Performance Comparison: Speed, Precision, and Efficiency in Steel Coil Packing Lines
In the fast-paced world of steel manufacturing, the packaging process is as critical as the production of the coils themselves. The steel coils must be safely packed, strapped, and prepared for transportation or storage, while ensuring minimal downtime and waste. This brings us to three vital factors that dictate the performance of steel coil packing lines—speed, precision, and efficiency.
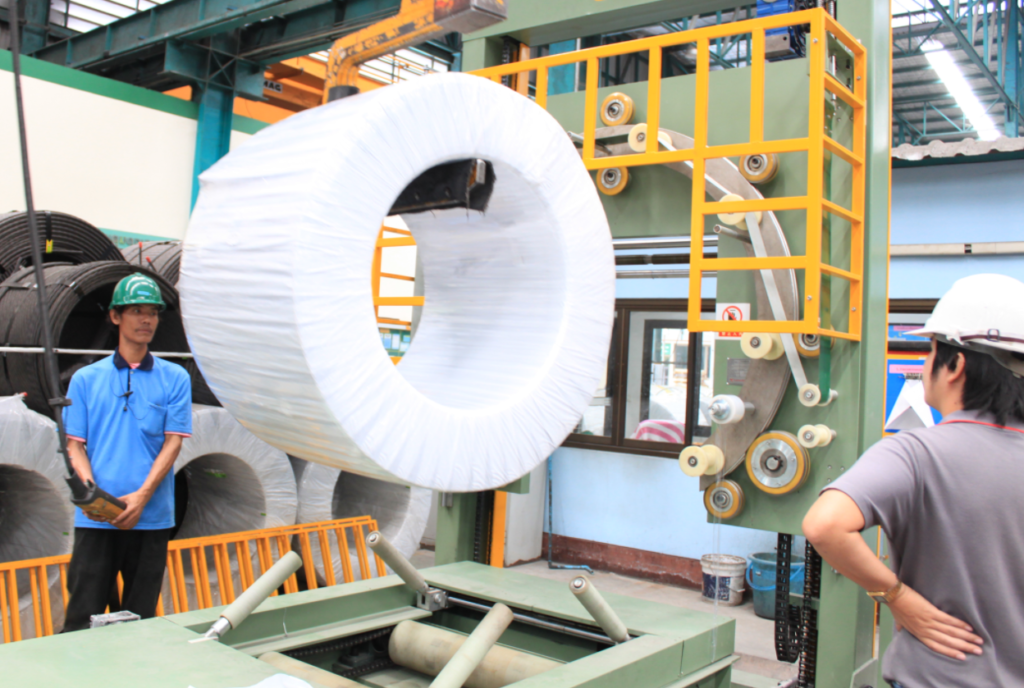
The advancements in automation and packaging technology have dramatically improved the performance of steel coil packing lines over recent years. As companies seek to optimize their processes and reduce costs, understanding the differences in performance—specifically in terms of speed, precision, and overall efficiency—is crucial to making informed decisions about equipment investments and operational strategies.
In this article, we will dive deep into these three pillars of performance in steel coil packaging lines, comparing traditional methods with modern automated solutions to highlight where manufacturers can gain the most in terms of output, quality, and return on investment.
1. Speed: Why It Matters in Steel Coil Packaging
Speed is a fundamental component in the evaluation of any packaging line. The faster a coil can be packed, the more productive the operation. However, achieving high speed should not compromise the quality or integrity of the packaging.
In traditional steel coil packaging lines, the packaging process was manual or semi-automated, leading to slower cycle times. Workers would take several minutes to wrap, strap, and secure each coil. This method had its limitations—human fatigue, inconsistency in execution, and the slow pace of manual operations. As a result, production throughput suffered, especially in high-demand environments where every minute counts.
Automated coil packaging lines, on the other hand, can achieve significantly faster packaging speeds. Automated wrapping and strapping machines are capable of processing coils in less than a minute, sometimes wrapping and securing in as little as 30 seconds per coil. Additionally, automated conveyors seamlessly transport coils from station to station, ensuring continuous movement through the packaging line.
High-speed machines also reduce the need for labor-intensive processes, allowing manufacturers to scale up production without increasing headcount. Moreover, faster lines contribute directly to higher throughput, enabling companies to meet tight deadlines, manage larger orders, and increase profitability.
