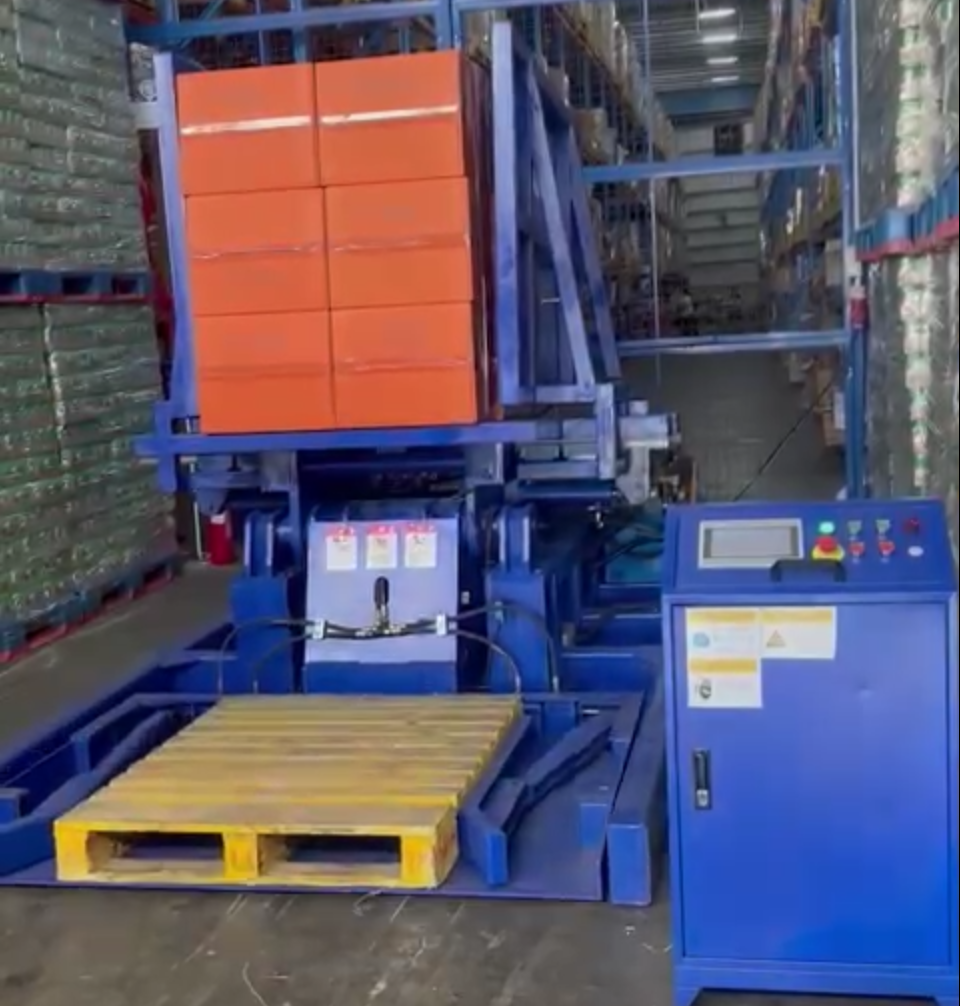
In the logistics and manufacturing industries, pallet changing machines have revolutionized the way goods are handled, transported, and stored. These machines are not just about efficiency; they are about safety, precision, and maximizing throughput. As I delved into the myriad options available, I found myself wondering: how do businesses decide which type of pallet changer is the perfect fit for their operations? This question led me to explore their functionalities, advantages, and the critical factors that influence a buyer’s decision.
Pallet changing machines come in many forms, from traditional manual systems to fully automated solutions equipped with cutting-edge technologies. Each type serves a specific purpose, tailored to different industry needs and operational scales. To make the right choice, you need a comprehensive understanding of the types available and their unique benefits.
Transitioning into the world of pallet changers requires more than just technical know-how; it demands insight into how these machines integrate with a company’s workflows, scalability needs, and long-term goals. This exploration will provide clarity on the options available and how to approach the selection process for your specific requirements.
[Claim]
The right pallet changing machine can save time, reduce costs, and ensure seamless operations, making it a cornerstone of modern supply chain efficiency.
