Spiral Stretch Wrapper for Efficient Product Handling: Implementation Phase Guidelines
- Spiral Stretch Wrapper for Efficient Product Handling: Implementation Phase Guidelines
- Introduction
- 1. Understanding Spiral Stretch Wrappers
- 2. Why the Implementation Phase Matters
- 3. Assessing Your Product Handling Needs
- 4. Selecting the Right Spiral Stretch Wrapper
- 5. Preparing the Installation Site
- 6. Initial Setup and Configuration
- 7. Staff Training and Safety Protocols
- 8. Integrating Spiral Stretch Wrappers into Existing Workflows
- 9. Routine Maintenance Best Practices
- 10. Long-Term Operational Benefits
- 11. Troubleshooting Common Issues
- 12. Customizing Your Spiral Stretch Wrapper
- Conclusion
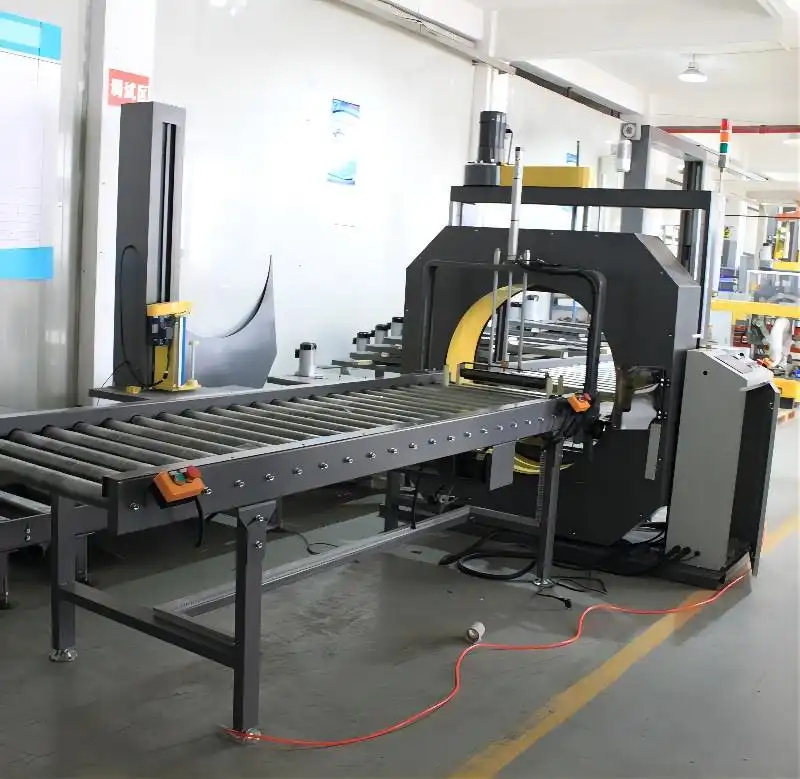
Introduction
In today’s fast-paced production and distribution environments, efficient product handling is essential to maintaining smooth operations and reducing costs. One of the most effective tools to achieve this is the spiral stretch wrapper, a versatile machine designed to secure and stabilize products for transport or storage. However, to truly leverage its potential, the implementation phase of these machines needs careful planning and execution.
This article serves as a comprehensive guide for businesses looking to implement spiral stretch wrappers for efficient product handling. From understanding the equipment’s benefits to ensuring proper installation and staff training, we will break down the key steps necessary for a successful implementation.
1. Understanding Spiral Stretch Wrappers
A spiral stretch wrapper is an advanced packaging machine that wraps products in a spiral pattern using stretch film. It is particularly useful for items that are irregularly shaped, long, or difficult to palletize. The film is applied tightly around the product, ensuring protection from damage during transport while also securing the item to its base or pallet.
Key Benefits of Spiral Stretch Wrappers:
- Increased stability for odd-shaped or fragile items.
- Reduced manual labor and packaging time.
- Cost savings through optimized film usage.
- Enhanced protection from dust, moisture, and external damage.
