Understanding the Horizontal Orbital Stretch Wrapper: A Comprehensive Guide
A horizontal orbital stretch wrapper is a specialized industrial packaging machine engineered for securing elongated or bulky products. Commonly used in industries handling items like pipes, lumber, aluminum extrusions, textiles, and doors, this equipment wraps products horizontally using stretch film. The process involves a rotating ring carrying the film dispenser that orbits around the stationary or slowly moving product, effectively cocooning it in multiple layers of stretch film. This method provides crucial load stabilization, protects against dust, moisture, and handling damage, and improves overall package integrity during storage and transportation.
Key Components of a Horizontal Orbital Stretch Wrapper
Understanding the main parts of an orbital wrapper helps clarify its operation and capabilities.
1. Wrapping Station
The heart of the machine, the wrapping station executes the core wrapping function. It typically comprises:
- Rotating Ring: This component orbits the product, carrying the film delivery system. Its speed and smoothness are critical for efficient wrapping.
- Film Carriage System: Mounted on the ring, this holds the stretch film roll and includes mechanisms for pre-stretching the film (improving yield and load containment) and applying it with consistent tension.
- Film Cut and Clamp System: Automatically cuts the film upon cycle completion and clamps it, ready for the next cycle, enabling seamless operation.
horizontal hose coil packing line3 2. Product Stabilization Device (Press Down)
Maintaining product stability during the wrapping cycle is essential, especially for bundles or irregularly shaped items. A press down device holds the product firmly on the conveyor, preventing shifting or vibration that could compromise wrap quality. Common types include:
a. Pneumatic (Air Cylinder)
Utilizes compressed air to apply gentle but firm pressure. Ideal for light to medium-weight products, offering quick action and easy pressure adjustment.
b. Motorized (Servo/Electric)
Provides highly precise, programmable control over the applied force. Best suited for delicate products, items requiring specific pressure points, or applications demanding high accuracy and repeatability.
c. Gravity/Weighted
A simpler, often cost-effective mechanism using weights or the component's own weight to provide hold-down force. Suitable for basic applications where precise pressure control is less critical.
3. Infeed and Outfeed Conveyor Systems
These systems manage the flow of products into and out of the wrapping station, crucial for automation and throughput. The type depends on the product characteristics (weight, shape, surface sensitivity):
a. Motor-Driven Roller Conveyor
Uses powered rollers for smooth, controlled movement. Versatile for various product sizes and weights, common in many automated lines.
b. Chain Conveyor
Features robust chains, ideal for very heavy loads like bundles of steel pipes, timber packs, or other substantial items requiring durable support.
c. Belt Conveyor (Rubber/PVC)
Employs a continuous belt surface. Preferred for products needing surface protection (e.g., painted profiles, furniture, doors, windows) as it minimizes scratching or marking during transit.
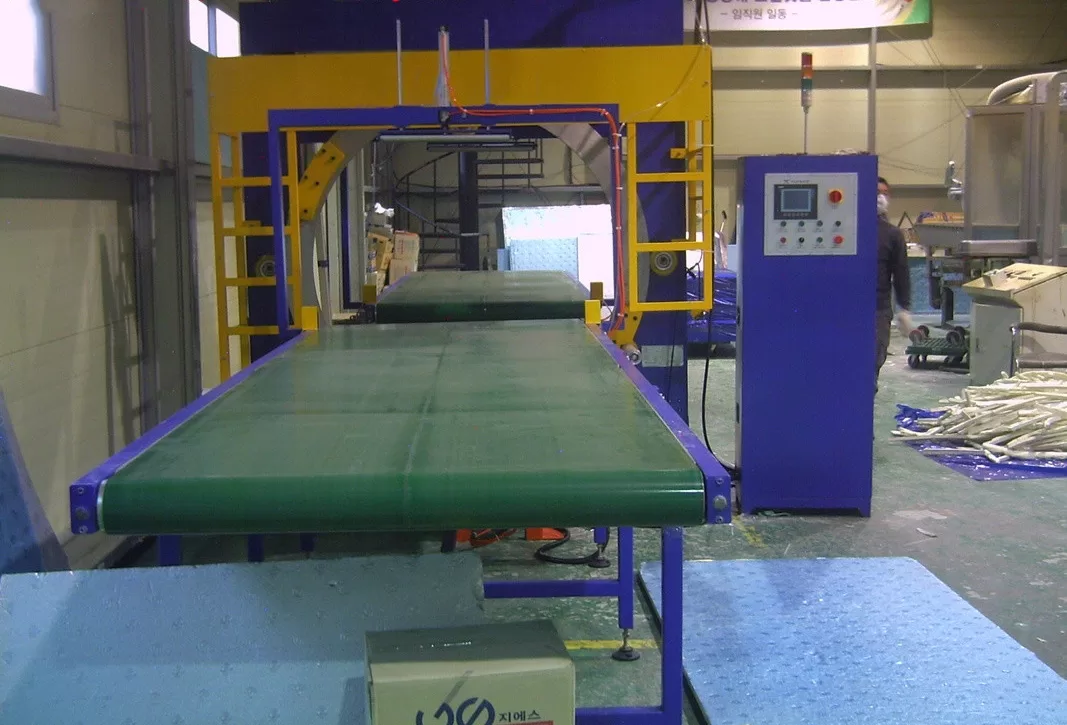
4. Safety Systems
Operator safety is paramount. Horizontal wrappers incorporate multiple safety features:
- Safety Fencing/Guarding: Physical barriers preventing access to moving parts during operation.
