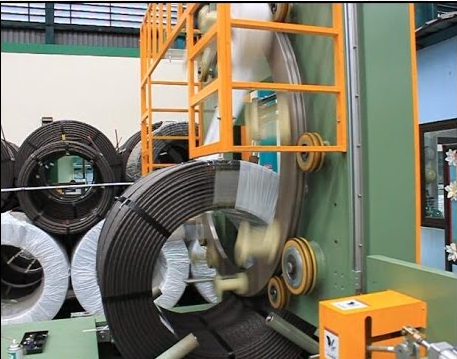
In the industrial world, where every process is meticulously planned for efficiency, coil wrapping machines play a critical role. These machines don’t merely wrap products; they protect, secure, and maintain the integrity of coiled materials such as steel, aluminum, and copper, ensuring they reach their destination intact. But with such a vast array of options, how do I decide which coil wrapping machine meets my specific needs? It’s not just about picking a machine—it’s about understanding the distinct types, their features, and their advantages.
Selecting the right type of coil wrapping machine goes beyond mere functionality. It’s an investment in operational efficiency, product protection, and even workplace safety. As I delve into the types of coil wrapping machines available, I’m guided by a simple principle: finding a machine that aligns with both current and future needs, ensuring a balance between cost and performance.
As the demand for faster, safer, and more efficient packaging solutions grows, knowing the options available and their benefits becomes essential. The choice of a coil wrapping machine isn’t only a logistical decision—it’s a strategic one, impacting every aspect of my business operations.
[claim] Understanding the different types of coil wrapping machines helps in selecting the best fit, ensuring that packaging processes are efficient, cost-effective, and tailored to specific industry needs.
- 1. What Are Horizontal Coil Wrapping Machines and Their Applications?
- 2. How Do Vertical Coil Wrapping Machines Differ?
- 3. What Are Automatic Coil Wrapping Machines and Why Are They Beneficial?
- 4. What Customization Options Exist for Specialized Needs?
- Conclusion: Choosing the Right Coil Wrapping Machine for Your Unique Needs
1. What Are Horizontal Coil Wrapping Machines and Their Applications?
1.1 Understanding Horizontal Coil Wrapping Machines
Horizontal coil wrapping machines are designed specifically for wrapping elongated or cylindrical coils. Unlike other machines that may require manual adjustments, horizontal machines can fully encase the coil in protective layers, sealing every surface uniformly. The coil is laid horizontally, allowing the machine’s wrapping arms to circle around it, applying precise layers of wrapping material. This setup is particularly useful when dealing with coils that have long diameters, providing a consistent wrap from end to end.
Horizontal coil wrapping machines excel in environments where uniform protection is essential. From steel manufacturers to cable producers, industries that require high levels of protection favor these machines for their reliability and ability to safeguard the coil’s surface. Given the configuration, the machine can achieve multiple wrap patterns—spiral, full encasement, or selective wraps, depending on the level of protection required.
1.2 Key Advantages of Horizontal Coil Wrapping
One of the primary advantages of horizontal coil wrapping machines is their flexibility with various coil diameters and lengths. These machines come with adjustable settings that allow operators to tweak wrapping speed, tension, and layering, adapting to different product needs. Horizontal machines provide a level of customization that enhances both efficiency and product integrity, as coils are less likely to be damaged or exposed to environmental factors.
The layout of horizontal machines also contributes to faster operational speeds. Since the machine wraps coils horizontally, it minimizes movement, allowing for a seamless process from loading to wrapping and unloading. This efficiency benefits high-volume operations, where productivity and speed directly impact profitability.

1.3 Applications of Horizontal Coil Wrapping in Industrial Settings
Industries that require heavy-duty protection and long-term storage of coils often prefer horizontal wrapping machines. For example, steel coils intended for overseas transport face harsh environmental conditions, making full coverage essential. Horizontal machines are ideal for these scenarios as they provide consistent protection across all coil surfaces, ensuring products withstand shipping and handling stresses.
Additionally, industries dealing with electrical cables, which are particularly vulnerable to damage from impact or moisture, rely on horizontal coil wrapping machines. By applying a precise, snug wrap, these machines protect sensitive materials and reduce the risk of costly damages.
