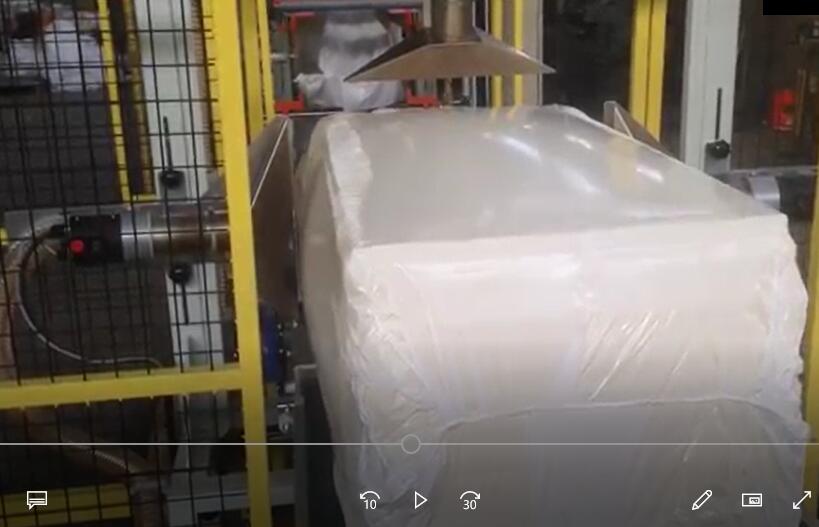
Understanding Panel Bagging Machines: With and Without Sealers
Introduction
In the realm of packaging technology, panel bagging machines stand out as essential tools for businesses aiming to streamline their operations. These machines are pivotal in ensuring products are efficiently and securely packaged. However, a key distinction within this category is between machines with sealers and those without. This article explores the differences, advantages, and applications of each type, providing a comprehensive understanding for businesses looking to optimize their packaging processes.
What Are Panel Bagging Machines?
Panel bagging machines are automated systems designed to fill and seal bags with various products. These machines are versatile, handling different materials such as plastics, paper, and composites. They are widely used across industries, including food processing, pharmaceuticals, and consumer goods.
The Role of Sealers in Bagging Machines
A sealer in a bagging machine ensures that the contents of the bag are securely enclosed. Sealers can employ different technologies, such as heat sealing, ultrasonic sealing, or adhesive sealing, each suitable for specific materials and applications. The presence of a sealer can significantly impact the efficiency and security of the packaging process.
Benefits of Bagging Machines with Sealers
- Enhanced Product Security: Sealers provide an airtight closure, protecting contents from contamination, moisture, and tampering.
- Extended Shelf Life: Especially important for perishable goods, sealed bags prevent spoilage and maintain freshness.
- Professional Appearance: Sealed bags often look more polished and consistent, enhancing brand image.
- Versatility in Materials: Machines with sealers can handle a broader range of bag materials, including those requiring specific sealing techniques.
Advantages of Bagging Machines Without Sealers
- Cost-Effectiveness: Machines without sealers are generally less expensive, both in terms of initial investment and maintenance.
- Faster Processing: Without the need for sealing, these machines can operate at higher speeds, ideal for high-volume operations.
- Simplicity and Maintenance: Fewer components mean easier maintenance and reduced downtime.
- Flexibility for Certain Products: For products not requiring airtight packaging, non-sealing machines can be more efficient.
Key Differences Between the Two
1. Operational Complexity
- With Sealer: Requires more intricate setup and adjustment, especially when dealing with different materials.
- Without Sealer: Simpler operation with fewer adjustments needed.
2. Application Range
- With Sealer: Ideal for products needing protection from environmental factors.
- Without Sealer: Suitable for bulk items or products where sealing is unnecessary.
3. Cost Implications
- With Sealer: Higher initial and operational costs due to additional components and energy consumption.
- Without Sealer: Lower costs, making them accessible for smaller businesses or specific applications.
Choosing the Right Machine for Your Business
Assessing Product Needs
Understand the specific requirements of your products. For instance, food items often require sealing to prevent spoilage, while non-perishable items might not.
Evaluating Volume and Speed
Consider your production volume and speed requirements. Machines without sealers might be better for high-speed operations, whereas sealed packaging might be necessary for certain quality standards.
Budget Considerations
Factor in both initial investment and long-term operational costs. Machines with sealers might incur higher costs but offer added benefits that justify the expense.
Technological Innovations in Bagging Machines
Recent advancements have introduced more efficient sealing technologies, such as:
- Ultrasonic Sealing: Offers precise and energy-efficient sealing, perfect for delicate materials.
- Continuous Motion Systems: Allow for faster processing speeds without sacrificing seal quality.
Environmental Considerations
With increasing emphasis on sustainability, many companies are opting for eco-friendly packaging solutions. Machines that support biodegradable materials or require less energy for sealing are gaining popularity.
Common Industries Utilizing Bagging Machines
- Food and Beverage: Ensures hygiene and extends shelf life.
- Pharmaceuticals: Protects sensitive products from contamination.
- Retail and Consumer Goods: Enhances product presentation and security.
- Agriculture: Efficiently packages seeds, fertilizers, and other bulk items.
Future Trends in Packaging Technology
The future of packaging technology is geared towards automation and sustainability. Integration with IoT and AI for predictive maintenance and efficiency optimization is on the rise. Moreover, there is a growing focus on developing machines that can handle recyclable and biodegradable materials without compromising on performance.
Conclusion
Choosing between panel bagging machines with or without sealers depends on various factors, including product type, operational requirements, and budget. Machines with sealers offer enhanced security and preservation, crucial for many industries. In contrast, non-sealing machines provide speed and cost benefits. By understanding the specific needs of your business and staying informed about technological advancements, you can make an informed decision that enhances your packaging process and aligns with your operational goals.
Panel bagging machines offer an affordable, scalable solution for any operation looking to modernize and streamline their packaging processes. With rapid return on investment, these machines are an easy choice for improving productivity, reducing costs, and increasing quality standards.