Welding Standards for Positioner Flipping Machines
- Welding Standards for Positioner Flipping Machines
- Introduction
- Importance of Welding Standards in Positioner Flipping Machines
- Key Welding Standards and Parameters for Thin Materials
- Challenges in Welding Thin Materials with Positioner Flipping Machines
- Avoiding Common Defects in Thin Material Welding
- Implementing Effective Welding Standards for Positioner Flipping Machines
- Conclusion
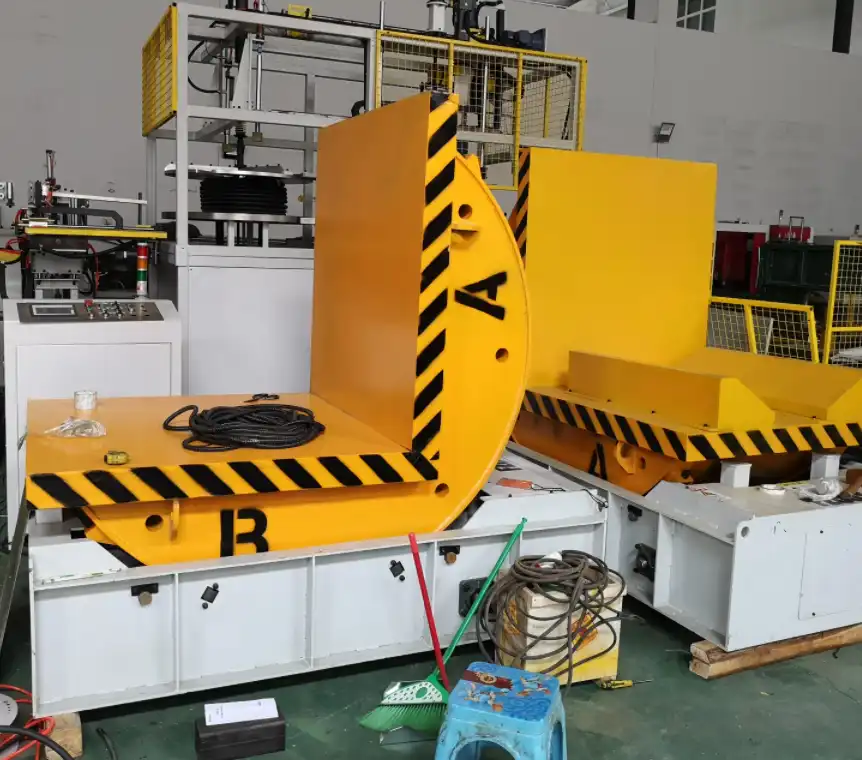
Introduction
The welding standards for a positioner flipping machine are critical in ensuring quality welds and preventing issues such as burn-through, incomplete penetration, and porosity. Selecting the correct welding parameters is essential to avoid these defects, particularly with thin materials, where the margin between adequate penetration and burn-through is narrow. This article explores the essential guidelines for welding standards in positioner flipping machines, discussing current and voltage settings, and the importance of maintaining consistency to achieve stable welds on thin materials.
Importance of Welding Standards in Positioner Flipping Machines
Positioner flipping machines are widely used in welding applications where precise positioning and rotation of the workpiece are necessary for optimal weld access and quality. Properly setting the welding parameters on these machines is crucial. For example, a deviation in welding current or voltage can lead to insufficient penetration, causing weak welds, or excessive heat, resulting in burn-through. These issues compromise the structural integrity of the weld and can lead to costly rework or part rejection.
In automatic welding, where material thickness is around 3 mm, the welding parameters become even more critical. For thin materials, the acceptable range for penetration depth (n1) is limited. When n1 is below 1.5 mm, incomplete penetration occurs, leading to insufficient bonding between welded parts. On the other hand, if the depth exceeds 2.0 mm, burn-through is likely. This tight range of acceptable penetration (less than 1 mm) imposes strict limitations on the welding parameters used with positioner flipping machines.
Key Welding Standards and Parameters for Thin Materials
For optimal results, selecting the correct current and voltage settings based on the type of weld (main seam versus root pass) is essential. This section outlines the welding standards for different wire sizes, specifically focusing on φ1.6 mm wire, and the corresponding current settings.
