Enhance Protection & Efficiency: A Guide to Semi-Automatic Horizontal Stretch Wrappers
Handling and securing long, bulky, or irregularly shaped items like pipes, lumber, doors, or panels presents unique packaging challenges. Traditional methods can be slow, inconsistent, and offer inadequate protection. This is where semi-automatic horizontal stretch wrappers provide a powerful solution. This guide explores the functionality, benefits, and applications of these essential machines, helping you understand how they can streamline your packaging operations.
What is a Semi-Automatic Horizontal Stretch Wrapper?
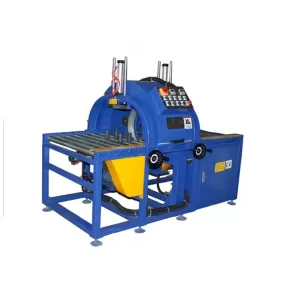
A Semi-Automatic Horizontal Stretch Wrapper, often called an orbital wrapper or ring wrapper, is specialized packaging equipment designed to apply stretch film around elongated products as they pass horizontally through the machine's wrapping ring. Unlike fully automatic systems, the semi-automatic version requires manual intervention for certain steps. An operator typically loads the product onto the conveyor and initiates the wrapping cycle. However, the machine then automates the core wrapping process itself, ensuring consistent film tension and complete coverage around the item. This horizontal orientation is key for efficiently handling products that are difficult or impossible to wrap on standard turntable-style machines.
For a specific example, you can view details on a typical Semiauto horizontal stretch wrapper.
How Does It Work?
The operational flow of a semi-automatic horizontal wrapper generally involves these steps:
- Loading: An operator manually places the product (e.g., a stack of panels, a door, bundled pipes) onto the machine's infeed conveyor system.
- Initiation: The operator uses the control panel to start the pre-programmed wrapping cycle.
- Wrapping: The product is automatically conveyed horizontally through the rotating ring or arm. This mechanism dispenses the stretch film, applying it around the product's circumference. Parameters like conveyor speed, ring rotation speed, and film overlap are typically adjustable to suit different product requirements.
- Completion & Unloading: Once the product has passed completely through the wrapping zone and the cycle is finished, it moves onto the outfeed conveyor. The operator then manually removes the securely wrapped item.
Key Features and Specifications to Consider
Understanding the key specifications helps determine if a machine aligns with your operational needs.
Please note: The parameters listed below are typical examples and may not exactly match the specific model shown in the video or every machine available. Always consult with the supplier for precise specifications relevant to your application.
- Machine Type: Semi-Automatic Horizontal Stretch Wrapper / Orbital Wrapper
- Primary Use: Ideal for packaging long or awkwardly shaped items such as panels, doors, windows, pipes, lumber, extrusions, textiles, and assembled furniture.
- Wrapping Material: Compatible with various types of stretch film, including standard and pre-stretched films.
- Max Product Width (Example): 1200mm (Determines the maximum width the machine can accommodate)
- Max Product Height (Example): 800mm (Determines the maximum height the machine can accommodate)
- Conveyor System: Usually includes powered infeed and outfeed roller conveyors (e.g., 4000mm total length).
- Conveyor Speed: Often adjustable (e.g., up to 10 m/min) to match wrapping needs and production pace.
- Film Delivery System: Frequently incorporates a pre-stretch carriage system (mechanical or powered) to maximize film yield and ensure tighter load containment.
- Operational Mode: Semi-automatic – requires operator for loading, starting the cycle, and unloading.
- Control System: Typically features a user-friendly interface (e.g., PLC control with touchscreen) allowing for programmable wrap patterns and settings.
- Safety Features: Essential features include emergency stop buttons, safety guarding around the wrap zone, and potentially light curtains.
- Power Requirements (Example): 220V, 50Hz, single phase (Verify based on regional standards and specific machine).
- Machine Footprint (Example): Length: 4500mm; Width: 1800mm; Height: 1900mm (Crucial for facility layout planning).
- Machine Weight (Example): Approximately 750kg.
Core Benefits of Using a Semi-Automatic Horizontal Wrapper
Integrating this type of machinery can offer significant advantages:
- Enhanced Product Protection: Delivers a tight, consistent wrap that shields products from dust, moisture, dirt, scratches, and damage caused by shifting during handling, transit, and storage. This is particularly vital for items with finished surfaces or fragile components like glass.
- Improved Operational Efficiency: While requiring an operator, the automated wrapping cycle is considerably faster and more consistent than manual wrapping methods. This reduces labor time per package and can increase overall throughput.
- Versatility in Application: Capable of effectively handling a wide array of product lengths, profiles, and shapes within its size constraints, making it adaptable to diverse industries and product lines.
- Better Load Security and Stability: Ensures that individual items or bundles are securely contained, improving handling safety, preventing product separation, and potentially allowing for more stable stacking.
- Professional Package Appearance: Provides a neat, professional-looking wrap that can enhance product presentation.
Industries and Common Applications
Semi-automatic horizontal stretch wrappers are invaluable across various sectors:
- Building Materials: Wrapping bundles of lumber, siding, flooring, metal or plastic pipes, conduits, insulation panels, and aluminum/vinyl extrusions.
- Furniture Manufacturing: Securely packaging assembled or flat-pack furniture components, doors, and cabinet parts to prevent damage during shipping and handling.
- Window & Door Production: Providing protective wrapping for large, often fragile, window units and door slabs.
- Textiles and Flooring: Wrapping rolls of carpet, fabric, or artificial turf.
- Metal Fabrication: Bundling metal rods, bars, sheets, or custom extrusions.
- Plastics Industry: Wrapping plastic profiles, sheets, or pipes.
See It In Action
Visualizing the machine's operation can be helpful. Watch this video demonstrating a semi-automatic horizontal stretch wrapper:
Conclusion
Semi-automatic horizontal stretch wrappers offer a practical and efficient packaging solution for businesses dealing with the challenges of securing long, bulky, or irregularly shaped products. By automating the most demanding part of the wrapping process, they significantly enhance product protection, improve operational speed compared to manual methods, and ensure consistent load stability. Investing in the right horizontal wrapper can lead to reduced product damage, lower labor costs, and improved overall supply chain integrity.