2. How Do Vertical Coil Wrapping Machines Differ?
2.1 Design and Functionality of Vertical Coil Wrapping Machines
Vertical coil wrapping machines are structured to handle coils that are positioned vertically during the wrapping process. This design is advantageous for coils with smaller diameters and taller profiles, as it enables the machine to wrap from the base up, covering the outer layers of the coil. These machines are well-suited for scenarios where space is limited, as their vertical layout takes up less floor space compared to horizontal models.
Vertical machines often employ rotating arms or spinning tables to wrap the coils. This setup allows for precise layering, making it ideal for coils that don’t require full encasement but still need reliable protection. As the machine moves, it carefully applies the wrapping material, ensuring each layer is secure without overusing materials. This level of control is crucial for maintaining consistency in industries where product uniformity is key.
2.2 Efficiency Benefits of Vertical Wrapping
A major advantage of vertical coil wrapping machines lies in their efficient use of space and material. Since these machines handle coils upright, they require less floor area, making them ideal for facilities with limited space. Additionally, vertical machines can be more energy-efficient, as they typically operate with fewer moving parts, resulting in less wear and tear and lower maintenance requirements.
For facilities looking to increase throughput without major spatial investments, vertical wrapping machines offer a compact yet powerful solution. By maximizing floor space and reducing material usage, these machines contribute to a leaner, more cost-effective packaging operation.
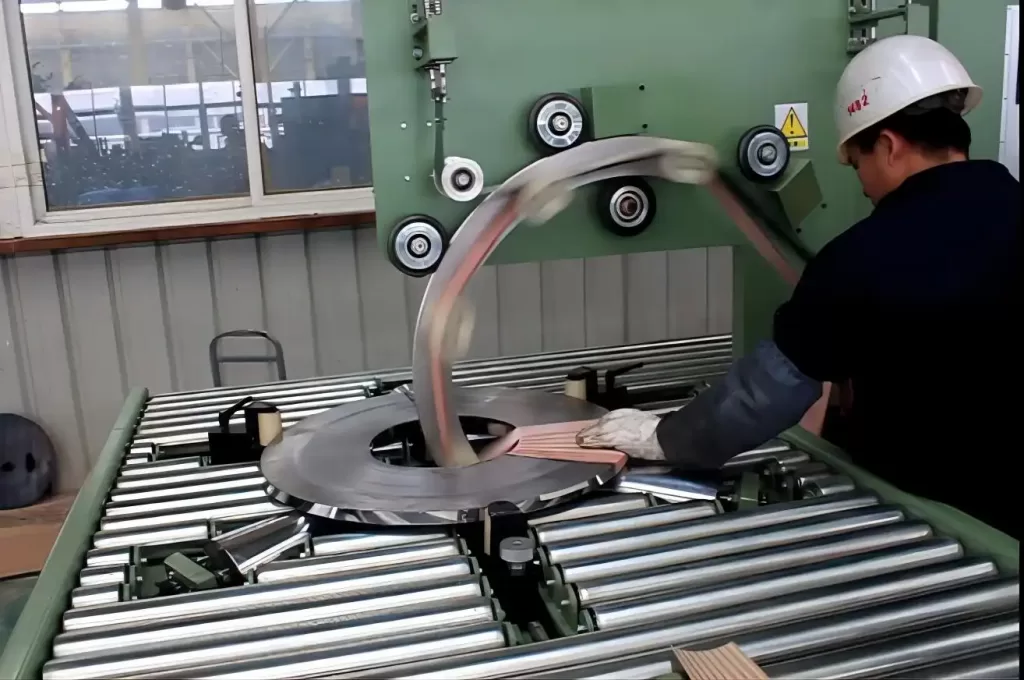
2.3 Common Industries Using Vertical Wrapping Machines
Vertical coil wrapping machines are popular in industries where space efficiency and product accessibility are essential. For example, facilities that package lightweight aluminum or copper coils often turn to vertical machines. These materials benefit from the secure wrapping provided by vertical machines, as they tend to be lighter and more manageable when positioned vertically.
