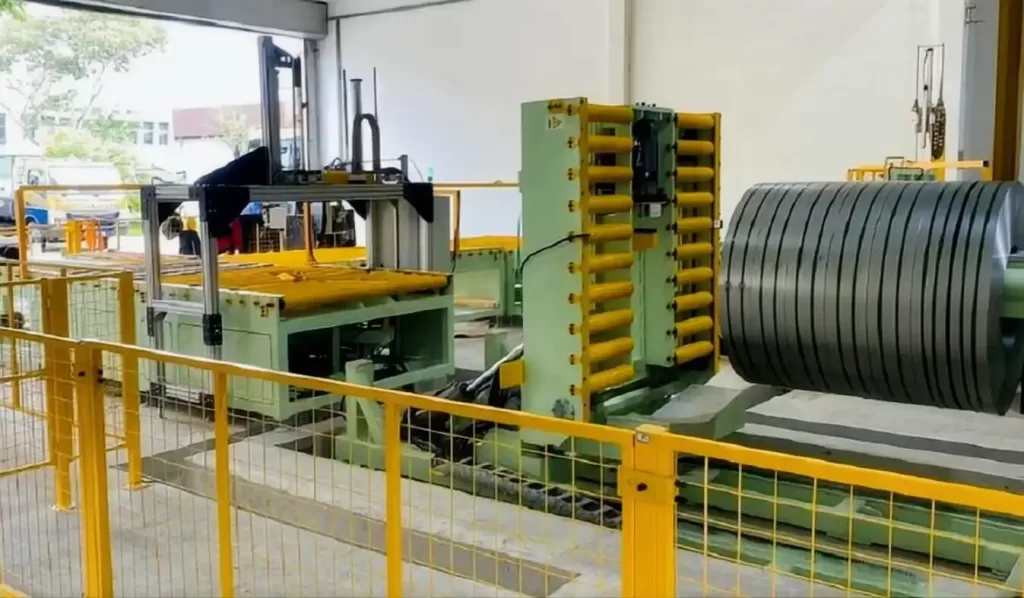
Steel wire packaging has come a long way, evolving from simple manual bundling to intricate, automated solutions designed for precision and efficiency. The latest technologies don’t just focus on packaging itself but integrate safety, speed, and sustainability to create a truly holistic process. In this exploration, we’ll dive into the cutting-edge technologies and solutions transforming steel wire packaging, offering insights into how each innovation is shaping the industry’s future.
For anyone working with steel wire packaging lines, it’s clear that productivity, cost efficiency, and product integrity are paramount. Yet, keeping up with new advancements in machinery and integrated solutions can seem daunting. This guide aims to simplify those complexities, breaking down the most significant advancements and examining how these technologies could impact your operations.
This guide will uncover what’s new in the world of steel wire packaging lines, examining how these advancements fit into the larger picture of manufacturing. As we proceed, we’ll answer questions like: What are the emerging technologies in this sector? How do they offer both efficiency and operational savings? And what should you consider when upgrading to an advanced system?
- 1. What is Automated Packaging, and How is it Revolutionizing Steel Wire Handling?
- 2. How Are Safety Features Enhancing Modern Packaging Lines?
- 3. What Role Does Data Analytics Play in Integrated Solutions?
- 4. How Are Sustainability Initiatives Shaping the Future of Steel Wire Packaging?
- Conclusion: Embracing Innovation in Steel Wire Packaging for a Competitive Edge
1. What is Automated Packaging, and How is it Revolutionizing Steel Wire Handling?
1.1 Understanding Automated Packaging Solutions
Automated packaging in steel wire manufacturing has shifted from a luxury to a necessity, especially as global demand pressures factories to enhance speed without sacrificing quality. At its core, automated packaging leverages robotic systems and sensors to complete tasks with minimal human intervention. These automated solutions tackle everything from coil wrapping and strapping to tagging and palletizing.
