Understanding Mold Rotator Technical Specifications and Evaluating Investment Payback
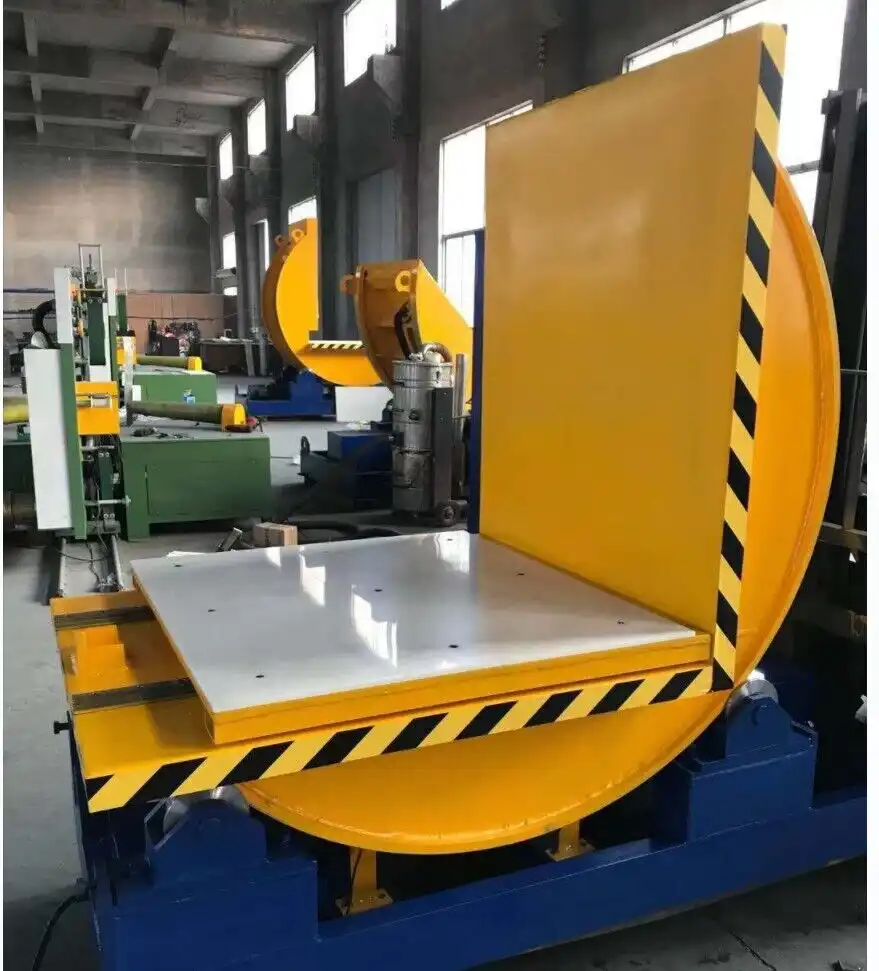
In today's competitive manufacturing landscape, optimizing production processes is crucial. For industries relying on heavy molds—such as automotive, plastics injection molding, die casting, and aerospace—equipment like mold rotators are indispensable. These machines streamline the safe movement, rotation, and precise positioning of large molds, significantly improving operational safety, reducing manual labor, and boosting overall productivity.
However, investing in a mold rotator requires careful consideration. Understanding the key technical specifications is essential to selecting the right machine for your needs. Furthermore, evaluating the payback period and return on investment (ROI) ensures the purchase aligns with your business goals. This guide delves into the critical technical aspects of mold rotators, explains how to assess their financial viability, and helps you make an informed investment decision.
1. What is a Mold Rotator and Why is it Essential?
A mold rotator, often referred to as a mold tilter or mold flipper, is specialized industrial equipment designed to safely rotate heavy and cumbersome molds. Handling these molds manually is often impractical and poses significant safety risks. Mold rotators are vital in manufacturing environments where precise mold orientation is necessary for maintenance, cleaning, or production processes.
Key benefits of integrating mold rotators include:
- Improved Workplace Safety: Automating the lifting and rotation of multi-ton molds drastically reduces the risk of musculoskeletal injuries and accidents associated with manual handling. This aligns with promoting safer work environments as emphasized by organizations like OSHA.
- Enhanced Productivity: Faster, automated mold rotation cycles shorten changeover times and reduce production downtime, leading to increased throughput and operational efficiency.
- Reduced Labor Costs: Automating the mold handling process minimizes the need for manual labor, freeing up personnel for other value-added tasks and lowering operational expenses.
- Mold Protection: Gentle, controlled rotation minimizes the risk of damage to expensive molds during handling.
upender and tilter with sliding table 2. Key Technical Specifications of Mold Rotators
Choosing the appropriate mold rotator hinges on understanding its technical specifications. Evaluate these key parameters carefully:
a) Load Capacity
This specifies the maximum weight the mold rotator can safely lift and rotate. Capacities vary widely, typically ranging from 1 ton to over 50 tons.
