Choosing the Right Pallet Inverter: A Guide to Essential Features
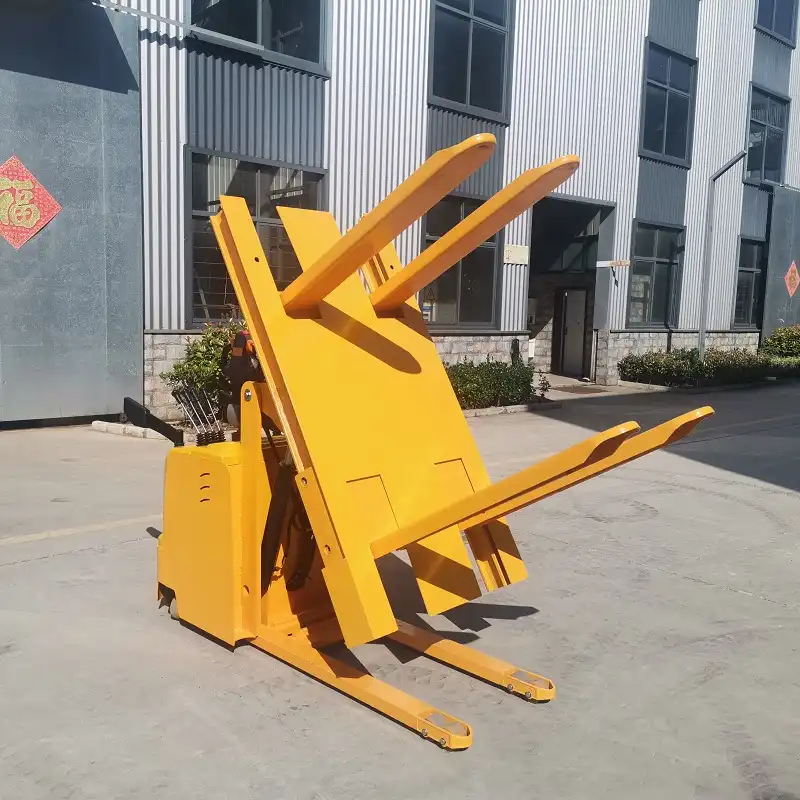
In modern logistics, distribution, and manufacturing environments, efficiency and safety are paramount. The pallet inverter has emerged as a vital piece of material handling equipment, enabling operations to quickly and safely invert, transfer, or exchange palletized loads. Common applications include swapping loads to hygienic plastic pallets, recovering damaged goods from the bottom of a stack, or replacing broken wooden pallets without manual restacking.
Choosing the right pallet inverter, however, requires careful consideration of your specific operational needs. Pallet inverters come in various configurations, including free-standing, mobile, and inline automated systems. This guide explores the key features to evaluate when selecting a pallet inverter, helping you make an informed investment that enhances productivity and safety in your facility.
1. Load Capacity and Load Handling Versatility
One of the first specifications to verify is the load capacity. Pallet inverters typically handle loads ranging from 1,000 kg (approx. 2,200 lbs) to 2,000 kg (approx. 4,400 lbs) or more. It's crucial to select a model rated significantly above the heaviest load you anticipate handling regularly. Overloading equipment can lead to premature wear, failure, and potential safety hazards.
Beyond just weight, consider the dimensions and characteristics of your typical loads:
- Size: Can the inverter accommodate your pallet footprint (e.g., standard GMA, CHEP, Euro pallets) and load height? Check the machine's opening range.
- Type: Are your loads stable boxes, fragile goods, uneven sacks, or liquid containers? This impacts the required clamping system (see section 3).
- Pallet Type: Will you be handling wood, plastic, or metal pallets? Some clamp designs work better with specific pallet types.
Investing in a versatile model capable of handling various load sizes, weights, and types ensures the pallet inverter remains effective even as your operational needs evolve.
