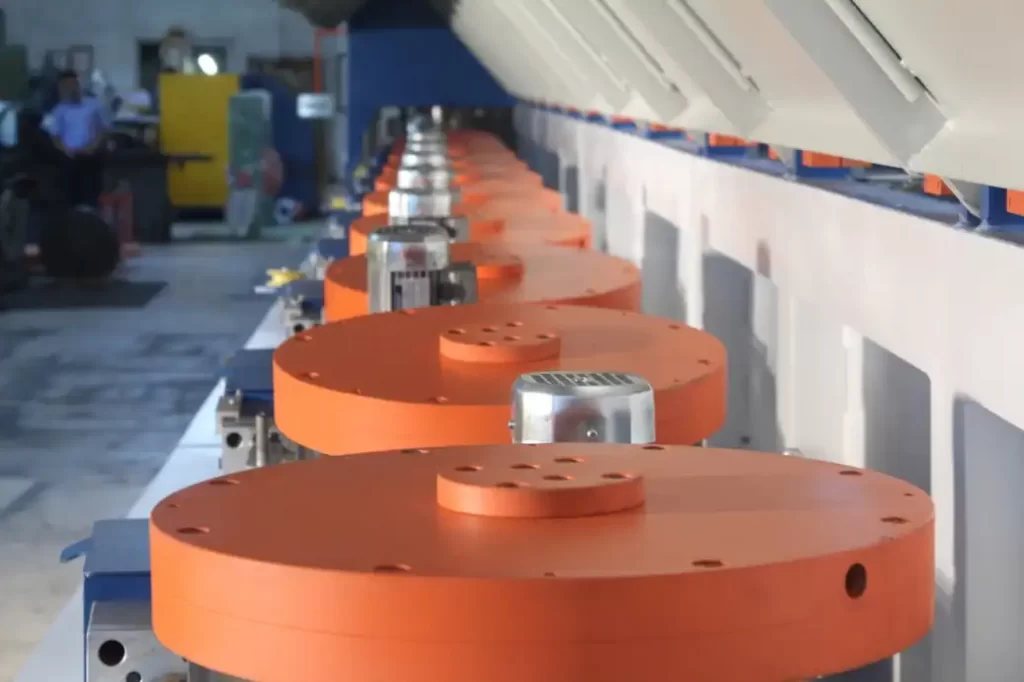
Essential Packaging Considerations for Your Steel Wire Drawing Line Investment
Investing in a steel wire drawing line represents a significant commitment to enhancing manufacturing capabilities. However, the success of this investment extends beyond the drawing process itself. An often-underestimated factor is the downstream packaging solution. Effective packaging is paramount for protecting product integrity, ensuring safe transport, and meeting customer expectations. This guide delves into the critical packaging solutions and considerations necessary to optimize your steel wire production.
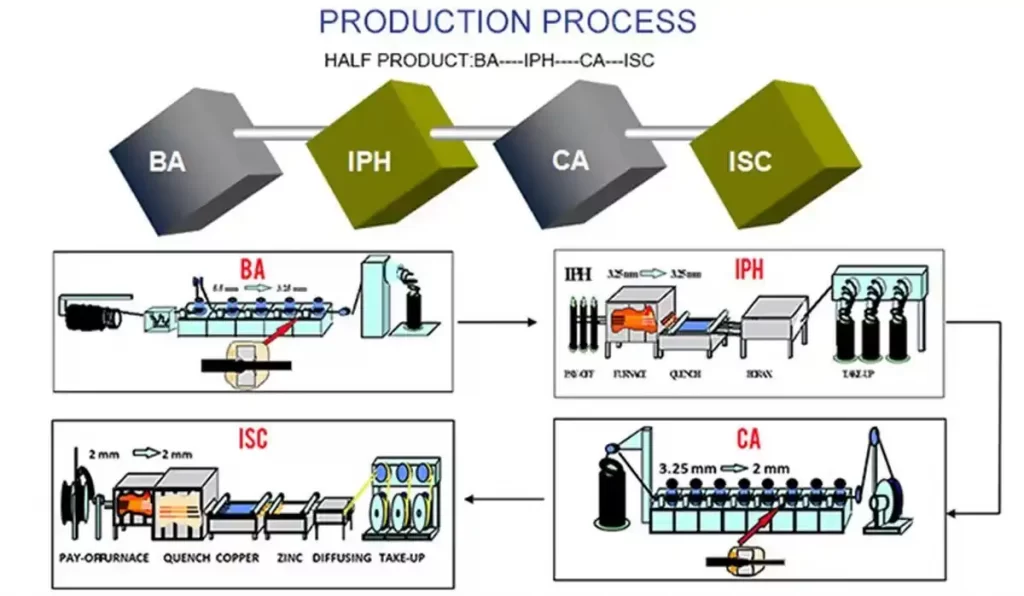
Understanding Steel Wire Drawing Lines
What Is a Steel Wire Drawing Line?
