Investing in a Steel Tube Mill? Don't Overlook Your Packing Strategy
I. Introduction: The Critical Role of Packaging in Steel Tube Operations
The steel tube industry forms the backbone of numerous critical sectors, including construction, automotive manufacturing, energy infrastructure (oil and gas), and more. For investors establishing or upgrading steel tube mills and factories, focusing solely on production machinery is insufficient. An often-underestimated element crucial for success is the steel tube packing solution.
Effective packaging is not merely about wrapping pipes; it's a strategic process that directly impacts product integrity, transportation safety, operational efficiency, and ultimately, customer satisfaction and profitability. This guide provides essential insights into selecting and implementing the right packing solutions for your steel tube manufacturing facility.
II. Understanding Common Steel Tube Packing Methods
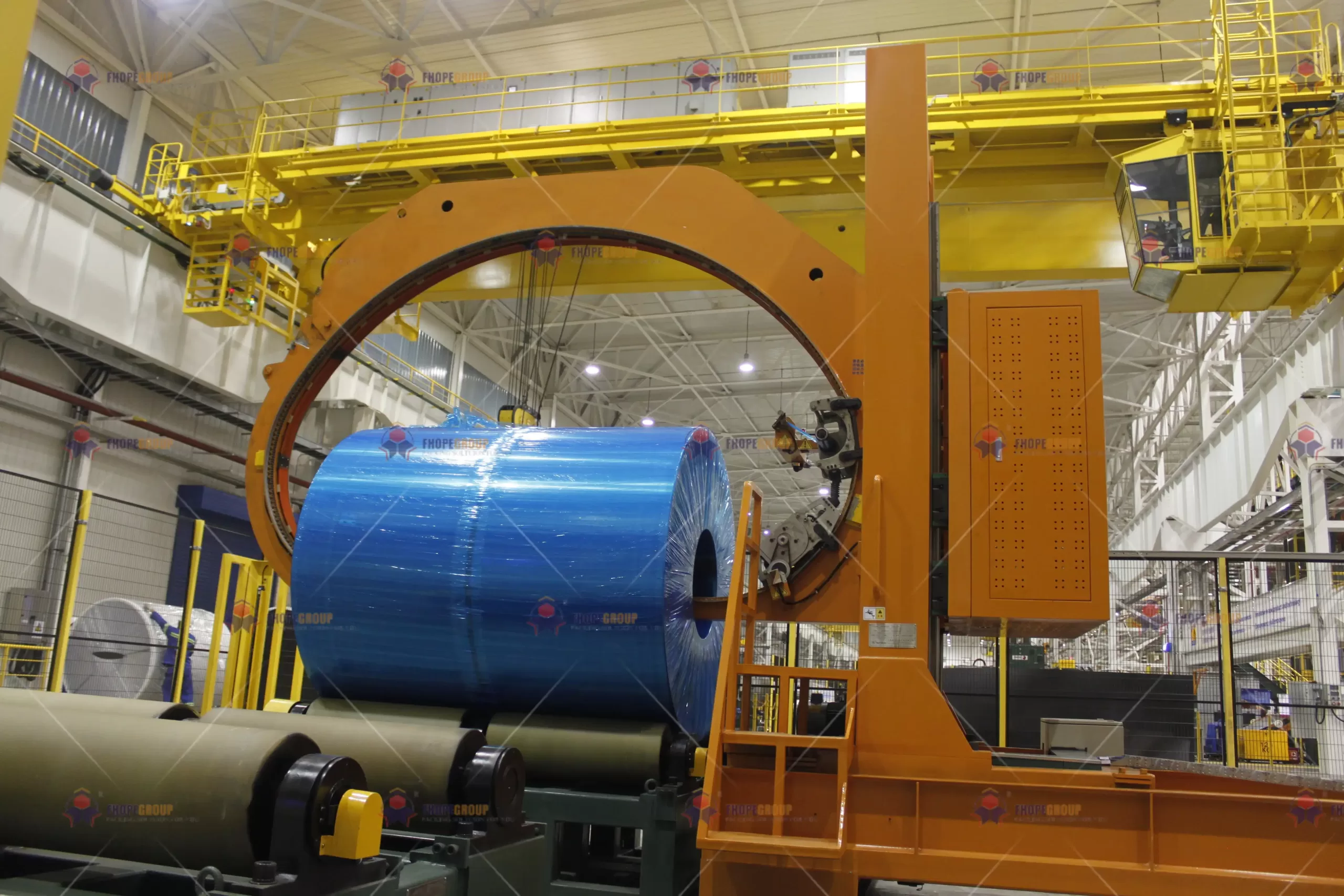
Protecting steel tubes from damage during handling, storage, and transit is paramount. Various methods cater to different tube types, sizes, and customer requirements. Key approaches include:
1. Bundling: Efficient Grouping for Transport
Bundling involves grouping multiple steel tubes—typically of similar size and profile—and securing them tightly using steel or high-strength plastic straps, wires, or bands. This method facilitates easier handling, loading, and unloading using forklifts or cranes.