- Interlock Switches: Sensors on doors or guards that stop the machine if opened.
- Light Curtains: Optical safety barriers that detect intrusion into hazardous areas.
- Emergency Stops: Easily accessible buttons to halt machine operation immediately.
5. Control System
The brain of the wrapper, coordinating all functions:
- PLC (Programmable Logic Controller): Manages sequences, timings, and machine logic.
- HMI (Human-Machine Interface): Touchscreen or panel for operator control, parameter adjustments (wrap counts, tension, speed), recipe storage, and diagnostics.
- Variable Frequency Drives (VFDs): Control motor speeds (conveyors, ring rotation) for flexibility and energy efficiency.
- Sensors: Detect product presence, position, and film status.
6. Customization Options
Orbital wrappers can be tailored to specific operational needs with features like:
- Top Sheet Applicator: Places a protective film layer on top of the load before wrapping.
- Integrated Strapping: Adds strapping for extra load security, often required for heavy or unstable bundles.
- Timber Feeder: Automatically places wooden spacers between products for stacking or handling.
- Head/Tail Wrapping: Provides extra wraps at the leading and trailing ends of the product for enhanced protection.
- Weighing Systems: Integrated scales for capturing load weight data.
Main Operational Versions of Horizontal Stretch Wrappers
Horizontal wrappers are available in different levels of automation to match production demands and budgets.
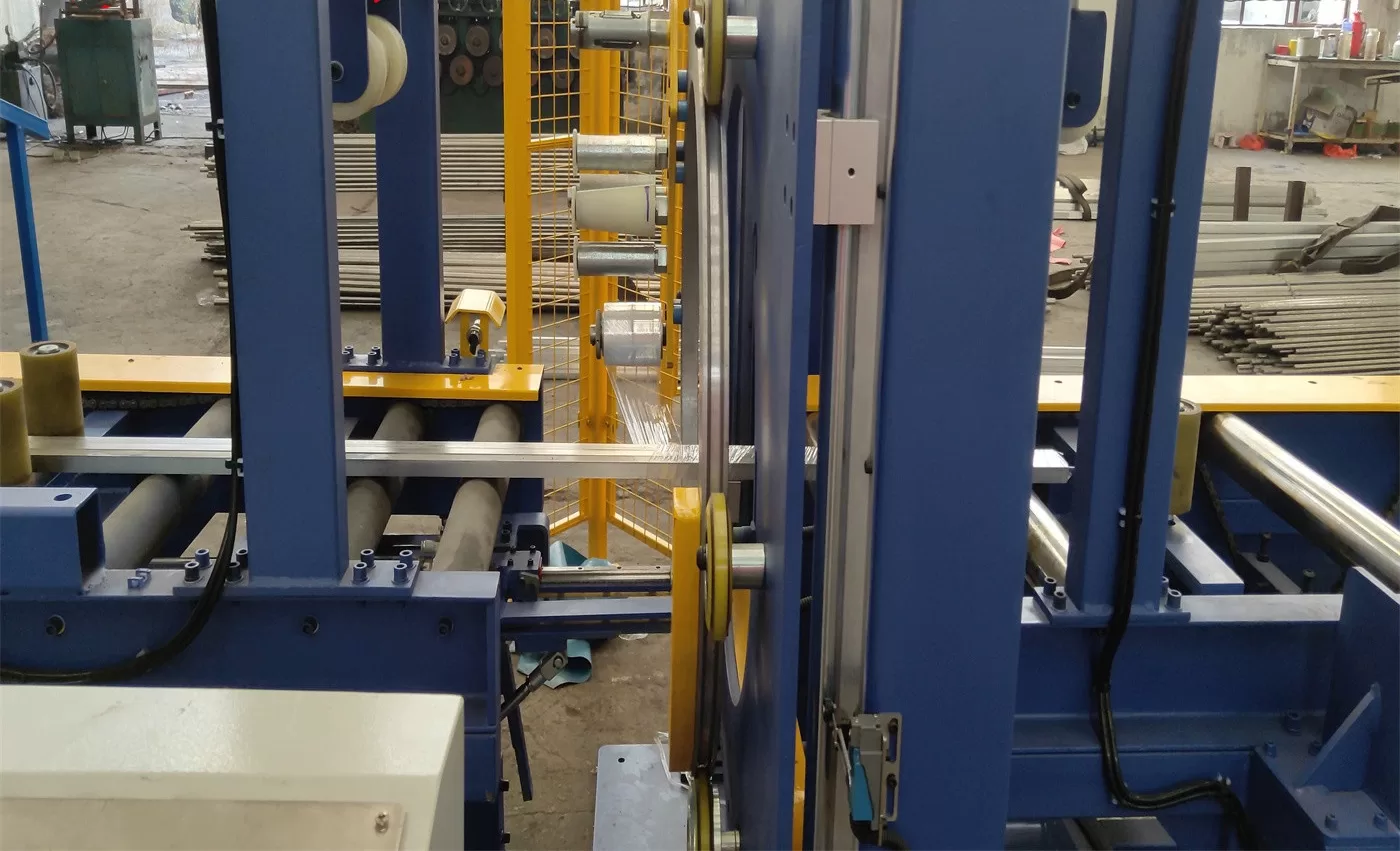
1. Semiautomatic Horizontal Wrapper
Requires operator intervention to start the wrap cycle, position the product (sometimes), and attach/cut the film manually or via button activation. Conveyors might be powered or unpowered (gravity/manual push). These are suitable for lower volume operations or where product types vary significantly, offering flexibility at a lower initial investment.
2. Automatic Horizontal Wrapper
Designed for integration into automated production lines. These systems handle product infeed, wrapping, film cutting/clamping, and outfeed automatically without operator intervention. Sensors manage the entire process. Ideal for high-volume, consistent production environments demanding speed and minimal labor.