- Consideration: Always select a rotator with a load capacity exceeding the weight of your heaviest mold, including any attached components. Incorporating a safety margin is crucial to prevent equipment failure and ensure operator safety.
b) Rotation Speed
Rotation speed determines how quickly the mold can be turned. Many modern rotators feature variable speed drives (VSDs) allowing operators to adjust the speed for optimal efficiency and safety.
- Consideration: Faster speeds can improve cycle times, but slower, controlled speeds might be necessary for delicate or complex molds to prevent damage.
c) Rotation Angle
This defines the degree to which the mold can be rotated. Common configurations include:
- 90-degree rotation: Often sufficient for maintenance access or specific positioning tasks.
- 180-degree rotation: Ideal for completely inverting molds (flipping).
- 360-degree rotation: Offers maximum flexibility for complex positioning or multi-sided access requirements.
- Consideration: Select the rotation angle that best matches the requirements of your specific mold handling tasks and workflow.
d) Control System
Modern mold rotators utilize sophisticated control systems for precise operation. Features often include:
- PLC (Programmable Logic Controller): For automated sequences and reliable operation.
- HMI (Human-Machine Interface): Touch screens or panels for easy parameter setting and monitoring.
- Remote Pendant/Control: Allows operators to manage rotation from a safe distance.
- Programmable Settings: Pre-set rotation angles and speeds enhance consistency and reduce potential for human error.
- Consideration: Evaluate the user-friendliness and the level of automation needed for your application.
e) Power Source
Mold rotators are typically powered by hydraulic or electric systems:
- Hydraulic Systems: Offer high power density, making them suitable for extremely heavy loads. They require hydraulic fluid maintenance.
- Electric Systems: Generally quieter, more energy-efficient, and require less maintenance (no fluid checks/leaks). Often preferred for cleaner environments.
- Pneumatic Systems: Less common, used in specific environments where compressed air is readily available and preferred.
- Consideration: Choose based on load requirements, available utilities, maintenance preferences, and environmental considerations (noise, potential leaks).
f) Machine Dimensions and Footprint
The physical size and the floor space required by the mold rotator are critical logistical factors.
- Consideration: Ensure the machine fits within your available production area and integrates smoothly with existing workflows, including crane access or forklift paths if necessary.
g) Safety Features
Safety is paramount when handling heavy loads. Key safety features include:
- Emergency Stops (E-stops): Easily accessible buttons to halt operation instantly.
- Overload Protection: Prevents operation if the load exceeds the rated capacity.
- Safety Guards/Fencing: Physical barriers to restrict access during operation.
- Interlocks: Sensors that prevent operation if guards are open or conditions are unsafe.
- Stable Base/Mounting: Ensures the machine remains secure during rotation.
- Consideration: Verify the rotator meets relevant safety standards and includes robust safety mechanisms.
3. Evaluating the Payback Period for a Mold Rotator Investment
Beyond technical suitability, assessing the financial viability is crucial. The payback period estimates the time required for the financial benefits (savings and revenue) generated by the mold rotator to offset its initial cost.
a) Initial Investment Cost
This includes not only the purchase price of the machine but also:
- Delivery and Installation: Costs associated with shipping and setting up the equipment.
- Training: Ensuring operators can use the machine safely and efficiently.
- Facility Modifications: Potential changes needed for power supply, floor reinforcement, or integration.
b) Operational Savings
Mold rotators generate significant ROI through various savings:
- Labor Cost Reduction: Fewer personnel required for mold handling tasks; redeployment of staff to higher-value activities.
- Reduced Injury Costs: Lower frequency of workplace injuries translates to savings on medical expenses, workers' compensation claims, insurance premiums, and lost workdays.
- Decreased Mold Damage: Automated, controlled handling minimizes costly repairs or replacements of valuable molds.
- Lower Maintenance Costs: Compared to manual methods or less efficient equipment.
c) Increased Production Efficiency
Faster and more reliable mold handling directly impacts the bottom line:
- Reduced Downtime: Quicker mold changes and maintenance access lead to more uptime for production machinery.
- Increased Throughput: More efficient workflow allows for higher production volumes within the same timeframe.
- Improved Consistency: Automated positioning ensures repeatable accuracy.
d) Tax Considerations
In some jurisdictions, investments in automation and safety equipment like mold rotators may qualify for tax deductions or incentives (e.g., depreciation allowances).
- Action: Consult with financial advisors or tax professionals to understand applicable benefits in your region.