A steel wire drawing line is an industrial setup designed to reduce the cross-sectional diameter of steel wire. This is accomplished by systematically pulling the wire through a sequence of drawing dies, which progressively decrease its size while simultaneously improving tensile strength and surface finish.
Importance in Modern Manufacturing
Steel wire serves as a foundational material in numerous sectors, including construction (reinforcement bars, mesh), automotive (springs, tyre cords), energy (cables), and consumer goods (fasteners, springs). High-quality wire, produced efficiently, is crucial for manufacturers aiming to meet stringent industry standards and maintain a competitive edge.
The Critical Role of Packaging in Wire Drawing Operations
Why Effective Wire Packaging Matters
Packaging steel wire transcends simple presentation. Its primary functions are:
- Protection: Shielding the wire from physical damage (dents, kinks), environmental factors (moisture, contaminants), and corrosion during handling, storage, and transit.
- Preservation: Maintaining the wire's properties and quality from the production line to the end-user.
- Handling Efficiency: Facilitating easier and safer movement, storage, and unwinding of the wire.
- Information: Conveying essential product details, specifications, and handling instructions.
Key Packaging Challenges for Steel Wire
Producers face several inherent challenges when packaging steel wire:
- Weight and Density: Steel wire coils or spools can be extremely heavy and dense, demanding robust and durable packaging materials and handling equipment.
- Corrosion Susceptibility: Steel is prone to rust when exposed to moisture and oxygen. Packaging must provide an adequate barrier or incorporate corrosion inhibitors (like VCI paper/film).
- Tangle Prevention and Payoff: The wire must be packaged to prevent tangling and allow for smooth, consistent payoff at the customer's end. Improper winding or securing can lead to significant downtime and waste.
- Dimensional Stability: Maintaining the shape and integrity of coils or spools during transport is vital.
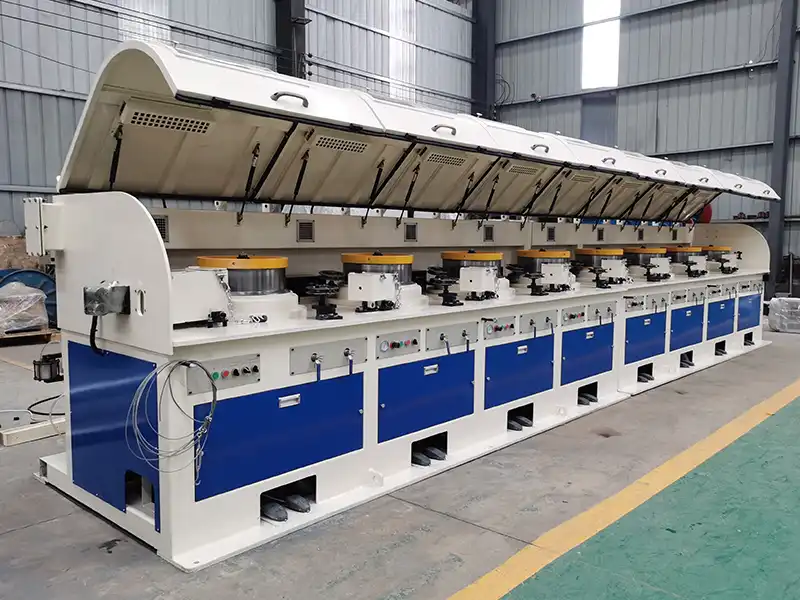
Common Types of Steel Wire Packaging Solutions
Choosing the right packaging format depends on wire type, diameter, weight, customer requirements, and handling capabilities.
