Steel Coil Packing Line Customization Options: Which Solution Fits You Best?
- Steel Coil Packing Line Customization Options: Which Solution Fits You Best?
- Introduction
- 1. Why Customization Matters in Steel Coil Packing Lines
- 2. Understanding the Core Components of a Steel Coil Packing Line
- 3. Customization Options for Conveyors
- 4. Choosing the Right Wrapping Solution
- 5. Strapping Customization: Securing Coils for Transport
- 6. Weighing and Labeling: Enhancing Traceability
- 7. Palletizing Solutions: Ensuring Safe Transportation
- 8. Integrating Automation into Your Steel Coil Packing Line
- 9. Advanced Customization with IoT and Data Integration
- 10. Environmental Sustainability and Custom Packaging Solutions
- 11. Choosing the Right Customization Options for Your Business
- Conclusion

Introduction
Steel coil packaging is a critical part of the steel production process, ensuring that products are well-protected during transportation and storage. However, every manufacturing facility has its own unique needs based on factors such as production volume, coil size, transportation methods, and safety regulations. This is why customizing your steel coil packing line is essential to meet the specific demands of your operation.
With a range of options available, from basic setups to fully automated systems with advanced features, the right customization can significantly improve efficiency, reduce costs, and enhance safety. In this article, we’ll explore the various customization options available for steel coil packing lines, helping you determine which solution fits your business best. By understanding the benefits and limitations of each option, you can make an informed decision that aligns with your production goals.
1. Why Customization Matters in Steel Coil Packing Lines
Meeting Specific Operational Needs
No two steel production facilities are exactly the same, and the requirements for packaging steel coils can vary significantly. A one-size-fits-all solution may not address the unique needs of your operation. Customization allows you to tailor your packaging line to factors such as:
- Coil size and weight: Large, heavy coils may require different handling systems than smaller, lighter ones.
- Production speed: High-volume production facilities may need faster, more automated systems to keep up with demand.
- Safety regulations: Facilities must comply with safety standards, and some may require additional safeguards depending on their operational risks.
By customizing your packing line, you can ensure that your system is optimized for efficiency, safety, and performance.
2. Understanding the Core Components of a Steel Coil Packing Line
Key Elements in a Basic Steel Coil Packing Line
Before diving into customization options, it’s essential to understand the core components of a standard steel coil packing line. These components form the foundation of any customization and can include:
- Conveyors: These systems transport steel coils from one station to another. They can be customized based on length, weight capacity, and automation level.
- Wrapping Stations: This is where the coils are wrapped with protective materials like stretch film or paper. Customization options include manual, semi-automated, and fully automated wrapping stations.
- Strapping Machines: Used to secure the coils with metal or plastic straps. Customization allows for varying levels of automation and flexibility in strapping materials.
- Weighing and Labeling Systems: Many facilities require coils to be weighed and labeled for tracking and compliance purposes.
- Palletizing Systems: Coils are often palletized for easier transportation, and this part of the line can be automated or manual depending on production needs.
Understanding these core components helps to identify which parts of the process can be customized to better meet your operational requirements.
3. Customization Options for Conveyors
Conveyor Types and Features
Conveyors are the backbone of a steel coil packing line, responsible for moving heavy coils through various stages of the process. Customization in conveyor systems allows you to match the specific needs of your operation, including:
- Belt vs. Roller Conveyors: Belt conveyors are ideal for smoother transport, while roller conveyors are better suited for heavy-duty operations where durability is key.
- Length and Width Adjustments: Depending on the size of your coils and available floor space, conveyors can be customized to fit the exact dimensions needed.
- Load Capacity: If your facility handles particularly large or heavy coils, the load capacity of the conveyors can be increased to accommodate higher weights.
- Automated vs. Manual Operation: Automation can be integrated into conveyor systems to reduce manual labor and improve efficiency. Automated conveyors can be programmed to move coils between stations without human intervention.
Benefits of Customizing Your Conveyor System
Customizing your conveyor system ensures that it can handle your specific coil dimensions, weight, and production speed. This not only enhances the efficiency of your packing line but also reduces the risk of equipment breakdowns due to overload or improper handling.
4. Choosing the Right Wrapping Solution
Wrapping Materials and Techniques
Steel coils require protective wrapping to shield them from moisture, dust, and other environmental factors. Depending on your needs, you can choose from a range of wrapping materials such as:
- Stretch Film: Often used for smaller coils or those that need flexibility in storage and transportation.
