
In industries handling coiled materials like steel, aluminum, or wire, selecting the optimal packaging method is crucial for operational efficiency, cost management, and maintaining product integrity. While traditional wrapping techniques, often manual or semi-automated, have been standard practice, modern automated coil wrapping machines present a compelling alternative. These systems offer significant advantages by streamlining packaging processes, reducing material consumption, ensuring consistent wrap quality, and enhancing workplace safety.
Comparing automated coil wrapping machines to traditional methods reveals clear benefits beyond simple packaging. These machines automate repetitive tasks, optimize the use of stretch film or other wrapping materials, and significantly improve safety protocols, all while delivering superior protection for coiled products. For businesses seeking to enhance their packaging operations, understanding these advantages highlights why investing in an automated coil wrapping machine is a strategic decision for long-term productivity and profitability.
This article examines the specific benefits of employing coil wrapping machines over conventional methods, detailing how this technology revolutionizes the packaging workflow and boosts overall operational effectiveness.
Key Takeaway: Automated coil wrapping machines offer substantial improvements over traditional methods by increasing speed, cutting material waste, ensuring packaging uniformity, and promoting a safer work environment.
1. Enhanced Operational Efficiency with Coil Wrapping Machines
1.1 Boosting Packaging Speed and Throughput
A primary advantage of automated coil wrapping machines is the dramatic increase in packaging speed compared to traditional methods. Manual wrapping is inherently slower and more labor-intensive, requiring operators to handle coils, apply wrapping material meticulously, and secure the package. Coil wrapping machines automate these steps, significantly cutting down the cycle time per coil. By automating repetitive tasks, operations achieve higher throughput and faster processing, keeping pace with production demands.
The enhanced speed allows more coils to be packaged and prepared for shipment or storage within a given timeframe. This capability is vital for high-volume operations, enabling businesses to meet tight deadlines, maintain smooth production flow, and improve overall profitability through increased output.
1.2 Streamlining Workflows through Automation
Automating the coil wrapping process simplifies the entire packaging workflow and reduces labor requirements. Traditional methods often necessitate multiple personnel for handling and securing heavy or bulky coils, potentially creating bottlenecks and increasing the risk of delays. An automated coil wrapping system can manage loading, wrapping, cutting, and sometimes even unloading with minimal human intervention, freeing up workers for other value-added tasks.
This streamlined approach minimizes idle time and optimizes labor allocation, contributing to a more balanced and efficient operational flow. Automation enhances not just the speed of wrapping but the overall cohesion and reliability of the packaging line.
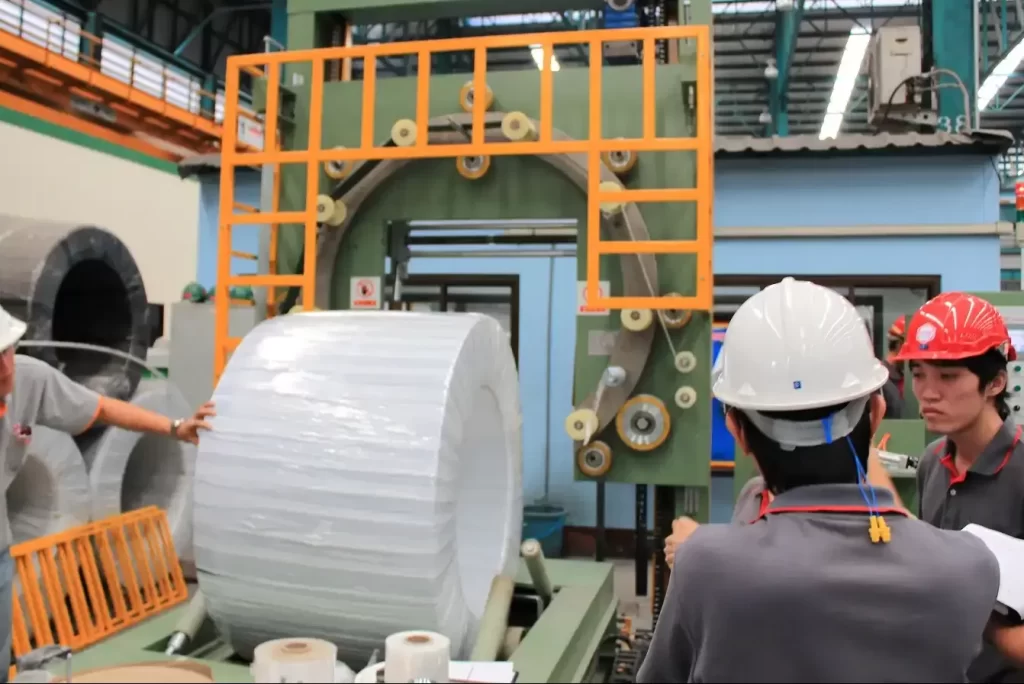
1.3 Minimizing Production Downtime
Coil wrapping machines are engineered for continuous operation in demanding industrial environments. Unlike manual processes susceptible to interruptions from worker fatigue, breaks, or shift changes, automated systems operate consistently with minimal downtime, primarily scheduled for routine maintenance. This reliability ensures the packaging line runs smoothly without frequent stoppages, preventing production delays often associated with traditional methods.
