Steel Coil Packing Lines: From Fundamentals to Future Innovations (Comprehensive Guide)
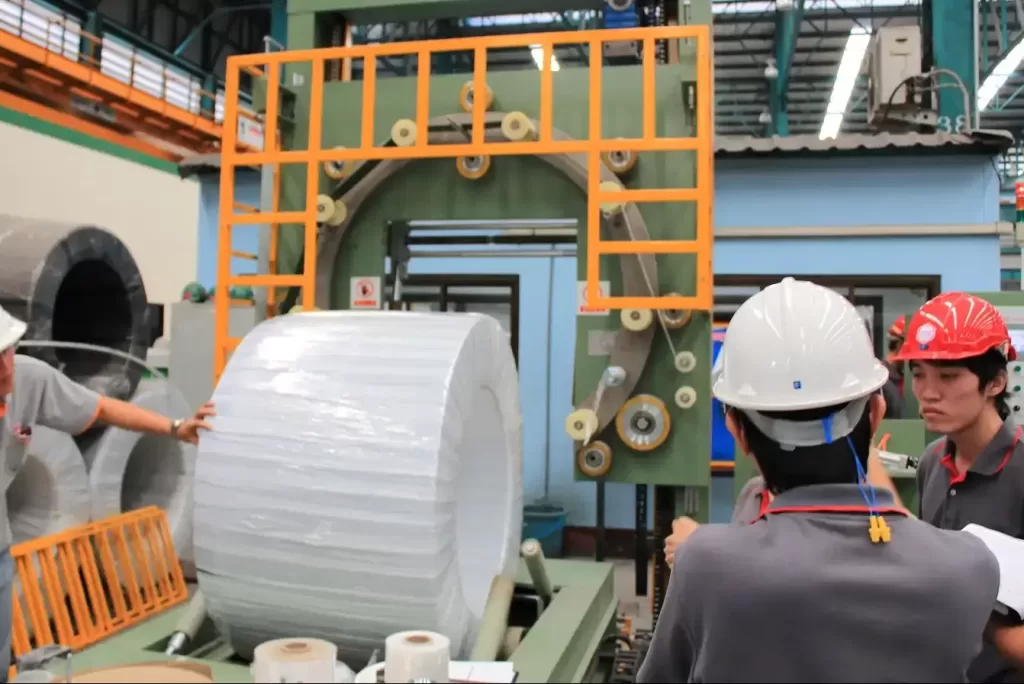
Understanding Steel Coil Packaging
The global steel industry forms the backbone of numerous sectors, including construction, automotive manufacturing, and energy production. Central to this industry is the steel coil, a vital component in the supply chain. However, steel coils are inherently large, heavy, and susceptible to environmental factors like moisture and physical damage. Therefore, effective packaging is not just a logistical necessity but a critical factor in preserving coil quality during storage and transportation. This is the essential role performed by steel coil packing lines.
A steel coil packing line represents a specialized, often automated system engineered to address the unique challenges of packaging these substantial products. These lines ensure coils are securely wrapped, strapped, and shielded from corrosion, contaminants, and handling impacts. Historically a manual, labor-intensive task, steel coil packaging has evolved significantly with technology. Modern systems leverage automation to deliver consistent, high-quality packaging with minimal human intervention, enhancing both efficiency and safety.
This guide, "Mastering Steel Coil Packing Lines: From Fundamentals to Future Innovations," offers a comprehensive exploration of the processes, technologies, and best practices defining contemporary steel coil packaging. Whether you are a steel producer, logistics professional, engineer, or manager within the industry, understanding the intricacies of these systems is vital for optimizing operational efficiency, reducing costs, and maintaining product integrity.
Throughout this guide, we will dissect the essential components of a typical steel coil packing line, compare manual and automated systems, and detail best practices for peak performance. You'll gain insights into the latest technological innovations revolutionizing efficiency and reliability.
We will thoroughly examine safety considerations, paramount when handling heavy steel coils, and discuss the importance of adhering to industry standards and regulations. Furthermore, we'll analyze cost efficiency and return on investment (ROI), crucial factors for businesses striving to maintain high packaging standards while managing expenses.
Finally, we look toward the horizon, identifying emerging trends like AI integration, smart systems, and sustainable practices that are shaping the future of steel coil packaging. This guide serves as an instructional resource for both industry newcomers and seasoned professionals aiming to stay informed in a dynamic field. Let's delve into the art and science of steel coil packaging.
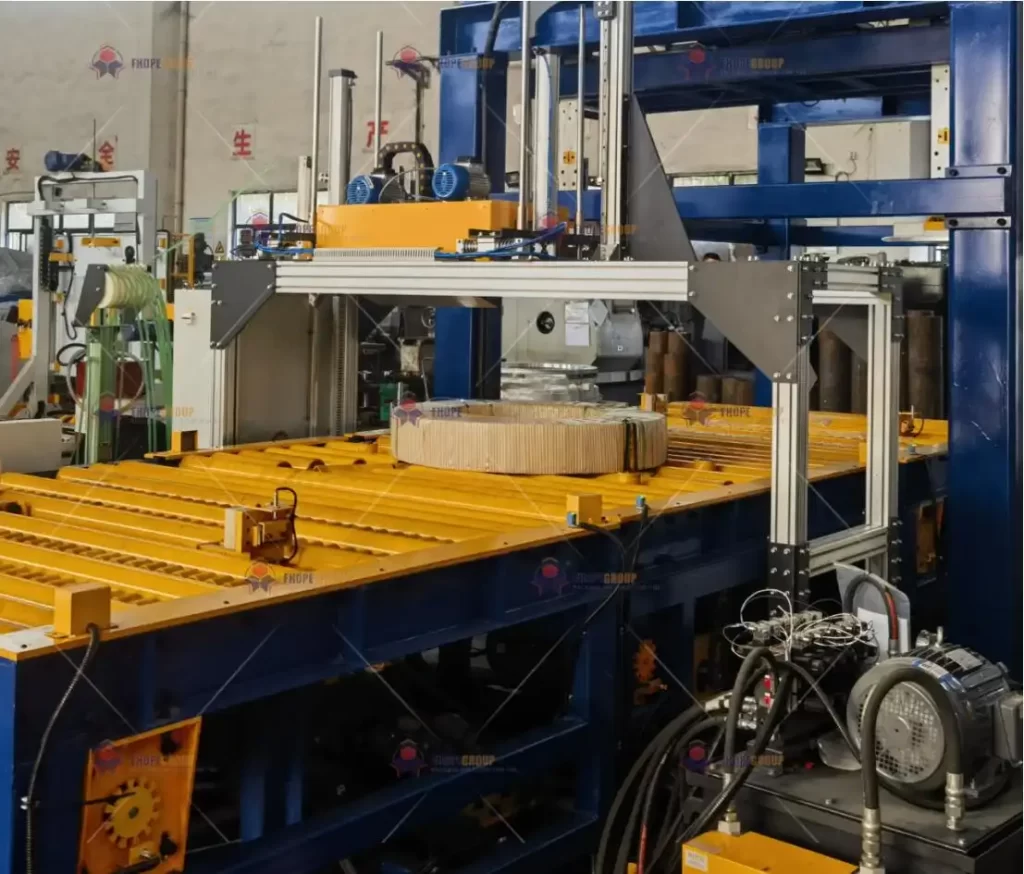
1. Introduction to Steel Coil Packing Lines: A Comprehensive Overview
Steel coil packaging transcends mere logistics; it's a vital process safeguarding valuable materials, ensuring operational safety, and optimizing supply chain efficiency. This first section lays the groundwork for understanding steel coil packing lines, offering an in-depth look at their purpose, core processes, and indispensable role in the modern steel industry.
At its essence, a steel coil packing line is engineered to handle steel coils of diverse sizes, weights, and specifications, ensuring they are packaged securely for both storage and transit. The typical packaging sequence involves multiple stages—wrapping, strapping, and often labeling—each contributing to a stable and protected package. These steps shield the coil from environmental threats like moisture (leading to rust), corrosion, and physical damage during handling and shipping.
Historically, steel coil packaging was a demanding, manual endeavor. Workers laboriously applied protective materials such as VCI (Volatile Corrosion Inhibitor) paper or film, stretch wrap, and metal straps. These manual methods were not only slow and inconsistent but also posed significant safety hazards, requiring personnel to manipulate heavy coils in potentially dangerous conditions.
The advent of automation has revolutionized steel coil packaging. Contemporary packing lines integrate sophisticated technologies that minimize human intervention while significantly boosting the speed, accuracy, consistency, and safety of the entire process. Automated systems employ advanced sensors, robust conveyor systems, turntables, and robotic elements to wrap and strap coils uniformly, guaranteeing optimal packaging integrity every time.
A key advantage of automated steel coil packing lines is the capacity for customization. Packaging processes can be tailored to meet specific customer or end-use requirements. Factors like the type of steel, its surface sensitivity, and the destination's climate influence the choice of materials and methods. High-speed strapping systems (using PET or steel straps), advanced coil wrapping machines applying stretch film or VCI materials, and efficient conveyor logistics combine to create a seamless, automated workflow.
Packaging materials themselves are critical. Common choices include durable polyethylene (PE) stretch wraps, high-strength steel or polyester (PET) straps, and specialized VCI films or papers that actively combat corrosion during extended storage or sea transport. Material selection hinges on the coil's dimensions, weight, value, and the anticipated environmental exposure during its journey.
Furthermore, the significance of proper coil packing extends beyond physical protection. Securely packaged steel coils are inherently easier and safer to handle, stack, and transport, reducing the risk of accidents and product loss. For businesses, this translates directly into lower insurance costs, minimized damage claims, reduced rework expenses, and ultimately, enhanced customer satisfaction—a crucial differentiator in the competitive steel market.
This section serves as an introduction to the detailed functioning of steel coil packing lines. We'll touch upon the types of machinery involved, common operational challenges, and the industry standards governing steel coil packaging. Whether you aim to implement a new system or enhance your current operations, grasping these fundamentals is essential.
By understanding the basics presented here, you'll be well-prepared for the more advanced topics in subsequent sections. You will appreciate why efficient, reliable, and safe packaging is not merely a logistical function but a strategic competitive advantage in the demanding steel industry.