- Common Shapes: Hexagonal bundles are frequent for round tubes, maximizing density and stability. Square or rectangular bundles are also used.
- Best Suited For: Standardized tubes where bulk handling efficiency is key.
- Considerations: Proper tensioning of straps is vital to prevent shifting or damage. Protective layers (like plastic wrap or end caps) may be added before bundling for sensitive surfaces.
2. Boxing/Crating: Enhanced Protection for Vulnerable Tubes
Placing steel tubes inside wooden crates, sturdy cardboard boxes, or custom-built containers offers superior protection against impacts, contamination, and environmental factors (like moisture).
- Best Suited For: Smaller diameter tubes, high-value products (e.g., stainless steel, precision tubes), tubes with delicate coatings, or products requiring long-term storage or complex logistics.
- Considerations: Increases packaging material cost and weight. Crates must comply with international shipping standards (e.g., ISPM-15 for wood packaging). [Link to authoritative source on ISPM-15]
3. Wrapping: Surface Protection Against Scratches and Corrosion
Wrapping individual tubes or entire bundles in protective materials like VCI (Vapor Corrosion Inhibitor) paper/film, plastic sheeting, bubble wrap, or foam provides a barrier against scratches, moisture, and corrosion.
- Best Suited For: Tubes with sensitive surfaces (polished, coated, painted), stainless steel tubes (preventing contamination), and products destined for humid environments or sea freight.
- Considerations: Can be manual or automated. Material choice depends on the level of protection needed and environmental factors.
4. Strapping: Securing the Load
Strapping uses high-tensile steel or plastic bands to secure tubes to pallets, within bundles, or inside crates. It prevents movement during transit, ensuring load stability.
- Best Suited For: Almost all packing methods utilize strapping as a primary or secondary securing technique.
- Considerations: Strap type (steel vs. plastic), width, and tension must match the weight and nature of the load. Edge protectors may be needed to prevent straps from damaging the tubes.
III. Manual vs. Semi-Automated vs. Fully Automated Packing Systems
The choice between manual labor, semi-automated equipment, and fully integrated automatic packaging lines significantly impacts efficiency, cost, and consistency.
Manual Packing:
- Pros: Low initial investment, high flexibility for custom/complex tasks.
- Cons: Slower speeds, higher labor costs, potential for inconsistency, ergonomic risks for workers.
- Suitable For: Low volume production, highly specialized packing needs, start-up operations.
Semi-Automated Systems: Incorporate machinery for specific tasks (e.g., automatic strapping machines, wrapping machines) while retaining manual handling for others.
- Pros: Balances cost and efficiency, improves consistency for specific tasks, reduces physical strain.
- Cons: Still requires significant labor, potential bottlenecks between manual and automated steps.
- Suitable For: Medium volume production, facilities upgrading from fully manual processes.
cold roll steel coil strapping & packing line5
Fully Automated Packaging Systems: Utilize robotics, conveyors, and integrated machinery for bundling, wrapping, strapping, weighing, and labeling with minimal human intervention.
- Pros: Highest throughput, consistent quality, reduced labor costs, improved safety, potential for data integration (tracking, inventory).
- Cons: High initial investment, requires skilled maintenance, less flexibility for highly variable products, requires significant factory space.
- Suitable For: High volume production, standardized products, facilities prioritizing efficiency and long-term cost reduction. [Link to relevant internal post on factory automation]
(Example of an automated system in action)
(Note: Ensure embedded videos are relevant and functional. Add descriptive alt text to all images illustrating packing methods or equipment.)
IV. Key Factors for Selecting Your Steel Tube Packing Solution
Choosing the optimal packing strategy requires careful consideration of several operational and business factors:
1. Product Specifications
- Tube Type & Material: Different materials (carbon steel, stainless, alloy) have different handling needs. [Link to another post about steel types]
- Dimensions & Weight: Size and weight dictate handling methods and packaging strength requirements.
- Surface Finish & Coatings: Sensitive surfaces need non-abrasive materials and careful handling.
- End Finish: Beveled or threaded ends may require specific protection (caps, rings).
2. Production Volume & Speed
- Your packing line's throughput must match or exceed your mill's output capacity to avoid bottlenecks. High-speed mills necessitate more automated packing solutions.
3. Factory Layout & Integration
- Space Availability: Automated lines require significant floor space. Ensure the chosen solution fits your layout.
- Workflow: How does packing integrate with end-of-line inspection, weighing, and staging areas?
- System Integration: Can the packing system communicate with Manufacturing Execution Systems (MES) or Enterprise Resource Planning (ERP) for tracking and inventory?
4. Budget & Return on Investment (ROI) Analysis
- Initial Cost: Factor in equipment purchase, installation, and commissioning.