1. What Are the Types of Pallet Changing Machines?
1.1 Overview of Standard Pallet Changers
Standard pallet changers are often the backbone of small to mid-sized warehouses. These machines typically handle the manual swapping of pallets, allowing operators to quickly replace damaged or incompatible pallets without disrupting workflows. They are designed for straightforward operations, making them an excellent choice for businesses with limited automation needs.
With capacities ranging from 1,000 kg to 3,000 kg, these machines are versatile and capable of managing a variety of pallet materials, including wood, plastic, and metal. Their simplicity translates to lower costs and minimal training requirements, which is why they are prevalent in industries like retail, pharmaceuticals, and light manufacturing.
1.2 Advanced Features in Modern Systems
Modern pallet changers have evolved to include automated systems with sensors, hydraulic lifts, and robotic arms. These advanced features significantly enhance speed and precision, making them ideal for high-volume operations. For instance, automated pallet changers can handle up to 60 pallets per hour, reducing labor dependence and minimizing human error.
A standout feature in modern systems is their adaptability to diverse pallet sizes and configurations. Whether your operation involves euro pallets, industrial pallets, or custom sizes, these machines can be adjusted to accommodate the required dimensions seamlessly.
Feature | Standard Pallet Changer | Automated Pallet Changer |
---|---|---|
Capacity | 1,000–3,000 kg | 3,000–5,000 kg |
Speed | 10–15 pallets/hour | Up to 60 pallets/hour |
Training Required | Minimal | Moderate to High |
1.3 Cost Comparisons Between Manual and Automated Systems
Investing in a pallet changer involves evaluating upfront costs against long-term benefits. Manual pallet changers typically cost between $5,000 and $15,000, depending on size and capacity. Automated systems, on the other hand, start at $30,000 and can exceed $100,000 for high-end models with advanced features.
While the initial cost of automation may seem steep, the return on investment (ROI) becomes evident over time. Automated systems not only reduce labor costs but also minimize downtime, enhance productivity, and improve accuracy in pallet handling.
1.4 Industry-Specific Applications of Pallet Changers
Each industry has unique requirements for pallet changing machines. In the food and beverage sector, for example, hygiene is paramount. Automated systems equipped with sterilization features ensure compliance with stringent safety standards. Meanwhile, in logistics and shipping, speed and versatility are critical, making robotic pallet changers a preferred choice.
Industries such as pharmaceuticals and electronics often require precision handling to avoid damage to sensitive goods. Specialized pallet changers with soft grips and adjustable pressure settings cater to these needs, ensuring product safety during transitions.
1.5 Two Facts About Machine Durability and Energy Consumption
Fact 1 (True): Automated pallet changers often have energy-efficient modes that reduce power consumption by up to 20% during idle periods, making them more sustainable for long-term use.