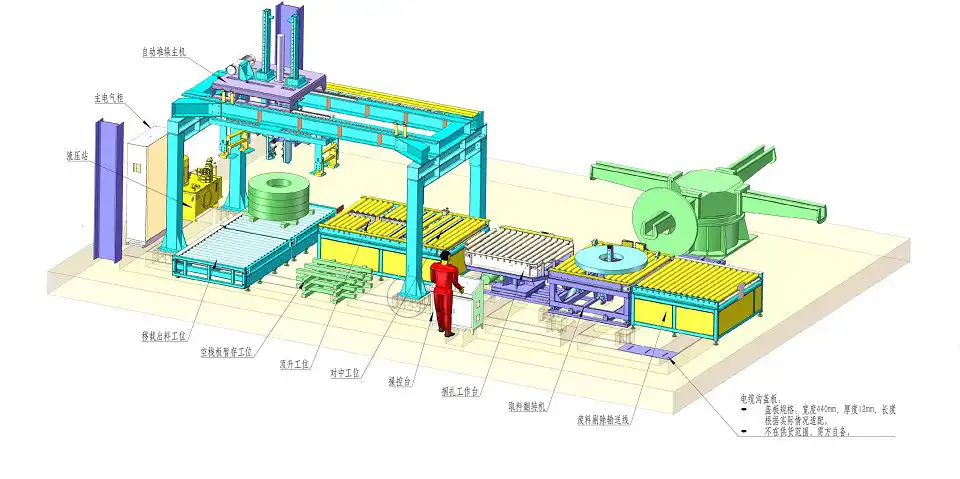
2. Essential Components of a Steel Coil Packing Line
A steel coil packing line is a sophisticated assembly of interconnected components, each engineered to perform specific tasks that ensure the efficient and secure packaging of steel coils. Understanding the function and interplay of these essential components is crucial for optimizing line performance, guaranteeing product safety, and adhering to industry packaging standards. This section details the key elements of a typical steel coil packing line.
2.1. Coil Loading and Unloading Stations
The packaging process begins with the safe and efficient introduction of coils onto the line. Coil loading stations are designed to handle the substantial weight and varying dimensions of steel coils, positioning them correctly for subsequent packaging steps.
- Coil Lifting Devices: Mechanisms like hydraulic scissor lifts, coil cars, or overhead cranes equipped with C-hooks or coil grabs safely place coils onto the initial conveyor or turntable, minimizing manual handling and associated risks.
- Automated Loading Mechanisms: Advanced systems utilize sensors for precise coil detection and alignment, along with robotic arms or pusher mechanisms, to accurately place coils, enhancing speed and reducing placement errors.
Conversely, unloading stations manage the efficient and safe removal of fully packaged coils from the line, often using automated systems to transfer them to storage areas or transport vehicles.
2.2. Coil Wrapping Machines
Coil wrapping machines are central to the packing line, applying the primary protective layer—typically stretch film, VCI film, or paper—around the steel coil. This wrapping shields the coil from moisture, dust, and surface damage while also helping to stabilize the coil structure.
- Types of Wrappers: Horizontal orbital wrappers are common for steel coils, rotating the wrapping material around the coil as it passes through the machine's ring or as the coil sits on a turntable. Vertical wrapping systems may also be used, especially for eye-to-sky packaging. The choice depends on coil orientation and packaging requirements.
- Wrapping Materials: Common materials include standard PE stretch film, high-performance reinforced films, VCI-impregnated films or papers for corrosion prevention, and sometimes protective papers or boards.
- Automatic Tension Control: Ensures consistent film stretch and application force, preventing loose wraps that offer poor protection or overly tight wraps that could damage sensitive coil edges or waste material.
- Edge Protection Applicators: Integrated systems can automatically apply protective materials (like cardboard or plastic profiles) to the coil edges before or during wrapping to prevent damage from strapping or handling.
2.3. Strapping Systems
After wrapping, strapping systems secure the coil and its protective wrapping, maintaining package integrity during handling, storage, and transport. Straps prevent the coil from unwinding and keep the wrapping material firmly in place.
- Automatic Strapping Machines: Essential in modern lines, these machines rapidly apply straps either radially (around the circumference) or axially (through the eye), tensioning, sealing (usually via heat or friction weld for PET, or crimping for steel), and cutting the strap automatically.
- Strapping Materials: High-tensile steel strapping is used for very heavy or demanding applications. Polyester (PET) strapping offers comparable strength for many applications, is lighter, safer to handle, resistant to rust, and often more cost-effective and recyclable. Polypropylene (PP) strap is suitable for lighter coils.
- Tension Control and Strap Placement: Precise control ensures straps are tight enough to secure the load without damaging the coil or wrap. Automated systems allow for programmable strap numbers and positions based on coil size and requirements.
2.4. Coil Turntables and Tilters
These components facilitate handling and orientation during the packaging process.
- Turntables: Rotating platforms allow coils to be turned 90, 180, or 360 degrees, enabling wrapping or strapping operations on different sides or facilitating transfer between conveyor sections.
- Tilters (Upenders/Downenders): Used to change the coil's orientation between eye-to-sky (vertical eye) and eye-to-horizon (horizontal eye), depending on packaging, storage, or transport requirements.
2.5. Conveyor Systems
Conveyor systems are the arteries of the packing line, transporting coils smoothly between stations. They are crucial for maintaining workflow and minimizing manual handling.
- Types of Conveyors: Heavy-duty roller conveyors and chain conveyors are typically used for steel coils due to their robustness and ability to handle significant weight. Belt conveyors may be used in specific sections, like labeling.
- Integrated Sensors and Controls: Photo-eyes and proximity sensors detect coil presence and position, coordinating movement between stations, preventing collisions, and ensuring coils are correctly aligned for each process. Variable speed drives allow for optimized flow control.
2.6. Labeling and Marking Systems
Once packaged, coils require clear identification for inventory management, tracking, and quality control. Labeling systems apply durable, informative labels.
- Automatic Label Applicators: Print-and-apply systems automatically generate and affix labels with essential data (e.g., coil ID, weight, dimensions, grade, customer info, barcodes, QR codes) onto the wrapped coil surface or tag.
- Marking Systems: Inkjet or laser marking systems can apply information directly onto the coil surface (if permissible before wrapping) or onto straps or tags.
- Data Integration: Systems are often linked to the plant's Manufacturing Execution System (MES) or Enterprise Resource Planning (ERP) system to ensure label accuracy and facilitate real-time tracking.
2.7. Control and Monitoring Systems (HMI/SCADA)
The brain of the automated packing line, control systems coordinate all components and provide operators with monitoring and control capabilities.
- Programmable Logic Controllers (PLCs): Coordinate the sequence, timing, and actions of all machines and conveyors on the line.
- Human-Machine Interface (HMI): Touchscreen panels provide operators with a graphical interface to monitor the line status, adjust settings (e.g., wrap programs, strap tension), troubleshoot issues, and receive alarms.
- Supervisory Control and Data Acquisition (SCADA): More advanced systems offer centralized monitoring, control, data logging, and reporting for the entire line, often integrating with higher-level plant systems.
- Safety Integration: Control systems incorporate safety circuits, emergency stops, light curtains, and safety interlocks to ensure worker protection.
2.8. Conclusion
Mastering the function of each essential component—from coil loading to wrapping, strapping, conveying, labeling, and control—is fundamental to designing, operating, and optimizing an effective steel coil packing line. When these components are integrated seamlessly into a well-designed automated system, manufacturers can achieve significant gains in packaging quality, throughput, safety, and cost efficiency. The next section will compare the merits and drawbacks of manual versus automated approaches.
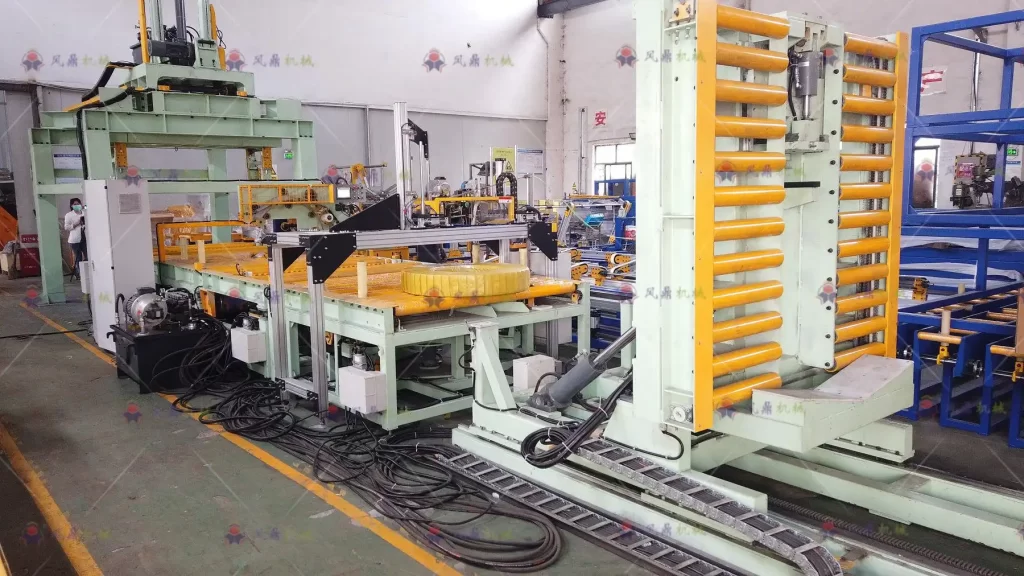
3. Manual vs. Automated Steel Coil Packaging: Key Differences and Considerations
The evolution of steel coil packaging mirrors broader industrial trends, moving from predominantly manual, labor-intensive methods towards highly efficient, automated systems. Both approaches have distinct characteristics, advantages, and disadvantages. Understanding these key differences is crucial for manufacturers when selecting or upgrading their packaging systems to align with operational scale, budget, safety requirements, and long-term strategic goals. This section provides a comparative analysis of manual and automated steel coil packaging.
3.1. Manual Steel Coil Packaging
Manual packaging involves workers performing most or all packaging tasks by hand or with basic hand tools. While less common in large-scale, modern facilities, it remains relevant in certain contexts.
a. Process Overview
- Workers manually apply protective wraps (like VCI paper or stretch film) around the coil, often using handheld dispensers or simple wrapping aids.
- Straps (steel or PET) are applied using manual tensioners, sealers, and cutters. This typically requires significant physical effort.
- Labels or tags are applied by hand.
- Coil handling (lifting, positioning) might involve basic aids like cranes or forklifts, but the precise positioning for wrapping/strapping often requires manual adjustment.
b. Advantages of Manual Packaging
- Lower Initial Investment: The primary advantage is significantly lower upfront capital cost compared to automated lines. This makes it feasible for smaller operations, low-volume producers, or businesses with tight budgets.
- Flexibility: Manual processes can easily adapt to non-standard coil sizes, shapes, or unique packaging requirements without complex reprogramming. Ideal for highly variable product mixes or custom orders.
- Simpler Maintenance: Hand tools require less specialized maintenance compared to complex automated machinery.
c. Challenges of Manual Packaging
- High Labor Costs: Relies heavily on manpower, leading to substantial ongoing labor expenses (wages, benefits, training). Efficiency is directly tied to workforce availability and skill.
- Slow Throughput: Manual processes are inherently slower than automated ones, limiting overall production capacity and potentially creating bottlenecks.
- Inconsistent Quality: Achieving uniform wrap tension, strap placement, and overall package quality is difficult manually. Variability can compromise coil protection and appearance.
- Significant Safety Risks: Manual handling of heavy coils and use of strapping tools increases the risk of musculoskeletal injuries, cuts, and accidents. Ergonomic challenges are prominent.
- Material Waste: Less precise application often leads to higher consumption of wrapping and strapping materials compared to optimized automated systems.