- Operating Costs: Include consumables (straps, wrap), energy, labor, and maintenance.
- ROI Calculation: Evaluate savings from reduced labor, increased throughput, lower damage rates, and improved customer satisfaction against the investment cost.
5. Labor Availability & Skill Requirements
- Assess the availability and cost of labor for manual packing versus the need for skilled technicians to operate and maintain automated systems.
6. Customer & Shipping Requirements
- Destination & Transit Mode: Export shipping, especially sea freight, often requires enhanced corrosion protection and robust packaging.
- Customer Specifications: Large clients may have specific packaging standards that must be met.
- Regulations: Comply with transportation regulations and wood packaging standards (ISPM-15).
7. Scalability & Future Needs
- Can the chosen system be easily expanded or adapted if your production volume increases or product mix changes?
V. Enhancing Safety in Steel Tube Packing Operations
Steel tube packing involves heavy materials and potentially automated machinery, making safety paramount. Implement these measures:
1. Ergonomic Workstation Design
- Minimize manual lifting of heavy tubes or bundles. Use lift assists, conveyors, and properly designed workstations to reduce strain.
2. Comprehensive Training & Procedures
- Ensure all personnel are trained on safe operating procedures (SOPs) for packing equipment and manual handling techniques.
- Mandate appropriate Personal Protective Equipment (PPE), such as gloves, safety glasses, hard hats, and steel-toed boots.
3. Machine Guarding & Safety Interlocks
- Automated equipment must have proper guarding around moving parts, pinch points, and robotic arms.
- Utilize safety interlocks, emergency stops, and light curtains to protect operators.
steel master coil wrapper 2010 4. Regular Equipment Maintenance
- Implement a preventive maintenance schedule to keep equipment in safe working order.
- Follow lockout/tagout procedures during maintenance and repairs.
VI. Sustainability in Steel Tube Packaging
Environmental responsibility is increasingly important. Consider these eco-friendly practices:
1. Material Selection
- Opt for recyclable materials like steel straps (highly recyclable) or PET straps made from recycled content.
- Explore biodegradable or recyclable wrapping films and edge protectors.
- Use sustainably sourced wood (FSC certified, ISPM-15 compliant) for crates.
2. Waste Reduction
- Optimize packing designs to use the minimum amount of material necessary for adequate protection.
- Implement systems to reuse or recycle packaging components (e.g., dunnage, pallets).
3. Energy Efficiency
- Choose automated equipment with energy-saving features (e.g., variable speed drives, efficient motors).
VII. Customized Packing Solutions for Specialized Steel Tubes
Standard packing methods may not suffice for all products. Customization is often necessary for:
- Coated or High-Gloss Tubes: Require soft, non-abrasive wrapping and careful handling to prevent scratches.
- High-Precision or Thin-Walled Tubes: Need protection against bending or deformation, often involving custom cradles or internal supports within boxes/crates.
- Large Diameter or Heavy Wall Pipes: Demand heavy-duty strapping, specialized handling equipment (e.g., C-hooks, spreader bars), and potentially custom saddles for support during transit.
- Stainless Steel Tubes: Must be protected from carbon contamination; use dedicated handling equipment and appropriate wrapping materials.
- Export Shipments: Often require enhanced corrosion protection (VCI materials, desiccants) and robust packaging to withstand long transit times and handling at multiple ports.
Collaborate closely with packaging equipment suppliers and material providers to develop solutions tailored to your specific product needs and market requirements.
VIII. Future Outlook: Trends Shaping Steel Tube Packaging
The technology and strategies for packing steel tubes continue to evolve:
1. Increased Automation & Robotics
- Expect wider adoption of robotics for complex handling tasks, vision systems for quality checks, and fully autonomous packing lines.
2. Smart Packaging & IoT Integration
- Sensors embedded in packaging could monitor conditions like humidity, temperature, or shock during transit.
- Integration with IoT platforms allows real-time tracking and data analysis for logistics optimization.
3. Advanced Materials
- Development of stronger, lighter, and more sustainable packaging materials will continue.
4. Data-Driven Optimization
- Using data from packing lines (speeds, material usage, downtime) to continuously improve efficiency and reduce costs.
5. Circular Economy Models
- Growing interest in reusable or returnable packaging systems, especially for regional or closed-loop supply chains.
IX. Conclusion: Strategic Packing Equals Smarter Investment
For investors in the steel tube industry, the packing solution is not an afterthought—it's a strategic component of your operation. Selecting the right combination of methods, equipment (manual, semi-auto, or fully automated), and materials directly influences product quality, operational costs, safety, and customer perception.
By carefully analyzing your product requirements, production volume, budget, and logistical needs, you can implement a packing strategy that protects your products, streamlines your operations, and contributes significantly to the overall success and profitability of your steel tube mill or factory. Making informed decisions about packing technology is a crucial step towards building a resilient and competitive manufacturing enterprise.