Top Innovations to Consider When Choosing a Steel Coil Packing Line
- Top Innovations to Consider When Choosing a Steel Coil Packing Line
- Introduction
- 1. Automation: The Backbone of Modern Steel Coil Packing Lines
- 2. IoT Integration for Real-Time Monitoring and Optimization
- 3. Customizable Wrapping Solutions
- 4. Advanced Strapping Technologies
- 5. Robotic Palletizing for Efficiency and Safety
- 6. Modular Designs for Scalability and Flexibility
- 7. Energy Efficiency and Sustainability
- 8. Real-Time Data Analytics for Continuous Improvement
- 9. Enhanced Safety Features
- 10. Predictive Maintenance for Reduced Downtime
- 11. User-Friendly Interfaces and Control Systems
- 12. Integration with Existing Production Systems
- 13. Sustainability and Eco-Friendly Technologies
- 14. High-Speed Packaging for Maximum Throughput
- 15. Choosing the Right Manufacturer
- Conclusion
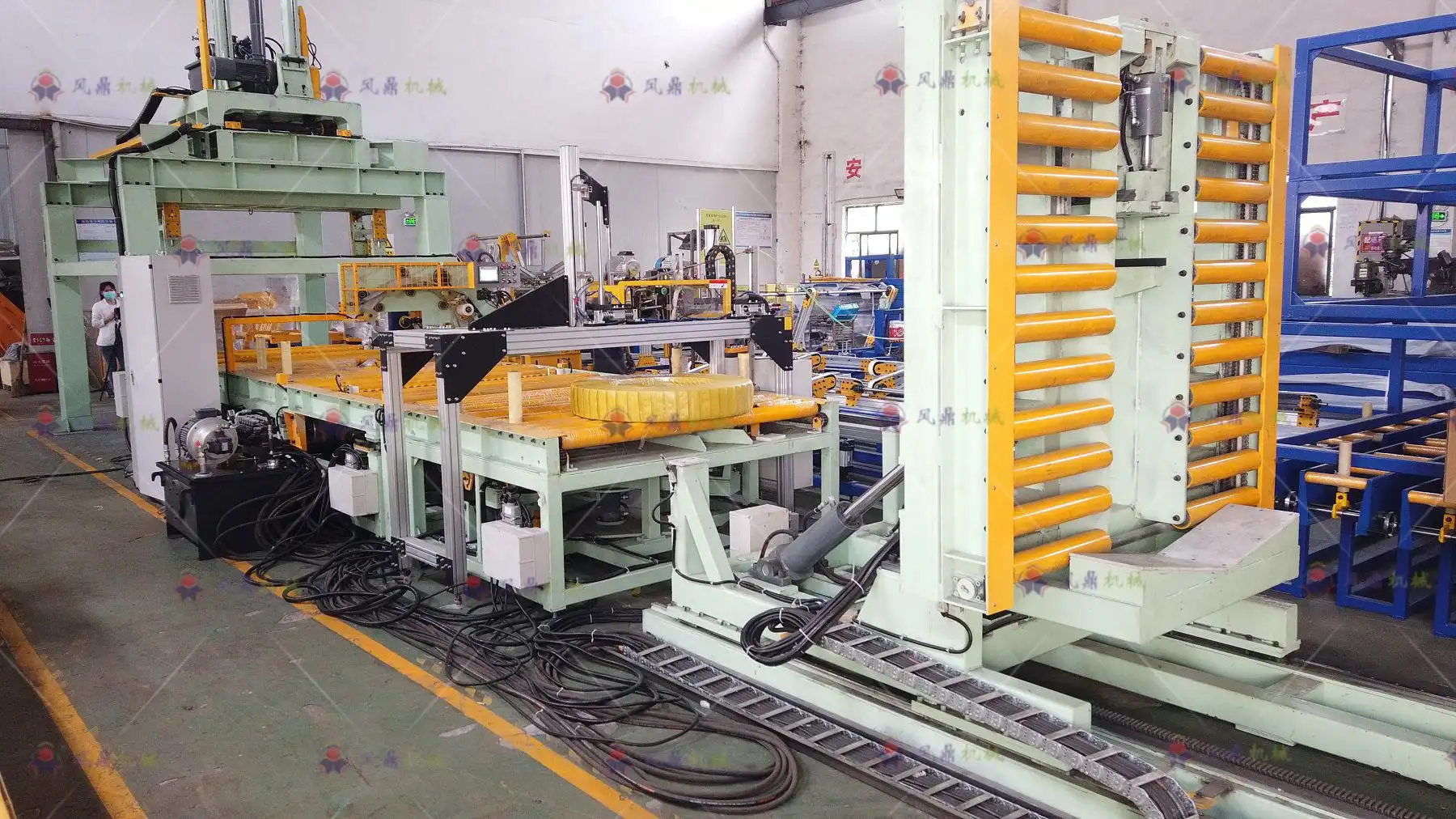
Introduction
In the steel industry, packaging plays a crucial role in protecting valuable steel coils during transportation and storage. With advancements in technology, steel coil packing lines have evolved to become more efficient, precise, and sustainable. For manufacturers looking to upgrade their operations or improve the quality of their packaging process, understanding the latest innovations in steel coil packing lines is essential.