3.2. Automated Steel Coil Packaging
Automated systems utilize machinery to perform most or all packaging tasks with minimal human intervention, offering solutions to many manual packaging challenges.
a. Process Overview
- Coils are automatically loaded and transported via conveyors.
- Automated wrapping machines apply film or paper with pre-set, controlled tension and overlap.
- Automated strapping machines apply, tension, seal, and cut straps at programmed locations.
- Integrated labeling systems print and apply labels automatically.
- The entire process is typically overseen via an HMI, requiring only supervisory labor.
b. Advantages of Automated Packaging
- Increased Speed and Throughput: Automation dramatically increases the number of coils packaged per hour, boosting overall plant capacity and efficiency.
- Consistent Quality: Machines apply wraps and straps with high precision and repeatability, ensuring uniform package quality and optimal coil protection.
- Reduced Labor Costs: Significantly lowers reliance on manual labor, leading to long-term operational cost savings despite higher initial investment.
- Improved Safety: Minimizes manual handling of heavy coils and interaction with potentially hazardous machinery components, drastically reducing workplace accident risks. Automated systems incorporate safety features like guards, interlocks, and E-stops.
- Optimized Material Usage: Precise control over film stretch and strap application minimizes material waste, contributing to cost savings and sustainability.
- Data Integration and Tracking: Automated lines easily integrate with plant control systems (MES/ERP) for better process monitoring, data collection (efficiency, downtime, material use), and product traceability.
c. Challenges of Automated Packaging
- High Initial Investment: The primary barrier is the significant upfront cost of purchasing, installing, and commissioning automated equipment.
- Maintenance Requirements: Automated systems require skilled maintenance personnel and regular preventive maintenance schedules to ensure reliability and minimize downtime. Repairs can be complex and costly.
- Less Flexibility (Potentially): While modern systems are increasingly adaptable, highly customized or frequently changing packaging needs might require significant reprogramming or adjustments, potentially causing delays compared to manual flexibility.
- Space Requirements: Automated lines typically require more floor space than manual workstations.
3.3. Cost Comparison Summary
- Manual: Low CapEx (Capital Expenditure), High OpEx (Operational Expenditure - primarily labor). Suitable for low volume, high variability, tight budgets.
- Automated: High CapEx, Lower OpEx (reduced labor, optimized materials). Favorable ROI (Return on Investment) for medium to high volume operations focused on consistency, speed, and safety.
3.4. Choosing the Right System
The optimal choice between manual and automated steel coil packaging depends heavily on specific operational factors:
- Production Volume: Higher volumes generally justify the investment in automation due to significant throughput gains and labor savings.
- Budget: Initial capital availability is often the deciding factor for smaller companies.
- Product Mix: Highly standardized products benefit most from automation, while highly variable or custom products might favor manual flexibility or require more sophisticated (and expensive) automated solutions.
- Safety Priorities: Operations prioritizing the reduction of manual handling risks will strongly favor automation.
- Quality Requirements: If consistent, high-quality packaging is paramount (e.g., for sensitive surfaces or demanding customers), automation is superior.
- Long-Term Strategy: Companies planning for growth and efficiency improvements will typically lean towards automation.
3.5. Conclusion
While manual steel coil packaging offers lower entry costs and flexibility, automated systems provide compelling advantages in speed, consistency, safety, and long-term cost efficiency, particularly for medium to large-scale producers. The trend clearly favors automation as technology advances and competitive pressures mount. Evaluating the factors outlined above will help manufacturers make an informed decision that best aligns with their operational needs and strategic objectives. The following section will delve into best practices for optimizing the efficiency of whichever system is chosen.
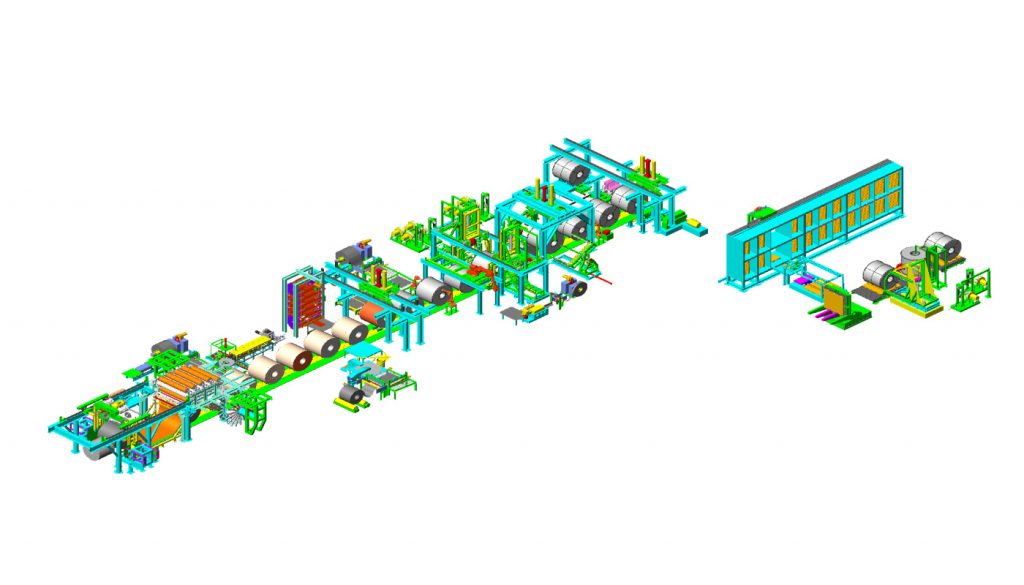
4. Optimizing Efficiency: Best Practices in Steel Coil Packaging
Maximizing the efficiency of steel coil packaging operations is paramount for controlling costs, meeting production targets, ensuring timely deliveries, and maintaining a competitive edge. Whether employing manual methods, semi-automated systems, or fully automated lines, implementing best practices can yield significant improvements in productivity, resource utilization, and overall performance. This section outlines key strategies and practices to enhance the efficiency of steel coil packaging processes.
4.1. Understanding and Tracking Key Efficiency Metrics (KPIs)
Effective optimization begins with measurement. Identifying and consistently tracking Key Performance Indicators (KPIs) provides crucial insights into current performance and highlights areas for improvement.
- Occupational Safety and Health Administration (OSHA) (USA): Sets and enforces workplace safety standards, including specific regulations for machine guarding (29 CFR 1910.212), control of hazardous energy (LOTO - 29 CFR 1910.147), material handling, and PPE.
- European Machinery Directive (EU): Mandates essential health and safety requirements (EHSRs) for machinery placed on the EU market. Compliance often involves adherence to harmonized standards (e.g., EN ISO 12100 for risk assessment, EN ISO 13849 for safety-related control systems). Requires CE marking.
- International Organization for Standardization (ISO): Develops globally recognized standards relevant to machinery safety, including:
- ISO 12100: Safety of machinery — General principles for design — Risk assessment and risk reduction.
- ISO 13849: Safety of machinery — Safety-related parts of control systems.
- ISO 13857: Safety of machinery — Safety distances to prevent hazard zones being reached by upper and lower limbs.
- National and Local Regulations: Specific countries or regions may have additional safety regulations that must be followed.
6.4. Fostering a Safety Culture
Beyond rules and procedures, creating a strong safety culture where safety is prioritized by everyone, from management to frontline workers, is essential.
- Management Commitment: Leadership must visibly demonstrate commitment to safety through resource allocation, policy enforcement, and active participation.
- Employee Involvement: Encourage workers to report hazards, suggest safety improvements, and participate in safety committees or audits.
- Incident Reporting and Investigation: Implement a non-punitive system for reporting all incidents and near misses. Conduct thorough investigations to identify root causes and implement corrective actions to prevent recurrence.
- Continuous Improvement: Treat safety as an ongoing process. Regularly review safety performance, update risk assessments, and adapt procedures based on new information or changes in operations.
6.5. Conclusion
Safety and compliance are integral components of successful steel coil packaging operations. By proactively identifying risks, implementing robust engineering and administrative controls, ensuring adherence to regulations, providing thorough training, and cultivating a strong safety culture, manufacturers can protect their workforce, prevent costly disruptions, and operate responsibly and sustainably. The financial implications and return on investment considerations for these systems will be discussed next.
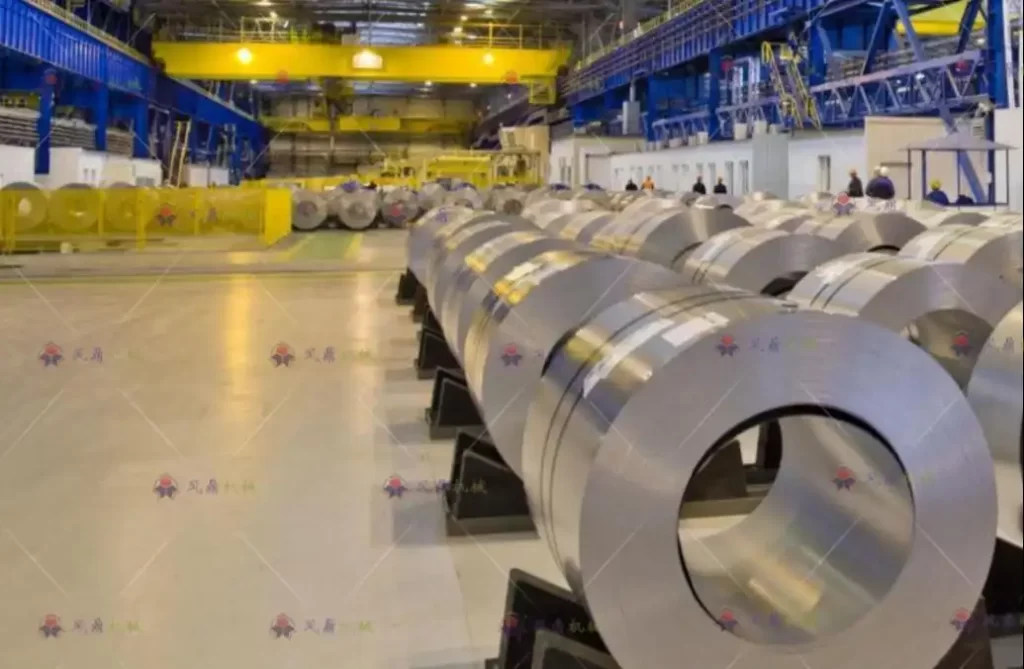
7. Analyzing Cost Efficiency and ROI in Steel Coil Packaging Lines
Implementing or upgrading a steel coil packaging line represents a significant financial undertaking. Therefore, a thorough analysis of cost efficiency and a clear understanding of the potential Return on Investment (ROI) are essential for justifying the expenditure and ensuring the system contributes positively to the company's financial health. This section examines the various cost components, strategies for enhancing cost efficiency, and methods for evaluating the ROI of steel coil packaging investments.
7.1. Key Cost Components
A comprehensive cost analysis must consider both initial investment and ongoing operational expenses.
- Capital Expenditure (CapEx):
- Equipment Purchase: The primary cost, including wrapping machines, strapping systems, conveyors, turntables, tilters, safety guarding, control systems (PLCs, HMIs), and potentially robotics or AGVs. Automated lines have significantly higher CapEx than manual setups.