- Paper Wrapping: Ideal for coils that need extra protection during long-distance transportation.
- VCI (Vapor Corrosion Inhibitor) Film: Used to prevent corrosion, particularly in environments with high humidity.
Wrapping Automation Levels
The level of automation in the wrapping station can be tailored to your production requirements. Options include:
- Manual Wrapping: Best for low-volume operations where customization is not critical.
- Semi-Automated Wrapping: The machine assists operators by automating parts of the process, improving speed while still requiring human oversight.
- Fully Automated Wrapping: Best for high-volume production lines where speed and consistency are crucial. Fully automated systems can wrap coils quickly without manual intervention, ensuring uniform protection for each coil.
5. Strapping Customization: Securing Coils for Transport
Strapping Materials and Methods
Strapping ensures that steel coils remain secure during transportation and storage. Depending on your packaging needs, you can choose from different strapping materials, such as:
- Steel Straps: Ideal for heavy coils or those that require extra security during transport.
- Plastic Straps: Lightweight and flexible, plastic straps are suitable for lighter coils or those that don’t require heavy-duty strapping.
Automation in Strapping
Similar to the wrapping process, strapping can be automated to improve efficiency and reduce the need for manual labor. Automated strapping machines ensure consistent tension and positioning of the straps, reducing the risk of product damage.
Customizing your strapping process ensures that your coils are safely secured with the appropriate materials, minimizing the risk of shifting or damage during transportation.

Get Your Best Solution !
6. Weighing and Labeling: Enhancing Traceability
The Importance of Accurate Weighing
Weighing is a critical step in the steel coil packaging process. Many facilities require accurate weight measurements for tracking, billing, and regulatory compliance. By customizing the weighing system, you can ensure that it meets your specific needs in terms of:
- Accuracy: Precision is key, especially when dealing with large volumes of steel.
- Speed: Faster weighing systems help to keep the packing line moving efficiently.
- Integration with Labeling: Weighing systems can be integrated with labeling machines to automatically print weight and product information, enhancing traceability.
Custom Labeling Options
Labeling is essential for identifying coils and ensuring compliance with industry regulations. Customization options for labeling systems include:
- Automatic Label Application: Automated systems can print and apply labels directly to the coils, reducing the need for manual intervention.
- Customizable Labels: Labels can be tailored to include specific information such as coil weight, size, batch number, and customer details, ensuring accurate tracking throughout the supply chain.
7. Palletizing Solutions: Ensuring Safe Transportation
Manual vs. Automated Palletizing
Palletizing is an important part of the steel coil packing process, as it ensures that the coils are securely placed on pallets for safe transportation. Depending on your production needs, you can opt for:
- Manual Palletizing: Workers manually place the coils onto pallets. This option is suitable for smaller operations but may be inefficient for high-volume production.
- Automated Palletizing: Fully automated palletizing systems use robotic arms or automated conveyors to position coils on pallets. This option reduces labor costs and improves speed and consistency.
Customization Options for Palletizing
Custom palletizing systems can be designed to accommodate different coil sizes and pallet types. Whether you need to transport small coils on custom-sized pallets or handle large, heavy-duty coils, a customized palletizing system ensures that your products are safely prepared for transport.
8. Integrating Automation into Your Steel Coil Packing Line
Benefits of Automation in Steel Coil Packaging
Automation is transforming the steel coil packaging industry by providing increased efficiency, reducing labor costs, and improving overall safety. Whether you’re operating a small-scale facility or a high-volume production line, integrating automation into your packing system can provide significant advantages:
- Improved Speed and Consistency: Automated systems perform repetitive tasks, such as wrapping and strapping, with greater speed and precision than manual labor, ensuring each coil is packed uniformly.
- Reduced Labor Costs: Automation reduces the need for manual intervention, freeing up your workforce for other value-added tasks and lowering operational costs.
- Enhanced Safety: By reducing manual handling of heavy steel coils, automation minimizes the risk of injuries caused by lifting, shifting, or improper handling of coils.
- Scalability: Automated systems are scalable and can be customized to handle increased production demands as your business grows.
Levels of Automation
Automation in steel coil packaging can be customized to different levels depending on your production needs. These include:
- Semi-Automated Systems: Semi-automated systems perform specific tasks but still require human supervision. For example, a semi-automated wrapping machine may still require an operator to position the coil correctly, but it will automate the actual wrapping process.
- Fully Automated Systems: Fully automated systems require minimal human intervention. From wrapping and strapping to labeling and palletizing, these systems can handle every aspect of the process, significantly improving throughput and operational efficiency.