Automation reduces errors, particularly in repetitive tasks that are prone to human mistakes. With precise movements and set parameters, automated systems can handle more wires in less time while achieving consistent wrapping quality. However, one drawback is the upfront investment required. Integrating automation demands substantial capital, and implementation may disrupt existing workflows temporarily.
1.2 The Rise of Robotics in Packaging
The use of robotics in packaging lines has enabled faster, more accurate operations. Robotic arms now excel in applying even pressure, essential for delicate wire products susceptible to bending or surface imperfections. These robotic systems can handle various coil sizes with ease, ensuring that each package meets strict specifications, thus maintaining product integrity from start to finish.
Nevertheless, this technology comes with a learning curve. Operators often need retraining, and not all packaging lines may support immediate robotic integration. Despite this, the productivity and error-reduction benefits often justify the effort and resources invested.
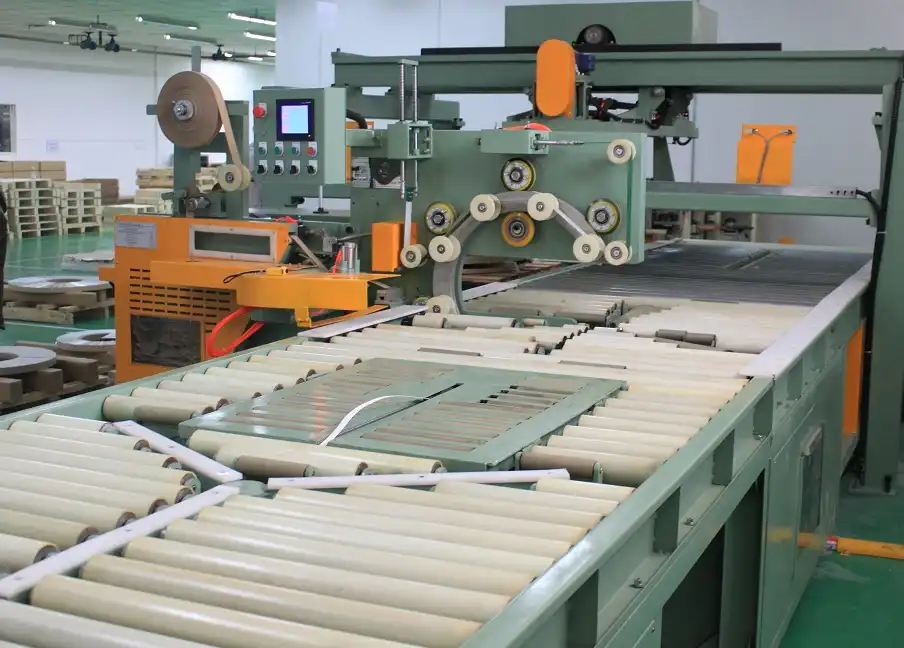
1.3 How Intelligent Sensors Enhance Process Efficiency
Intelligent sensors are becoming a crucial element in automated steel wire packaging lines. These sensors track data points like weight, alignment, and wrapping consistency in real-time, enabling on-the-fly adjustments to optimize packaging quality. They reduce the risk of errors that may arise from manual inspections and can catch issues like misalignment or abnormal tension immediately.
A key benefit here is that sensors reduce waste by ensuring only the correct amount of packaging material is used, lowering both costs and environmental impact. However, like any digital technology, these sensors are vulnerable to software issues and occasional malfunctions, requiring skilled technicians for repairs and adjustments.
2. How Are Safety Features Enhancing Modern Packaging Lines?
2.1 The Importance of Safety Protocols in Packaging
Safety has become a critical focus in modern steel wire packaging lines, as manufacturers aim to protect both their products and employees. Today’s packaging systems include sophisticated safety mechanisms such as emergency stops, protective barriers, and automated shutdowns when a potential hazard is detected. These features help prevent accidents, ensuring workers remain safe even in fast-paced or high-temperature environments.