1. Coil Packaging
Wire is wound into coils, often secured with strapping.
- Pros: Efficient use of space, suitable for larger diameter wires, cost-effective.
- Cons: Can be prone to tangling if not properly secured or handled, requires careful payoff setup.
- Variations: Eye-to-sky or eye-to-wall orientation, with or without central cores (formers).
2. Spool (Reel) Packaging
Wire is wound onto rigid spools made of plastic, metal, or wood/plywood.
- Pros: Excellent tangle prevention, easy payoff, suitable for finer wires and automated processes.
- Cons: Spools add weight and cost, less space-efficient than coreless coils.
3. Bundle Packaging
Typically used for shorter lengths or specific forms like straightened and cut wire. Wires are grouped and secured, often with straps or wrapping.
- Pros: Suitable for specific product forms.
- Cons: Less common for continuous wire from drawing lines.
Comparing Common Packaging Materials
Plastic (Stretch Film, Shrink Film, Straps)
- Properties: Lightweight, flexible, provides good moisture resistance and coil stability when applied correctly. Stretch film is widely used for overwrapping coils and spools. Plastic strapping secures coils and bundles.
- Applications: Overwrapping, securing loads, moisture barrier.
Steel (Strapping, Structural Supports)
- Properties: High strength and rigidity. Steel strapping offers maximum security for heavy coils. Steel frames or pallets may be used for large, heavy units.
- Applications: Heavy-duty strapping, structural support for large coils/spools.
Paper and Cardboard (VCI Paper, Liners, Labels)
- Properties: Often incorporates Volatile Corrosion Inhibitors (VCI) to protect against rust. Provides cushioning and surface protection. Used for labeling and documentation. Eco-friendly options are increasingly available.
- Applications: Corrosion protection, interleaving, labeling, light cushioning.
Leveraging Advanced Packaging Technologies
Automated Packaging Systems
Integrating automated packaging equipment downstream from the wire drawing line significantly boosts efficiency, consistency, and safety. Systems can include:
- Automated coil strapping machines
- Coil compactors
- Orbital stretch wrappers
- Robotic palletizing and handling systems
Smart Packaging Solutions
Incorporating sensors or RFID tags into packaging allows for:
- Real-time tracking of shipments.
- Monitoring environmental conditions (humidity, temperature).
- Enhanced inventory management and traceability.
Environmental Considerations in Wire Packaging
Sustainable Packaging Materials
There is growing pressure and opportunity to adopt sustainable packaging practices:
- Using recyclable or biodegradable materials (e.g., recycled content plastics, responsibly sourced wood for spools).
- Optimizing packaging design to minimize material usage ("lightweighting").
- Implementing returnable/reusable packaging systems where feasible (e.g., durable metal spools).
Energy Consumption
Automated packaging lines consume energy. Opting for energy-efficient machinery and optimizing line layouts can reduce operational costs and environmental impact.
Tailoring Packaging to Industry-Specific Needs
Construction Industry
- Focus: Durability, weather resistance, ease of handling on rough job sites. Robust strapping and weather-resistant wrapping are key.
Automotive Industry
- Focus: High precision, cleanliness, consistent payoff for automated manufacturing lines. Spool packaging is common. Protection against contamination is crucial.
Electronics Industry
- Focus: Protection for fine wires, potentially requiring anti-static materials. Precise winding and spooling are essential.
Conducting a Cost-Benefit Analysis
Initial Investment Costs
Consider the capital expenditure for packaging machinery (strappers, wrappers, conveyors, robots) and the ongoing cost of consumable materials (film, straps, spools, VCI paper).
Long-Term Savings and ROI
Effective packaging minimizes costs associated with:
- Product damage during transit and storage.
- Customer claims and returns due to quality issues (corrosion, tangles).
- Inefficient handling and storage.
- Workplace injuries related to manual handling.
Investing in automation and quality materials often yields significant long-term returns through reduced waste, improved efficiency, and enhanced customer satisfaction.
Choosing the Right Packaging Supplier
Evaluate Reputation and Experience
Partner with suppliers who have a proven track record in the wire industry. Experienced suppliers can offer valuable advice on material selection, machine integration, and process optimization. Look for case studies and client testimonials.