- Main Seam Welding Current (I1): For the main seam, the welding current is generally set between 160A and 200A. The specific choices are as follows:
- I1 = 160A
- I1 = 180A
- I1 = 200A
- Root Pass Welding Current (I2): For root passes or sealing passes, higher current levels are typically required to ensure full fusion and weld strength. The welding currents for this stage are set at:
- I2 = 220A
- I2 = 240A
- I2 = 260A
- I2 = 280A
When using the initial setting (160A to 200A for the main seam and 220A to 280A for the root pass), it is often challenging to maintain proper fusion without the risk of overlap or burn-through. Hence, careful calibration and consistency in parameter application are crucial.
Challenges in Welding Thin Materials with Positioner Flipping Machines
Welding thin materials, especially 3 mm sheets, requires stringent control of welding parameters due to the narrow threshold between adequate fusion and burn-through. To address this, the following standards and adjustments are critical:
- Stability Requirements: Thin materials demand high stability in welding currents and voltages. Even minor fluctuations can result in defects such as burn-through or incomplete penetration, leading to a degraded weld profile and increased chances of porosity.
- Current and Voltage Control: To achieve consistent quality, current fluctuations should be limited to within ±10A, and voltage fluctuations should remain within ±2V. This narrow range minimizes variations in heat input, ensuring that the weld bead forms uniformly without undercutting or over-penetrating the base material.
- Consistent Heat Input: Uniform heat input is essential for preventing porosity, especially in automatic welding systems where the welding speed is constant. Inconsistent heat can cause gas bubbles to be trapped within the weld, leading to pores and compromising weld integrity.
- Fine Adjustment Mechanisms: Positioner flipping machines should be equipped with fine adjustment mechanisms that allow for precise control over welding parameters. This enables operators to maintain stable welding conditions even with variations in material thickness or composition.
Avoiding Common Defects in Thin Material Welding
Several welding defects commonly arise when the parameters are not meticulously controlled, especially in thin materials. Here are some key issues and solutions:
- Burn-Through: Excessive penetration due to high current or voltage can lead to burn-through. To prevent this, it is essential to keep heat input low while ensuring sufficient fusion. Fine-tuning the welding parameters within the recommended range (e.g., keeping current at the lower end for thin sections) helps avoid this issue.
- Incomplete Penetration: When the welding current or voltage is too low, incomplete penetration may occur, leading to weak joints. To avoid this, ensure that the root pass current (I2) is adequately set to penetrate through the entire thickness of the material without causing burn-through.
- Porosity and Weld Contamination: Porosity is often a result of inconsistent heat input, contamination, or gas trapping within the weld pool. Maintaining stable currents and voltages minimizes these risks. Additionally, using clean, dry shielding gas and ensuring the material is free of oil or contaminants can significantly reduce porosity.
Implementing Effective Welding Standards for Positioner Flipping Machines
Manufacturers and operators can achieve optimal welding outcomes by adhering to standardized guidelines, particularly in applications involving thin materials. Below are recommended practices:
- Parameter Testing and Calibration: Conducting test welds to determine the ideal parameters for each application is essential. During testing, record the optimal current, voltage, and travel speed that produce the desired penetration and bead profile without defects.
- Monitoring and Automation: Positioner flipping machines should include monitoring systems that automatically adjust welding parameters based on real-time feedback from sensors. This capability is especially useful for applications involving variable thicknesses, where adjusting parameters mid-weld can prevent defects.
- Regular Maintenance of Equipment: Proper maintenance of the welding equipment, including the positioner flipping machine, helps ensure that current and voltage fluctuations remain within acceptable ranges. Calibrating the machine regularly can prevent unexpected deviations in welding parameters, ensuring consistency in weld quality.
Conclusion
Welding standards for positioner flipping machines are essential for achieving high-quality welds, especially in applications involving thin materials. By maintaining strict control over welding parameters, manufacturers can prevent common issues such as burn-through, incomplete penetration, and porosity. Adopting standardized guidelines for current and voltage settings, along with regular calibration and maintenance, ensures that welding outcomes meet industry standards for strength and durability. As automation in welding continues to evolve, maintaining precision in these standards will be increasingly vital to achieving efficient, defect-free welding in industrial applications.

Get Your Best Solution !