Vertical machines are also preferred in the electrical sector, where large quantities of small-diameter cables or wires require careful packaging. These machines allow quick, standardized wraps that protect the integrity of each coil while ensuring that production can continue without major interruptions or spatial constraints.
3. What Are Automatic Coil Wrapping Machines and Why Are They Beneficial?
3.1 The Power of Automation in Coil Wrapping
Automatic coil wrapping machines bring a new level of convenience and efficiency to industrial operations. Unlike manual or semi-automatic machines, automatic systems handle the entire wrapping process from start to finish with minimal human intervention. These machines are often equipped with sensors, programmable settings, and self-diagnostic tools, allowing them to adjust wrapping parameters in real-time based on coil specifications. This automation eliminates variability and boosts efficiency, as each coil is wrapped consistently, regardless of size or material.
Automation also helps minimize labor requirements. With automatic machines, operators can oversee multiple processes simultaneously, freeing up resources and reducing labor costs. The reliability of these machines not only speeds up operations but also enhances productivity across the board, enabling companies to meet higher production targets with less effort.
3.2 Consistency and Quality Control with Automated Machines
Automated coil wrapping machines are renowned for their consistency and precision. Because they operate on pre-set parameters, they apply the exact amount of wrapping material needed for each coil, reducing waste and improving the quality of the wrap. This consistency is especially valuable in industries where uniformity is critical, such as in the production of steel coils destined for export, where products must withstand harsh transit conditions.
Furthermore, automated machines often come with quality control features, such as tension control and layer monitoring. These features ensure that each layer of wrapping adheres tightly and evenly, reducing the risk of coil slippage or damage. With automated quality checks built into the wrapping process, companies can maintain higher standards without dedicating extra resources to manual inspection.
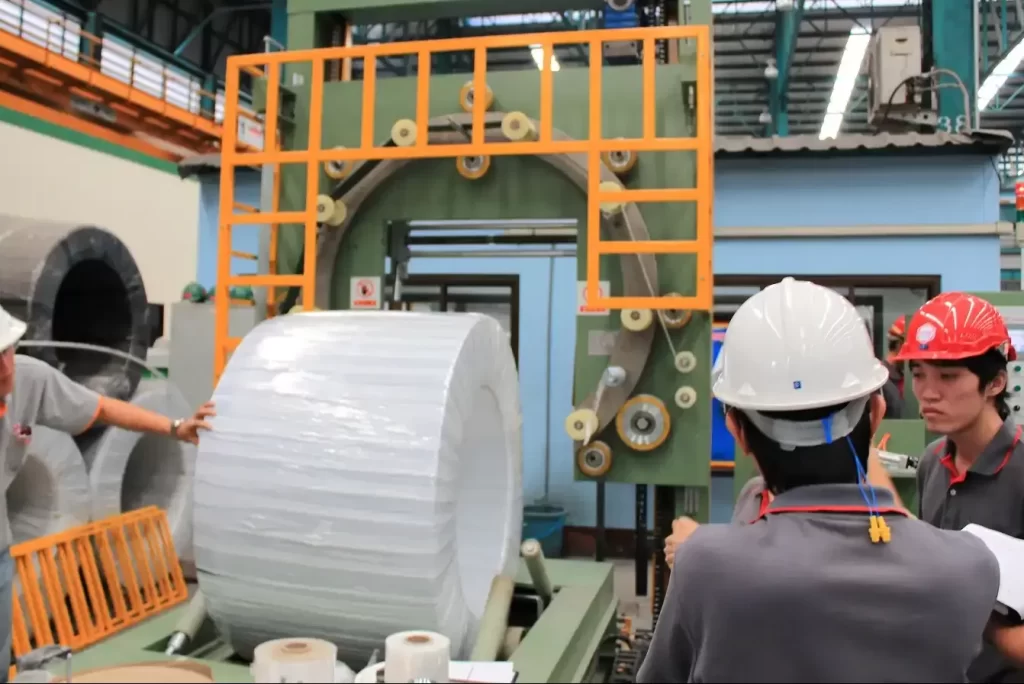
3.3 Enhanced Speed and Scalability in High-Volume Operations
In high-volume industries, speed and scalability are paramount, and automatic coil wrapping machines excel in these areas. By automating repetitive tasks, these machines significantly increase the speed of packaging operations, allowing companies to meet larger orders without compromising on quality. This capability is crucial for manufacturers aiming to scale their operations efficiently, as automatic machines can handle high outputs with ease.