3. Customized Horizontal Wrapping Lines
Beyond standard models, fully customized solutions address unique challenges. This can involve specialized conveyors, integration with upstream/downstream equipment (like saws, stackers, or robotics), unique stabilization methods, or combined processes like wrapping and labeling within a single system.
Common Applications for Horizontal Stretch Wrappers
These machines excel in securing products that are challenging to wrap on traditional turntable or rotary arm machines.
1. Wrapping Wood Products (Panels, Lumber, Flooring)
Long wooden panels, bundles of lumber, or packs of flooring (e.g., 2-6 meters long, varying widths/heights, up to 500-1500 kg) benefit greatly. The wrap protects finished surfaces from scratches, contains bundles securely, and shields against moisture. Automatic top sheet dispensers are often used for added protection.
2. Packaging Metal Products (Pipes, Rods, Extrusions)
Bundles of steel rods, copper pipes, or aluminum profiles (often 6-12 meters long, potentially weighing 1000-3000 kg or more) are common applications. Heavy-duty chain conveyors are typically used. The stretch wrap prevents shifting, protects against corrosion/surface damage, and simplifies handling of potentially awkward bundles.
3. Securing Plastic Items (Pipes, Profiles, Sheets)
Plastic pipes, window profiles, or bundles of plastic sheets (e.g., 3-6 meters long, lighter weight but bulky, up to 1000 kg) are efficiently wrapped. The film provides containment, keeps items clean, and protects against UV exposure (if using UV-inhibiting film). Belt conveyors are often preferred to prevent marking sensitive surfaces.
4. Other Industries
Horizontal orbital wrappers are also found in textiles (carpet rolls, fabric rolls), building materials (insulation panels, doors), furniture manufacturing, and other sectors dealing with long, bundled, or oversized items requiring secure, protective packaging.
By understanding the components, versions, and applications of horizontal orbital stretch wrappers, businesses can make informed decisions about incorporating this efficient and protective packaging technology into their operations.