Steel Coil Packing Lines: Tailored Solutions for Small and Medium Businesses
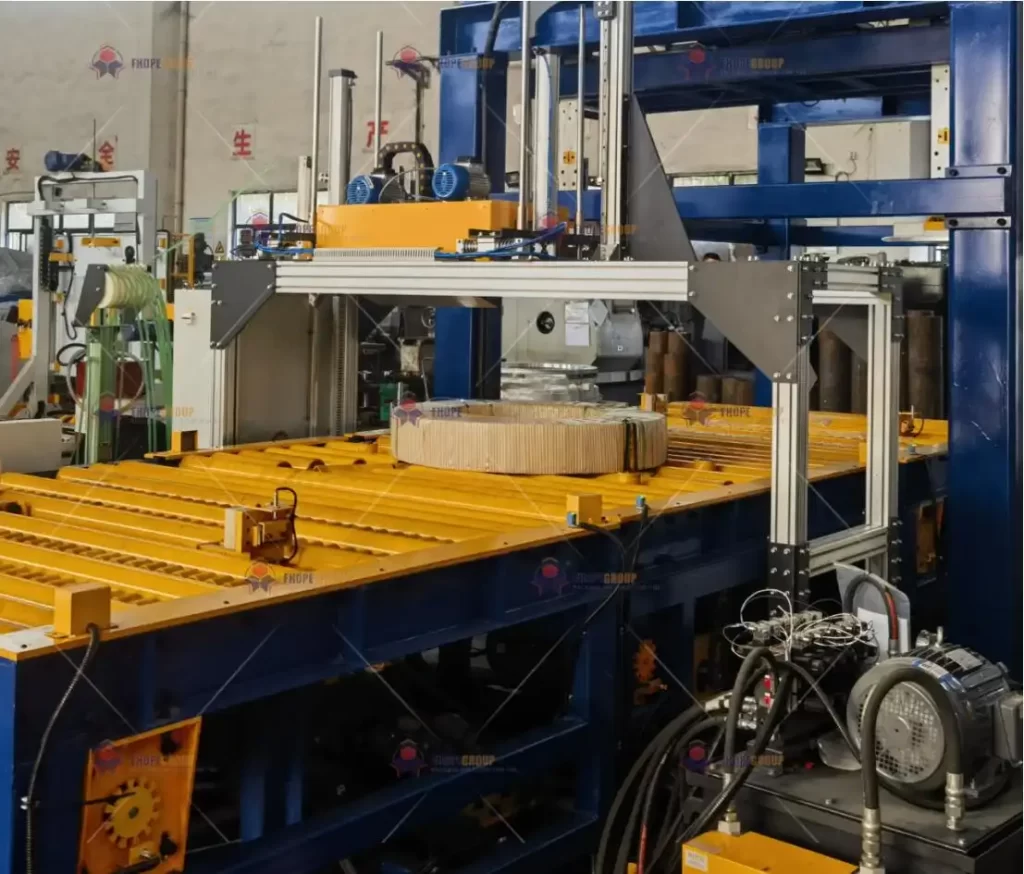
Effective steel coil packing is essential for metal service centers and fabricators to protect valuable products from physical damage, corrosion, and contamination during handling, transit, and storage. While large enterprises often deploy comprehensive automation, small and medium-sized businesses (SMBs) face unique hurdles when implementing efficient steel coil packing lines. Budget limitations, restricted floor space, and diverse coil specifications often complicate the adoption of standard solutions. This guide explores how customized steel coil packing lines can provide SMBs with optimal, cost-effective results, enhancing their operational efficiency and competitive standing.
1. Why Customized Steel Coil Packing Lines Are Crucial for SMBs
Customization is paramount when addressing the specific operational context of SMBs. Unlike large corporations with standardized high-volume runs, smaller businesses often cannot justify a generic, one-size-fits-all packing line due to distinct constraints. Many SMBs process coils with varying widths, diameters, and weights. A flexible steel coil packing line, tailored to their product mix, ensures each coil is packaged securely and appropriately without requiring frequent manual changeovers or multiple specialized machines.
Investing in tailored solutions prevents SMBs from overspending on features irrelevant to their scale or specific needs. This ensures an optimal balance between necessary functionality and capital investment. For SMBs, the right packing line configuration reduces operational expenditures, improves workflow efficiency, enhances worker safety, and safeguards product quality. Custom-designed machines can be configured for compact layouts, allow for future upgrades as the business expands, and efficiently handle a specified range of coil sizes, minimizing product damage and lowering overall packing costs per coil.
