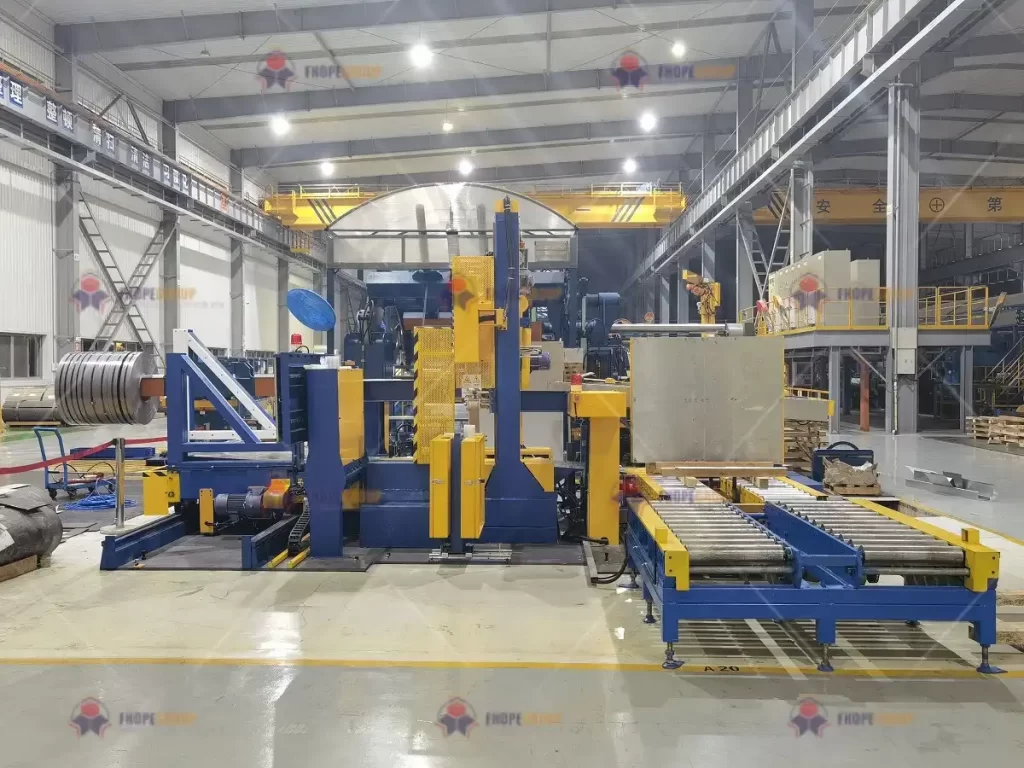
Steel coil packaging has come a long way in the last decade, becoming increasingly sophisticated and efficient. Now more than ever, manufacturers seek ways to streamline their packaging processes to stay competitive in a fast-evolving industry. Emerging technologies and integrated solutions for steel coil packaging lines are reshaping this landscape, helping companies to save costs, reduce errors, and increase safety. As we dive into this topic, I'll explore these advancements in detail, bringing you up to speed on the latest innovations and what they mean for the future of steel coil packaging.
Steel coil packaging lines now offer more than just automated wrapping—they encompass a range of technologies from automated quality control systems to data-driven predictive maintenance. For anyone in manufacturing, understanding these advancements is crucial. Let’s delve into the core questions surrounding this technology transformation.
The first step in understanding this evolution lies in grasping the comprehensive picture of how each element of an advanced packaging line integrates to form a streamlined, cost-effective system. In this article, I’ll dissect the primary technologies, showcasing what each advancement contributes to efficiency and longevity.
1. What are the key components of a modern steel coil packaging line?
1.1 Key Innovations in Material Handling Systems
Modern steel coil packaging lines have evolved to include highly specialized material handling systems that handle everything from the movement to the alignment of coils for seamless packaging. At the heart of these systems are hydraulic and servo-controlled machines, which allow for precise, reliable movement and orientation. Companies now use automated guided vehicles (AGVs) or robotic arms to transport coils, reducing manual handling needs. This shift not only increases productivity but also minimizes the risk of injury to personnel.