Choosing the right packing line can significantly impact your production speed, packaging quality, labor costs, and material usage. By embracing cutting-edge technologies, companies can reduce downtime, enhance safety, and ensure that their coils are protected from damage. In this article, we will explore the top innovations to consider when selecting a steel coil packing line, focusing on features that offer long-term value and operational efficiency.
1. Automation: The Backbone of Modern Steel Coil Packing Lines
Why Automation is Critical
Automation is at the heart of modern steel coil packing lines. By automating key steps such as wrapping, strapping, and palletizing, companies can achieve faster production rates while reducing the need for manual labor. This not only improves productivity but also enhances consistency in packaging quality.
Automated packing lines are equipped with sensors, robotic arms, and programmable logic controllers (PLCs) that allow for precise control over every aspect of the packaging process. These systems can adjust parameters like wrapping tension and material usage automatically, ensuring that each coil is packaged according to specific requirements without manual intervention.
Benefits of Automation in Coil Packaging
- Increased Efficiency: Automated systems work faster than manual labor, allowing for higher throughput and shorter production cycles.
- Reduced Human Error: Automation eliminates the inconsistencies associated with manual packaging, ensuring that every coil is wrapped and strapped to the same standard.
- Lower Labor Costs: By reducing the need for manual operators, automated systems can help manufacturers cut labor costs and allocate resources to other areas of the operation.
2. IoT Integration for Real-Time Monitoring and Optimization
The Role of IoT in Modern Packaging Lines
The Internet of Things (IoT) is transforming the way manufacturers manage their operations. In steel coil packing lines, IoT integration allows machines and systems to communicate with each other and provide real-time data on performance, material usage, and potential maintenance needs. This data-driven approach enables manufacturers to make informed decisions that improve efficiency and reduce downtime.
Key Benefits of IoT Integration
- Real-Time Monitoring: IoT sensors collect data from various points in the packing line, allowing operators to monitor performance in real time. This ensures that any issues are identified and addressed before they cause major disruptions.
- Predictive Maintenance: By analyzing data on equipment performance, IoT systems can predict when components are likely to fail, allowing for timely maintenance. This reduces unplanned downtime and extends the life of the equipment.
- Enhanced Efficiency: IoT-enabled systems can adjust their operations based on real-time data, optimizing material usage and improving overall efficiency. This leads to significant cost savings over time.
3. Customizable Wrapping Solutions
Flexible Wrapping for Different Coil Sizes
Steel coils come in various sizes and shapes, and the ability to customize wrapping solutions for each coil is crucial for ensuring optimal protection. Modern steel coil packing lines are equipped with customizable wrapping systems that can adjust the amount of film, wrapping tension, and wrapping speed based on the specific dimensions of the coil.
This flexibility ensures that every coil is wrapped securely, whether it is a small, lightweight coil or a large, heavy one. By tailoring the wrapping process to each coil, manufacturers can reduce material waste and improve packaging consistency.
Wrapping Materials for Enhanced Protection
In addition to flexibility in the wrapping process, modern systems also support the use of various wrapping materials. These include:
- Stretch Film: Ideal for securing coils for short-term storage or transportation.
- VCI (Vapor Corrosion Inhibitor) Film: Used to prevent rust and corrosion, especially for coils stored in humid environments.
- Heavy-Duty Film: Provides extra protection for large or heavy coils that require additional support during transport.
By offering a range of material options, manufacturers can ensure that their packaging is tailored to the specific needs of their products.