Customizing the level of automation in your packing line ensures that you meet production goals while maintaining flexibility and control over critical packaging tasks.
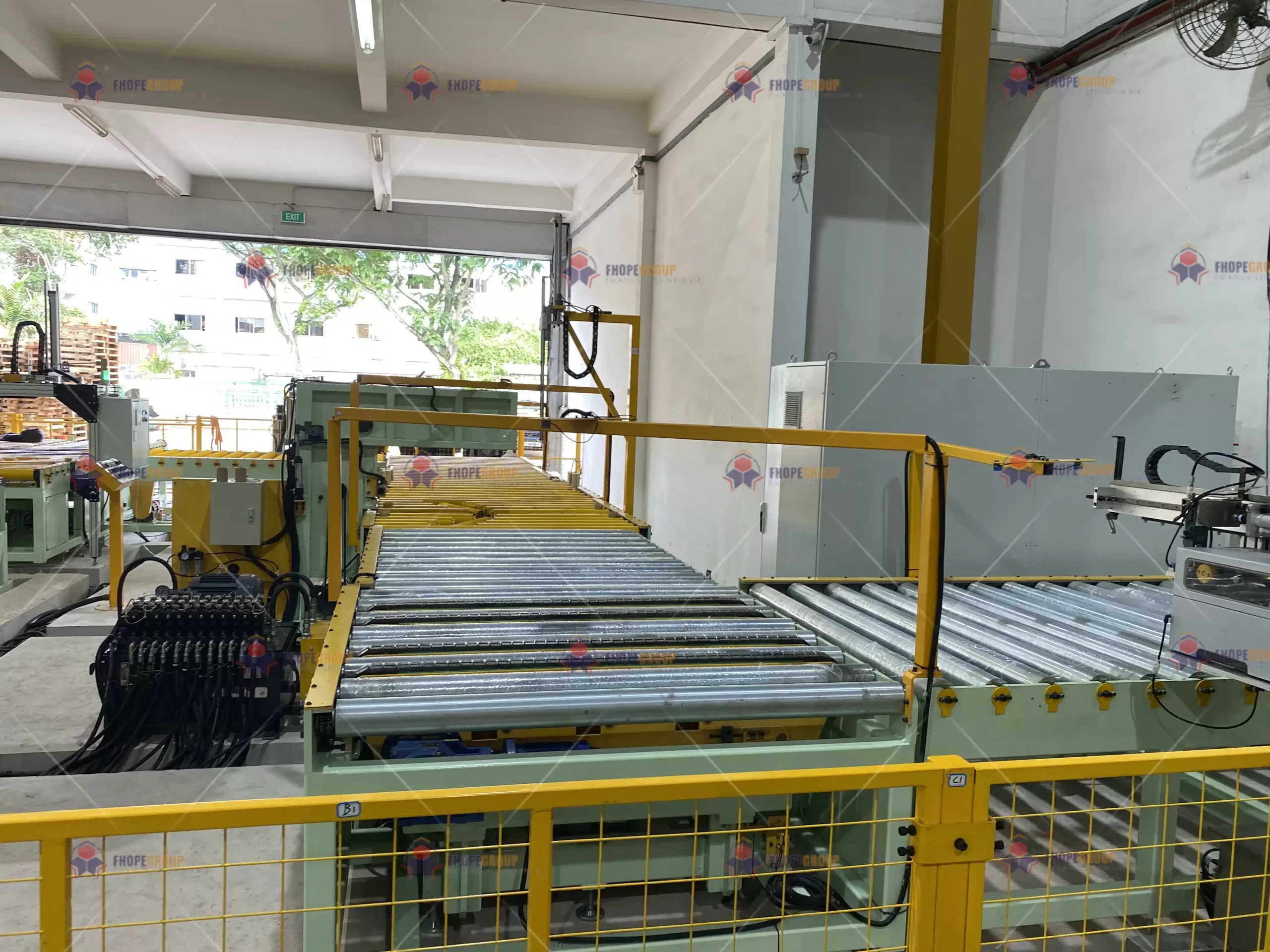
9. Advanced Customization with IoT and Data Integration
Leveraging the Power of IoT in Steel Coil Packaging
The Internet of Things (IoT) is revolutionizing manufacturing by enabling machines and systems to communicate with each other in real time. In steel coil packaging, IoT integration provides valuable data that can help you optimize your operations, reduce downtime, and improve productivity.
