Safety Hazards in Coil Handling and How to Avoid Accidents
- Safety Hazards in Coil Handling and How to Avoid Accidents
- 1. Understanding the Importance of Coil Safety
- 2. Common Safety Hazards in Coil Handling
- 3. The Role of Training in Preventing Accidents
- 4. Best Practices for Safe Coil Handling
- 5. Proper Storage and Stacking of Coils
- 6. The Impact of Automation in Coil Handling Safety
- 7. The Role of Personal Protective Equipment (PPE)
- 8. Emergency Preparedness in Coil Handling
- Conclusion
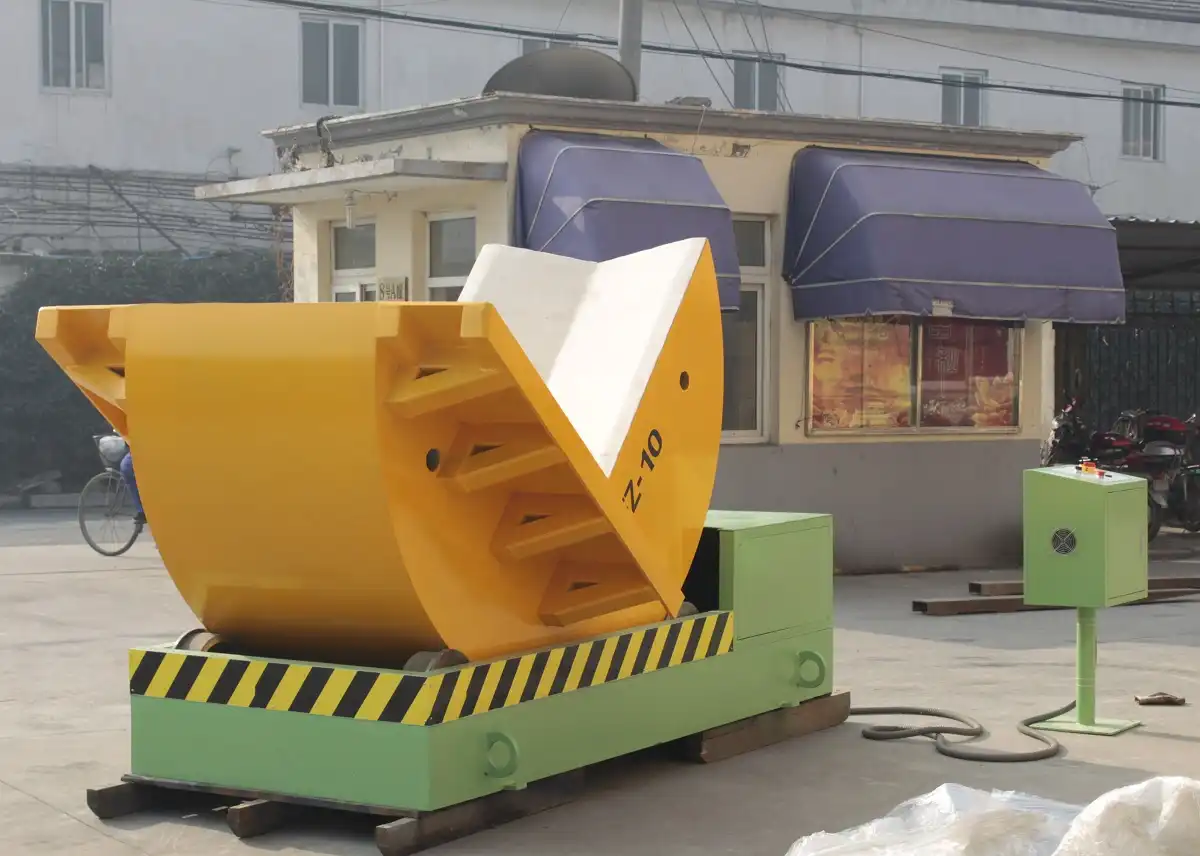
Handling coils in an industrial environment comes with its own set of inherent risks. Coils, whether they are steel, aluminum, or any other material, are typically heavy and require specialized equipment to transport them safely. Without proper handling procedures and equipment, the likelihood of accidents rises significantly. This article explores common safety hazards associated with coil handling and provides practical solutions to help minimize risks and avoid accidents. Ensuring the safety of your workforce should be a top priority, and understanding how to properly manage these hazards is the first step.