- Installation and Commissioning: Costs associated with site preparation, mechanical and electrical installation, system integration, programming, and start-up testing.
- Training: Initial training costs for operators and maintenance personnel on the new equipment.
- Operational Expenditure (OpEx):
- Labor: Wages, benefits, and overhead for operators, maintenance staff, and supervisors. Automation significantly reduces direct operator labor costs compared to manual lines.
- Consumable Materials: Ongoing costs for stretch film, VCI materials, strapping (steel or PET), seals/clips, labels, ink, edge protectors, etc.
- Energy: Electricity consumption of motors, heaters (for sealing), controls, lighting, etc.
- Maintenance and Spare Parts: Costs for routine preventive maintenance, repairs, replacement parts, and potential service contracts.
- Downtime Costs: Lost production revenue and associated costs when the line is unexpectedly down.
- Indirect Costs:
- Floor Space: Opportunity cost or rental cost of the factory space occupied by the line.
- Waste Disposal: Costs associated with disposing of packaging waste or scrap.
- Insurance: Premiums potentially affected by safety records and equipment value.
- Quality Costs: Costs related to damaged products due to inadequate packaging (rework, scrap, customer claims).
7.2. Strategies for Improving Cost Efficiency
Optimizing costs involves addressing multiple factors across the system's lifecycle.
- Right-Sizing Automation: Choose a level of automation appropriate for the production volume and complexity. Over-automating a low-volume line might not provide a good ROI, while under-automating a high-volume line leads to high labor costs and bottlenecks.
- Optimizing Material Usage:
- Utilize automated systems with precise control over film pre-stretch and tension to minimize film consumption per coil.
- Select the most cost-effective strapping material (e.g., PET vs. steel) that meets performance requirements.
- Regularly evaluate and test new, potentially more efficient or cost-effective packaging materials.
- Minimize waste during material loading and changeovers.
- Maximizing Energy Efficiency:
- Specify energy-efficient components (motors, drives) when purchasing equipment.
- Implement energy-saving modes during idle periods.
- Ensure proper maintenance (e.g., clean motors, lubricated parts) to prevent increased energy draw.
- Implementing Effective Maintenance Strategies:
- A robust Preventive Maintenance (PM) program is crucial to minimize costly unplanned downtime and extend equipment life.
- Consider Predictive Maintenance (PdM) technologies (vibration analysis, thermal imaging, oil analysis) to anticipate failures and schedule repairs efficiently.
- Maintain an adequate inventory of critical spare parts to expedite repairs.
- Reducing Downtime: Track downtime causes meticulously and implement corrective actions. Optimize changeover procedures (SMED). Ensure reliable supply of coils and materials to the line.
- Improving Labor Efficiency: Provide effective training, clear SOPs, and ergonomic tools/workstations. Utilize automation to reallocate labor to higher-value tasks.
7.3. Evaluating Return on Investment (ROI)
ROI analysis helps determine the financial viability of investing in a new or upgraded packaging line. It compares the net financial benefits generated by the investment against its total cost.
a. Calculation Methods
- Simple ROI:
ROI (%) = [(Gain from Investment - Cost of Investment) / Cost of Investment] x 100
(Gain typically includes annual savings in labor, materials, reduced damage, plus potentially increased revenue from higher throughput). - Payback Period:
Payback Period (Years) = Initial Investment / Annual Savings (or Cash Flow)
Indicates how quickly the initial investment is recovered. - Net Present Value (NPV): Considers the time value of money by discounting future cash flows back to their present value. A positive NPV generally indicates a worthwhile investment.
- Internal Rate of Return (IRR): The discount rate at which the NPV of the investment equals zero. If IRR exceeds the company's required rate of return, the project is typically considered acceptable.
b. Key Factors Influencing ROI
- Labor Cost Savings: A primary driver for automation ROI.
- Throughput Increase: Higher production capacity can lead to increased sales revenue.
- Material Cost Reduction: Savings from optimized film/strap usage.
- Improved Quality / Reduced Damage: Lower costs associated with product damage claims, rework, or scrap.
- Enhanced Safety: Reduced costs associated with accidents ( LTA, insurance premiums, potential fines).
- Equipment Lifespan and Reliability: Longer-lasting, reliable equipment yields returns over a longer period.
c. Intangible Benefits
While harder to quantify, consider intangible benefits like improved worker morale (due to better safety and ergonomics), enhanced company image (modern, efficient operations), and greater operational flexibility.
7.4. Conclusion
Achieving optimal cost efficiency and a strong ROI from a steel coil packaging line requires a holistic approach. It involves careful initial planning and equipment selection, diligent operational management focused on minimizing waste and downtime, effective maintenance, and continuous monitoring of performance against financial goals. By thoroughly analyzing costs, implementing efficiency strategies, and rigorously evaluating ROI using appropriate financial metrics, manufacturers can ensure their packaging operations are not just functional but also financially sound and contribute significantly to overall business success. The final section will look ahead at future trends shaping this critical industrial process.

8. The Future of Steel Coil Packaging: Trends and Emerging Technologies
The steel coil packaging industry stands at an inflection point, driven by converging forces of technological innovation, escalating demands for efficiency and sustainability, and the transformative potential of data. Looking ahead, several key trends and emerging technologies are poised to redefine how steel coils are packaged, handled, and tracked. This final section explores the future landscape, highlighting the innovations that will shape the next generation of steel coil packaging systems.
8.1. Hyper-Automation and Intelligent Systems
Automation will become even more sophisticated, integrated, and intelligent.
- AI-Powered Optimization: Beyond predictive maintenance, AI will increasingly optimize packaging parameters (wrap patterns, strap placement/tension) in real-time based on specific coil characteristics (dimensions, grade, surface sensitivity detected by sensors) and destination requirements, ensuring optimal protection with minimal material usage.
- Autonomous Operations: Expect more fully autonomous lines requiring minimal human oversight. This includes self-adjusting machines, automated troubleshooting routines, and integration with AGVs/AMRs for end-to-end material flow from production to warehousing/shipping without manual intervention.
- Enhanced Robotics and Vision Systems: Robots will become more dexterous and adaptable, capable of handling a wider variety of tasks. AI-driven vision systems will offer more sophisticated inspection capabilities, identifying subtle defects and ensuring near-perfect packaging quality.
8.2. Data-Centric Ecosystems (IIoT and Digital Twins)
Data will be the lifeblood of future packaging operations, enabled by pervasive connectivity.
- Ubiquitous IIoT Integration: Nearly every component on the packaging line will be sensor-equipped and connected, generating vast amounts of data on performance, condition, and material flow.
- Advanced Analytics and Cloud Platforms: Cloud-based platforms will aggregate and analyze data from multiple lines or even multiple plants, providing deeper insights into performance bottlenecks, enabling benchmarking, and facilitating enterprise-level optimization strategies.
- Digital Twins: Creating virtual replicas (digital twins) of the physical packaging line will allow manufacturers to simulate changes, test new configurations, optimize parameters, and train operators in a risk-free virtual environment before implementing changes on the actual line.
- Blockchain for Supply Chain Traceability: For high-value coils or regulated industries, blockchain technology could provide an immutable record of the coil's journey, including packaging details and sensor data (e.g., temperature, shock), enhancing security and transparency.
8.3. Sustainability as a Core Driver
Environmental responsibility will increasingly influence technology and material choices.
- Circular Economy Materials: Increased focus on using packaging materials (films, straps) with high recycled content and designing packages for easy disassembly and recycling at the destination. Development of closed-loop systems for packaging materials may emerge.
- Biodegradable and Bio-based Materials: Continued innovation in biodegradable VCI and wrapping materials that offer comparable performance to traditional plastics but with a significantly lower environmental impact.
- Material Reduction Technologies: Continued development of ultra-thin, high-strength films and optimized wrapping/strapping techniques driven by AI to minimize the absolute quantity of material used per package.
- Energy Harvesting and Ultra-Efficient Machinery: Integration of energy recovery systems and designs that drastically reduce the energy footprint of packaging operations, potentially moving towards energy-neutral systems in some cases.
8.4. Modular, Flexible, and Scalable Systems
Packaging lines will need to adapt quickly to changing market demands.
- Modular Design: Equipment designed as interchangeable modules (e.g., different types of wrappers, strappers, labeling units) that can be easily added, removed, or reconfigured to adapt the line's capabilities to new products or capacity requirements.
- Increased Flexibility: Systems capable of handling a wider range of coil sizes, weights, and packaging specifications with minimal manual setup or adjustment, facilitated by robotics and AI-driven parameter settings.
- Scalability: Designs that allow for incremental capacity increases by adding parallel modules or upgrading existing ones without requiring a complete line replacement.
8.5. Enhanced Human-Machine Collaboration
While automation increases, the human role will evolve towards supervision, optimization, and handling exceptions.
- Advanced HMIs and Augmented Reality (AR): More intuitive interfaces, potentially incorporating AR overlays that provide operators with real-time instructions, diagnostic information, or maintenance guidance directly onto their view of the equipment.
- Cobot Integration: Wider adoption of cobots for tasks requiring a blend of automation and human dexterity or judgment, creating safer and more ergonomic hybrid workstations.
8.6. Conclusion: Embracing the Transformation
The future of steel coil packaging promises systems that are significantly more intelligent, efficient, adaptable, sustainable, and data-driven than today's counterparts. Technologies like AI, IIoT, advanced robotics, and innovative materials are not just incremental improvements but catalysts for fundamental transformation. Manufacturers who proactively embrace these changes, invest strategically in new technologies, and foster a culture of continuous adaptation will be best positioned to thrive. By leveraging these advancements, they can optimize operations, reduce environmental impact, enhance product protection, and meet the increasingly complex demands of the global steel market, securing their competitive advantage in the years to come.

Get Your Best Solution !
- Comprehensive Risk Assessments: Regularly conduct thorough risk assessments of the entire packaging line and associated tasks to identify hazards and evaluate existing control measures.
- Engineering Controls (Elimination/Substitution):
- Prioritize automation to eliminate hazardous manual handling tasks.
- Use appropriate machine guarding (fixed guards, interlocked guards, light curtains, safety mats) to prevent access to dangerous moving parts. Ensure guarding complies with relevant standards (e.g., ISO 13857).
- Incorporate safety-rated components and control systems (e.g., safety PLCs, emergency stops) designed according to standards like ISO 13849-1.
- Design workstations ergonomically to minimize strain.
- Substitute hazardous materials where possible (e.g., using PET strap instead of steel strap can reduce cut risks).
- Administrative Controls:
- Develop and enforce strict Safe Work Procedures (SWPs) for all tasks, including operation, maintenance, and troubleshooting.
- Implement robust Lockout/Tagout (LOTO) procedures for maintenance and servicing activities to prevent unexpected machine start-up. Ensure authorized personnel are properly trained.
- Provide comprehensive, task-specific safety training for all employees, including hazard recognition, proper use of equipment, emergency procedures, and LOTO. Conduct regular refresher training.
- Clear signage indicating hazards, required PPE, and safety procedures.