One major advantage of these safety protocols is the peace of mind they bring to both operators and management. With automated safety checks, the chances of injury from machinery malfunction or mishandling decrease significantly. However, companies need to maintain these safety features regularly, as neglect can lead to costly repairs or downtime.
2.2 Enhancing Worker Safety with Automation
Automation has dramatically reduced the amount of physical labor required on steel wire packaging lines. By automating heavy lifting, coil wrapping, and palletizing, packaging lines reduce the risk of worker injuries from tasks like lifting or moving heavy steel coils. Robotic arms and conveyor systems handle these intense physical tasks, allowing operators to supervise safely from a distance.
Although automation decreases physical strain, workers still need training to safely interact with these systems. For example, knowing when and how to perform emergency shutdowns or adjust robotic settings is essential. Therefore, companies often need to invest in regular training to maximize the effectiveness of these safety features.
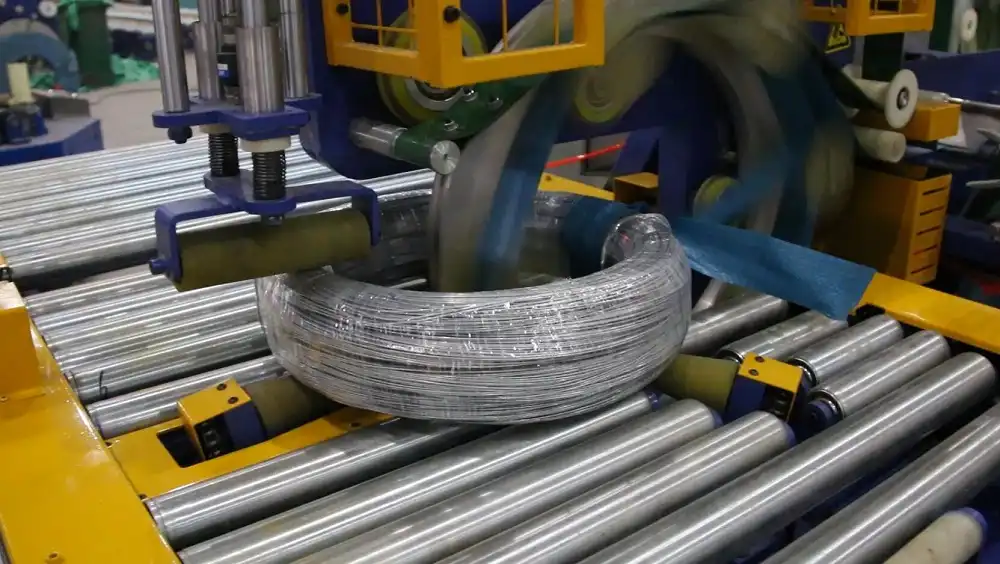
2.3 The Role of AI in Proactive Safety Monitoring
Artificial intelligence (AI) is emerging as a powerful tool for proactive safety monitoring in packaging lines. AI-driven systems can detect abnormal behaviors, such as unusual coil movements or machinery vibrations, signaling potential hazards before they escalate. By analyzing historical data and recognizing patterns, AI systems can predict when a machine might require maintenance, thereby preventing malfunctions that could jeopardize safety.
One of the significant advantages of AI in safety is its ability to learn and adapt. Over time, these systems refine their accuracy, minimizing false alarms while improving response to real threats. However, the integration of AI in safety protocols requires high-quality data inputs and routine updates, which can add complexity to system management.
3. What Role Does Data Analytics Play in Integrated Solutions?
3.1 How Data Analytics Drives Operational Efficiency
Data analytics has transformed the steel wire packaging industry by providing valuable insights into operational efficiency. Through the collection and analysis of real-time data from various stages in the packaging line, managers can monitor key performance indicators (KPIs) like output rate, material usage, and downtime. By interpreting these metrics, companies can identify bottlenecks, optimize resource allocation, and ultimately improve overall productivity.