1. Understanding the Importance of Coil Safety
Industrial environments that deal with coil handling often face numerous challenges due to the sheer size, weight, and potential instability of coils. Whether it’s during the loading, unloading, or transporting of coils, employees are exposed to various safety hazards. Injuries and even fatalities can result from improper handling procedures, lack of training, or equipment malfunction.
The consequences of neglecting safety in coil handling can be severe. Not only do accidents lead to potential injuries or loss of life, but they can also cause significant operational delays, legal liabilities, and increased costs due to downtime and medical expenses. Thus, implementing proper safety measures is essential for both worker well-being and business efficiency.
2. Common Safety Hazards in Coil Handling
a) Falling Coils
One of the most prominent dangers is the risk of falling coils. Coils are often stacked in warehouses, and if they are not stored or transported correctly, there is a real possibility that they could topple over, leading to serious injury or death. Loose coils or improper stacking methods can amplify this risk, especially when multiple coils are stored in confined spaces.
b) Pinching and Crushing Injuries
Pinching and crushing are common injuries that occur when workers are in close proximity to the coils during handling or loading. These injuries typically occur when a coil slips from its grip or when a worker’s hand or foot becomes caught between the coil and another surface. The weight of the coil can lead to broken bones or more severe injuries.
c) Improper Lifting and Transporting
Coils require specialized equipment like coil upenders, cranes, and forklifts to move them safely. When workers are not properly trained to use this equipment or if faulty machinery is in play, the risks of accidents increase. The sudden dropping of a coil during transport, for example, can not only damage the product but also put workers at risk.
d) Coil Instability
Another hazard arises from the instability of the coils themselves. Due to their circular shape, coils can easily roll or shift if not properly secured. This creates an unpredictable and hazardous environment. If a coil starts to roll or move unexpectedly, workers could be caught off guard, leading to accidents.
e) Inadequate Equipment Maintenance
Using worn-out or malfunctioning equipment is another leading cause of accidents in coil handling. Regular inspections and timely maintenance of lifting equipment, such as cranes or coil upenders, are essential to ensure that they are in good working condition. Equipment failure mid-operation can lead to dropped coils or other dangerous situations.
3. The Role of Training in Preventing Accidents
Lack of proper training is a significant contributor to coil handling accidents. Workers who are unfamiliar with how to operate heavy machinery, such as forklifts or coil upenders, may make dangerous mistakes, like improperly lifting or transporting a coil.
Employers should invest in comprehensive safety training programs that cover the correct methods for handling coils, how to use the necessary equipment, and how to react in emergency situations. By ensuring that employees are well-versed in safety protocols, the risk of accidents can be significantly reduced.
4. Best Practices for Safe Coil Handling
a) Use of Proper Equipment
Investing in the right equipment is essential for safely handling coils. Coil upenders, coil grabs, and automated handling systems are designed to minimize human interaction with the coils, reducing the risk of accidents. Automated solutions not only increase efficiency but also drastically reduce the likelihood of human error during the handling process.
b) Regular Equipment Inspections
To prevent accidents related to equipment failure, regular inspection and maintenance are critical. All lifting devices and transport systems should be thoroughly checked for signs of wear and tear, malfunction, or defects. Implementing a preventive maintenance program ensures that equipment operates at peak performance and helps avoid unexpected breakdowns.