1.2 Enhanced Wrapping Technologies
One of the most notable advancements in steel coil packaging lines lies in the wrapping process itself. Wrapping technologies have become highly customizable, enabling manufacturers to adjust wrapping strength, film thickness, and wrap speed. These features are crucial, as they allow manufacturers to secure coils effectively without overusing materials, thereby reducing waste. Newer systems incorporate intelligent controls that adapt to coil size and weight, applying just the right amount of wrap for optimal protection during storage or transit.
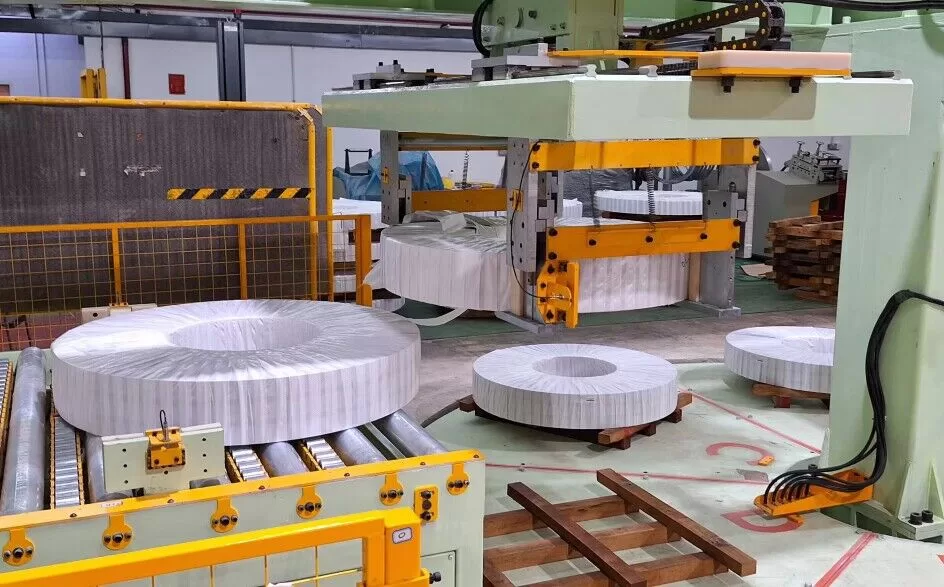
1.3 Integration of Automated Quality Control
Beyond material handling and wrapping, modern packaging lines integrate quality control systems to ensure every packaged coil meets specific standards. Advanced inspection tools, such as laser or camera-based systems, automatically scan each coil for any inconsistencies, like misalignments or irregular wrapping. This proactive approach enables quick identification of issues, allowing operators to correct errors in real time. Quality control systems are often connected to central data networks, feeding data back for analysis and continuous improvement.
2. How does automation enhance efficiency in packaging lines?
2.1 Advanced Robotics and Process Synchronization
Automation has transformed steel coil packaging, where robotics play a significant role in streamlining operations. Robots, capable of multi-axis movement and high-speed precision, assist in loading, unloading, and positioning steel coils seamlessly. Process synchronization aligns each stage—wrapping, strapping, labeling, and inspection—creating a flow that minimizes downtime and increases output. By reducing human intervention, companies not only improve efficiency but also lower the potential for errors and accidents, driving the entire packaging process toward higher consistency.
2.2 Intelligent Conveyor Systems
Today’s steel coil packaging lines often incorporate intelligent conveyor systems that automatically adjust speeds based on coil characteristics and workflow demands. These conveyors, integrated with sensors, detect weight and dimensions, adapting to the coil in real time to prevent accidents or misalignment. This feature keeps the packaging process flowing smoothly, reducing bottlenecks and ensuring that each stage operates at optimal speed. With the addition of IoT-enabled sensors, companies can monitor conveyor performance, predict maintenance needs, and prevent costly breakdowns before they occur.