Assess Customization Capabilities
Your packaging needs might be unique. Seek suppliers who can offer customized solutions, whether it's specific spool designs, tailored VCI formulations, or integrated automated systems designed for your specific output and layout.
Implementation Strategies for Packaging Solutions
Seamless Integration with Production
Plan the layout and workflow carefully to ensure the packaging line integrates smoothly with the wire drawing and takeoff equipment. Minimize bottlenecks and unnecessary handling steps. Consider buffer zones and material flow.
Operator Training and Ongoing Support
Proper training is essential for operators to run and maintain packaging equipment efficiently and safely. Ensure your supplier provides comprehensive training and readily available technical support for troubleshooting and maintenance.
Conclusion: Strategic Packaging for Wire Production Success
Investing in the optimal packaging solution is not an afterthought but a strategic necessity for any steel wire drawing operation. By carefully considering the types of packaging, materials, available technologies, industry requirements, and cost implications, manufacturers can protect their products, enhance operational efficiency, meet sustainability goals, and ultimately satisfy their customers. Prioritizing robust and efficient packaging safeguards the significant investment made in the wire drawing line itself and contributes directly to long-term business success.
Key Considerations for Investing in a Steel Wire Plant
When planning a new steel wire plant or upgrading an existing one, incorporating packaging considerations early is crucial for efficiency and success.
1. Wire Winding Carrier Design (Basket/Cart/Former)
The design of the carrier onto which wire is wound (be it a basket, cart, spool, or former) must be compatible with downstream automated packaging processes like strapping and wrapping. Retrofitting carriers later can be costly and inefficient. Design considerations include dimensions, handling points, and stability for automated handling.
2. Factory Layout and Workflow Design
The physical layout of the factory must allocate sufficient space and logical positioning for the automated packaging line. Consider material flow from the drawing/winding machines to compacting, strapping, wrapping, labeling, and finally to warehousing or dispatch. Efficient layout minimizes transit distances and prevents bottlenecks.
3. Digitization in Production and Packing
Integrating digital technologies offers significant advantages:
- Process Monitoring: Sensors on drawing and packaging machines provide real-time performance data.
- Automation Control: PLC and SCADA systems manage and coordinate production and packaging steps.
- Data Management: ERP/MES systems track production orders, inventory levels, quality data, and shipping information, linking production output directly to packaged, labeled goods.
Digitization enhances control, traceability, and data-driven decision-making.
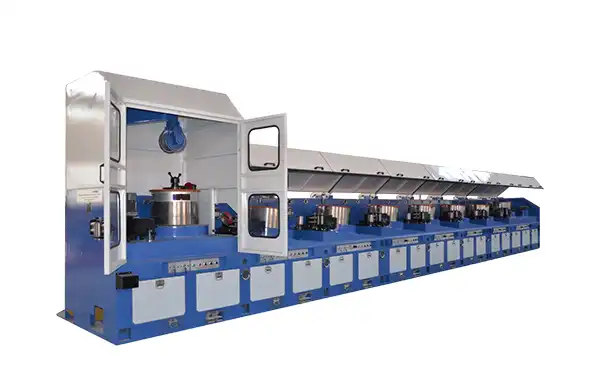
Benefits of Automation in Steel Wire Production and Packaging
Automation offers compelling advantages throughout the steel wire production and packaging process:
1. Increased Efficiency
Automated systems operate continuously at consistent speeds, reducing cycle times and increasing overall throughput compared to manual operations. This leads to higher production capacity and shorter lead times.
2. Improved Product Quality & Consistency
Automation minimizes human error in processes like winding tension control, strapping placement, wrapping consistency, and labeling accuracy. This results in more uniform product quality and reduced variability.
3. Reduced Labor Costs & Optimized Workforce
Automation reduces the need for manual labor in repetitive, strenuous, or potentially hazardous tasks, lowering direct labor costs. Staff can be reallocated to higher-value roles like quality control, maintenance, and supervision.
4. Enhanced Workplace Safety
Automating tasks like heavy coil handling, strapping, and cutting reduces the risk of musculoskeletal injuries and accidents associated with manual labor.
5. Scalability and Flexibility
Automated lines can often be adjusted more easily than manual processes to handle variations in production volume or product specifications. Modular automation allows for easier expansion or modification.