Why it Matters:
Selecting an inverter with the appropriate load capacity and handling versatility prevents equipment strain, minimizes the risk of load damage or accidents, and ensures reliable performance for all your required tasks, safeguarding both efficiency and operational safety.
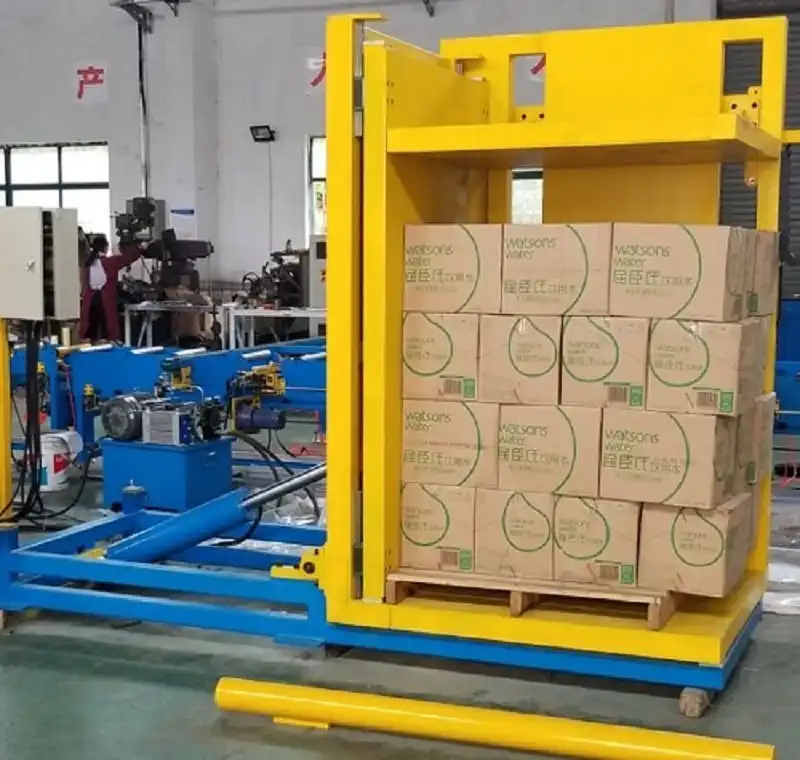
2. Rotation Angle and Method
The primary function of a pallet inverter is rotation. Most standard models offer 180-degree rotation. This is ideal for:
- Exchanging a load from one pallet to another (e.g., wood to plastic).
- Replacing a broken pallet at the bottom of a stack.
- Inverting products for processing or storage requirements.
Some applications might benefit from a 90-degree rotation feature, often found on specialized tilters or certain inverter models. This allows access to the side or bottom of a load, which can be useful for tasks like:
- Layer picking or inspection.
- Transferring goods between different handling equipment.
Consider how the rotation is achieved. Most inverters use hydraulic or electric systems for smooth, controlled movement. Dual-clamp systems, which clamp both the top and bottom of the load independently before rotation, offer enhanced stability for tall or unstable loads.
Why it Matters:
Matching the rotation angle and method to your primary tasks ensures operational efficiency. A standard 180-degree inverter suits most pallet exchange needs, while a 90-degree option might be necessary for specific access requirements, optimizing workflow and potentially cycle time.
3. Clamp System Design and Pressure Control
The clamp system secures the load during the inversion cycle. Its design is critical for preventing product damage, especially with fragile or unevenly packed goods. Key considerations include:
- Actuation Method:
- Hydraulic Clamps: Offer high clamping force and precise pressure control, making them ideal for heavy loads and delicate products. Pressure can often be adjusted to suit different load types.
- Pneumatic Clamps: Generally faster actuation, often used in automated systems. Pressure control might be less precise than hydraulic systems.
- Manual Clamps: Found on simpler, lower-cost units, requiring operator effort. Suitable for lighter, more robust loads.
- Clamp Surface: Look for non-slip, non-damaging surfaces, such as rubber lining, to protect packaging.