4. Advanced Strapping Technologies
Automated Strapping Systems
Strapping is a critical step in securing steel coils for transportation, and automated strapping systems offer significant advantages over manual processes. Automated systems apply straps with precise tension, ensuring that each coil is tightly secured without damaging the material. These systems can also adjust the number of straps and the positioning based on coil size, providing flexibility and accuracy.
Benefits of Advanced Strapping
- Consistency: Automated strapping ensures that each coil is secured with the same level of tension and precision, reducing the risk of product damage.
- Speed: Automated systems can strap coils much faster than manual methods, increasing production speed and reducing bottlenecks.
- Material Efficiency: By optimizing strap usage, advanced strapping systems minimize waste and reduce material costs.

Get Your Best Solution !
5. Robotic Palletizing for Efficiency and Safety
The Role of Robotics in Palletizing
In modern steel coil packing lines, robotic palletizing has become a game-changer for both efficiency and safety. Palletizing is a labor-intensive process, especially when dealing with heavy steel coils. Robotics can automate this process, stacking coils on pallets with precision and speed, reducing the need for manual handling.
Benefits of Robotic Palletizing
- Increased Throughput: Robotic palletizers can handle large volumes of coils quickly, speeding up the packaging process and increasing overall throughput.
- Enhanced Safety: By automating the lifting and stacking of heavy coils, robotic palletizers reduce the risk of workplace injuries caused by manual lifting.
- Accuracy: Robotic systems can stack coils with greater precision than manual labor, ensuring that pallets are stable and coils are properly aligned for transport.
6. Modular Designs for Scalability and Flexibility
The Importance of Scalability
As production demands grow, manufacturers need packing lines that can scale with their operations. Modular coil packing lines are designed with scalability in mind, allowing manufacturers to start with a basic system and add advanced features as their needs evolve. This flexibility ensures that the packing line remains efficient and cost-effective, even as production volumes increase.
Customization and Upgrades
Modular designs also offer the advantage of customization. Manufacturers can tailor their packing lines to specific operational requirements, such as coil size, production speed, and packaging materials. Additionally, modular systems can be upgraded with new technologies—such as IoT sensors or robotic palletizers—without the need for a complete system overhaul.
7. Energy Efficiency and Sustainability
Reducing Energy Consumption
As manufacturers look for ways to reduce their environmental impact, energy efficiency has become a key consideration in selecting a steel coil packing line. Modern packing lines are designed to use less energy without compromising performance. Energy-efficient motors, optimized workflows, and intelligent automation systems all contribute to reducing the overall energy consumption of the packaging process.
Sustainable Packaging Materials
In addition to energy efficiency, many steel coil packing lines are now designed to support the use of sustainable packaging materials. These include recyclable or biodegradable films and straps, which help reduce the environmental footprint of the packaging process. By adopting sustainable materials, manufacturers can meet growing consumer demand for eco-friendly packaging and align their operations with global sustainability initiatives.
8. Real-Time Data Analytics for Continuous Improvement
The Role of Data in Optimizing Packaging
Data is one of the most valuable resources in modern manufacturing, and real-time data analytics allows companies to continuously improve their packaging processes. By collecting and analyzing data on machine performance, material usage, and production output, manufacturers can identify inefficiencies and make informed decisions to optimize their operations.
Benefits of Real-Time Data Analytics
- Improved Decision Making: Data analytics provides insights into how the packing line is performing, allowing operators to adjust settings and improve efficiency.
- Cost Savings: By identifying areas where materials are being wasted or machines are not running at optimal capacity, manufacturers can reduce costs and improve overall profitability.
- Continuous Improvement: Real-time data enables a cycle of continuous improvement, where manufacturers can monitor performance, make adjustments, and track the results in real time.
9. Enhanced Safety Features
Safety as a Top Priority
Worker safety is a top priority in any manufacturing operation, and modern steel coil packing lines are equipped with advanced safety features to protect workers from injury. These features include emergency stop buttons, safety guards, and sensors that detect when workers are too close to moving parts.
Automated Safety Systems
Some packing lines also feature automated safety systems that shut down the machine if a safety issue is detected. These systems are designed to prevent accidents and ensure that workers can operate the equipment safely. By investing in systems with robust safety features, manufacturers can reduce the risk of workplace accidents and improve overall safety compliance.
10. Predictive Maintenance for Reduced Downtime
How Predictive Maintenance Works
One of the most powerful innovations in modern steel coil packing lines is predictive maintenance. By using sensors and IoT technology, predictive maintenance systems can monitor the condition of machinery in real time. These systems analyze data such as vibration levels, temperature, and operational efficiency to detect early signs of wear or malfunction.