6. Comprehensive Data Collection and Analysis
Automated systems generate vast amounts of data on machine performance, cycle times, material consumption, and potential errors. This data is invaluable for process optimization, predictive maintenance, and quality tracking.
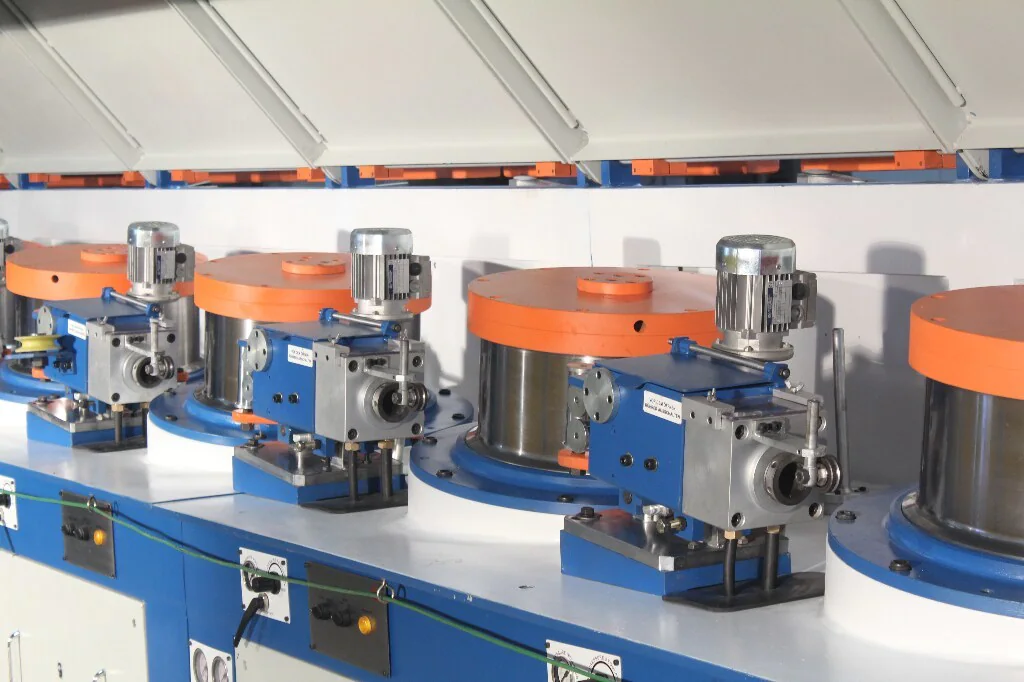
Components of an Automated Steel Wire Coil Packing Line
A fully automated packing line can streamline the entire process from winding to warehouse-ready pallets. Key stages include:
1. Automatic Winding/Rewinding Control
Integration with the drawing line or dedicated rewinders ensures coils are produced to precise length or weight specifications, ready for automated handling.
2. Automatic Steel Wire Coil Compacting and Strapping
Coils are automatically transported to a station where they are compacted (if necessary) to achieve desired density and dimensions, followed by automatic application of radial and/or through-eye straps for security.
3. Automatic Steel Wire Coil Wrapping
Compacted and strapped coils move to a wrapping station, typically an orbital stretch wrapper, which applies protective layers of stretch film or VCI paper/film for environmental protection and stability.
4. Automatic Steel Wire Coil Stacking and Palletizing
Wrapped coils are automatically picked, oriented, and stacked onto pallets according to pre-programmed patterns. Robotic arms are commonly used for this task due to the weight and precision required.
5. Integration with ERP/MES Systems
The packing line control system communicates with higher-level ERP (Enterprise Resource Planning) or MES (Manufacturing Execution System) software to receive order information, track coil data (weight, length, grade, heat number), and update inventory records automatically.
6. Automatic Labeling
An automated label applicator prints and applies labels with barcodes, QR codes, and human-readable information (product details, batch numbers, customer info) to each coil or pallet, ensuring full traceability.
7. Automatic Pallet Handling and Warehousing Integration
Finished pallets can be automatically conveyed to stretch hooding or wrapping stations, then transported via AGVs (Automated Guided Vehicles) or conveyor systems to designated warehouse locations, integrating with automated storage and retrieval systems (AS/RS) if available.