- Pressure Adjustment: The ability to easily adjust clamping pressure is vital to avoid crushing sensitive goods while ensuring heavier loads are held securely.
Why it Matters:
An inadequate or poorly adjusted clamp system can lead to significant product damage, costly waste, and operational delays. Choosing a system appropriate for your load types, with adjustable pressure control, is essential for secure and damage-free handling.

Get Your Best Solution !
Editor's Note: Please check the content of reusable block 16995. If it contains YouTube video links, ensure they are converted to the iframe format specified in the instructions.
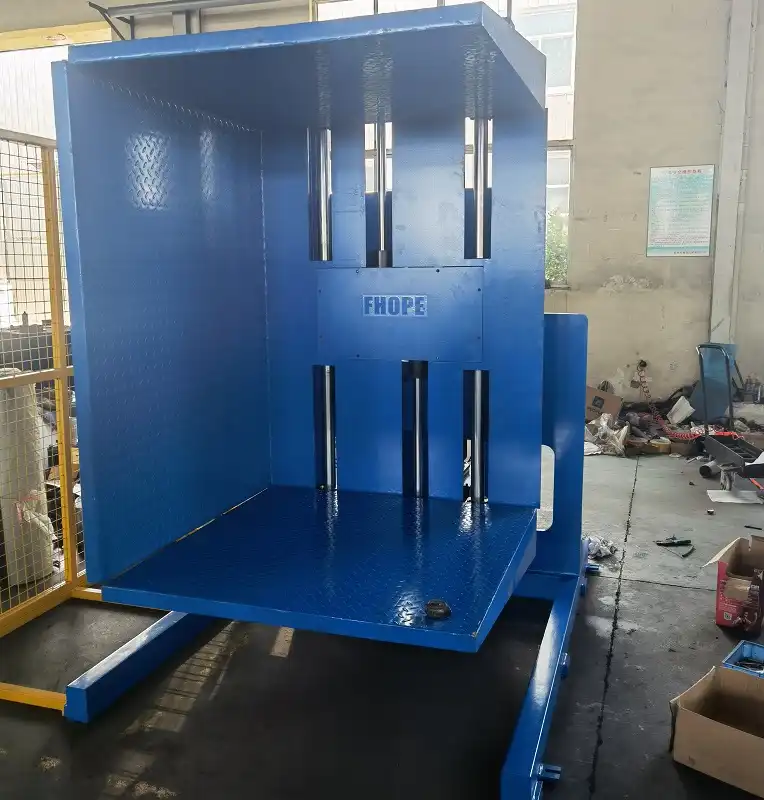
4. Essential Safety Features
Given the forces and movement involved, safety features are non-negotiable. A well-designed pallet inverter should protect operators and the surrounding workspace. Look for:
- Physical Guarding: Safety cages or fencing with interlocking gates that stop machine operation if opened during a cycle.
- Presence Sensing: Light curtains or area scanners that detect personnel entry into the operating zone and trigger a safe stop.
- Emergency Stop Buttons: Easily accessible E-stops to halt operation immediately in case of malfunction or hazard.
- Hydraulic Safety: Pressure relief valves to prevent over-pressurization in hydraulic clamp and rotation systems.
- Controlled Operation: Smooth, predictable rotation speed and secure clamping before inversion begins.
- Clear Markings & Warnings: Visible safety labels and instructions.
Compliance with relevant safety standards (e.g., CE marking in Europe) indicates adherence to recognized safety protocols.
Why it Matters:
Prioritizing pallet inverter safety features is crucial for preventing workplace accidents and protecting personnel. Robust safety systems minimize operational risks, reduce potential downtime, and contribute to a safer working environment, which is fundamental for any material handling operation.
5. Automation Level and Ease of Use
Pallet inverters range from manually loaded, push-button activated units to fully automated systems integrated into conveyor lines. Consider:
- Manual/Semi-Automatic: Operator uses a forklift or pallet jack to load/unload the inverter; rotation is typically activated via push-button controls. Suitable for lower throughput applications.
