Exploring the Economic Advantages of Automated Coil Wrapping Machines
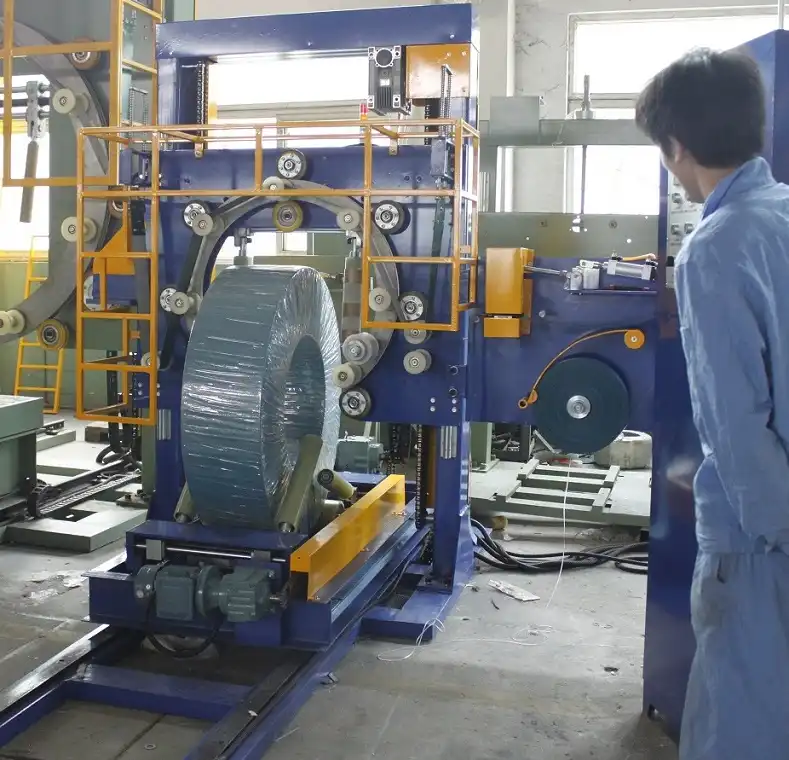
In today's competitive industrial landscape, achieving operational efficiency and cost-effectiveness is crucial for success. Automation has evolved from a trend to a fundamental necessity. For businesses handling significant volumes of coiled materials like steel, wire, or hose, investing in an automated coil wrapping machine offers a strategic advantage. This technology streamlines packaging processes, significantly cuts operational costs, and ensures product integrity during transit and storage. But what are the specific economic benefits that justify this investment? The primary advantages stem from substantial time savings, enhanced packaging consistency, and minimized labor expenditures.
Investing in an automated coil wrapping machine goes beyond acquiring new equipment; it's a long-term commitment to boosting productivity and reducing waste. Industrial automation provides a level of precision and reliability that manual processes cannot match. In sectors where minor inefficiencies accumulate into major expenses, the accuracy offered by automation becomes invaluable. Understanding the financial impact clarifies why automated packaging solutions are essential for maintaining a competitive edge and achieving lean operations.
This guide delves into the tangible economic benefits of automated coil wrapping. These machines are not just about convenience; they represent a strategic investment for businesses aiming to optimize resource use, decrease overheads, and ultimately increase profitability. Implementing this technology makes superior operational efficiency an attainable reality.
(Note: A Table of Contents is recommended here for user navigation. This can be added using a WordPress plugin or block.)
1. How Does Automation Reduce Labor Costs in Coil Wrapping?
1.1 Labor Cost Reduction Through Automated Processes
Labor often constitutes one of the largest operational expenses in manufacturing and warehousing. Manual coil wrapping is typically labor-intensive and time-consuming. An automated coil wrapping machine significantly reduces the reliance on manual labor, often allowing one machine to perform the tasks previously requiring multiple workers. This machine operates with minimal supervision, executing complex wrapping sequences consistently. Consequently, fewer operators are needed for the wrapping process, freeing up valuable personnel to be reassigned to higher-value or more strategic tasks within the facility.
