Optimizing Sandwich Panel Wrapping with Orbital Stretch Wrappers
Sandwich panels, valued for their structural and insulating properties, require careful handling and protection during storage and transit. Damage from impact, moisture, or surface abrasion can compromise their integrity and appearance. Automated wrapping solutions, specifically orbital stretch wrappers, provide an effective method for securing and safeguarding these valuable building components.
Understanding Orbital Stretch Wrapping for Sandwich Panels
Orbital stretch wrappers, exemplified by systems like the Fhope-F200, are specifically engineered for long or bulky products like sandwich panels. Unlike traditional turntable wrappers, the panel typically moves horizontally through the machine (or remains stationary for certain models) while a ring carrying the stretch film roll orbits around the panel.
This process involves:
- Infeed: Panels are fed into the wrapping zone, often via conveyors.
- Orbital Wrapping: The film carriage dispenses stretch film as it rotates around the panel's cross-section.
- Film Application: The film is applied under controlled tension, often utilizing pre-stretch mechanisms to maximize film efficiency and load containment.
- Sealing and Cutting: Once the panel is fully wrapped, the film is automatically clamped, sealed, and cut.
- Outfeed: The securely wrapped panel exits the machine.
orbital stretch wrapper for panel 6 sides wrapping (3) Key Advantages of Automated Orbital Wrapping
Implementing an orbital stretch wrapper for sandwich panels offers significant operational benefits:
- Enhanced Protection: A tight, continuous wrap shields panels from dust, dirt, moisture, and surface scratches during handling, storage, and shipping.
- Improved Load Stability: Consistent film tension secures the panels, preventing shifting or movement during transport, reducing the risk of damage.
- Increased Throughput: Automated systems wrap panels much faster than manual methods, boosting production efficiency and reducing bottlenecks.
- Reduced Labor Costs: Automation minimizes the manual labor required for wrapping, allowing personnel to focus on other tasks.
- Material Savings: Pre-stretch units can significantly elongate the stretch film before application, reducing overall film consumption and cost per wrapped panel.
Essential Features and Considerations
Modern orbital stretch wrappers designed for sandwich panels often incorporate features tailored to specific needs:
- Handling Capacity: Machines are built to accommodate a range of panel dimensions (length, width, height) and weights. Ensure the machine specification matches your product range.
- Conveyor Systems: Integrated powered conveyors facilitate smooth panel transfer through the wrapping cycle.
- Adjustable Tension Control: Allows optimization of film tension based on panel type and stability requirements.
- Variable Pre-Stretch: Maximizes film yield and ensures secure wrapping.
- Customizable Wrap Programs: Enables operators to set specific wrapping patterns (e.g., number of wraps, overlap percentage) for different panel types.
panel horizontal stretch wrapping machine Critical Safety Mechanisms in Orbital Wrappers
Safe operation is paramount. Look for robust safety features integrated into the machinery:
- Emergency Stop Buttons: Strategically placed for immediate machine halt by the operator in emergencies.
- Safety Fencing/Guards: Physical barriers preventing access to moving parts and the wrapping zone during operation.
- Light Curtains: Infrared safety barriers that detect intrusion into hazardous areas, triggering an immediate machine stop.
- Interlocked Access Doors/Guards: Switches ensuring the machine cannot operate if safety guards are open or improperly secured.
- Overload Protection: Systems designed to detect excessive film tension or mechanical strain, preventing damage to the machine or product.
- Process Monitoring: Features that may automatically stop the machine if a cycle isn't completed correctly or within a set time, preventing potential issues.
Regular inspection, maintenance, and operator training are crucial to ensure these safety systems function correctly and effectively protect personnel.
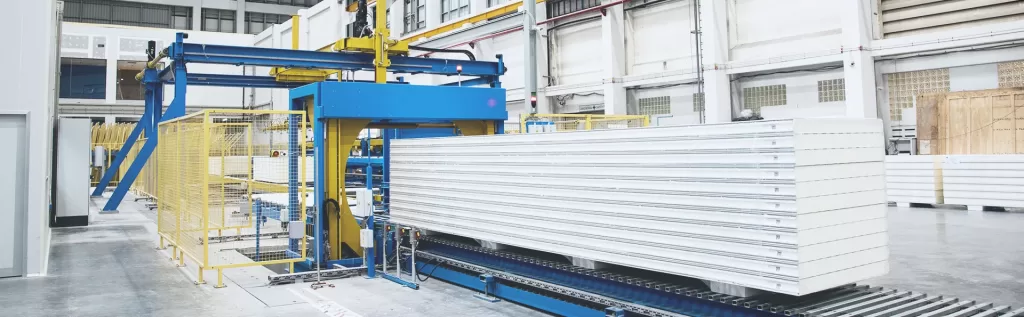
Conclusion
Automated orbital stretch wrapping presents a reliable and efficient solution for protecting sandwich panels throughout the supply chain. By ensuring load stability and shielding panels from environmental factors and handling damage, these systems contribute to reduced waste, lower costs, and improved product quality upon delivery. When selecting a system, carefully consider panel dimensions, throughput requirements, level of automation needed, and critically, the integration of comprehensive safety features.