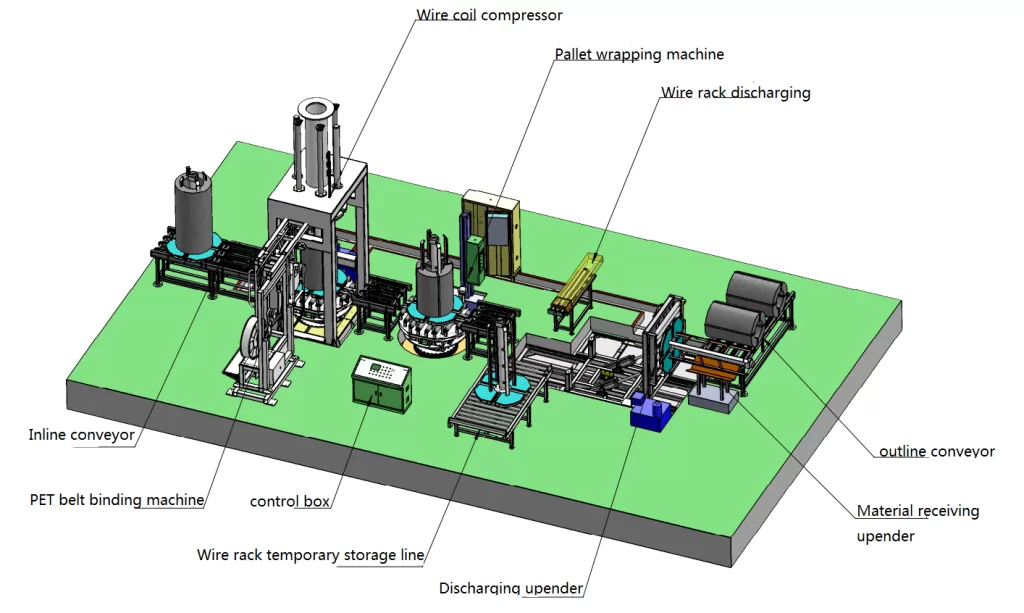
2.3 Predictive Maintenance through IoT
Integrating IoT within packaging lines has empowered manufacturers to implement predictive maintenance—a leap from traditional reactive strategies. Through sensors embedded in critical components like motors and conveyors, IoT systems collect data on operational conditions, detecting anomalies before they lead to failures. These systems notify maintenance teams to address issues preemptively, reducing costly downtime. With predictive maintenance, manufacturers not only extend equipment lifespan but also maintain a more consistent output, ultimately leading to substantial savings over time.
3. How can data analytics drive performance improvements?
3.1 Data Collection and Real-Time Monitoring
In modern steel coil packaging lines, data analytics begins with extensive data collection from various touchpoints, including material handling equipment, wrapping machinery, and quality control systems. Real-time monitoring enables operators to observe line performance continuously, identifying inefficiencies that may otherwise go unnoticed. Data collected on coil weight, size, wrap quality, and production speeds helps create a clear performance baseline, making it easier to detect and address deviations in productivity as they arise.
3.2 Machine Learning and Predictive Insights
Machine learning algorithms now play a vital role in optimizing steel coil packaging processes by analyzing historical and real-time data. These algorithms provide insights into areas for improvement, predicting potential disruptions and suggesting tweaks for enhanced efficiency. For instance, machine learning may identify patterns indicating when a coil might require additional reinforcement or detect inefficiencies in material use, prompting adjustments that conserve resources. By predicting issues and optimizing workflows, data-driven insights allow companies to remain agile in a competitive industry.