2. Why the Implementation Phase Matters
The implementation phase of a spiral stretch wrapper is crucial because it lays the foundation for long-term operational efficiency. Without a well-thought-out implementation plan, even the best machines can fail to deliver the desired results. Missteps in installation, configuration, or training can lead to production bottlenecks, increased downtime, and even safety hazards.
Common Challenges during Implementation:
- Incorrect machine setup or configuration.
- Inadequate employee training.
- Improper integration with existing workflows.
- Lack of routine maintenance schedules.
To avoid these issues, a strategic approach is essential from the very beginning.
3. Assessing Your Product Handling Needs
Before diving into the specifics of spiral stretch wrapper installation, it’s important to assess your product handling requirements. Each business has unique challenges, and understanding your specific needs is key to selecting the right machine and implementation strategy.
Questions to consider:
- What type of products will you be wrapping? (e.g., long pipes, irregular items, etc.)
- How often will the machine be used in daily operations?
- What are the size, weight, and fragility considerations for your products?
By having a clear understanding of these factors, you can choose the right spiral stretch wrapper model and features that align with your business’s operational goals.
4. Selecting the Right Spiral Stretch Wrapper
Not all spiral stretch wrappers are the same, and choosing the right one for your operation is critical. The market offers a variety of models, each with different capabilities based on factors such as speed, film tension control, and wrapping configurations.
Key Features to Consider:
- Adjustable tension control to accommodate different product sizes and shapes.
- Automatic film cutter to streamline operations.
- Variable speed options to match the pace of your production line.
- Customizable wrapping cycles for specific product requirements.
Consult with a professional or your machine provider to ensure that the model you select fits your workflow, product type, and long-term operational goals.
5. Preparing the Installation Site
Once you’ve selected the appropriate machine, the next step in the implementation process is preparing the installation site. The success of your spiral stretch wrapper will largely depend on how well it integrates with your current layout and processes.
Installation Site Considerations:
- Space availability: Ensure the area is spacious enough for the machine, its operators, and any surrounding equipment.
- Power requirements: Confirm that the area has the necessary power supply to support the machine’s electrical needs.
- Safety considerations: Ensure that the machine is installed away from high-traffic areas to avoid accidents.
Taking the time to set up the site properly will reduce future issues and ensure smoother operations from day one.
6. Initial Setup and Configuration
The setup and configuration stage is where your spiral stretch wrapper begins to come to life in your production process. Whether you opt for a professional installation service or handle it in-house, precision is key at this phase.
Best Practices for Setup:
- Follow the manufacturer’s instructions carefully to avoid setup errors.
- Run initial tests with sample products to check that the machine is configured correctly.
- Fine-tune film tension to match the specific needs of your product, ensuring a tight wrap without damage.
Ensure that the machine’s control panel is properly calibrated for your specific products. This includes setting parameters like film tension, wrap count, and wrapping speed to avoid product damage or excessive material usage.
7. Staff Training and Safety Protocols
A critical aspect of a successful spiral stretch wrapper implementation is ensuring that your staff is well-trained to use the equipment. Even the most advanced machines can become a bottleneck if operators don’t know how to use them correctly.
Key Training Elements:
- Machine operation: Teach employees how to load products, set wrapping parameters, and troubleshoot common issues.
- Safety training: Ensure staff is trained on safety protocols, such as emergency stops and handling machinery near moving parts.
- Routine maintenance: Operators should be familiar with the machine’s maintenance needs, including cleaning and routine checks.
Proper training not only ensures smooth operations but also reduces the risk of accidents and downtime due to user error.

Get Your Best Solution !
8. Integrating Spiral Stretch Wrappers into Existing Workflows
To fully realize the benefits of a spiral stretch wrapper, it needs to be integrated into your existing workflows seamlessly. This involves aligning the machine’s operation with the pace and rhythm of your production line.
Steps to Achieve Workflow Integration:
- Coordinate with upstream and downstream processes to ensure that the wrapper doesn’t become a bottleneck.
- Automate repetitive tasks where possible, such as moving products from the production line to the wrapper.
- Monitor machine output and adjust processes as needed to maintain efficiency.