2. Optimizing Material Use for Significant Cost Savings
2.1 Precision Wrapping Reduces Material Waste
A common drawback of manual wrapping is inconsistent material application, often leading to excessive use of stretch film or other packaging supplies to ensure adequate protection. This results in unnecessary material waste and increased operational costs. Coil wrapping machines, conversely, are programmed for precise material application, utilizing the optimal amount of wrap required for secure and protective packaging based on pre-set parameters. This precision minimizes waste and leads to substantial cost savings over time.
Material optimization not only cuts costs but also supports sustainability goals. Reducing consumption of packaging materials aligns with environmentally conscious practices, helping businesses achieve a leaner, greener, and more cost-effective operation.
2.2 Minimizing Rework through Consistent Application
Precision in material usage also minimizes packaging errors and the need for costly rework. Traditional methods can result in inconsistent wrapping – some coils might be under-wrapped, risking damage during handling or transit, while others might be over-wrapped, wasting material. Automated coil wrapping machines apply wrap with consistent tension, overlap, and coverage every time, ensuring each coil meets protection standards on the first pass. This reliability eliminates the need for manual adjustments or re-wrapping.
Reducing rework directly boosts productivity, as valuable time and resources are not diverted to correcting packaging mistakes. Achieving the correct wrap initially conserves materials and maintains a steady, uninterrupted workflow.
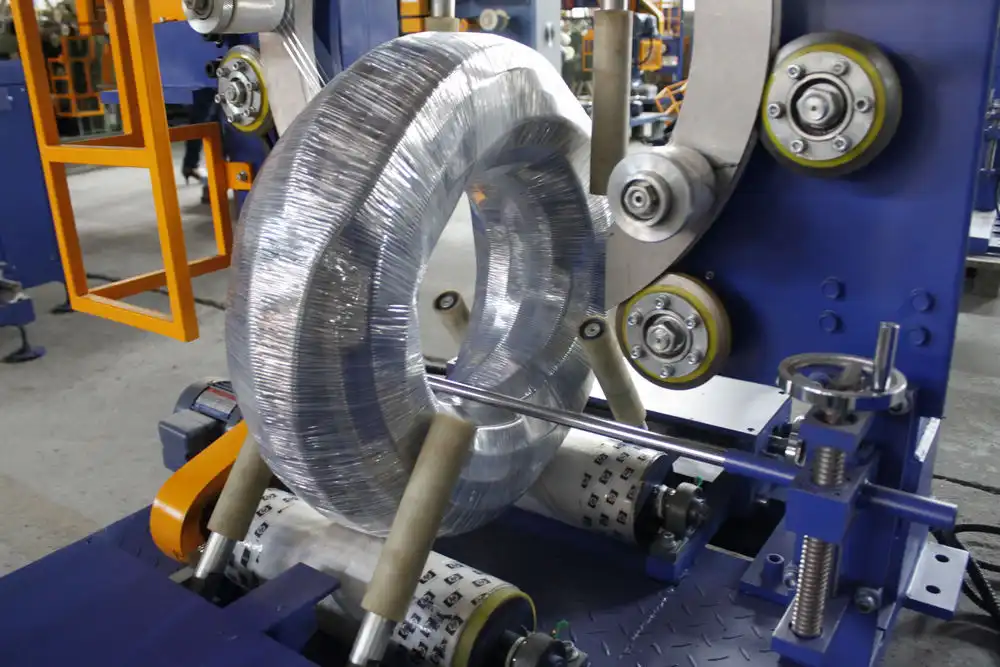
2.3 Achieving Lower Packaging Costs
The efficiency gained from precise material usage translates directly into lower overall packaging costs. By applying a measured, consistent amount of wrapping material to each coil, businesses can accurately forecast material consumption and manage budgets more effectively. In contrast, the variability of manual wrapping often leads to unpredictable material usage and fluctuating expenses, complicating financial planning. The predictability offered by automated systems supports better long-term cost management and control.