- Good housekeeping practices (5S) to prevent slips, trips, and falls.
- Personal Protective Equipment (PPE): Mandate and provide appropriate PPE based on risk assessment, which typically includes:
- Hard hats
- Safety glasses or face shields
- Cut-resistant gloves
- Steel-toed safety boots
- High-visibility clothing (if operating near mobile equipment)
- Regular Inspections and Maintenance: Ensure safety devices (E-stops, interlocks, guards) are regularly inspected, tested, and maintained in proper working order as part of the preventive maintenance program.
6.3. Compliance with Standards and Regulations
Adherence to legal and industry standards is crucial. Key regulatory bodies and standards include:
- Occupational Safety and Health Administration (OSHA) (USA): Sets and enforces workplace safety standards, including specific regulations for machine guarding (29 CFR 1910.212), control of hazardous energy (LOTO - 29 CFR 1910.147), material handling, and PPE.
- European Machinery Directive (EU): Mandates essential health and safety requirements (EHSRs) for machinery placed on the EU market. Compliance often involves adherence to harmonized standards (e.g., EN ISO 12100 for risk assessment, EN ISO 13849 for safety-related control systems). Requires CE marking.
- International Organization for Standardization (ISO): Develops globally recognized standards relevant to machinery safety, including:
- ISO 12100: Safety of machinery — General principles for design — Risk assessment and risk reduction.
- ISO 13849: Safety of machinery — Safety-related parts of control systems.
- ISO 13857: Safety of machinery — Safety distances to prevent hazard zones being reached by upper and lower limbs.
- National and Local Regulations: Specific countries or regions may have additional safety regulations that must be followed.
6.4. Fostering a Safety Culture
Beyond rules and procedures, creating a strong safety culture where safety is prioritized by everyone, from management to frontline workers, is essential.
- Management Commitment: Leadership must visibly demonstrate commitment to safety through resource allocation, policy enforcement, and active participation.
- Employee Involvement: Encourage workers to report hazards, suggest safety improvements, and participate in safety committees or audits.
- Incident Reporting and Investigation: Implement a non-punitive system for reporting all incidents and near misses. Conduct thorough investigations to identify root causes and implement corrective actions to prevent recurrence.
- Continuous Improvement: Treat safety as an ongoing process. Regularly review safety performance, update risk assessments, and adapt procedures based on new information or changes in operations.
6.5. Conclusion
Safety and compliance are integral components of successful steel coil packaging operations. By proactively identifying risks, implementing robust engineering and administrative controls, ensuring adherence to regulations, providing thorough training, and cultivating a strong safety culture, manufacturers can protect their workforce, prevent costly disruptions, and operate responsibly and sustainably. The financial implications and return on investment considerations for these systems will be discussed next.
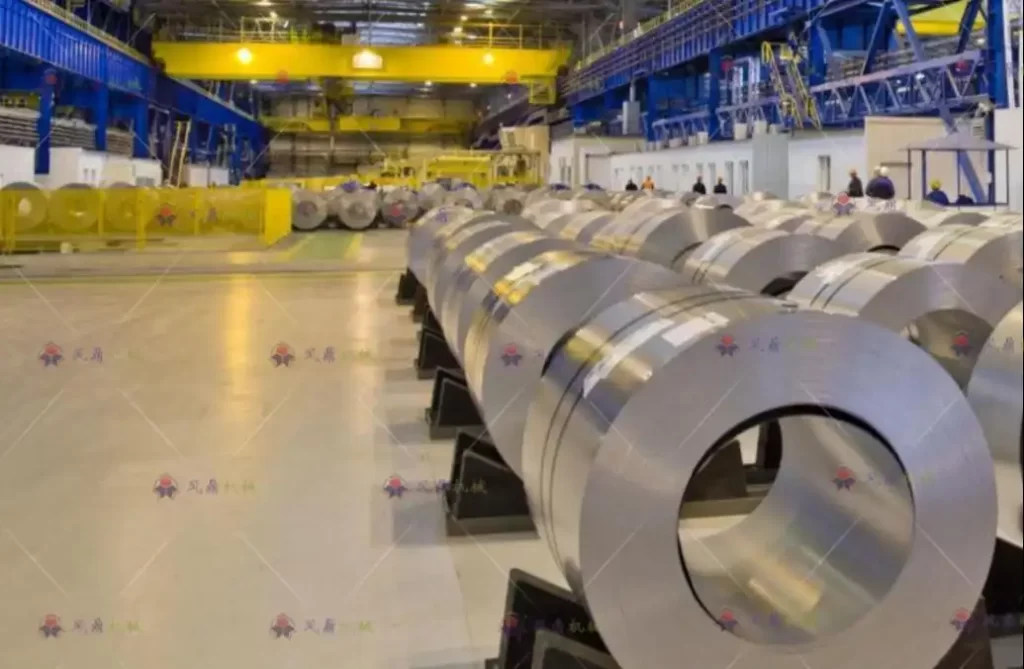
7. Analyzing Cost Efficiency and ROI in Steel Coil Packaging Lines
Implementing or upgrading a steel coil packaging line represents a significant financial undertaking. Therefore, a thorough analysis of cost efficiency and a clear understanding of the potential Return on Investment (ROI) are essential for justifying the expenditure and ensuring the system contributes positively to the company's financial health. This section examines the various cost components, strategies for enhancing cost efficiency, and methods for evaluating the ROI of steel coil packaging investments.
7.1. Key Cost Components
A comprehensive cost analysis must consider both initial investment and ongoing operational expenses.
- Capital Expenditure (CapEx):
- Equipment Purchase: The primary cost, including wrapping machines, strapping systems, conveyors, turntables, tilters, safety guarding, control systems (PLCs, HMIs), and potentially robotics or AGVs. Automated lines have significantly higher CapEx than manual setups.
- Installation and Commissioning: Costs associated with site preparation, mechanical and electrical installation, system integration, programming, and start-up testing.
- Training: Initial training costs for operators and maintenance personnel on the new equipment.
- Operational Expenditure (OpEx):
- Labor: Wages, benefits, and overhead for operators, maintenance staff, and supervisors. Automation significantly reduces direct operator labor costs compared to manual lines.
- Consumable Materials: Ongoing costs for stretch film, VCI materials, strapping (steel or PET), seals/clips, labels, ink, edge protectors, etc.
- Energy: Electricity consumption of motors, heaters (for sealing), controls, lighting, etc.
- Maintenance and Spare Parts: Costs for routine preventive maintenance, repairs, replacement parts, and potential service contracts.
- Downtime Costs: Lost production revenue and associated costs when the line is unexpectedly down.
- Indirect Costs:
- Floor Space: Opportunity cost or rental cost of the factory space occupied by the line.
- Waste Disposal: Costs associated with disposing of packaging waste or scrap.
- Insurance: Premiums potentially affected by safety records and equipment value.
- Quality Costs: Costs related to damaged products due to inadequate packaging (rework, scrap, customer claims).
7.2. Strategies for Improving Cost Efficiency
Optimizing costs involves addressing multiple factors across the system's lifecycle.
- Right-Sizing Automation: Choose a level of automation appropriate for the production volume and complexity. Over-automating a low-volume line might not provide a good ROI, while under-automating a high-volume line leads to high labor costs and bottlenecks.
- Optimizing Material Usage:
- Utilize automated systems with precise control over film pre-stretch and tension to minimize film consumption per coil.
- Select the most cost-effective strapping material (e.g., PET vs. steel) that meets performance requirements.
- Regularly evaluate and test new, potentially more efficient or cost-effective packaging materials.
- Minimize waste during material loading and changeovers.
- Maximizing Energy Efficiency:
- Specify energy-efficient components (motors, drives) when purchasing equipment.
- Implement energy-saving modes during idle periods.
- Ensure proper maintenance (e.g., clean motors, lubricated parts) to prevent increased energy draw.
- Implementing Effective Maintenance Strategies:
- A robust Preventive Maintenance (PM) program is crucial to minimize costly unplanned downtime and extend equipment life.
- Consider Predictive Maintenance (PdM) technologies (vibration analysis, thermal imaging, oil analysis) to anticipate failures and schedule repairs efficiently.
- Maintain an adequate inventory of critical spare parts to expedite repairs.
- Reducing Downtime: Track downtime causes meticulously and implement corrective actions. Optimize changeover procedures (SMED). Ensure reliable supply of coils and materials to the line.
- Improving Labor Efficiency: Provide effective training, clear SOPs, and ergonomic tools/workstations. Utilize automation to reallocate labor to higher-value tasks.
7.3. Evaluating Return on Investment (ROI)
ROI analysis helps determine the financial viability of investing in a new or upgraded packaging line. It compares the net financial benefits generated by the investment against its total cost.
a. Calculation Methods
- Simple ROI:
ROI (%) = [(Gain from Investment - Cost of Investment) / Cost of Investment] x 100
(Gain typically includes annual savings in labor, materials, reduced damage, plus potentially increased revenue from higher throughput). - Payback Period:
Payback Period (Years) = Initial Investment / Annual Savings (or Cash Flow)
Indicates how quickly the initial investment is recovered. - Net Present Value (NPV): Considers the time value of money by discounting future cash flows back to their present value. A positive NPV generally indicates a worthwhile investment.
- Internal Rate of Return (IRR): The discount rate at which the NPV of the investment equals zero. If IRR exceeds the company's required rate of return, the project is typically considered acceptable.
b. Key Factors Influencing ROI
- Labor Cost Savings: A primary driver for automation ROI.
- Throughput Increase: Higher production capacity can lead to increased sales revenue.
- Material Cost Reduction: Savings from optimized film/strap usage.
- Improved Quality / Reduced Damage: Lower costs associated with product damage claims, rework, or scrap.
- Enhanced Safety: Reduced costs associated with accidents ( LTA, insurance premiums, potential fines).
- Equipment Lifespan and Reliability: Longer-lasting, reliable equipment yields returns over a longer period.
c. Intangible Benefits
While harder to quantify, consider intangible benefits like improved worker morale (due to better safety and ergonomics), enhanced company image (modern, efficient operations), and greater operational flexibility.
7.4. Conclusion
Achieving optimal cost efficiency and a strong ROI from a steel coil packaging line requires a holistic approach. It involves careful initial planning and equipment selection, diligent operational management focused on minimizing waste and downtime, effective maintenance, and continuous monitoring of performance against financial goals. By thoroughly analyzing costs, implementing efficiency strategies, and rigorously evaluating ROI using appropriate financial metrics, manufacturers can ensure their packaging operations are not just functional but also financially sound and contribute significantly to overall business success. The final section will look ahead at future trends shaping this critical industrial process.

8. The Future of Steel Coil Packaging: Trends and Emerging Technologies
The steel coil packaging industry stands at an inflection point, driven by converging forces of technological innovation, escalating demands for efficiency and sustainability, and the transformative potential of data. Looking ahead, several key trends and emerging technologies are poised to redefine how steel coils are packaged, handled, and tracked. This final section explores the future landscape, highlighting the innovations that will shape the next generation of steel coil packaging systems.
