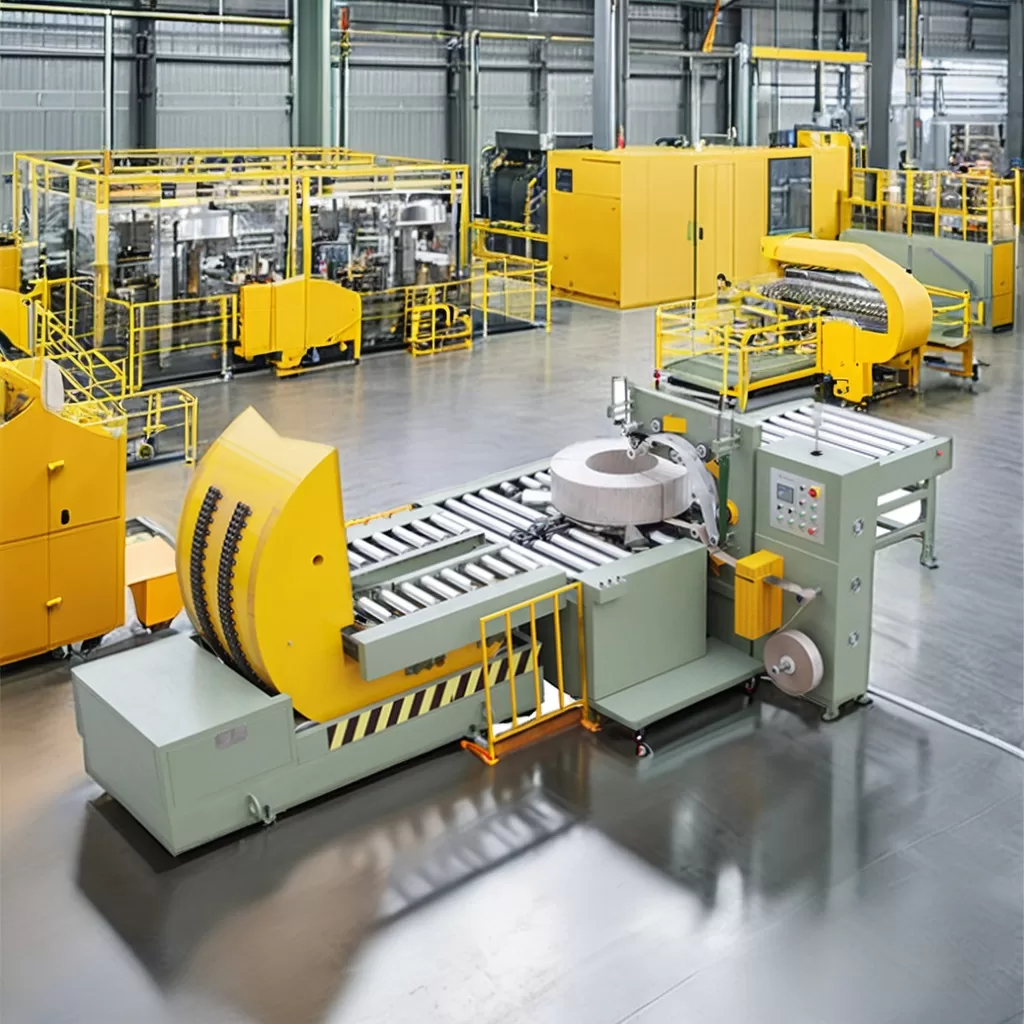
Choose the Best Materials for Your Coil Packaging Needs
I want to break down the criteria for picking packaging materials. First, I look at the coil’s weight. If a coil is very heavy, I need a robust material. Steel strapping is common for heavy coils. It offers tight tension and a secure hold. For lighter coils, I might prefer polyester straps, which are easier to handle. They still provide decent tension without the risk of corrosion that metal straps can bring.
Moisture resistance is the second major factor. Coils can corrode if exposed to humidity. I often recommend using VCI (Vapor Corrosion Inhibitor) paper or film. VCI materials emit a vapor that creates a protective layer on metal surfaces. This is especially helpful when shipping coils across long distances. I also look at shrink wrapping. If the environment is extra humid, I might add desiccant packs to absorb moisture inside the packaging.
Then I think about edge protectors. Coils have sharp edges that can slice through film if not protected. Thick paperboard protectors or plastic edge guards can distribute pressure. This avoids those cuts that ruin the wrap. I usually see them placed under the strapping, so the strap does not dig into the coil’s outer layer.