The ability to analyze data and adjust operations accordingly means packaging lines can adapt faster to changes in demand or shifts in production requirements. This adaptability not only improves response times but also minimizes waste. However, to benefit fully, companies need robust data infrastructure and skilled analysts to interpret and act on the data insights accurately.
3.2 Predictive Maintenance and Downtime Reduction
One of the standout applications of data analytics is predictive maintenance. Through advanced data analysis, companies can track machinery wear-and-tear patterns and anticipate maintenance needs before an issue causes downtime. This proactive approach prevents costly disruptions and extends the lifespan of equipment by addressing issues early on.
Incorporating predictive maintenance into packaging lines has allowed companies to achieve remarkable uptime levels, making operations more dependable. However, effective predictive maintenance relies heavily on consistent data collection and real-time monitoring systems. A failure in these systems can result in overlooked issues, making regular checks essential to ensure accuracy.
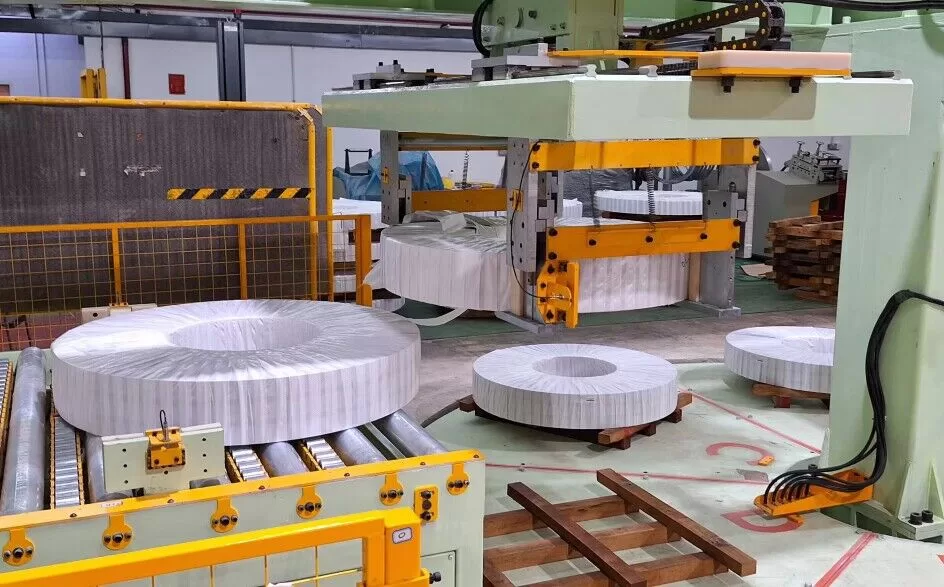
3.3 Real-Time Adjustments and Process Optimization
Data analytics enables real-time adjustments, allowing systems to adapt instantly to process requirements. For instance, if a packaging line detects an incoming batch of wires requiring specific wrapping or labeling, it can adjust settings automatically to meet these needs. This adaptability reduces the time and errors involved in manual reconfiguration and increases overall throughput.
Real-time data analytics also contributes to enhanced quality control by enabling continuous monitoring of product specifications. This immediate feedback loop allows operators to detect and correct deviations promptly, ensuring each package meets required standards. However, real-time systems can be data-intensive, requiring high processing power and reliable network infrastructure to function effectively.
4. How Are Sustainability Initiatives Shaping the Future of Steel Wire Packaging?
4.1 The Shift Toward Eco-Friendly Materials
As industries across the board push toward greener practices, the steel wire packaging sector is no exception. Companies are increasingly exploring eco-friendly materials such as biodegradable plastics, recycled packaging components, and low-emission adhesives to reduce environmental impact. These sustainable materials not only help meet regulatory standards but also appeal to customers who prioritize eco-conscious suppliers.
Switching to sustainable materials offers both environmental and economic benefits by reducing waste disposal costs and potentially attracting new, environmentally-aware clients. However, these materials often come with a higher price tag, and their durability can vary, which means companies must evaluate both the short-term and long-term impacts before full adoption.