8.1. Hyper-Automation and Intelligent Systems
Automation will become even more sophisticated, integrated, and intelligent.
- AI-Powered Optimization: Beyond predictive maintenance, AI will increasingly optimize packaging parameters (wrap patterns, strap placement/tension) in real-time based on specific coil characteristics (dimensions, grade, surface sensitivity detected by sensors) and destination requirements, ensuring optimal protection with minimal material usage.
- Autonomous Operations: Expect more fully autonomous lines requiring minimal human oversight. This includes self-adjusting machines, automated troubleshooting routines, and integration with AGVs/AMRs for end-to-end material flow from production to warehousing/shipping without manual intervention.
- Enhanced Robotics and Vision Systems: Robots will become more dexterous and adaptable, capable of handling a wider variety of tasks. AI-driven vision systems will offer more sophisticated inspection capabilities, identifying subtle defects and ensuring near-perfect packaging quality.
8.2. Data-Centric Ecosystems (IIoT and Digital Twins)
Data will be the lifeblood of future packaging operations, enabled by pervasive connectivity.
- Ubiquitous IIoT Integration: Nearly every component on the packaging line will be sensor-equipped and connected, generating vast amounts of data on performance, condition, and material flow.
- Advanced Analytics and Cloud Platforms: Cloud-based platforms will aggregate and analyze data from multiple lines or even multiple plants, providing deeper insights into performance bottlenecks, enabling benchmarking, and facilitating enterprise-level optimization strategies.
- Digital Twins: Creating virtual replicas (digital twins) of the physical packaging line will allow manufacturers to simulate changes, test new configurations, optimize parameters, and train operators in a risk-free virtual environment before implementing changes on the actual line.
- Blockchain for Supply Chain Traceability: For high-value coils or regulated industries, blockchain technology could provide an immutable record of the coil's journey, including packaging details and sensor data (e.g., temperature, shock), enhancing security and transparency.
8.3. Sustainability as a Core Driver
Environmental responsibility will increasingly influence technology and material choices.
- Circular Economy Materials: Increased focus on using packaging materials (films, straps) with high recycled content and designing packages for easy disassembly and recycling at the destination. Development of closed-loop systems for packaging materials may emerge.
- Biodegradable and Bio-based Materials: Continued innovation in biodegradable VCI and wrapping materials that offer comparable performance to traditional plastics but with a significantly lower environmental impact.
- Material Reduction Technologies: Continued development of ultra-thin, high-strength films and optimized wrapping/strapping techniques driven by AI to minimize the absolute quantity of material used per package.
- Energy Harvesting and Ultra-Efficient Machinery: Integration of energy recovery systems and designs that drastically reduce the energy footprint of packaging operations, potentially moving towards energy-neutral systems in some cases.
8.4. Modular, Flexible, and Scalable Systems
Packaging lines will need to adapt quickly to changing market demands.
- Modular Design: Equipment designed as interchangeable modules (e.g., different types of wrappers, strappers, labeling units) that can be easily added, removed, or reconfigured to adapt the line's capabilities to new products or capacity requirements.
- Increased Flexibility: Systems capable of handling a wider range of coil sizes, weights, and packaging specifications with minimal manual setup or adjustment, facilitated by robotics and AI-driven parameter settings.
- Scalability: Designs that allow for incremental capacity increases by adding parallel modules or upgrading existing ones without requiring a complete line replacement.
8.5. Enhanced Human-Machine Collaboration
While automation increases, the human role will evolve towards supervision, optimization, and handling exceptions.
- Advanced HMIs and Augmented Reality (AR): More intuitive interfaces, potentially incorporating AR overlays that provide operators with real-time instructions, diagnostic information, or maintenance guidance directly onto their view of the equipment.
- Cobot Integration: Wider adoption of cobots for tasks requiring a blend of automation and human dexterity or judgment, creating safer and more ergonomic hybrid workstations.
8.6. Conclusion: Embracing the Transformation
The future of steel coil packaging promises systems that are significantly more intelligent, efficient, adaptable, sustainable, and data-driven than today's counterparts. Technologies like AI, IIoT, advanced robotics, and innovative materials are not just incremental improvements but catalysts for fundamental transformation. Manufacturers who proactively embrace these changes, invest strategically in new technologies, and foster a culture of continuous adaptation will be best positioned to thrive. By leveraging these advancements, they can optimize operations, reduce environmental impact, enhance product protection, and meet the increasingly complex demands of the global steel market, securing their competitive advantage in the years to come.
- Cycle Time: The total time taken to package one steel coil, from loading onto the line to unloading the finished package. Reducing cycle time directly increases potential throughput.
- Throughput: The number of coils successfully packaged per unit of time (e.g., coils per hour, coils per shift). This is a primary measure of line productivity.
- Overall Equipment Effectiveness (OEE): A comprehensive metric for automated lines, calculated as Availability x Performance x Quality. OEE provides a holistic view of efficiency, considering downtime, speed losses, and defect rates.
- Downtime Analysis: Tracking the frequency, duration, and causes of line stoppages (e.g., equipment failure, material changes, lack of coils, operator breaks). Minimizing unplanned downtime is critical.
- Material Consumption Rate: Measuring the amount of wrapping film, strapping, labels, and other consumables used per coil or per ton of steel. Optimizing this reduces costs and waste.
- Labor Efficiency: For manual or semi-automated lines, tracking coils packaged per labor hour.
4.2. Best Practices Applicable to Both Manual and Automated Lines
Certain principles enhance efficiency regardless of the level of automation:
- Standardize Work Procedures (SOPs): Develop clear, documented procedures for all packaging tasks, including setup, operation, material handling, quality checks, and changeovers. Consistency reduces errors and improves speed.
- Effective Training Programs: Ensure all personnel (operators, maintenance staff) are thoroughly trained on equipment operation, SOPs, safety protocols, and basic troubleshooting. Cross-training can enhance flexibility.
- Optimize Line Layout and Workflow: Design the physical layout to minimize coil travel distance, eliminate bottlenecks, and ensure smooth flow between stations. Provide adequate space for safe operation and material staging.
- Implement 5S Principles: Apply Sort, Set in Order, Shine, Standardize, and Sustain methodologies to maintain a clean, organized, and efficient workspace. This reduces search times, improves safety, and highlights potential issues.
- Efficient Material Management: Ensure timely availability of correct packaging materials. Implement strategies like Just-in-Time (JIT) inventory or Kanban systems for consumables to prevent line stoppages due to material shortages. Maintain strong supplier relationships.
4.3. Best Practices Specific to Manual Packaging Efficiency
- Ergonomic Workstation Design: Arrange workstations to minimize physical strain. Use adjustable height platforms, anti-fatigue mats, and position tools and materials within easy reach to reduce bending, stretching, and fatigue.
- Utilize Assistive Tools: Employ tools like powered hand wrappers, ergonomic strapping tensioners, and lift assists where feasible to reduce physical effort and improve speed.
- Task Rotation: Rotate workers between different tasks to reduce monotony and the risk of repetitive strain injuries, helping maintain alertness and productivity.
- Clear Material Usage Guidelines: Train workers on the optimal amount of wrap/strap to use per coil type to minimize waste while ensuring adequate protection.
4.4. Best Practices Specific to Automated Packaging Efficiency
- Optimize Machine Settings: Regularly review and fine-tune machine parameters (e.g., wrapper rotation speed, film pre-stretch percentage, strap tension, conveyor speed) for each coil type to maximize speed and minimize material usage without compromising quality.
- Implement Robust Preventive Maintenance (PM): Adhere strictly to a scheduled PM program covering inspections, lubrication, cleaning, and replacement of wear parts. This minimizes unexpected breakdowns, extends equipment life, and maintains optimal performance. Consider predictive maintenance (PdM) using sensors if available.
- Minimize Changeover Times (SMED): If handling various coil sizes/types, apply Single-Minute Exchange of Die (SMED) principles to streamline changeovers. Use quick-release mechanisms, preset adjustments, and efficient procedures to reduce non-productive time. Schedule production runs to minimize frequency of changeovers.
- Leverage Automation Features: Utilize features like automatic fault detection, HMI diagnostics, and performance data logging to quickly identify and resolve issues. Train operators on interpreting system feedback.
- Ensure Proper Sensor Functionality: Regularly clean and check alignment of photo-eyes and other sensors, as dirty or misaligned sensors are common causes of line stoppages.
4.5. Continuous Improvement Culture
- Regular Performance Reviews: Hold regular meetings with operators, maintenance, and management to review KPIs, discuss challenges, and brainstorm improvement ideas.
- Root Cause Analysis (RCA): When inefficiencies or failures occur, conduct thorough RCA (e.g., using Fishbone diagrams or 5 Whys) to identify underlying problems rather than just addressing symptoms.
- Encourage Employee Feedback: Foster an environment where operators feel empowered to suggest improvements, as they often have the best insights into daily operational hurdles.
- Benchmark and Adopt Best Practices: Stay informed about industry trends and technologies. Benchmark performance against similar operations where possible.
4.6. Conclusion
Optimizing the efficiency of a steel coil packing line is an ongoing effort involving meticulous planning, consistent execution of best practices, effective use of technology, and a commitment to continuous improvement. By focusing on key metrics, standardizing processes, maintaining equipment diligently, managing materials wisely, and fostering an engaged workforce, manufacturers can significantly enhance productivity, reduce operational costs, and ensure their packaging operations contribute positively to the bottom line. Next, we explore the exciting technological innovations further propelling efficiency and capability in this field.

Get Your Best Solution !
5. Technological Innovations Shaping Steel Coil Packaging
The steel coil packaging landscape is continually evolving, driven by rapid technological advancements aimed at boosting efficiency, enhancing safety, improving product protection, integrating data, and promoting sustainability. Staying abreast of these innovations is crucial for manufacturers seeking to maintain a competitive advantage. This section explores the cutting-edge technologies and trends currently reshaping steel coil packaging systems.
5.1. Advanced Automation, Robotics, and AI
Automation is moving beyond simple mechanization towards intelligent systems capable of adaptive and complex tasks.
- Robotics Integration: Industrial robots (e.g., articulated arm robots) are increasingly used for tasks requiring high precision, speed, or flexibility, such as coil handling (loading/unloading), precise placement of edge protectors, complex strapping patterns, and palletizing packaged coils.
- Collaborative Robots (Cobots): Designed to work safely alongside humans without extensive guarding, cobots can assist operators with physically demanding or repetitive tasks like material handling or tool positioning, blending the benefits of automation with human oversight and flexibility.
- Artificial Intelligence (AI) and Machine Learning (ML):
- Predictive Maintenance (PdM): AI algorithms analyze sensor data (vibration, temperature, power consumption) to predict potential equipment failures before they occur, allowing for proactive maintenance scheduling, minimizing unplanned downtime, and extending machine life.
- Process Optimization: ML models can analyze historical performance data to identify optimal machine settings (e.g., wrap tension, strap placement) for different coil types and environmental conditions, automatically adjusting parameters for peak efficiency and minimal material waste.