Fact 2 (False): All pallet changers require extensive lubrication every 24 hours to maintain functionality. Modern systems are designed with self-lubricating components that reduce maintenance demands.
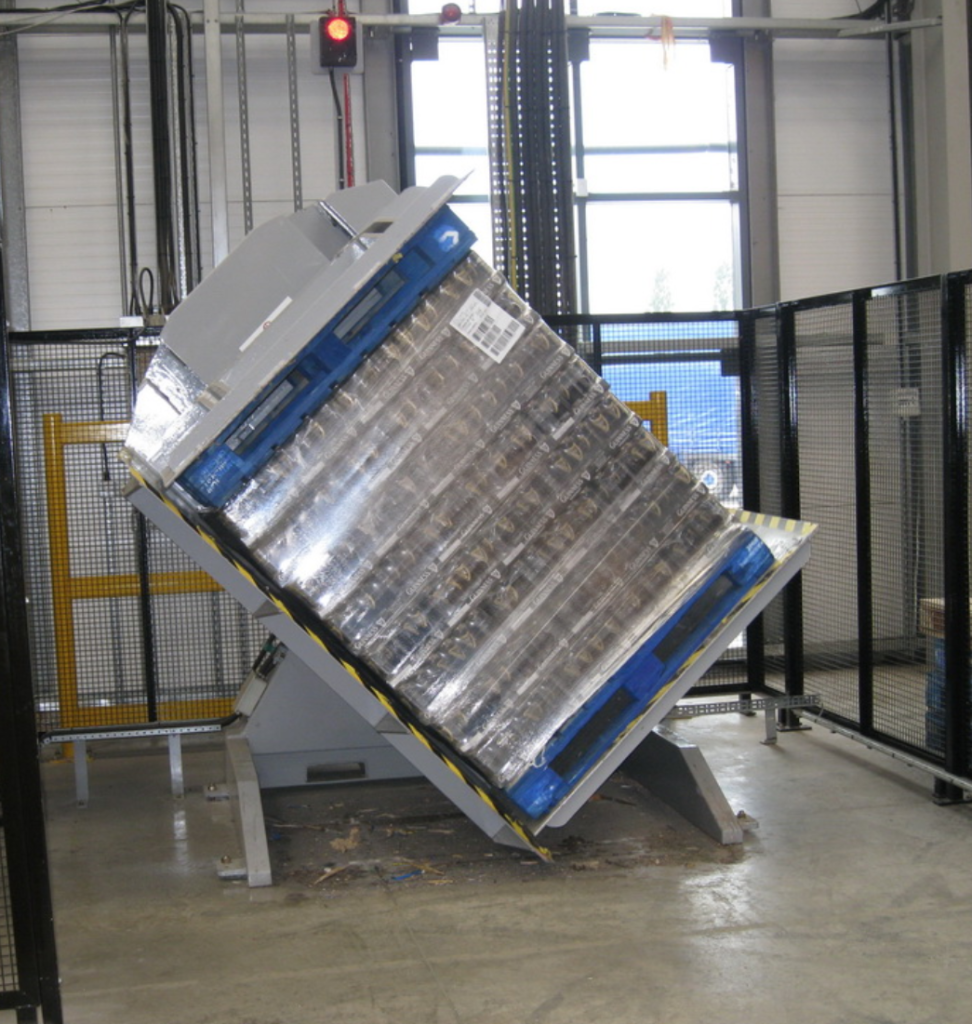
2. How Do Pallet Changers Address Specific Operational Challenges?
2.1 Adapting to High-Volume Warehouses
High-volume warehouses present unique challenges, such as the need to handle a large number of pallets quickly and efficiently. Pallet changers designed for these environments are equipped with high-capacity loaders and automated systems capable of handling up to 100 pallets per hour.
For instance, warehouses managing fast-moving consumer goods (FMCG) require seamless integration between pallet changers and conveyor systems. Automated solutions ensure that pallets are swapped without delays, keeping the supply chain running smoothly. These machines also reduce reliance on manual labor, a critical factor for meeting the demands of peak operational periods.
2.2 Safety Features to Prevent Workplace Accidents
Safety is a paramount concern when introducing heavy machinery into a workspace. Modern pallet changers incorporate features like safety guards, emergency stop buttons, and sensors that detect obstructions. These measures significantly reduce the risk of workplace accidents, protecting both employees and equipment.
Additionally, advanced machines come with load stability systems that prevent goods from tipping over during pallet swaps. This is particularly important in industries handling fragile or hazardous materials. According to a 2023 industry report, warehouses with automated pallet changers reported a 35% reduction in workplace injuries compared to those relying on manual systems.
Safety Feature | Manual Systems | Automated Systems |
---|---|---|
Safety Guards | Limited | Extensive |
Emergency Stop Button | Standard | Advanced with Sensors |
Load Stability Systems | N/A | Fully Integrated |
2.3 ROI: Are Pallet Changers Worth the Investment?
Calculating the ROI of a pallet changer requires evaluating both tangible and intangible benefits. On average, automated systems can reduce operational costs by 20% within the first year of implementation. Factors contributing to this ROI include reduced labor costs, lower error rates, and minimized downtime.
Moreover, automated pallet changers enhance scalability, allowing businesses to handle increasing volumes without significant additional investments. For example, a logistics center that implemented a $50,000 pallet changer recovered its investment within 18 months through increased productivity and reduced manual handling costs.
2.4 Common Misconceptions About Pallet Changers
One common misconception is that pallet changers are only suitable for large-scale operations. While it’s true that automated systems are often used in high-volume environments, manual and semi-automated solutions are highly effective for smaller businesses. These machines provide an affordable entry point into automation, helping SMEs improve efficiency without a significant capital outlay.