Predictive maintenance allows manufacturers to schedule repairs or part replacements before a breakdown occurs, reducing the risk of unexpected downtime and extending the life of the equipment.
Benefits of Predictive Maintenance
- Minimized Downtime: Predictive maintenance reduces the likelihood of unplanned downtime by addressing potential issues before they lead to machine failure.
- Cost Savings: By avoiding emergency repairs and preventing breakdowns, manufacturers can save on costly downtime and avoid expensive part replacements.
- Longer Equipment Lifespan: Regular maintenance based on predictive data ensures that equipment operates at optimal performance, extending the overall lifespan of the machinery.
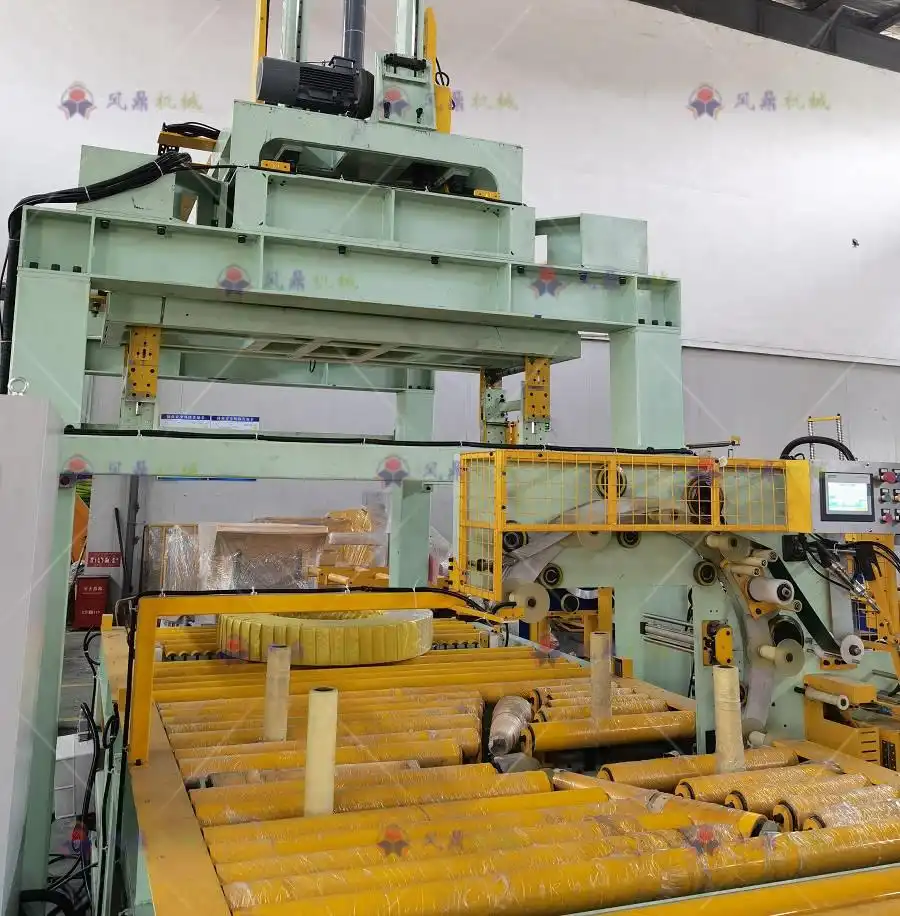
11. User-Friendly Interfaces and Control Systems
Intuitive User Interfaces
Operating a complex steel coil packing line requires precision and control, and modern systems are equipped with user-friendly interfaces that make it easy for operators to manage the entire process. Touchscreen controls, intuitive software, and clear visual displays provide operators with real-time information on the status of the packing line, material usage, and machine performance.
Remote Monitoring and Control
Many advanced systems also feature remote monitoring and control capabilities. This allows operators to manage the packing line from a distance, whether through a mobile device or a desktop computer. Remote access provides flexibility and convenience, enabling operators to make adjustments or troubleshoot issues without being physically present at the machine.
Customizable Settings
In addition to intuitive controls, modern packing lines offer customizable settings that allow operators to adjust parameters based on the specific needs of the production line. Whether it’s modifying the wrapping tension, adjusting strapping strength, or selecting the type of packaging material, these customizable options ensure that the system can be tailored to each coil’s requirements.