- Vision Systems: AI-powered machine vision systems can inspect coils for defects before packaging, verify correct wrap and strap application, and read codes for tracking, enhancing quality control.
- Fully Integrated and Autonomous Lines: The trend is towards seamless integration of all packaging stages (wrapping, strapping, labeling, weighing, conveying, palletizing) controlled by a central system, minimizing manual touchpoints and maximizing throughput. Autonomous Guided Vehicles (AGVs) or Autonomous Mobile Robots (AMRs) may handle coil transport to and from the line.
5.2. Innovations in Packaging Materials
Material science advancements are leading to more effective, efficient, and sustainable packaging solutions.
- High-Performance Stretch Films: Nanotechnology and multi-layer extrusion create thinner yet stronger films with enhanced puncture resistance, load containment, and clarity. Pre-stretched films reduce material consumption while maintaining secure wrapping.
- Advanced VCI (Volatile Corrosion Inhibitor) Technology: New VCI formulations offer longer-lasting, multi-metal protection. Innovations include VCI emitters integrated directly into stretch films or papers, providing more consistent and effective corrosion prevention, especially crucial for export shipments. Some are becoming biodegradable.
- Reinforced and Sustainable Strapping: High-strength PET strapping continues to gain ground against steel due to safety, recyclability, and resistance to environmental factors. Developments focus on increasing tensile strength and using recycled content. Composite straps offer unique properties combining strength and flexibility.
- Eco-Friendly Alternatives: Research into biodegradable and compostable films (e.g., PLA-based) and papers is ongoing, driven by environmental regulations and corporate sustainability goals. Paper-based wrapping solutions are also being explored as plastic alternatives.
5.3. Smart Packaging Systems and the Industrial Internet of Things (IIoT)
Connectivity and data are transforming packaging lines into intelligent, data-driven assets.
- IIoT-Enabled Sensors: Machines equipped with sensors continuously collect data on operational parameters (speed, tension, temperature, vibration), material consumption, and machine health.
- Real-Time Monitoring and Dashboards: Data is transmitted wirelessly to HMIs, SCADA systems, or cloud platforms, providing operators and managers with real-time visibility into line performance, OEE, and potential issues via intuitive dashboards.
- Remote Diagnostics and Support: IIoT connectivity allows equipment suppliers to remotely diagnose problems, update software, and provide faster technical support, reducing downtime.
- Integration with MES/ERP Systems: Seamless data exchange between the packaging line and higher-level business systems enables automated order processing, accurate inventory tracking, quality data logging, and streamlined supply chain management.
- Smart Labeling and Tracking: RFID tags or advanced barcodes integrated with the IIoT platform provide enhanced traceability of individual coils throughout the supply chain, offering valuable data on transit conditions and handling.
5.4. Focus on Energy Efficiency and Sustainability
- Energy-Efficient Machinery Design: Manufacturers are incorporating energy-saving components like high-efficiency motors, variable frequency drives (VFDs), regenerative braking systems, and intelligent power-down modes during idle periods to reduce the line's overall energy consumption and carbon footprint.
- Optimized Material Usage Systems: Technologies that precisely control film stretch and strap tension not only save material costs but also contribute to sustainability by reducing resource consumption and waste generation.
- Waste Reduction and Recycling Integration: Systems designed to minimize scrap during material loading and changeovers, along with integrated solutions for collecting and processing recyclable materials (like PET strap remnants), support circular economy principles.
5.5. Conclusion
The pace of technological innovation in steel coil packaging is accelerating. Embracing advanced automation, AI, smarter materials, IIoT connectivity, and sustainable practices is no longer optional but essential for manufacturers aiming to enhance efficiency, improve quality, ensure safety, and meet evolving market demands. These technologies collectively promise a future of highly optimized, data-rich, flexible, and environmentally conscious steel coil packaging operations. The subsequent chapter will address the critical aspects of safety and regulatory compliance within this technological context.

6. Safety Considerations and Compliance in Steel Coil Packaging
Safety is non-negotiable in any industrial environment, and steel coil packaging operations present unique hazards due to the massive weight of the coils, the presence of heavy machinery, and the nature of the materials handled. Ensuring a safe working environment is not only a moral and legal obligation but also crucial for maintaining operational continuity, protecting valuable assets, and managing costs associated with accidents and downtime. Furthermore, strict adherence to relevant industry standards and governmental regulations is mandatory. This section outlines key safety considerations and compliance requirements for steel coil packaging lines.
6.1. Identifying Key Safety Risks
Understanding the potential hazards is the first step towards mitigating them. Common risks include:
- Crushing and Impact Injuries: Due to the immense weight, falling or shifting coils pose severe crushing hazards. Personnel can also be struck by moving coils on conveyors or handling equipment.
- Entanglement and Pinch Points: Moving parts on wrapping machines, strapping heads, conveyors, and robotic arms create risks of entanglement or pinching if proper guarding is not in place.
- Musculoskeletal Disorders (MSDs): Manual handling tasks, even infrequent ones, such as loading materials, clearing jams, or assisting with positioning, can lead to strains and sprains if ergonomic principles are ignored.
- Lacerations and Punctures: Sharp edges on steel coils, strapping materials (especially steel straps), and cutting tools present cut hazards.
- Slips, Trips, and Falls: Oil or grease spills, debris from packaging materials, uneven surfaces, or poorly managed cables can lead to falls.
- Electrical Hazards: Improper maintenance or damaged wiring on automated equipment poses risks of electric shock.
6.2. Best Practices for Ensuring Safety
A multi-faceted approach is required to create and maintain a safe packaging environment.
- Comprehensive Risk Assessments: Regularly conduct thorough risk assessments of the entire packaging line and associated tasks to identify hazards and evaluate existing control measures.
- Engineering Controls (Elimination/Substitution):
- Prioritize automation to eliminate hazardous manual handling tasks.
- Use appropriate machine guarding (fixed guards, interlocked guards, light curtains, safety mats) to prevent access to dangerous moving parts. Ensure guarding complies with relevant standards (e.g., ISO 13857).
- Incorporate safety-rated components and control systems (e.g., safety PLCs, emergency stops) designed according to standards like ISO 13849-1.
- Design workstations ergonomically to minimize strain.
- Substitute hazardous materials where possible (e.g., using PET strap instead of steel strap can reduce cut risks).
- Administrative Controls:
- Develop and enforce strict Safe Work Procedures (SWPs) for all tasks, including operation, maintenance, and troubleshooting.
- Implement robust Lockout/Tagout (LOTO) procedures for maintenance and servicing activities to prevent unexpected machine start-up. Ensure authorized personnel are properly trained.
- Provide comprehensive, task-specific safety training for all employees, including hazard recognition, proper use of equipment, emergency procedures, and LOTO. Conduct regular refresher training.
- Clear signage indicating hazards, required PPE, and safety procedures.
- Good housekeeping practices (5S) to prevent slips, trips, and falls.
- Personal Protective Equipment (PPE): Mandate and provide appropriate PPE based on risk assessment, which typically includes:
- Hard hats
- Safety glasses or face shields
- Cut-resistant gloves
- Steel-toed safety boots
- High-visibility clothing (if operating near mobile equipment)
- Regular Inspections and Maintenance: Ensure safety devices (E-stops, interlocks, guards) are regularly inspected, tested, and maintained in proper working order as part of the preventive maintenance program.
6.3. Compliance with Standards and Regulations
Adherence to legal and industry standards is crucial. Key regulatory bodies and standards include:
- Occupational Safety and Health Administration (OSHA) (USA): Sets and enforces workplace safety standards, including specific regulations for machine guarding (29 CFR 1910.212), control of hazardous energy (LOTO - 29 CFR 1910.147), material handling, and PPE.
- European Machinery Directive (EU): Mandates essential health and safety requirements (EHSRs) for machinery placed on the EU market. Compliance often involves adherence to harmonized standards (e.g., EN ISO 12100 for risk assessment, EN ISO 13849 for safety-related control systems). Requires CE marking.
- International Organization for Standardization (ISO): Develops globally recognized standards relevant to machinery safety, including:
- ISO 12100: Safety of machinery — General principles for design — Risk assessment and risk reduction.
- ISO 13849: Safety of machinery — Safety-related parts of control systems.
- ISO 13857: Safety of machinery — Safety distances to prevent hazard zones being reached by upper and lower limbs.
- National and Local Regulations: Specific countries or regions may have additional safety regulations that must be followed.
6.4. Fostering a Safety Culture
Beyond rules and procedures, creating a strong safety culture where safety is prioritized by everyone, from management to frontline workers, is essential.
- Management Commitment: Leadership must visibly demonstrate commitment to safety through resource allocation, policy enforcement, and active participation.
- Employee Involvement: Encourage workers to report hazards, suggest safety improvements, and participate in safety committees or audits.
- Incident Reporting and Investigation: Implement a non-punitive system for reporting all incidents and near misses. Conduct thorough investigations to identify root causes and implement corrective actions to prevent recurrence.
- Continuous Improvement: Treat safety as an ongoing process. Regularly review safety performance, update risk assessments, and adapt procedures based on new information or changes in operations.
6.5. Conclusion
Safety and compliance are integral components of successful steel coil packaging operations. By proactively identifying risks, implementing robust engineering and administrative controls, ensuring adherence to regulations, providing thorough training, and cultivating a strong safety culture, manufacturers can protect their workforce, prevent costly disruptions, and operate responsibly and sustainably. The financial implications and return on investment considerations for these systems will be discussed next.
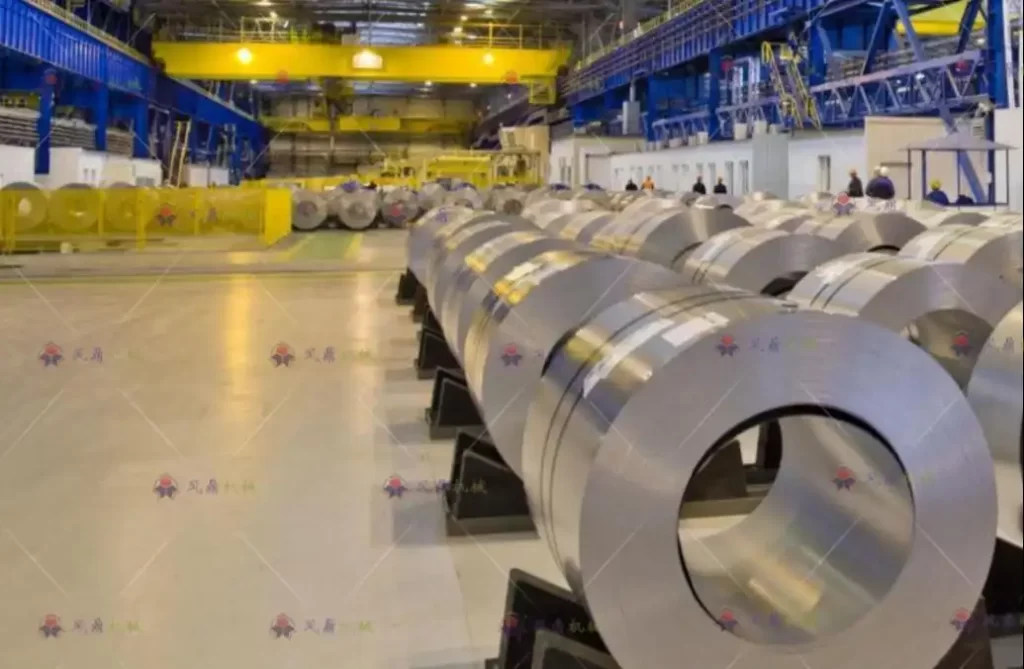
7. Analyzing Cost Efficiency and ROI in Steel Coil Packaging Lines
Implementing or upgrading a steel coil packaging line represents a significant financial undertaking. Therefore, a thorough analysis of cost efficiency and a clear understanding of the potential Return on Investment (ROI) are essential for justifying the expenditure and ensuring the system contributes positively to the company's financial health. This section examines the various cost components, strategies for enhancing cost efficiency, and methods for evaluating the ROI of steel coil packaging investments.