4.2 Energy-Efficient Machinery and Reduced Carbon Footprint
The latest packaging lines are now designed with energy efficiency in mind. Advanced machinery consumes less power, reducing the overall carbon footprint of packaging operations. Many new systems use energy-saving motors, optimized conveyor speeds, and low-voltage controls to conserve electricity without compromising performance. Some systems also come with energy monitoring tools, allowing managers to track usage and make adjustments in real time.
By investing in energy-efficient machines, companies reduce operational costs and lessen their environmental impact. However, energy-efficient technology often requires significant initial investment, making it essential for companies to evaluate cost-benefit ratios before implementation.
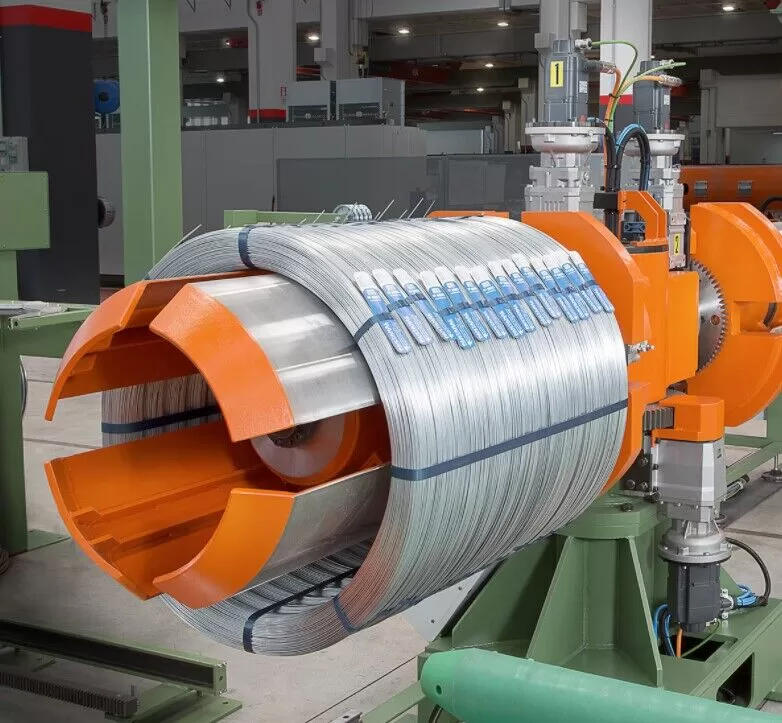
4.3 Waste Reduction Through Process Optimization
Sustainability in steel wire packaging isn’t limited to materials and energy use; it also encompasses waste reduction strategies. By optimizing each step in the packaging process, companies can significantly reduce material waste. Automation, precision cutting, and data-driven process adjustments ensure that only the necessary amount of material is used for each package, eliminating excess.
Minimizing waste benefits both the environment and the company’s bottom line. However, achieving optimal waste reduction requires regular audits and data monitoring to identify areas for improvement continuously. Companies dedicated to sustainability often conduct these evaluations to refine their packaging lines and maximize eco-friendly outcomes.
Conclusion: Embracing Innovation in Steel Wire Packaging for a Competitive Edge
As we’ve seen, the steel wire packaging industry is rapidly evolving, driven by advancements in automation, safety, data analytics, and sustainability. Each of these areas offers unique advantages, from enhanced efficiency and reduced downtime to improved safety and eco-friendly practices. By embracing these innovations, companies not only boost their operational performance but also position themselves as forward-thinking leaders in an increasingly competitive market.
Implementing these technologies, however, requires careful planning and investment. While automated and data-driven systems offer long-term savings, they also demand initial capital and technical expertise. Similarly, adopting sustainable practices may entail upfront costs but offers the potential for significant returns in customer loyalty and regulatory compliance.
In conclusion, companies willing to invest in modern steel wire packaging technologies will find themselves equipped to meet the demands of today’s market while paving the way for future growth.

Get Your Best Solution !