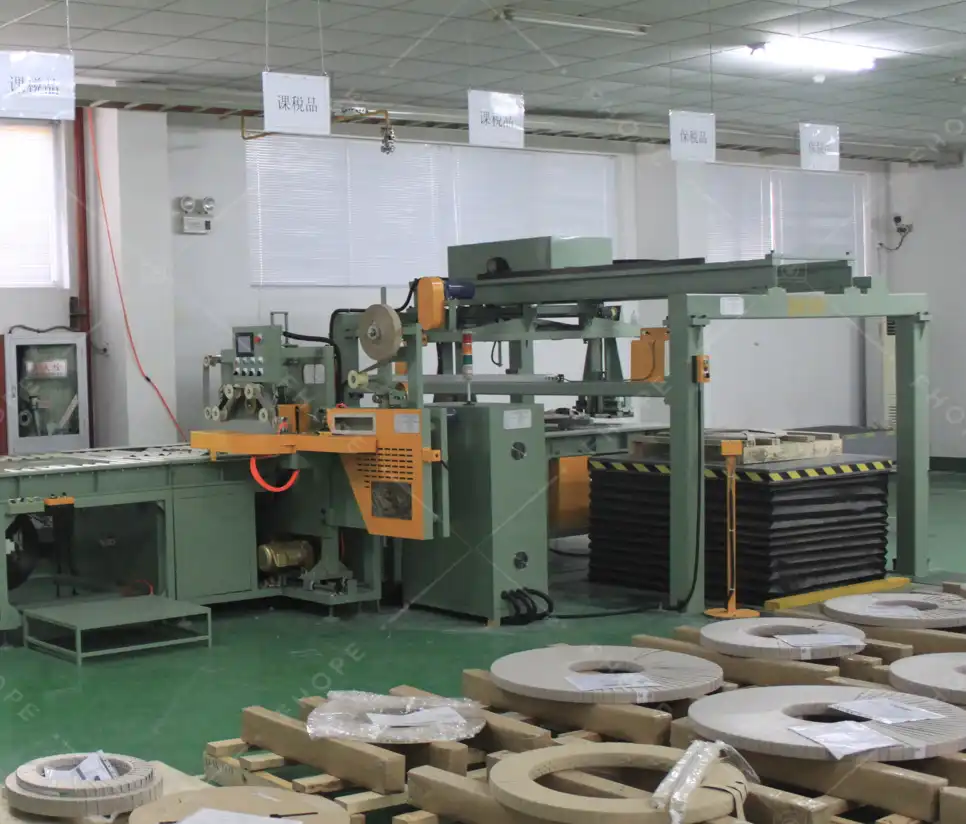
2. Assessing the Unique Needs of Small and Medium Businesses
Before selecting or designing a steel coil packing line, SMBs must perform a detailed assessment of their specific operational requirements. Key factors to evaluate include:
- Coil Specifications:
- Inner Diameter (ID) and Outer Diameter (OD) range
- Maximum and minimum coil width
- Maximum and minimum coil weight
- Material type (e.g., galvanized, stainless, aluminum) and surface sensitivity
- Throughput Requirements:
- Required packing speed (coils per hour/shift) to meet production or shipping demands.
- Batch sizes and frequency of changeovers.
- Budgetary Constraints:
- Available capital for initial investment.
- Consideration of long-term operational costs (labor, energy, maintenance, consumables).
- Available Facility Space:
- Maximum footprint available for the packing line.
- Ceiling height limitations.
- Integration points with existing production flow (e.g., slitter outfeed, crane access).
- Packing Requirements:
- Need for eye-to-sky or eye-to-wall orientation.
- Specific strapping requirements (material: PET or steel; number and position of straps).
- Wrapping needs (e.g., stretch film, VCI paper/film for corrosion protection).
- Labeling or marking requirements.
- Future Scalability:
- Potential for increased production volume.
- Anticipated changes in coil sizes or types.
- Desire for phased implementation or future automation upgrades.
A clear understanding of these factors enables equipment providers to propose or design a customized packing line that delivers optimal performance and ROI without incorporating costly, unnecessary features.