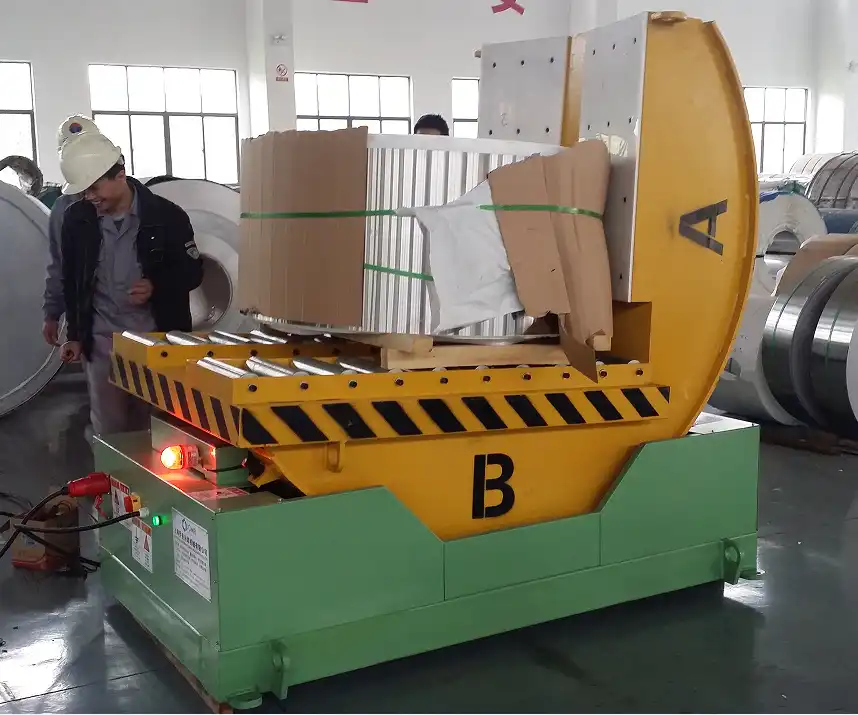
4. Factors Influencing the Payback Period
The actual payback period for a mold rotator investment varies based on several operational factors:
- Frequency of Use: Higher utilization rates lead to faster accumulation of savings and a shorter payback period.
- Current Labor Costs: Facilities with high manual labor costs for mold handling will see more substantial savings.
- Production Volume: High-volume operations benefit significantly from efficiency gains.
- Cost of Workplace Injuries: Environments with a history of handling-related injuries will realize faster payback through injury reduction.
- Mold Value and Complexity: Preventing damage to expensive or intricate molds provides significant cost avoidance.
- Maintenance Costs: Comparing the rotator's maintenance needs versus the upkeep of previous methods.
5. Calculating the Payback Period
A simple formula provides an initial estimate:
Payback Period (in years) = Initial Investment Cost / Annual Net Savings
Where:
- Initial Investment Cost: Total upfront cost (purchase, installation, training, etc.).
- Annual Net Savings: The total quantifiable financial benefits per year. This includes:
- Labor cost savings
- Savings from reduced injuries
- Cost avoidance from preventing mold damage
- Value of increased production/reduced downtime
- Minus any new annual operating/maintenance costs for the rotator.
Example: If a mold rotator has a total initial investment cost of $50,000 and generates combined annual net savings (labor reduction, injury prevention, efficiency gains) of $15,000, the simple payback period is: $50,000 / $15,000/year = 3.33 years
Note: This simple calculation doesn't account for factors like the time value of money or potential tax benefits, which can be included in more detailed ROI analyses.
6. Real-World ROI Examples
Case Summary 1: Automotive Supplier
- Challenge: Frequent injuries and production delays due to manual rotation of heavy casting molds.
- Solution: Invested in a high-capacity mold rotator.
- Outcome: Achieved a 30% increase in production efficiency and drastically reduced workplace injury incidents. The investment paid for itself in approximately two years through combined savings and productivity gains.
Case Summary 2: Plastic Injection Molding Facility
- Challenge: Production bottlenecks and mold damage resulting from difficult manual handling of large molds.
- Solution: Implemented a 20-ton capacity mold rotator with 180-degree rotation.
- Outcome: Eliminated hazardous manual handling, reduced production downtime by 25%, and minimized mold repair costs. The ROI was realized within three years.
coil upenders 7. Conclusion
Investing in a mold rotator is a strategic decision that enhances workplace safety, streamlines production, and ultimately improves profitability. By thoroughly understanding the essential technical specifications—such as load capacity, rotation angle, control systems, and safety features—you can select a machine precisely tailored to your operational needs.
Furthermore, conducting a careful evaluation of the payback period, considering factors like initial costs, operational savings, and efficiency improvements, ensures the investment aligns with your financial objectives. A well-chosen mold rotator delivers immediate benefits in safety and efficiency and provides sustained value long after the initial costs are recovered, making it a vital asset for modern manufacturing facilities handling heavy molds.

Get Your Best Solution !