3. Improving Product Protection and Quality Control
3.1 Consistent Wrapping for Superior Coil Protection
Achieving uniform wrap coverage is a significant challenge with manual methods, as results can vary based on operator skill and fatigue. Automated coil wrapping machines eliminate this variability, applying wrap consistently across every coil. This ensures each product receives the specified level of protection against environmental factors like moisture, dust, dirt, and physical damage during transit and storage. Consistent wrapping is crucial in industries where products face demanding logistical conditions.
Uniform protection safeguards the integrity of the coiled material, minimizing the risk of corrosion, scratches, or deformation. By reliably securing each coil, businesses can reduce product damage rates, leading to fewer returns and increased customer satisfaction.
3.2 Elevating Quality Control Standards
Packaging consistency is fundamental to effective quality control. Variations inherent in manual wrapping can compromise package integrity, potentially leading to damaged goods or the need for secondary checks and rework. A coil wrapping machine enforces precise wrapping standards for every cycle, minimizing defects and ensuring that each packaged coil meets quality specifications. This systematic approach enhances overall product quality assurance.
Automated wrapping simplifies quality control processes. Since each coil undergoes an identical wrapping procedure, inspections become more straightforward and reliable. Fewer inconsistencies mean less time spent on quality checks and a consistently higher standard of outgoing product packaging.
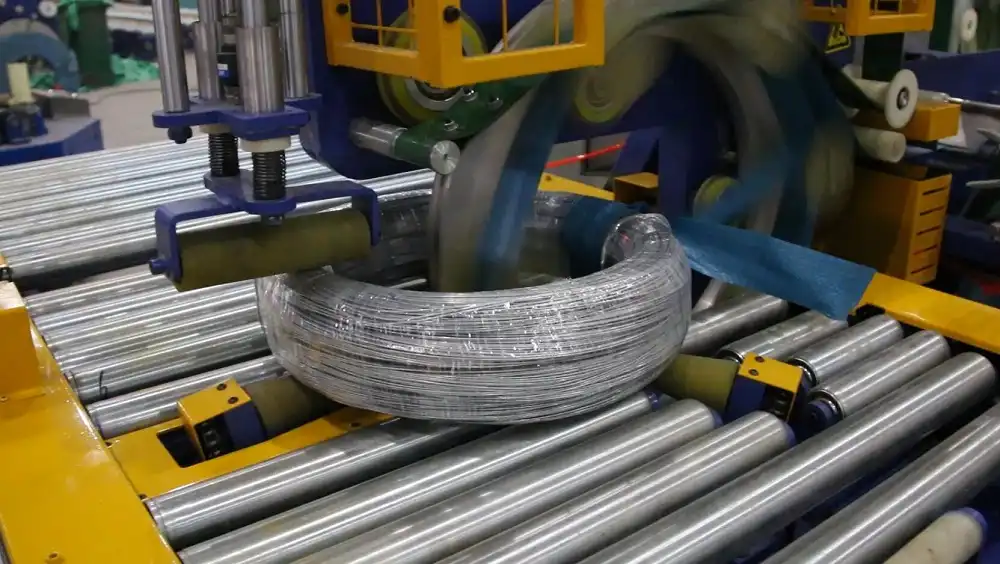
3.3 Professional Presentation Enhances Customer Perception
The final appearance of packaged goods significantly influences customer perception. Inconsistent or sloppy manual wrapping can look unprofessional and detract from the perceived value of the product. Automated coil wrapping machines produce neat, uniform packages consistently, enhancing the product's presentation and conveying professionalism and attention to detail.
A professionally wrapped coil reassures customers about the quality of the product and the supplier's standards. This positive first impression can improve customer satisfaction, strengthen brand reputation, and potentially encourage repeat business.
4. Key Safety Advantages of Automated Coil Wrapping
4.1 Reducing Manual Handling and Workplace Injury Risks
Manual wrapping processes often involve strenuous physical tasks such as heavy lifting, awkward postures, and repetitive motions, all known contributors to workplace injuries like strains and sprains. Coil wrapping machines automate these demanding activities, significantly reducing the physical burden on workers. By minimizing manual handling requirements, automation creates a safer work environment and lowers the incidence of musculoskeletal injuries.
A reduction in injuries leads to fewer work disruptions, lower workers' compensation costs, and improved employee morale. In industrial settings, enhancing safety through automation is both an ethical responsibility and a sound economic strategy, contributing to sustained productivity.