- Fully Automatic: Integrated with conveyors for automatic loading, inversion, and unloading. Ideal for high-volume operations, minimizing manual handling and labor requirements.
Regardless of the automation level, ease of use is important. Look for:
- Intuitive Controls: Simple, clearly labeled buttons or a user-friendly HMI (Human-Machine Interface), possibly with a touchscreen.
- Programmable Settings: Ability to save parameters (like clamp pressure) for different load types can improve consistency and reduce setup time.
- Clear Diagnostics: Error messages or status indicators help troubleshoot issues quickly.
Why it Matters:
An appropriate level of automation and an intuitive interface streamline operations, reduce operator training time, minimize errors, and can significantly cut labor costs in high-throughput scenarios. Matching the machine's complexity to your workforce skills and operational volume is key.
6. Durability, Build Quality, and Support
A pallet inverter is a significant investment expected to provide years of reliable service. Evaluate its durability and build quality:
- Construction: Look for a robust frame made from heavy-gauge steel. Quality welding and construction techniques are essential.
- Components: High-quality motors, hydraulics, bearings, and electrical components contribute to longevity and reduce breakdowns.
- Finish: A durable powder coat or paint finish protects against corrosion in industrial environments.
- Maintenance Access: Ensure key components are reasonably accessible for routine inspection and maintenance.
Consider the manufacturer's reputation, warranty coverage, and the availability of after-sales support, including spare parts and qualified service technicians.
Why it Matters:
Investing in a durable, well-built pallet inverter minimizes downtime due to equipment failure and reduces long-term repair costs. Good manufacturer support ensures you can keep the machine running efficiently for its entire lifespan, maximizing your return on investment.
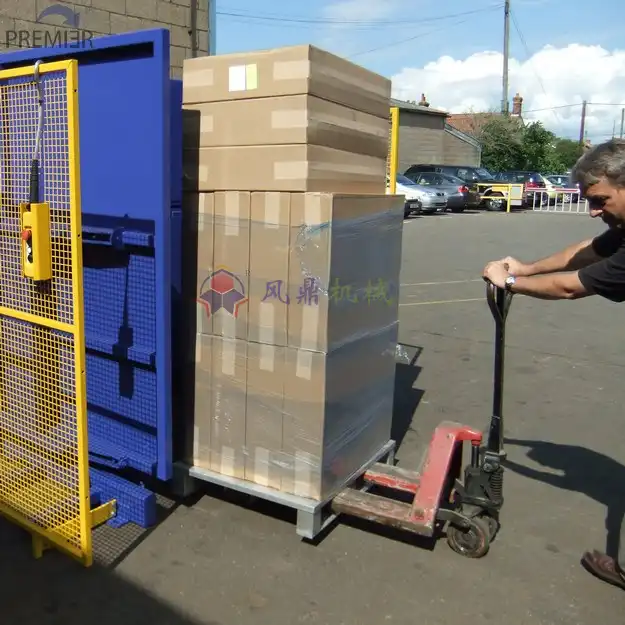
Conclusion
Selecting the right pallet inverter requires a thorough assessment of your specific needs against the available features. By carefully considering load capacity and versatility, rotation angle, clamp system design, safety features, automation level, and build quality, you can choose a machine that significantly boosts efficiency, enhances safety, and offers long-term value for your material handling operations.
Focus on matching the inverter's capabilities to your primary applications – whether it's frequent pallet exchange, handling delicate goods, or integration into an automated line. A well-chosen pallet inverter is more than just equipment; it's a solution that can streamline workflows, reduce labor costs associated with manual handling, minimize product damage, and contribute to a safer, more productive workplace. For further information on material handling best practices, resources from organizations like MHI (Material Handling Industry) can be valuable.

Get Your Best Solution !
Editor's Note: Please check the content of reusable block 16995. If it contains YouTube video links, ensure they are converted to the iframe format specified in the instructions.