7.1. Key Cost Components
A comprehensive cost analysis must consider both initial investment and ongoing operational expenses.
- Capital Expenditure (CapEx):
- Equipment Purchase: The primary cost, including wrapping machines, strapping systems, conveyors, turntables, tilters, safety guarding, control systems (PLCs, HMIs), and potentially robotics or AGVs. Automated lines have significantly higher CapEx than manual setups.
- Installation and Commissioning: Costs associated with site preparation, mechanical and electrical installation, system integration, programming, and start-up testing.
- Training: Initial training costs for operators and maintenance personnel on the new equipment.
- Operational Expenditure (OpEx):
- Labor: Wages, benefits, and overhead for operators, maintenance staff, and supervisors. Automation significantly reduces direct operator labor costs compared to manual lines.
- Consumable Materials: Ongoing costs for stretch film, VCI materials, strapping (steel or PET), seals/clips, labels, ink, edge protectors, etc.
- Energy: Electricity consumption of motors, heaters (for sealing), controls, lighting, etc.
- Maintenance and Spare Parts: Costs for routine preventive maintenance, repairs, replacement parts, and potential service contracts.
- Downtime Costs: Lost production revenue and associated costs when the line is unexpectedly down.
- Indirect Costs:
- Floor Space: Opportunity cost or rental cost of the factory space occupied by the line.
- Waste Disposal: Costs associated with disposing of packaging waste or scrap.
- Insurance: Premiums potentially affected by safety records and equipment value.
- Quality Costs: Costs related to damaged products due to inadequate packaging (rework, scrap, customer claims).
7.2. Strategies for Improving Cost Efficiency
Optimizing costs involves addressing multiple factors across the system's lifecycle.
- Right-Sizing Automation: Choose a level of automation appropriate for the production volume and complexity. Over-automating a low-volume line might not provide a good ROI, while under-automating a high-volume line leads to high labor costs and bottlenecks.
- Optimizing Material Usage:
- Utilize automated systems with precise control over film pre-stretch and tension to minimize film consumption per coil.
- Select the most cost-effective strapping material (e.g., PET vs. steel) that meets performance requirements.
- Regularly evaluate and test new, potentially more efficient or cost-effective packaging materials.
- Minimize waste during material loading and changeovers.
- Maximizing Energy Efficiency:
- Specify energy-efficient components (motors, drives) when purchasing equipment.
- Implement energy-saving modes during idle periods.
- Ensure proper maintenance (e.g., clean motors, lubricated parts) to prevent increased energy draw.
- Implementing Effective Maintenance Strategies:
- A robust Preventive Maintenance (PM) program is crucial to minimize costly unplanned downtime and extend equipment life.
- Consider Predictive Maintenance (PdM) technologies (vibration analysis, thermal imaging, oil analysis) to anticipate failures and schedule repairs efficiently.
- Maintain an adequate inventory of critical spare parts to expedite repairs.
- Reducing Downtime: Track downtime causes meticulously and implement corrective actions. Optimize changeover procedures (SMED). Ensure reliable supply of coils and materials to the line.
- Improving Labor Efficiency: Provide effective training, clear SOPs, and ergonomic tools/workstations. Utilize automation to reallocate labor to higher-value tasks.
7.3. Evaluating Return on Investment (ROI)
ROI analysis helps determine the financial viability of investing in a new or upgraded packaging line. It compares the net financial benefits generated by the investment against its total cost.
a. Calculation Methods
- Simple ROI:
ROI (%) = [(Gain from Investment - Cost of Investment) / Cost of Investment] x 100
(Gain typically includes annual savings in labor, materials, reduced damage, plus potentially increased revenue from higher throughput). - Payback Period:
Payback Period (Years) = Initial Investment / Annual Savings (or Cash Flow)
Indicates how quickly the initial investment is recovered. - Net Present Value (NPV): Considers the time value of money by discounting future cash flows back to their present value. A positive NPV generally indicates a worthwhile investment.
- Internal Rate of Return (IRR): The discount rate at which the NPV of the investment equals zero. If IRR exceeds the company's required rate of return, the project is typically considered acceptable.
b. Key Factors Influencing ROI
- Labor Cost Savings: A primary driver for automation ROI.
- Throughput Increase: Higher production capacity can lead to increased sales revenue.
- Material Cost Reduction: Savings from optimized film/strap usage.
- Improved Quality / Reduced Damage: Lower costs associated with product damage claims, rework, or scrap.
- Enhanced Safety: Reduced costs associated with accidents ( LTA, insurance premiums, potential fines).
- Equipment Lifespan and Reliability: Longer-lasting, reliable equipment yields returns over a longer period.
c. Intangible Benefits
While harder to quantify, consider intangible benefits like improved worker morale (due to better safety and ergonomics), enhanced company image (modern, efficient operations), and greater operational flexibility.
7.4. Conclusion
Achieving optimal cost efficiency and a strong ROI from a steel coil packaging line requires a holistic approach. It involves careful initial planning and equipment selection, diligent operational management focused on minimizing waste and downtime, effective maintenance, and continuous monitoring of performance against financial goals. By thoroughly analyzing costs, implementing efficiency strategies, and rigorously evaluating ROI using appropriate financial metrics, manufacturers can ensure their packaging operations are not just functional but also financially sound and contribute significantly to overall business success. The final section will look ahead at future trends shaping this critical industrial process.

8. The Future of Steel Coil Packaging: Trends and Emerging Technologies
The steel coil packaging industry stands at an inflection point, driven by converging forces of technological innovation, escalating demands for efficiency and sustainability, and the transformative potential of data. Looking ahead, several key trends and emerging technologies are poised to redefine how steel coils are packaged, handled, and tracked. This final section explores the future landscape, highlighting the innovations that will shape the next generation of steel coil packaging systems.
8.1. Hyper-Automation and Intelligent Systems
Automation will become even more sophisticated, integrated, and intelligent.
- AI-Powered Optimization: Beyond predictive maintenance, AI will increasingly optimize packaging parameters (wrap patterns, strap placement/tension) in real-time based on specific coil characteristics (dimensions, grade, surface sensitivity detected by sensors) and destination requirements, ensuring optimal protection with minimal material usage.
- Autonomous Operations: Expect more fully autonomous lines requiring minimal human oversight. This includes self-adjusting machines, automated troubleshooting routines, and integration with AGVs/AMRs for end-to-end material flow from production to warehousing/shipping without manual intervention.
- Enhanced Robotics and Vision Systems: Robots will become more dexterous and adaptable, capable of handling a wider variety of tasks. AI-driven vision systems will offer more sophisticated inspection capabilities, identifying subtle defects and ensuring near-perfect packaging quality.
8.2. Data-Centric Ecosystems (IIoT and Digital Twins)
Data will be the lifeblood of future packaging operations, enabled by pervasive connectivity.
- Ubiquitous IIoT Integration: Nearly every component on the packaging line will be sensor-equipped and connected, generating vast amounts of data on performance, condition, and material flow.
- Advanced Analytics and Cloud Platforms: Cloud-based platforms will aggregate and analyze data from multiple lines or even multiple plants, providing deeper insights into performance bottlenecks, enabling benchmarking, and facilitating enterprise-level optimization strategies.
- Digital Twins: Creating virtual replicas (digital twins) of the physical packaging line will allow manufacturers to simulate changes, test new configurations, optimize parameters, and train operators in a risk-free virtual environment before implementing changes on the actual line.
- Blockchain for Supply Chain Traceability: For high-value coils or regulated industries, blockchain technology could provide an immutable record of the coil's journey, including packaging details and sensor data (e.g., temperature, shock), enhancing security and transparency.
8.3. Sustainability as a Core Driver
Environmental responsibility will increasingly influence technology and material choices.
- Circular Economy Materials: Increased focus on using packaging materials (films, straps) with high recycled content and designing packages for easy disassembly and recycling at the destination. Development of closed-loop systems for packaging materials may emerge.
- Biodegradable and Bio-based Materials: Continued innovation in biodegradable VCI and wrapping materials that offer comparable performance to traditional plastics but with a significantly lower environmental impact.
- Material Reduction Technologies: Continued development of ultra-thin, high-strength films and optimized wrapping/strapping techniques driven by AI to minimize the absolute quantity of material used per package.
- Energy Harvesting and Ultra-Efficient Machinery: Integration of energy recovery systems and designs that drastically reduce the energy footprint of packaging operations, potentially moving towards energy-neutral systems in some cases.
8.4. Modular, Flexible, and Scalable Systems
Packaging lines will need to adapt quickly to changing market demands.
- Modular Design: Equipment designed as interchangeable modules (e.g., different types of wrappers, strappers, labeling units) that can be easily added, removed, or reconfigured to adapt the line's capabilities to new products or capacity requirements.
- Increased Flexibility: Systems capable of handling a wider range of coil sizes, weights, and packaging specifications with minimal manual setup or adjustment, facilitated by robotics and AI-driven parameter settings.
- Scalability: Designs that allow for incremental capacity increases by adding parallel modules or upgrading existing ones without requiring a complete line replacement.
8.5. Enhanced Human-Machine Collaboration
While automation increases, the human role will evolve towards supervision, optimization, and handling exceptions.
- Advanced HMIs and Augmented Reality (AR): More intuitive interfaces, potentially incorporating AR overlays that provide operators with real-time instructions, diagnostic information, or maintenance guidance directly onto their view of the equipment.
- Cobot Integration: Wider adoption of cobots for tasks requiring a blend of automation and human dexterity or judgment, creating safer and more ergonomic hybrid workstations.
8.6. Conclusion: Embracing the Transformation
The future of steel coil packaging promises systems that are significantly more intelligent, efficient, adaptable, sustainable, and data-driven than today's counterparts. Technologies like AI, IIoT, advanced robotics, and innovative materials are not just incremental improvements but catalysts for fundamental transformation. Manufacturers who proactively embrace these changes, invest strategically in new technologies, and foster a culture of continuous adaptation will be best positioned to thrive. By leveraging these advancements, they can optimize operations, reduce environmental impact, enhance product protection, and meet the increasingly complex demands of the global steel market, securing their competitive advantage in the years to come.