This reduction in labor requirements directly lowers immediate payroll costs and has a long-term impact on expenses related to wages, benefits, training, and recruitment. By leveraging automation, businesses can reallocate these savings to other critical areas, fostering a leaner, more financially resilient operation.
1.2 Enhanced Productivity with Less Human Intervention
Automation dramatically increases the productivity of coil wrapping operations. Unlike manual labor, which is subject to fatigue, breaks, and variability, automated machines maintain a consistent, optimized speed throughout shifts. This reliability not only accelerates the packaging process but also enables businesses to meet higher production demands without incurring overtime costs or hiring additional staff.
The capacity to produce more output in less time directly contributes to revenue potential. In markets where quick turnaround times are a key differentiator, automated coil wrapping provides a significant competitive advantage. Maintaining a swift and uninterrupted production flow allows operations to be more responsive to customer needs and market fluctuations without straining resources.
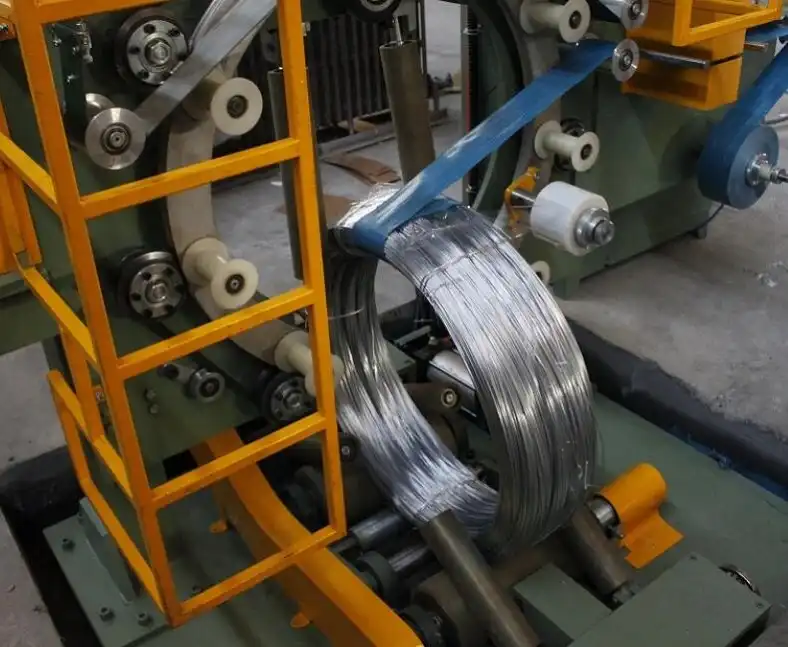
1.3 Reducing Workplace Injuries and Associated Costs
Implementing automation significantly improves workplace safety by removing employees from potentially strenuous or hazardous tasks. Manually wrapping large, heavy coils can involve repetitive motions and heavy lifting, increasing the risk of musculoskeletal injuries. Automated machines handle these demanding tasks precisely and safely, drastically reducing workers' exposure to physical risks. This focus on safety leads to fewer workplace injuries, which in turn lowers costs associated with workers' compensation claims, insurance premiums, and lost productivity due to employee absence.
Prioritizing worker safety through automation is not just an ethical imperative but also a sound economic strategy. A safer work environment minimizes costly disruptions and fosters a more positive and productive workforce. Resources like those provided by the Occupational Safety and Health Administration (OSHA) highlight the financial benefits of proactive safety measures ([link to OSHA or relevant safety resource could be added here]).
2. What Is the Role of Material Efficiency in Cost Savings?
2.1 Precision in Material Use
Automated coil wrapping machines are engineered for precision. They can be programmed to apply the exact amount of wrapping material (like stretch film, VCI paper, or strapping) required for optimal protection, tailored to specific coil dimensions and product requirements. This precise application prevents the material overconsumption common in manual wrapping, where operators might err on the side of caution, leading to significant waste over time. Automation ensures each coil receives consistent, optimized coverage, directly reducing material costs.