I also consider facility conditions. If my plant is dusty, I might use covers that keep debris away. If I store coils outside, I need UV-resistant wraps that do not degrade in sunlight. Another factor is how easy the material is to recycle or dispose of. Some facilities prefer eco-friendly options to meet sustainability goals. They might select biodegradable films or reduce plastic usage by switching to reusable wraps.
I want to talk about cost, too. A high-end packaging material can look expensive at first. But if it prevents rust and lowers rework, it might save money over time. I also see that using cheap materials leads to coil damage, which is far more costly to fix. The trick is to find the right balance. If the coil is made of stainless steel and headed for a controlled environment, maybe standard film works fine. If it is carbon steel for a long ocean trip, advanced moisture barriers are wise.
Below is a quick table that compares some popular materials:
Material | Best Use Cases | Pros | Cons |
---|---|---|---|
Steel Strapping | Heavy coils | Strong, secure | Can corrode without treatment |
Polyester Strap | Medium-to-light coils | Lightweight, easy to handle | Not as robust for extreme loads |
VCI Paper/Film | Metal coils prone to rust | Protects against corrosion | Requires sealed environment |
Edge Protectors | All coil sizes | Prevents wrap cuts | Extra cost and setup |
When I make a final choice, I also think about handling. Operators must easily apply the wraps or straps without much hassle. If it takes too long or requires special tools, that slows production. I also check if the wrapping machine is compatible with these materials. Automated lines often have specific settings for tension, sealing, or cut length. A mismatch could lead to jams or incomplete wraps.
I see that picking coil packaging materials is not a one-size-fits-all task. Each coil might need a different approach. The environment, shipping route, coil weight, and cost constraints all matter. Taking time to match these factors prevents coil damage, saves money, and leads to a safer, cleaner process.
What Are the Key Steps in Coil Packaging?
I hear people rush through packaging. They assume any wrap will do. That leads to confusion and coil mishaps. A clear set of steps helps avoid these problems.
Key coil packaging steps include inspection, surface protection, secure wrapping, strapping or banding, edge guard application, and final labeling. Each step ensures the coil stays stable during transport. Skipping any step increases the chance of damage or mislabeling.
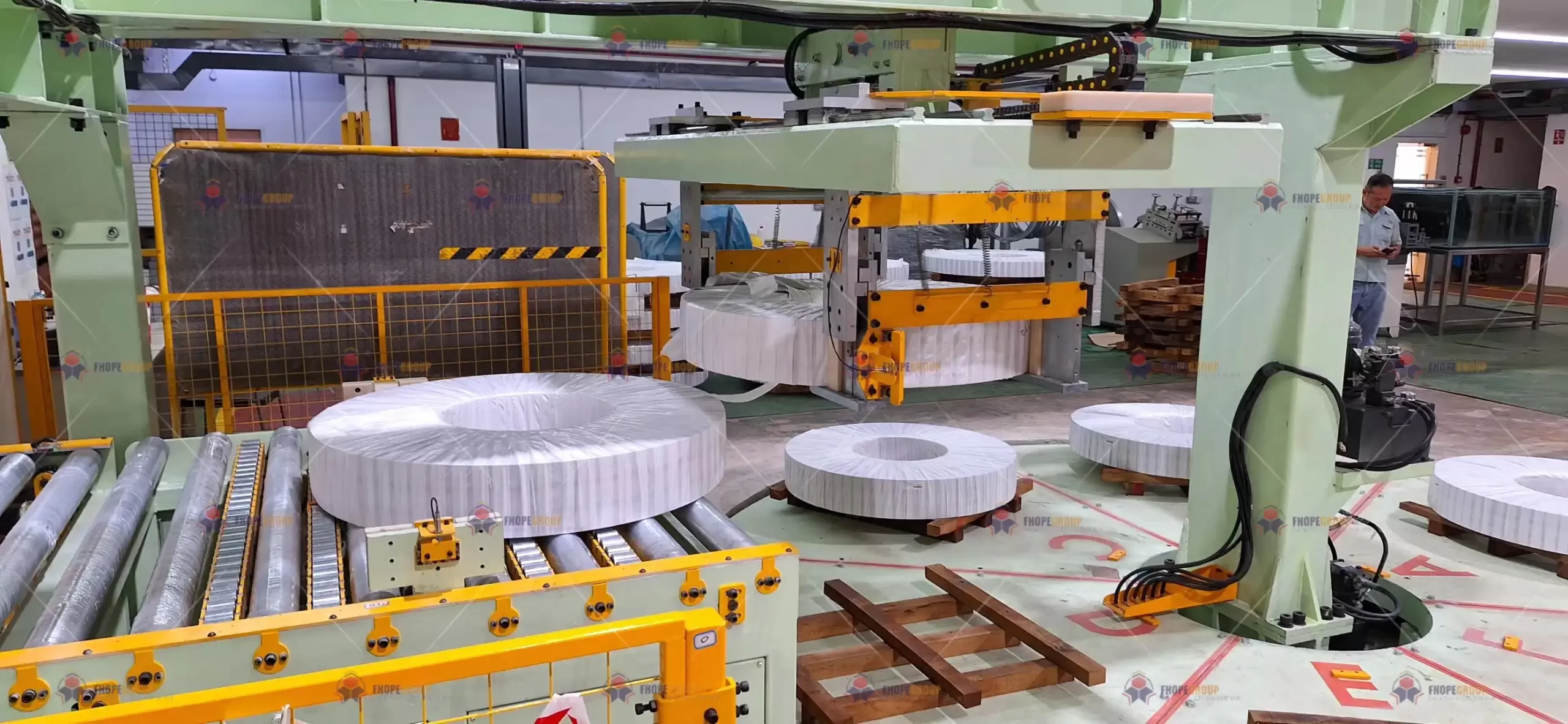
Step-by-Step Guide to Effective Coil Packaging Procedures
I want to detail the main tasks involved in coil packaging. The first step is thorough inspection. I see many places skip this. They just start wrapping. But an inspection can catch rust spots or surface debris before the coil is covered. If the coil is already damaged, wrapping hides the problem. It might worsen in transit. By detecting issues early, you can fix them or reclassify the coil.