5. Proper Storage and Stacking of Coils
Safe storage practices are crucial to prevent accidents involving coils. Coils should be stacked in a way that ensures they remain stable and secure at all times. If coils are stacked too high or on uneven surfaces, they may roll or collapse, posing serious risks to nearby workers. Using safety wedges or coil racks can provide extra stability and help prevent unintended movement.
a) Implementing Safe Stacking Methods
Coils should always be stacked according to their size, weight, and material. For example, placing smaller coils on top of larger ones is risky as it can lead to uneven weight distribution and increase the chance of falling. Additionally, employees should be trained to recognize the appropriate height for stacking based on coil specifications to avoid accidents.
b) Clear Designation of Storage Areas
Marking and designating specific areas for coil storage can also help prevent accidents. This ensures that coils are stored in safe zones, away from heavy traffic areas where forklifts or other machinery operate. Establishing clear storage protocols also makes it easier for workers to handle the coils safely, reducing the risk of accidents due to cluttered or poorly organized workspaces.

6. The Impact of Automation in Coil Handling Safety
The introduction of automation technologies in coil handling has drastically reduced the number of accidents in many industries. Automated systems take over the most dangerous aspects of coil handling, such as lifting, rotating, and moving the coils, reducing the need for human intervention and minimizing the risk of injuries.
a) Automated Coil Handling Systems
Automated coil handling systems are designed to carry out the tasks that traditionally required manual labor, which are often the most dangerous aspects of the job. From automated cranes to robotic coil upenders, these systems allow coils to be moved safely without requiring workers to be in close proximity to the heavy loads. Automation also ensures consistency in handling, eliminating human error, which is a common cause of accidents.
b) Reducing Human Exposure to Hazards
By integrating automated systems into the coil handling process, human exposure to hazards is minimized. Workers no longer need to manually lift, push, or pull heavy coils, reducing the risk of strain injuries, crushed limbs, or worse. As automation continues to evolve, companies that invest in these technologies can see both safety improvements and operational efficiency gains.
7. The Role of Personal Protective Equipment (PPE)
Despite the implementation of automation and other safety measures, personal protective equipment (PPE) remains a vital component in preventing injuries. Workers should always wear the appropriate PPE when handling coils, including steel-toed boots, gloves, helmets, and protective eyewear.
a) Specific PPE for Coil Handling
In coil handling operations, the appropriate PPE should be determined by the specific risks associated with the job. For instance, workers involved in lifting or stacking should wear gloves to protect their hands from sharp edges or heavy impacts, while steel-toed boots can prevent foot injuries in case a coil drops unexpectedly. Hard hats and protective eyewear also help protect against head and facial injuries.
b) Ensuring Consistent Use of PPE
Simply providing PPE isn’t enough; employees must be trained on the correct usage and maintenance of their gear. Additionally, supervisors should enforce consistent PPE compliance to ensure that all workers are following the necessary safety protocols at all times. Regular checks and reminders can help foster a culture of safety within the workplace.
8. Emergency Preparedness in Coil Handling
Even with the best preventive measures in place, accidents can still happen. That's why it's essential for every workplace that handles coils to have an effective emergency response plan in place. Workers should know how to react swiftly and appropriately in the event of an accident, such as a falling coil or equipment malfunction.
a) Training for Emergency Situations
Regular safety drills and training sessions should be conducted to ensure all employees are familiar with emergency procedures. This includes knowing how to shut down equipment in the event of an emergency, how to administer first aid, and the proper procedures for reporting accidents.
b) First Aid and Immediate Response
In the event of an accident, immediate first aid can make a significant difference in the severity of injuries. Employers should ensure that first aid kits are readily available and that some employees are trained in basic first aid practices. Swift action can prevent minor injuries from becoming more serious and can save lives in the case of a severe accident.
Conclusion
Coil handling is a high-risk activity that requires diligent attention to safety protocols to avoid accidents and injuries. Understanding the common hazards, such as falling coils, improper equipment use, and inadequate training, is crucial in preventing these risks. By implementing automated handling systems, using appropriate personal protective equipment, conducting regular equipment inspections, and providing comprehensive safety training, employers can significantly reduce the dangers associated with coil handling.
Safety in coil handling isn’t just about following regulations—it's about creating a work environment where accidents are less likely to happen, and where employees feel confident that their well-being is being prioritized. Investing in the right technologies and procedures not only ensures a safer workplace but also leads to improved operational efficiency, fewer disruptions, and greater long-term success.