Another misconception is that these machines are challenging to integrate into existing workflows. In reality, modern pallet changers are designed for seamless integration, with customizable features that adapt to a variety of operational setups.
2.5 Two Facts About Maintenance Costs and Lifespan
Fact 1 (True): Automated pallet changers typically have a lifespan of 10–15 years with regular maintenance, offering long-term value.
Fact 2 (False): Maintenance costs for automated systems are always higher than those for manual systems. In fact, advanced machines often require less frequent servicing due to their self-diagnostic capabilities, which detect and address issues before they escalate.

3. What Are the Key Considerations When Selecting a Pallet Changer?
3.1 Identifying the Operational Scale of Your Business
The first step in choosing a pallet changer is assessing the scale and nature of your operations. For small businesses, manual or semi-automated systems may be sufficient, providing a balance between cost and functionality. Larger enterprises, however, benefit from fully automated systems that can handle high volumes and complex workflows.
A practical way to evaluate your needs is to conduct a cost-benefit analysis. Consider factors such as current labor costs, pallet handling volumes, and the potential for future expansion. For example, a company handling 500 pallets per day may find that an automated system pays for itself within two years through improved efficiency.
3.2 Comparing Brands and Technologies
With numerous brands and technologies on the market, selecting the right pallet changer can be overwhelming. Key factors to consider include the machine’s build quality, warranty terms, and available customer support. Leading brands often provide detailed case studies and customer testimonials, which can offer valuable insights into real-world performance.
Another consideration is compatibility with existing equipment. Machines that integrate seamlessly with your current systems minimize disruption during implementation, ensuring a smoother transition to automation.
3.3 Evaluating Service and Support Options
Service and support are critical when investing in pallet changers, as even minor downtime can disrupt operations. Look for manufacturers that offer comprehensive after-sales support, including remote diagnostics, on-site repairs, and readily available spare parts.
In one instance, a company that prioritized robust service agreements reported a 40% reduction in downtime compared to competitors relying on basic support packages. This highlights the importance of choosing a supplier committed to long-term customer satisfaction.
3.4 Adopting Sustainable Solutions
Sustainability is an increasingly important consideration for businesses investing in pallet changers. Machines designed with energy-efficient components and recyclable materials align with corporate sustainability goals while reducing operational costs.
For example, some automated systems feature regenerative braking, which recovers energy during operation and reduces overall power consumption. Additionally, choosing durable machines with long lifespans minimizes waste, contributing to a more sustainable supply chain.
3.5 Two Facts About Customization Options and Initial Setup Time
Fact 1 (True): Many modern pallet changers offer customizable features, such as adjustable clamps and programmable settings, to cater to specific operational needs.
Fact 2 (False): Initial setup always takes weeks to complete. In reality, many systems are designed for quick installation, with basic configurations operational within two to three days.