Then you apply surface protection. This might be a thin film of rust-inhibiting oil for metal coils. Or it could be a protective film if the coil has a delicate finish. Some companies add corner or edge protectors at this stage. The goal is to preserve coil integrity. I like to use materials that do not leave residues. That way, the next process downstream does not require extra cleaning.
After that, you move to wrapping. You pick the right material. You might use stretch film, shrink wrap, or paper. The choice depends on the coil’s weight, shape, and environment. The operator or machine carefully applies it around the coil. Overlapping layers maintain coverage without gaps. I also recommend sealing edges or corners with tape. This step keeps moisture, dust, or dirt from penetrating.
The fourth step is strapping or banding. Straps hold the wrap in place and add structural support. You can use steel or polyester straps. The tension must be enough to keep the coil tight, but not so tight that it cuts into the coil. If your coil is large, you may need multiple straps placed at intervals. This step is vital for preventing movement, especially if the coil is transported over bumpy roads or long ocean voyages.
Edge guards come next. If your coil has sharp edges, place guards to absorb any stress from the straps. Some companies place guards before strapping. Others slip them under each strap. The main idea is to distribute pressure so the coil does not slice the wrap or snap the strap.
Labeling is the final major step. A simple label might include coil dimensions, weight, material grade, and a tracking number. This label helps forklift operators handle the coil correctly. It also helps the receiver confirm they got the right order. If there are special instructions, such as “keep dry” or “fragile edges,” that should appear on the label. Clear labeling lowers confusion and makes the receiving process faster.
Here is a table that outlines the steps:
Step | Action | Reason |
---|---|---|
Inspection | Check coil for damage or debris | Prevents packing hidden defects |
Surface Prep | Apply anti-rust or protective film | Preserves coil finish |
Wrapping | Wrap the coil with chosen material | Shields from moisture and dust |
Strapping | Secure with steel or plastic bands | Adds stability during shipping |
Edge Guards | Protect edges with reinforcements | Stops tearing or strap breakage |
Labeling | Mark coil details and instructions | Helps identification and tracking |
I learned that each step matters. If you skip one, you can invite issues. For example, if you do not label the coil, it might get stored incorrectly. If you do not add edge guards, the wrap can tear. If you do not inspect the coil, you might package a rusted section. Then the rust will spread under the wrapping, which creates more damage.
When I started with coil packaging, I tried to cut corners. I thought a quick wrap was enough. Then I found damaged coils after shipping. That cost money and time. Now I follow these steps diligently. I have seen fewer problems and happier clients. Adopting a consistent method also makes training new operators simpler. Everyone follows the same checklist, which ensures uniform quality.
Conclusion
I believe coil packaging is a strategic process. It keeps each coil safe, saves costs, and supports smooth logistics, leading to better outcomes for everyone involved.