3. Key Features of Customized Steel Coil Packing Lines for SMBs
When engineering a tailored packing solution for SMBs, several features are critical for balancing efficiency, cost-effectiveness, and flexibility:
a) Adjustable and Modular Design
Given the potential variability in coil sizes handled by SMBs, adjustable packing modules are essential. Systems should accommodate the specified range of coil dimensions (ID, OD, width, weight) with minimal manual intervention. Automated adjustments based on coil detection sensors can significantly save time during changeovers. A modular design allows SMBs to select only the necessary stations (e.g., weighing, strapping, wrapping, labeling) and potentially add more later.
b) Appropriate Level of Automation (e.g., Coil Strapping)
Automation is key to improving efficiency and consistency. For SMBs, automating critical or labor-intensive processes like strapping offers significant benefits. Automated coil strapping systems (using PET or steel strap) can be integrated to secure coils reliably and quickly, reducing manual labor requirements, improving safety, and ensuring consistent strap placement and tension. The level of automation should match the SMB's throughput needs and budget – semi-automatic options might be suitable for lower volumes.
c) Space-Efficient Layouts
Limited factory floor space is a common constraint for SMBs. Packing line designs must prioritize space efficiency. Compact machine footprints, vertical configurations where feasible, and modular layouts allow SMBs to integrate essential packing functions without requiring excessive space, optimizing workflow within existing facility constraints.
d) User-Friendly Controls and HMI
An intuitive Human-Machine Interface (HMI) ensures that operators can run and monitor the packing line with minimal training. Clear instructions, simple controls for adjustments, real-time status updates, and straightforward diagnostic messages reduce the learning curve and minimize operational errors. This is crucial for SMBs where dedicated maintenance staff may be limited.
e) Customizable Wrapping and Protection Options
Different steel products and end-use applications necessitate specific protection levels. Some coils require robust corrosion protection (e.g., using VCI materials), while others need durable wrapping to prevent surface damage. A customizable wrapping system allows SMBs to utilize appropriate materials (stretch film, VCI paper, barrier film) and methods (orbital wrapping, through-eye wrapping) tailored to their product requirements and customer specifications.
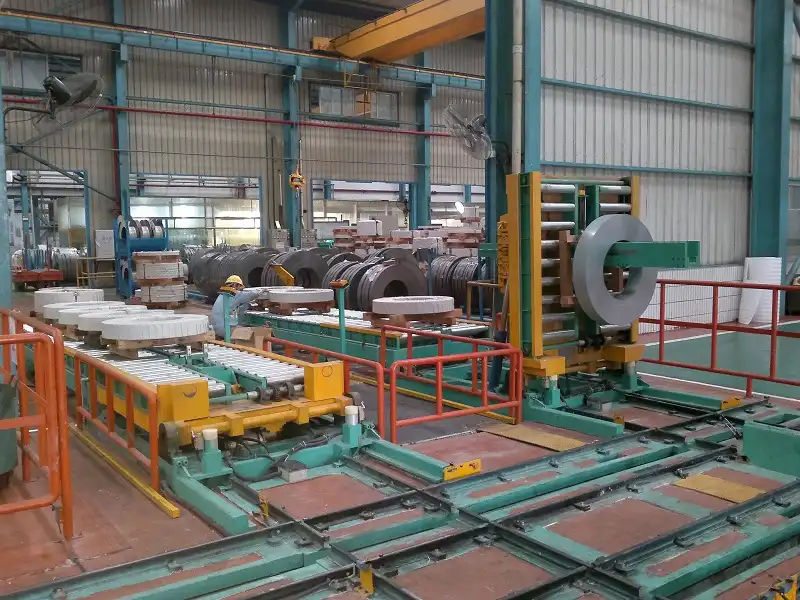
4. Achieving Cost-Effectiveness with Tailored Solutions
A primary concern for SMBs is the investment cost. However, customized packing solutions can be highly cost-effective, delivering long-term value. Here’s how:
a) Avoiding Over-Specification
A customized approach prevents SMBs from paying for over-engineered systems with capabilities they don't need. By focusing investment on features directly addressing their specific operational requirements (throughput, coil sizes, protection levels), tailored solutions optimize the initial capital expenditure.
b) Reducing Manual Labor Costs
Strategic automation within the packing line significantly reduces the need for manual handling and packing tasks. This leads to substantial long-term savings in labor costs, reduces ergonomic risks, and frees up employees for higher-value activities. Even semi-automated solutions can offer considerable labor savings compared to fully manual methods.