This enhanced material efficiency also supports environmental sustainability goals. Using less packaging material translates to a smaller environmental footprint and less waste generation. For modern businesses focused on both economic performance and corporate social responsibility, optimizing material usage is a smart strategy with dual benefits.
2.2 Minimizing Packaging Waste
Packaging waste represents a often-overlooked operational cost. Automated coil wrapping systems are designed to minimize this waste by optimizing the wrap pattern and tension control, applying material efficiently only where needed. This contrasts sharply with manual methods where inconsistencies can lead to excessive material use and higher scrap rates.
Reducing waste not only saves money on purchasing materials but also lowers expenses related to waste disposal and recycling. Managing industrial waste can be costly, and regulations are often stringent. An automated system helps control these costs by minimizing the volume of packaging waste generated per unit, contributing to a cleaner and more cost-effective operation overall. Information on industrial waste reduction can often be found through resources like the Environmental Protection Agency (EPA) ([link to EPA or relevant environmental resource could be added here]).
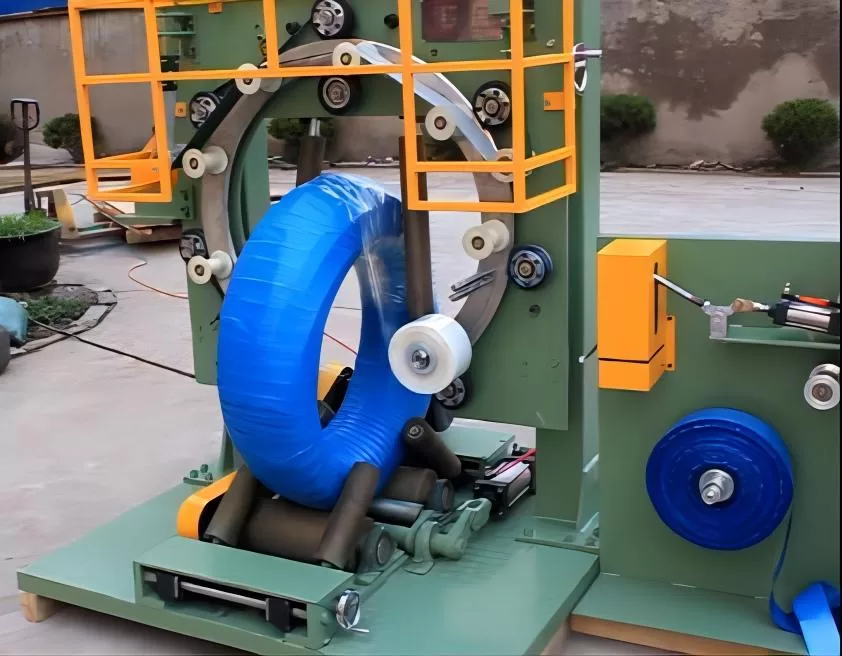
2.3 Enhanced Quality Control through Consistent Material Application
A key benefit tied to material efficiency is improved quality control. Automated machines apply wrapping materials with consistent tension and overlap, ensuring every coil is packaged to the same high standard. This uniformity significantly reduces the risk of packaging failures that could lead to product damage during handling, shipping, or storage. Properly protected coils minimize costly returns, customer complaints, warranty claims, and repairs associated with inadequate packaging.
Consistent, professional-looking packaging also enhances brand perception. Customers receiving well-wrapped, undamaged products are more likely to trust the quality and reliability of the supplier. By maintaining high packaging standards through automation, businesses not only avoid costs associated with damage but also build customer loyalty and satisfaction – invaluable assets in competitive markets.
3. How Does Consistency Improve Product Quality and Reduce Waste?
3.1 Uniformity in Packaging for Product Protection
The primary advantage of automated coil wrapping lies in its consistency. Manual wrapping inevitably introduces variations between coils, potentially compromising protection levels. Automated systems, however, execute pre-programmed wrap cycles identically every time, applying materials evenly and securely. This uniform protection minimizes the chance of damage from moisture, dust, impacts, or shifting during transit. Ultimately, this leads to fewer damaged goods, reducing the costs associated with replacements, rework, and scrap.