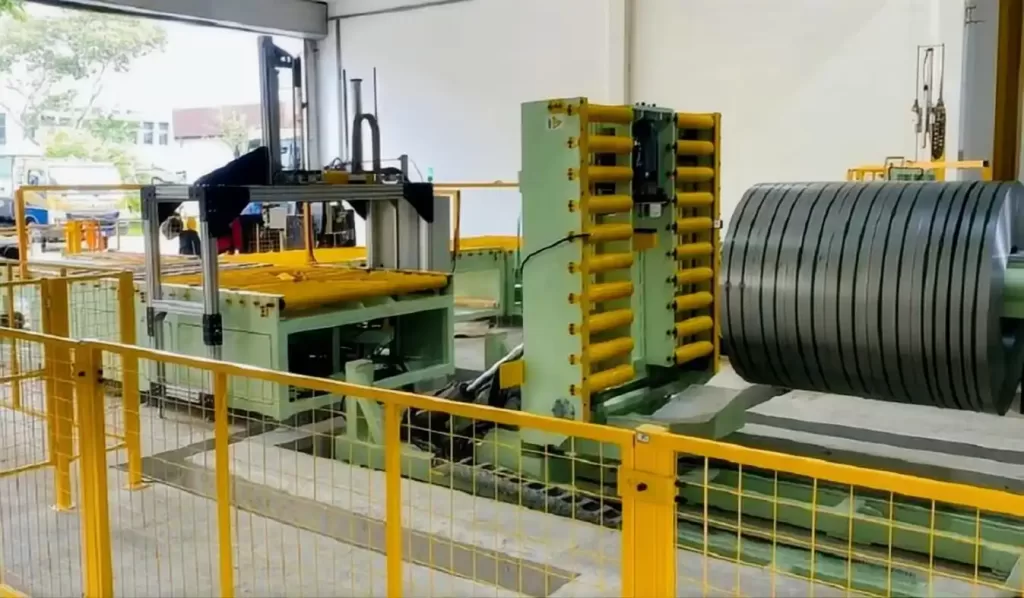
3.3 Enhancing Decision-Making with Data Visualization
Data visualization tools transform raw data into easily interpretable charts, graphs, and dashboards, enabling quick, informed decision-making. For management teams, real-time dashboards can highlight key performance indicators (KPIs), such as wrapping speed, material use, and downtime. With a clear visual representation of these metrics, decision-makers can implement changes more effectively, responding quickly to fluctuating production demands or emerging trends. Data visualization enhances the collaborative process, as team members across departments can discuss data-backed strategies for continuous improvement.
4. What are the sustainability benefits of integrated packaging solutions?
4.1 Eco-Friendly Materials and Resource Optimization
Integrated packaging solutions are now moving toward sustainable practices by incorporating eco-friendly materials and reducing material waste. Many manufacturers have switched to biodegradable or recyclable wrapping films, which align with growing environmental standards. These materials protect the steel coils while ensuring that, post-usage, they have minimal environmental impact. In addition, resource optimization tools in packaging lines calculate the precise amount of wrapping material required for each coil, minimizing excess use and supporting sustainability goals. This approach not only cuts costs but also reflects a commitment to eco-friendly operations.
4.2 Energy-Efficient Machinery
Energy consumption is a significant concern for manufacturers, and the latest packaging lines incorporate energy-efficient machinery to mitigate this issue. From conveyor systems to automated wrapping equipment, energy-efficient solutions reduce overall power use without compromising performance. For example, certain machines have standby modes or automatically power down when not in use, conserving energy during downtime. By investing in energy-efficient machinery, manufacturers can significantly reduce their carbon footprint, contributing to both environmental responsibility and long-term cost savings.

4.3 Sustainable Supply Chain Integration
Integrated packaging solutions also enhance sustainability by streamlining the supply chain. Advanced tracking and inventory management systems reduce overproduction and allow for more efficient use of materials. This approach enables manufacturers to align packaging operations more closely with actual demand, preventing overstock and unnecessary waste. Furthermore, by digitizing supply chain elements, companies can reduce the need for paper-based tracking, cutting down on resource use and making the entire process more sustainable.
Conclusion
The rise of advanced technologies and integrated solutions in steel coil packaging lines marks a significant leap forward for the industry. With innovations in material handling, automated quality control, and data-driven insights, manufacturers are achieving levels of efficiency and accuracy previously unattainable. As more companies adopt sustainable practices through eco-friendly materials and energy-efficient machinery, the future of steel coil packaging appears both bright and environmentally conscious.

Get Your Best Solution !