Effective integration will reduce wait times, minimize human intervention, and keep your production line flowing smoothly.
9. Routine Maintenance Best Practices
A well-maintained spiral stretch wrapper will ensure consistent performance and reduce unexpected downtime. Implementing a regular maintenance schedule is essential to keep your equipment running efficiently and to extend its lifespan.
Key Maintenance Practices:
- Regular cleaning of moving parts, especially the film rollers and cutter blades, to prevent debris build-up that could affect performance.
- Lubrication of mechanical parts to reduce wear and tear, ensuring smooth operation.
- Inspecting film tension settings and film rollers to ensure they remain in optimal condition.
- Checking electrical connections and sensors to prevent operational failures or misreadings during wrapping.
- Replacing worn-out parts such as belts, gears, or film clamps to avoid unplanned breakdowns.
By adhering to these practices, you can minimize the chances of production delays due to machine malfunctions.
10. Long-Term Operational Benefits
Over time, implementing a spiral stretch wrapper can result in numerous long-term operational benefits. By automating what was once a labor-intensive task, you gain efficiencies that positively impact your entire production process.
Key Benefits Include:
- Consistent product quality: The automated nature of the machine ensures that each product is wrapped uniformly, reducing the risk of product damage.
- Improved worker safety: Automation reduces the need for manual handling, minimizing the risk of injury, especially in industries dealing with heavy or awkwardly shaped products.
- Labor cost savings: By cutting down on manual work, businesses can allocate labor resources more effectively, improving overall productivity.
- Faster throughput: Spiral stretch wrappers can handle large volumes quickly, enabling businesses to meet growing demand without increasing manpower.
These benefits not only improve day-to-day operations but also enhance a company’s ability to scale and respond to market needs more efficiently.
11. Troubleshooting Common Issues
Despite their efficiency, spiral stretch wrappers can occasionally experience technical issues. Familiarizing your team with common problems and their solutions can prevent extended downtime and costly service calls.
Common Issues and Solutions:
- Film breaking during wrapping: Check the film tension settings and ensure the film is of the correct grade for your products. Also, inspect the rollers for debris or wear that could be damaging the film.
- Misalignment of the wrap: Ensure that the product is centered properly on the wrapping platform and that the film carriage is aligned correctly.
- Film not cutting properly: This is often caused by a dull or damaged blade. Regularly inspect and replace the film cutter as needed.
- Machine stops mid-cycle: This could indicate a sensor issue or an electrical fault. Check the control panel for error messages and inspect sensors for cleanliness and proper alignment.
By empowering your team to handle these common issues, you can keep your production line running smoothly.
12. Customizing Your Spiral Stretch Wrapper
Another major advantage of spiral stretch wrappers is the ability to customize them to suit specific business needs. Whether you’re handling fragile items, large industrial products, or a mixture of both, most models allow for significant adjustments and add-ons to enhance performance.
Customization Options:
- Film type and thickness: Depending on the level of protection needed, you can adjust the film’s thickness and material.
- Wrap patterns: Tailor the number of wraps and the overlapping pattern based on the product’s size, shape, and fragility.
- Automation features: Options such as automatic film threading, cut-and-seal mechanisms, and integrated pallet conveyors can further streamline operations.
- Specialized sensors: These can detect the size and shape of each product to ensure accurate wrapping, even for irregular items.
Customizing the spiral stretch wrapper to match your unique production requirements enhances both efficiency and product protection.
Conclusion
Implementing a spiral stretch wrapper for efficient product handling is an excellent way to boost productivity, improve packaging consistency, and enhance safety in your operations. However, to fully reap the benefits, it’s important to approach the implementation phase methodically, ensuring that the right machine is selected, installed correctly, and integrated smoothly into your workflows. Regular maintenance, staff training, and customization will also play crucial roles in ensuring long-term success. By following these guidelines, businesses can ensure that their investment in a spiral stretch wrapper is not only operationally effective but also future-proofed for growth.
With the right approach, this powerful packaging tool can significantly enhance your product handling capabilities, leading to faster production times, reduced labor costs, and improved product protection.

Get Your Best Solution !