Consistently wrapped coils assure customers of reliable product quality upon arrival. Furthermore, optimized, uniform packaging often eliminates the need for secondary or excessive protective layers, saving on both material costs and the labor required to apply them.
3.2 Reducing Variability to Control Costs
Variability in manual processes leads to unpredictable costs. Operators might use inconsistent amounts of wrapping material, making it difficult to accurately forecast packaging expenses. Automated wrapping systems eliminate this guesswork by adhering strictly to programmed parameters, using only the predetermined, necessary amount of material for each coil. This predictability is a direct cost-saving measure, preventing overspending on materials and ensuring adequate protection without excess.
Reduced variability also simplifies budgeting and cost analysis. Knowing the precise material consumption per coil allows for accurate cost allocation and improved financial planning, contributing to better overall cost management within the production or logistics chain.
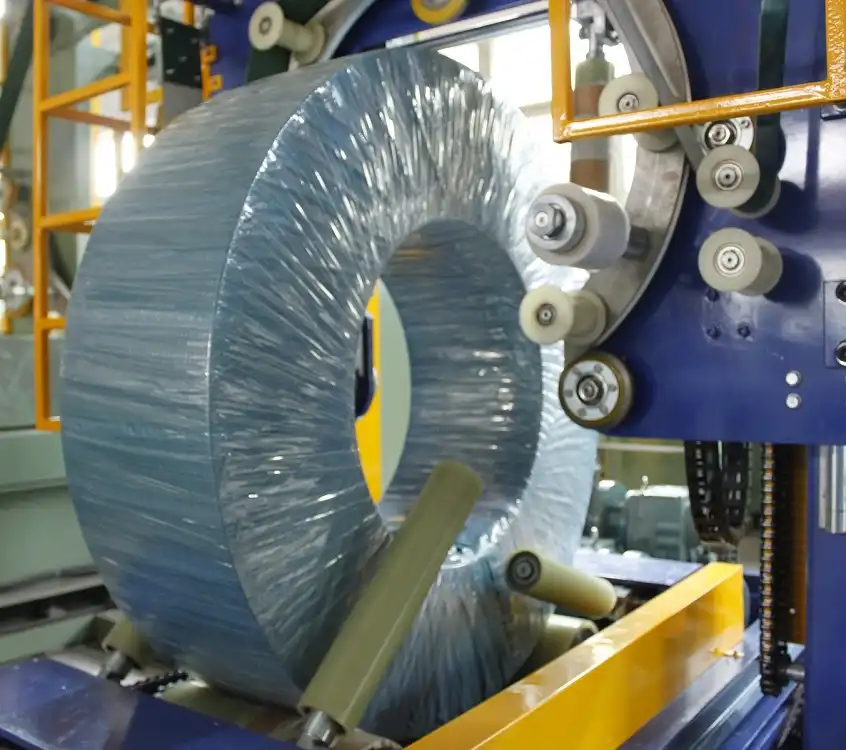
3.3 Quality Assurance with Minimal Supervision
Many modern automated wrapping machines incorporate sensors and control systems that monitor the wrapping process in real-time. These features can detect issues like film breaks, incorrect tension, or material depletion, often pausing the operation or making automatic adjustments to maintain quality standards. This built-in quality assurance minimizes errors without requiring constant human oversight. Consequently, the need for extensive manual inspection is reduced, freeing up personnel while ensuring high packaging integrity.
Automated systems inherently reduce the potential for human error, which can be costly to rectify (e.g., re-wrapping improperly secured coils). By entrusting consistency to a machine, businesses can confidently maintain high quality standards across their entire output, enhancing reliability and customer trust.
4. Why Does Automation Lead to Long-Term Operational Savings?
4.1 Durability and Reduced Maintenance Costs
Industrial automated coil wrapping machines are typically engineered for demanding environments and continuous operation. Constructed with robust materials and high-quality components, they offer greater durability compared to manual tools or less integrated systems. This resilience translates into fewer breakdowns, less frequent need for repairs, and lower overall maintenance costs throughout the machine's lifespan. Automated systems perform repetitive tasks efficiently with minimal wear on critical parts, reducing the likelihood of expensive emergency repairs or component replacements.