2. Precision: Consistency is Key
Precision in packaging is equally important as speed. Poorly packaged coils may suffer damage during transit or storage, leading to higher costs and reputational damage for manufacturers. Precise packaging ensures that each coil is wrapped and strapped uniformly, providing the best possible protection.
In manual packaging processes, precision is often compromised due to human error or fatigue. Workers may apply inconsistent tension to straps, leading to loose or over-tightened packaging. Similarly, manual wrapping often results in uneven coverage, exposing parts of the coil to potential damage from external elements like moisture or dust. This not only affects the quality of packaging but also risks damaging the product, leading to customer complaints and costly returns.
Automated systems eliminate these inconsistencies by ensuring that each step of the packaging process is executed with the same level of accuracy every time. Robotic wrapping systems apply the correct amount of stretch film or protective material in uniform layers, guaranteeing that every coil receives identical coverage. In addition, automated strapping systems apply uniform tension to each strap, reducing the risk of coil movement or shifting during transit.
The precision achieved with automation also allows manufacturers to optimize material usage. Instead of over-wrapping or over-strapping, automated systems use the exact amount of material required to secure the coils, cutting down on waste and lowering packaging costs.
3. Efficiency: The Complete Package
When evaluating the performance of a steel coil packaging line, efficiency encompasses several factors: energy consumption, material usage, labor involvement, and downtime. An efficient line is one that maximizes throughput while minimizing resource usage and operational costs.
In manual operations, efficiency often suffers due to downtime between shifts, the need for human operators to take breaks, and the risk of errors requiring rework. These factors increase the time it takes to package each coil and can cause bottlenecks in production. Moreover, inefficiencies in material usage, such as over-wrapping coils, lead to higher costs.
Automated steel coil packaging systems offer a significant improvement in efficiency. First, these systems can run continuously with minimal downtime, processing coils at a consistent pace throughout the day. Automated systems also use real-time sensors to monitor each step of the packaging process, ensuring that every action—whether it’s applying the stretch film or strapping the coil—is done precisely.
Modern automated systems also incorporate smart energy-saving features, such as power-saving modes that reduce electricity consumption during idle times. This contributes to lower overall operational costs and supports sustainability initiatives, making automated packaging lines more environmentally friendly.
Additionally, automated systems can be integrated with Manufacturing Execution Systems (MES) or Enterprise Resource Planning (ERP) software, enabling real-time tracking of production data, packaging performance, and material usage. This data-driven approach allows operators to optimize the line’s efficiency continuously and make adjustments that enhance performance without sacrificing quality.
4. Speed vs. Precision: Striking the Right Balance
While high-speed packaging lines are impressive, speed must be balanced with precision to ensure that the packaging meets the necessary standards for protection. It’s not enough to package coils quickly if the quality of the packaging suffers.
One challenge in manual packaging lines is the trade-off between speed and precision. Workers may rush to complete orders, leading to sloppy wrapping or poorly secured straps. This compromises the quality of the packaging and, in some cases, leads to rework, which negates any time savings achieved through faster work.
Automated systems are designed to address this balance by optimizing both speed and precision. PLC-controlled packaging machines allow operators to set parameters that ensure packaging is applied correctly at high speeds. For example, the machine can adjust the wrapping tension based on the size and weight of each coil, ensuring that the wrapping is neither too tight nor too loose.
Moreover, advanced strapping machines equipped with sensor-driven technology ensure that straps are applied uniformly, with precise tension to hold the coil in place without damaging it. This combination of speed and precision allows manufacturers to process more coils per shift without compromising on packaging quality.
5. The Role of Robotics in Enhancing Precision and Speed
Robotics have become a game-changer in modern steel coil packaging lines, particularly in how they enhance both speed and precision. Robotic arms can handle tasks such as coil positioning, wrapping, and strapping with greater accuracy and consistency than human operators.
Robots are capable of lifting heavy coils, placing them on turntables or conveyors, and positioning them for wrapping without the need for manual handling. This not only increases the speed of the process but also ensures that coils are positioned perfectly every time, reducing the risk of errors.
Additionally, robotic wrapping systems can adjust the application of stretch film dynamically, ensuring that each layer of film is applied evenly, regardless of the coil’s shape or size. This level of precision is difficult to achieve with manual labor, where human fatigue and error often lead to inconsistencies.
By integrating robotics into the packaging line, manufacturers can also reduce labor costs and improve workplace safety. Robots can handle tasks that are repetitive, dangerous, or require high levels of precision, allowing human workers to focus on more complex and value-added activities.