c) Optimizing Energy Efficiency
Modern packing machinery can be designed with energy-efficient components, such as variable speed drives and smart power management systems. Minimizing energy consumption reduces ongoing operational costs and aligns with sustainability goals, which can be increasingly important for SMBs.
d) Phased Implementation and Modular Expansion
SMBs don't necessarily need to invest in a fully automated line upfront. Modular solutions allow for a phased approach. A business might start with essential modules like strapping and gradually add automated wrapping, weighing, or labeling stations as production grows or budgets allow. This scalability protects the initial investment and aligns spending with business growth.
5. How Customized Solutions Boost Productivity
By directly addressing the operational realities of SMBs, customized packing lines deliver significant productivity gains:
a) Minimizing Changeover Times
Packing lines designed for the specific range of coils handled by an SMB, potentially with automated adjustments, drastically reduce the downtime associated with changing between different coil sizes or packing requirements.
b) Reducing Errors and Rework
Manual packing is susceptible to inconsistencies and errors, potentially leading to insecure loads, damaged products, customer complaints, and costly rework. Automated or semi-automated systems ensure consistent application of straps, wrap, and labels according to predefined parameters, improving package integrity and reducing defect rates.
c) Streamlining Material Flow
Integrating a customized packing line smoothly into the overall production workflow eliminates bottlenecks between processes (e.g., slitting and shipping). A well-designed line facilitates a continuous flow, reducing coil staging time and shortening the overall lead time from production to dispatch.
d) Improving Uptime
Automated systems often include self-diagnostics and maintenance alerts, helping to predict potential issues before they cause unexpected breakdowns. Quick troubleshooting and reliable operation contribute to higher overall equipment effectiveness (OEE) and consistent throughput.
6. Overcoming Common SMB Challenges with Custom Packing Lines
Customized steel coil packing lines are specifically designed to mitigate the typical challenges faced by smaller operations:
- Space Constraints: Custom layouts, compact machine designs, and potentially vertical accumulation can fit efficient packing capabilities into limited floor areas.
- Product Diversity: Flexible, adjustable systems with quick-changeover features or automated adjustments handle varying coil dimensions (ID, OD, width) without significant downtime or manual effort.
- Budget Limitations: Focusing on essential automation, exploring semi-automatic options, utilizing modular designs for phased investment, and calculating long-term ROI helps justify the expenditure and ensures affordability.
- Limited Technical Staff: User-friendly interfaces, remote diagnostics support, and comprehensive training minimize reliance on specialized in-house maintenance expertise.
vertical coil packaging line2 7. The Importance of Supplier Support and Training
Investing in a customized packing line is just the first step. To maximize the return on investment, SMBs need adequate support and training from the equipment supplier:
a) Comprehensive Training
Operators and maintenance staff require thorough training covering machine operation, safety procedures, routine maintenance tasks, and basic troubleshooting. Effective training ensures the equipment is used correctly and efficiently from day one.
b) Reliable Technical Support
Access to responsive technical support (phone, online, or field service) is crucial for quickly resolving any operational issues or unexpected downtime. SMBs should partner with suppliers known for reliable after-sales service. Look for options like remote diagnostics which can expedite problem-solving.
c) Spare Parts Availability
Ensure the supplier maintains adequate stock of critical spare parts and can deliver them promptly to minimize potential downtime. Understanding the recommended spare parts list is essential for proactive maintenance planning.
d) Continuous Improvement Partnership
A good supplier relationship extends beyond installation. Look for partners willing to discuss potential upgrades, process optimization, or adapting the line to future business needs, ensuring the system continues to provide value long-term.
8. Conclusion: Investing Wisely in Coil Packaging
Steel coil packing lines are a critical investment for protecting product quality and ensuring safe transport. For small and medium-sized businesses, the most effective approach is through customized solutions designed to meet their specific operational needs, budget constraints, and facility limitations. By focusing on flexible and adjustable designs, appropriate levels of cost-effective automation, space efficiency, and scalability, SMBs can significantly enhance packing productivity, reduce operational costs, minimize product damage, and maintain consistent quality.
Collaborating with an experienced equipment provider capable of understanding SMB challenges and delivering tailored, well-supported packing lines allows these businesses to make a smart investment that strengthens their competitiveness and provides lasting value as they grow.