12. Integration with Existing Production Systems
Seamless System Integration
For many manufacturers, one of the key considerations when selecting a steel coil packing line is how well it integrates with existing production systems. A well-integrated system streamlines the workflow, ensuring that packaging operations are in sync with other manufacturing processes such as coil production, quality control, and inventory management.
By integrating the coil packing line with other Enterprise Resource Planning (ERP) systems, manufacturers can achieve a seamless flow of data across the entire production chain. This ensures real-time tracking of coil packaging, enhances communication between departments, and improves overall operational efficiency.
Enhancing Workflow Efficiency
System integration improves workflow efficiency by automating data transfer between systems, eliminating the need for manual data entry and reducing the risk of errors. For example, when a coil is wrapped and strapped, the system can automatically update the inventory records, generate shipping labels, and schedule transportation—all without human intervention. This level of integration ensures that packaging is not a bottleneck in the production process.
13. Sustainability and Eco-Friendly Technologies
Reducing Environmental Impact
As sustainability becomes a growing concern for manufacturers worldwide, many steel coil packing lines are being designed with eco-friendly features. This includes using energy-efficient motors, reducing packaging material waste, and supporting the use of recyclable or biodegradable materials.
By investing in a sustainable packaging line, manufacturers can minimize their environmental impact, reduce costs, and align their operations with global sustainability goals. Additionally, adopting green packaging practices can enhance a company’s brand reputation, especially among environmentally conscious customers.
Energy-Efficient Operations
Energy-efficient systems are designed to minimize power consumption while maintaining high levels of performance. Features such as automatic shut-off during idle periods, optimized motor designs, and efficient material handling can significantly reduce the overall energy usage of the packing line. This not only helps reduce operating costs but also lowers the carbon footprint of the packaging process.

Get Your Best Solution !
14. High-Speed Packaging for Maximum Throughput
Increasing Production Speeds
For manufacturers handling large volumes of steel coils, high-speed packaging systems are essential for maximizing throughput. Modern coil wrapping lines are capable of handling multiple coils per minute, ensuring that packaging does not become a bottleneck in the production process.
High-speed systems are equipped with features such as dual wrapping stations and automated palletizers, which allow multiple coils to be processed simultaneously. These systems maintain high levels of precision and consistency, even at fast speeds, ensuring that each coil is packaged securely.
Benefits of High-Speed Systems
- Increased Productivity: High-speed systems enable manufacturers to process more coils in less time, helping them meet tight production schedules and increase overall output.
- Reduced Labor Costs: By automating the packaging process, high-speed systems reduce the need for manual labor, allowing companies to reallocate workers to other tasks.
- Improved Packaging Consistency: Even at fast speeds, these systems deliver consistent results, ensuring that each coil is packaged to the same high standard.
15. Choosing the Right Manufacturer
Evaluating Experience and Expertise
When choosing a steel coil packing line, it’s important to select a manufacturer with a proven track record of delivering reliable and innovative solutions. Look for manufacturers that specialize in automated packaging systems for the steel industry, and evaluate their experience in designing and installing systems for similar operations.
Customization and Support
The best manufacturers offer customizable solutions that can be tailored to meet the specific needs of your operation. Whether you require a system that handles large coils, supports multiple packaging materials, or integrates with existing production systems, customization is key to ensuring that the packing line delivers maximum value.
Additionally, consider the level of support offered by the manufacturer. From installation and training to ongoing maintenance and technical support, a strong partnership with the manufacturer can ensure that your packing line operates efficiently and remains up-to-date with the latest innovations.
Conclusion
Investing in a steel coil packing line equipped with the latest innovations can have a transformative effect on your operation. From automation and IoT integration to robotic palletizing and predictive maintenance, the technologies discussed in this article offer significant benefits in terms of efficiency, cost savings, and packaging quality.
By understanding the top innovations available, manufacturers can make informed decisions that improve their production speed, reduce material waste, and enhance product protection. Whether you’re looking to scale up your operations or simply improve the efficiency of your packaging process, choosing the right coil packing line with the most advanced features will help you stay competitive in a rapidly evolving industry.
With innovations like customizable wrapping, high-speed systems, and eco-friendly materials, today’s coil packing lines are designed to meet the demands of modern manufacturing while reducing environmental impact. As you evaluate your options, consider these key innovations to ensure that your investment delivers long-term value and operational success.

Get Your Best Solution !