4.2 Integrated Safety Features for Accident Prevention
Modern coil wrapping machines incorporate numerous safety features designed to protect operators and prevent accidents. Standard features often include emergency stop buttons accessible from multiple points, safety interlocks on doors and guards, light curtains or area scanners to detect human presence in hazardous zones, and automatic shutdown mechanisms in case of malfunction. These integrated systems ensure the machine operates safely, even during continuous, high-speed cycles.
Implementing machinery with robust safety features helps businesses comply with occupational health and safety regulations (like those outlined by OSHA or equivalent bodies), minimizing the risk of accidents, potential fines, and safety-related downtime. Safe operations are typically more continuous and reliable.
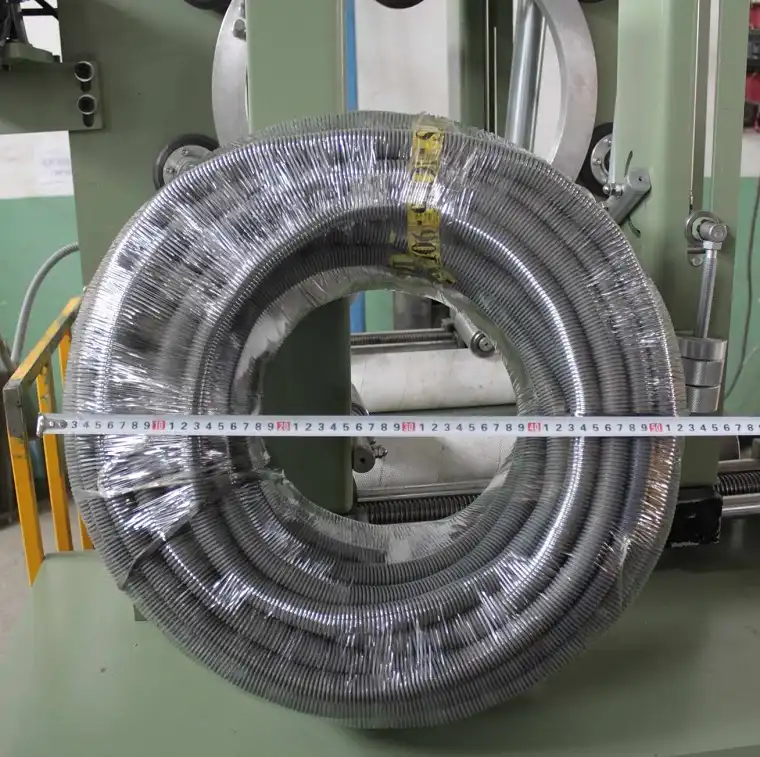
4.3 Improving Ergonomics for Operator Well-being
Beyond reducing acute injury risks, automated coil wrapping improves workplace ergonomics. Traditional wrapping methods frequently require operators to work in uncomfortable positions, involving bending, reaching, twisting, and sustained physical effort, leading to fatigue and long-term strain. Automated systems eliminate most of these strenuous physical demands, allowing operators to oversee the process from ergonomic control stations, reducing physical stress and enhancing comfort.
Better ergonomics contribute to a healthier and more productive workforce. Employees experiencing less physical fatigue and discomfort are typically more alert, focused, and efficient. Prioritizing ergonomic design through automation fosters a work environment where operational efficiency and employee well-being go hand-in-hand.
Conclusion: Why Automated Coil Wrapping Outperforms Traditional Methods
Automated coil wrapping machines deliver a comprehensive suite of advantages that extend well beyond the basic function of packaging. By significantly enhancing operational efficiency, optimizing the use of packaging materials for cost savings, ensuring consistent product protection and quality, and dramatically improving workplace safety, these systems transform coil packaging into a streamlined, reliable, and cost-effective process. When compared directly to traditional manual or semi-automated methods, the benefits of speed, consistency, material efficiency, and safety make automated solutions a superior choice for modern industrial operations.
Investing in a coil wrapping machine represents a strategic commitment to long-term operational excellence. This technology directly supports higher productivity, lower operating costs, superior product quality, and a safer working environment, making it an indispensable tool for companies aiming to maintain competitiveness and efficiency in today's demanding industrial landscape.
Final Assessment: The clear advantages in speed, material savings, wrap consistency, and safety solidify automated coil wrapping machines as a critical investment for operations prioritizing efficiency, reliability, and protection of coiled products.

Get Your Best Solution !