Investing in durable, high-quality automation provides a reliable long-term asset. It minimizes operational disruptions caused by unexpected downtime, ensuring a smooth, uninterrupted workflow that consistently meets production targets. This contributes to a lower Total Cost of Ownership (TCO) compared to relying solely on manual labor or less robust equipment.
4.2 Energy Efficiency for Lower Utility Bills
Modern automated machinery often incorporates energy-efficient designs. Features like variable frequency drives (VFDs) for motors, optimized power usage algorithms, and automatic standby modes help reduce electricity consumption during operation and idle periods. This focus on energy efficiency leads directly to lower utility bills, contributing to significant operational cost savings over time, particularly in energy-intensive industrial settings.
Reducing energy consumption not only impacts the bottom line but also aligns operations with sustainability initiatives and potential environmental regulations. An energy-efficient automated wrapper provides both economic and ecological benefits, enhancing the company's profile as a responsible manufacturer.
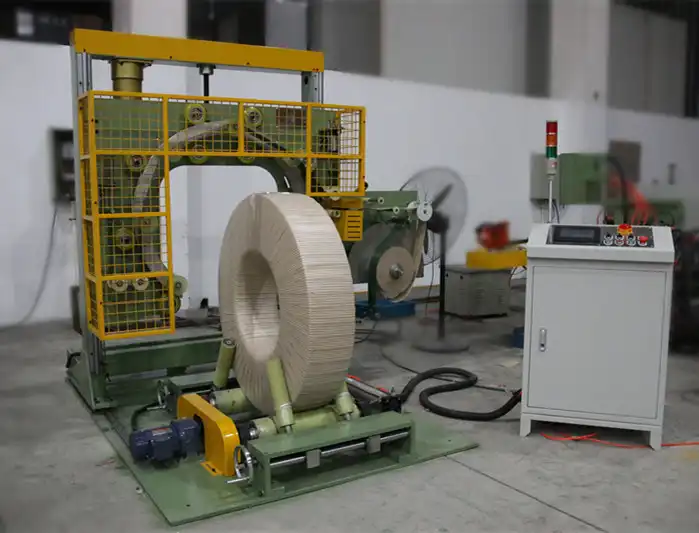
4.3 Scalability and Adaptability for Future Growth
Automated coil wrapping systems offer inherent scalability to accommodate changing business needs. Many machines feature modular designs or programmable controls that allow easy adjustment for different coil sizes, weights, and specific wrapping requirements (e.g., varying numbers of wraps, different material types). This adaptability means that as production volumes increase or product lines diversify, the existing automated system can often handle the changes without requiring complete replacement or major capital reinvestment.
This scalability is crucial for long-term operational savings. It future-proofs the packaging operation, ensuring that growth can be managed efficiently without incurring disproportionately high additional costs for equipment upgrades. Investing in a flexible automated system prepares the business for expansion and evolving market demands.
Conclusion: Automation as a Pathway to Economic Efficiency
Investing in an automated coil wrapping machine is far more than a simple equipment purchase; it represents a strategic decision aimed at enhancing long-term operational efficiency, controlling costs, and optimizing resource management. The economic benefits are clear and measurable:
- Reduced Labor Costs: Lowering reliance on manual labor and associated expenses.
- Improved Material Efficiency: Minimizing material consumption and packaging waste.
- Enhanced Product Quality: Ensuring consistent packaging for better product protection and fewer damage claims.
- Increased Productivity: Achieving higher throughput with reliable, continuous operation.
- Long-Term Savings: Benefiting from durability, energy efficiency, and scalability.
By improving consistency, boosting safety, and enabling scalable production, automation provides a sustainable and economically sound approach to coil wrapping. Choosing an automated solution is a commitment to operational excellence – adopting technology that meets today's demands while adapting to tomorrow's challenges, all while protecting products and bolstering the company's financial health. In the demanding industrial sector, where efficiency directly impacts profitability, automated coil wrapping machines stand out as a prudent, value-driven investment.

Get Your Best Solution !