Moreover, these machines are easily programmable, enabling quick adjustments for different coil sizes or types. This flexibility allows companies to switch between product specifications without extensive downtime, further enhancing productivity. Automatic machines are a long-term investment in scalability, providing the means to meet growing demands in a competitive industrial landscape.
4. What Customization Options Exist for Specialized Needs?
4.1 Tailored Wrapping Techniques for Different Coil Specifications
Customization is key for companies with unique coil requirements. Many modern coil wrapping machines come with customizable wrapping settings, allowing for tailored techniques that match the specific needs of various coils. These adjustments might include variable tension settings, selective wrapping zones, or the ability to add extra protective layers. For example, heavy steel coils may require thicker wraps for enhanced protection, while lighter coils might need only minimal layers to avoid excessive material use.
Customized wrapping techniques not only improve product protection but also optimize resource use, ensuring that each coil is wrapped according to its exact requirements. This precision translates to cost savings, as materials are applied where needed without excess.
4.2 Industry-Specific Configurations for Added Efficiency
Certain industries, like automotive or electrical, may require coil wrapping machines with specialized configurations. Some machines offer add-ons like automated labeling or protective film layers designed to shield coils from specific environmental factors, such as moisture or UV exposure. These configurations enhance the machine’s adaptability, making it possible to wrap coils in a way that meets both industry standards and unique customer demands.
In addition to protective layers, some machines come with custom palletizing options, making it easier to stack and transport wrapped coils directly from the machine. These industry-specific features improve overall workflow, making packaging faster and more integrated with other production processes.
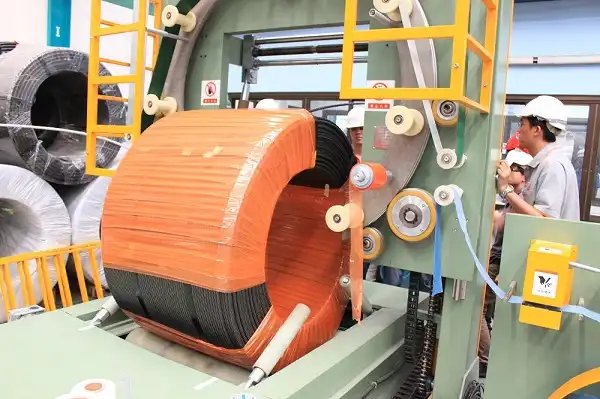
4.3 Flexibility to Upgrade as Needs Evolve
Flexibility in customization also means that companies can upgrade their coil wrapping machines over time. Many machines are built with modular designs, allowing businesses to add new features as their requirements change. Whether it’s integrating new wrapping materials, adjusting for larger coil sizes, or adding more automation features, modular upgrades extend the machine’s lifespan, maximizing its value.
This flexibility to evolve is particularly beneficial in dynamic industries where production needs shift frequently. Rather than investing in an entirely new machine, companies can make incremental improvements, saving on capital expenses while keeping their operations agile and responsive to market demands.
Conclusion: Choosing the Right Coil Wrapping Machine for Your Unique Needs
The variety of coil wrapping machines available today offers solutions for almost every industrial need. From horizontal to vertical and automatic to customized, each type brings unique advantages to the packaging process, catering to different coil specifications, volumes, and environmental challenges. The right choice depends on understanding these distinctions and aligning them with specific operational goals.
Selecting the best coil wrapping machine involves a balance between cost, flexibility, and future scalability. By carefully considering each type’s advantages and customization options, I can choose a machine that not only meets today’s demands but also adapts to tomorrow’s challenges. Investing in the right machine isn’t just about packaging—it’s about securing products, optimizing resources, and maintaining operational efficiency in a competitive landscape.
[claim] Selecting the appropriate coil wrapping machine based on functionality and customization potential ensures that packaging processes remain cost-effective, efficient, and prepared for future demands. This strategic choice can significantly enhance operational resilience and product protection.

Get Your Best Solution !