7. The Impact of Downtime on Packaging Line Efficiency
Downtime is one of the biggest contributors to inefficiency in any packaging operation. Whether due to equipment failure, maintenance, or operator errors, unplanned downtime can significantly slow down production and increase costs. In manual operations, downtime is often caused by the need for breaks, human errors, or the manual handling of heavy coils.
Automated systems are built to minimize downtime through several key features. For starters, real-time monitoring systems provide operators with up-to-the-minute data on the performance of the packaging line. Sensors detect issues such as low material levels, machine errors, or equipment malfunctions, allowing operators to address them before they result in costly downtime.
Additionally, automated packaging lines often come with predictive maintenance features. These systems use historical data and sensor feedback to predict when a machine will require maintenance or repair. By scheduling maintenance during planned downtime or off-peak hours, manufacturers can avoid unexpected shutdowns and keep their operations running smoothly.
Reducing downtime is crucial for maintaining high efficiency and throughput, as even short periods of downtime can significantly impact the overall productivity of the line. Automated systems, with their advanced monitoring and predictive capabilities, ensure that downtime is minimized and production continues at optimal levels.
8. Integration of Smart Technology for Performance Optimization
The integration of smart technology into steel coil packaging lines has revolutionized the way companies monitor and improve the performance of their equipment. Smart packaging systems are equipped with sensors, IoT connectivity, and data analytics tools that allow manufacturers to track and analyze every aspect of their operations in real-time.
These systems collect data on key performance indicators (KPIs) such as packaging speed, material usage, energy consumption, and machine performance. With this data, manufacturers can identify inefficiencies, optimize machine settings, and improve overall performance. For example, if a machine is using more wrapping film than necessary, operators can adjust the settings to reduce waste.
Real-time monitoring also enables manufacturers to address issues as they arise, reducing the risk of equipment failures or material shortages. In addition, the data collected by these systems can be used for long-term planning and continuous improvement. By analyzing trends and performance over time, manufacturers can make data-driven decisions to enhance the efficiency and precision of their packaging lines.
With smart technology, manufacturers are no longer guessing when it comes to optimizing their packaging lines. Instead, they have access to actionable insights that allow them to fine-tune every aspect of the process, leading to improved performance and greater efficiency.
9. Balancing Speed, Precision, and Efficiency: Finding the Sweet Spot
Achieving the perfect balance between speed, precision, and efficiency is the ultimate goal of any steel coil packaging operation. While speed is critical for maximizing throughput, it must be balanced with precision to ensure that the packaging meets the required standards. At the same time, efficiency encompasses everything from material usage and energy consumption to labor costs and downtime.
Automated packaging lines offer the ideal solution for achieving this balance. By integrating high-speed equipment with precision control systems and energy-efficient technologies, manufacturers can optimize every aspect of the packaging process. PLC-controlled machines, robotic arms, and advanced sensors ensure that each coil is packaged with the highest level of accuracy and consistency, all while minimizing material waste and energy consumption.
Furthermore, the ability to monitor and adjust system settings in real-time allows manufacturers to continuously improve performance. Whether it’s fine-tuning the wrapping tension or adjusting the strapping strength, automated systems provide the flexibility needed to meet specific packaging requirements without sacrificing speed or efficiency.
By investing in modern automated systems, manufacturers can strike the perfect balance between speed, precision, and efficiency, ensuring that their packaging lines operate at peak performance.
10. Conclusion: Investing in the Future of Steel Coil Packaging
In the competitive world of steel manufacturing, having a packaging line that excels in speed, precision, and efficiency is crucial to success. Traditional manual packaging methods simply can’t keep up with the demands of modern production environments, where high throughput and consistent quality are essential.
Automated steel coil packaging lines provide the perfect solution, offering faster processing speeds, greater precision, and optimized efficiency. From robotic wrapping systems to automated strapping machines, these technologies streamline the packaging process, reduce material waste, and improve overall productivity.
By investing in smart technology, real-time monitoring, and predictive maintenance, manufacturers can further enhance the performance of their packaging lines, minimizing downtime and ensuring continuous operations. As the industry continues to evolve, those who embrace automation and advanced technology will be well-positioned to meet future challenges and stay ahead of the competition.
For companies looking to improve their packaging operations, the future is clear: investing in automated systems that deliver speed, precision, and efficiency is the key to long-term success in steel coil packaging.