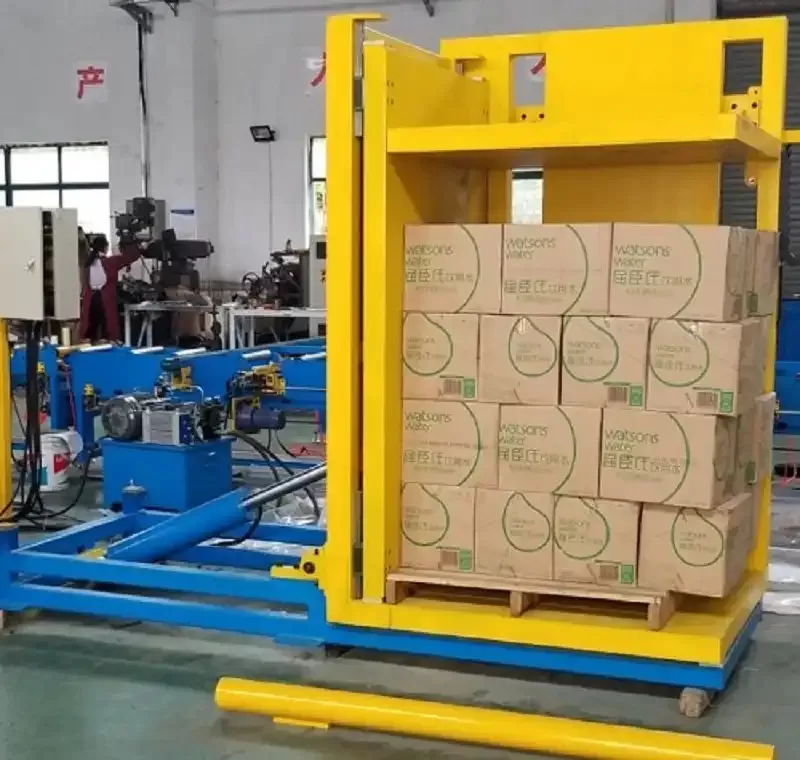
4. How to Make the Final Decision?
4.1 Balancing Cost and Functionality
Selecting the right pallet changer requires finding a balance between cost and functionality. While manual systems are cost-effective, they may not provide the speed or precision needed for larger operations. Automated systems, though more expensive upfront, deliver long-term savings by reducing labor costs and operational inefficiencies.
A practical approach is to calculate the total cost of ownership (TCO), factoring in initial investment, maintenance costs, and potential productivity gains. For example, a mid-sized warehouse investing in a $50,000 automated system may realize savings of $20,000 annually through labor reduction and faster pallet handling times.
4.2 Assessing Long-Term Scalability
Businesses experiencing rapid growth must consider scalability when investing in pallet changers. Machines with modular designs or upgradeable features offer flexibility to accommodate increasing volumes or evolving operational needs. This ensures that your investment remains relevant as your business expands.
For example, a logistics company initially handling 300 pallets per day can invest in a semi-automated system with the capability to upgrade to full automation. This forward-thinking approach avoids the need for a complete system overhaul, saving both time and resources.
4.3 Reviewing Case Studies for Insights
Case studies offer valuable insights into how pallet changers perform in real-world scenarios. These examples often highlight challenges faced during implementation and the solutions that delivered measurable results. For instance, a food processing company reduced pallet handling times by 40% after integrating an automated system tailored to their hygiene standards.
Examining industry-specific case studies can also help you understand how similar businesses have benefited from various features, such as adjustable clamps for fragile goods or high-speed handling for perishable items.
4.4 Final Steps Before Purchase
Before finalizing your purchase, conduct thorough testing and review. Many manufacturers offer demo units or trial periods to help you assess the machine’s compatibility with your operations. Additionally, involve key stakeholders, including operators and maintenance teams, to ensure the system meets their practical requirements.
Another critical step is to review warranty terms and service agreements. Opting for a supplier with comprehensive after-sales support ensures peace of mind and long-term reliability for your investment.
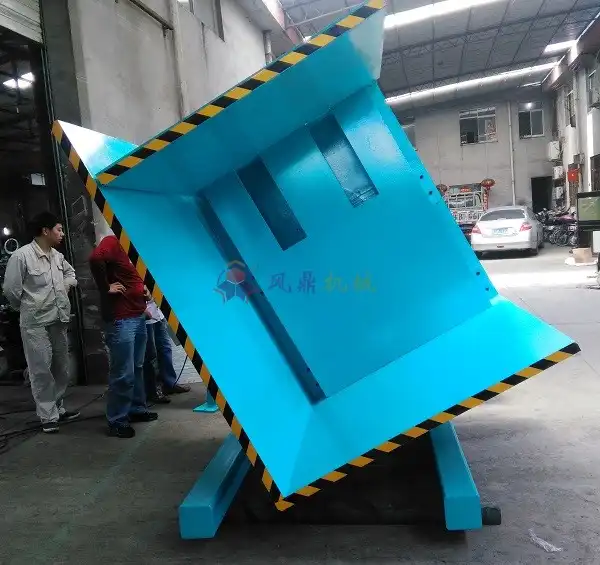
Conclusion
Pallet changers are a vital component of efficient supply chains, offering solutions for faster pallet handling, enhanced safety, and reduced operational costs. From understanding the types of machines available to evaluating specific features and benefits, the decision-making process demands careful consideration of both current and future needs.
[Claim]
By investing in the right pallet changing machine, businesses can unlock significant operational efficiencies, reduce costs, and position themselves for long-term success in an increasingly competitive market.

Get Your Best Solution !