IoT-Enabled Customization Options
- Real-Time Monitoring: IoT sensors can track every aspect of the packaging process, from machine performance to coil movement. This data allows operators to monitor the health of the system and identify potential issues before they lead to downtime.
- Predictive Maintenance: IoT sensors collect data on wear and tear, allowing for predictive maintenance schedules. Instead of waiting for a machine to break down, operators can proactively address maintenance issues, reducing the risk of unexpected disruptions.
- Data-Driven Decision Making: By analyzing data collected from IoT-enabled machines, operators can make informed decisions about production rates, material usage, and energy consumption. This helps optimize resource allocation and ensures that the packing line is running at peak efficiency.
Integration with Enterprise Resource Planning (ERP) Systems
For companies looking to take their customization to the next level, integrating the steel coil packing line with an Enterprise Resource Planning (ERP) system offers a seamless way to manage production, inventory, and shipping. With ERP integration, data from the packing line can be automatically fed into your company’s broader supply chain and production management systems.
This level of integration ensures that production schedules, material orders, and shipment tracking are all aligned with the actual performance of the packing line, providing end-to-end visibility and control over your operations.
10. Environmental Sustainability and Custom Packaging Solutions
Reducing Waste and Improving Efficiency
In today’s manufacturing landscape, sustainability is a growing concern. Many companies are looking for ways to reduce their environmental impact while maintaining efficient production. Customizing your steel coil packing line can help achieve these goals by minimizing waste and improving energy efficiency.
Eco-Friendly Packaging Materials
Choosing sustainable packaging materials can help reduce your environmental footprint. For example, you can opt for recyclable or biodegradable wrapping films and strapping materials. Additionally, customization allows you to optimize material usage, ensuring that coils are wrapped securely without using excess materials.
Energy-Efficient Systems
Automated packing systems can also be designed to minimize energy consumption. For example, custom-built machines can be programmed to power down during idle periods, reducing unnecessary energy use. IoT sensors can monitor energy consumption in real time, allowing operators to adjust settings and reduce the system’s overall carbon footprint.
Compliance with Environmental Regulations
By customizing your packaging line with sustainability in mind, you can ensure compliance with environmental regulations and meet the growing demand from consumers and clients for eco-friendly business practices.
11. Choosing the Right Customization Options for Your Business
Factors to Consider When Customizing Your Packing Line
Selecting the right customization options for your steel coil packing line depends on several key factors:
- Production Volume: High-volume operations require more automation and advanced systems to handle the increased demand, while smaller facilities may benefit from semi-automated solutions.
- Coil Size and Weight: The size and weight of the coils you handle will dictate the type of conveyors, wrapping, and strapping systems you need.
- Budget: Your budget will play a significant role in determining the level of automation and customization you can implement. While fully automated systems offer the highest efficiency, they also come with higher upfront costs.
- Future Growth: Consider your company’s long-term growth potential when customizing your packing line. Choosing scalable systems that can grow with your business ensures that your investment remains valuable as your production needs expand.
Customization for Specific Industry Requirements
In some cases, steel coil packaging lines need to be customized to meet industry-specific regulations or client demands. For example:
- Automotive Industry: Coils used in the automotive sector often require precise labeling, traceability, and high levels of protection against corrosion. Customizing your system with advanced labeling and wrapping technologies ensures compliance with industry standards.
- Construction Industry: Coils destined for construction sites may need additional reinforcement to withstand the harsh environments. Customizing your packing line with heavier-duty materials and strapping ensures that your product arrives intact.
By understanding your industry’s specific requirements, you can tailor your packaging solution to meet these demands effectively.
Conclusion
Customizing your steel coil packing line is a critical step toward optimizing efficiency, enhancing safety, and meeting the specific needs of your operation. Whether you’re looking to implement basic modifications or seeking advanced automation with IoT integration and data-driven solutions, the right customization can make a significant difference in your overall performance.
By focusing on key areas such as conveyors, wrapping, strapping, palletizing, and data integration, businesses can create a customized packing line that meets their production goals while remaining flexible enough to scale with future demands. Automation, sustainability, and data-driven decision-making are essential components of modern packaging lines, and choosing the right customization options ensures that your investment delivers long-term value.
Now is the time to assess your current packaging processes, identify areas for improvement, and explore the wide range of customization options available. Whether you’re operating a small facility or managing high-volume production, the right custom solution will help you stay competitive, efficient, and environmentally responsible in today’s demanding market.

Get Your Best Solution !