Safety and Efficiency Combined: The Role of Automated Steel Coil Packaging Systems
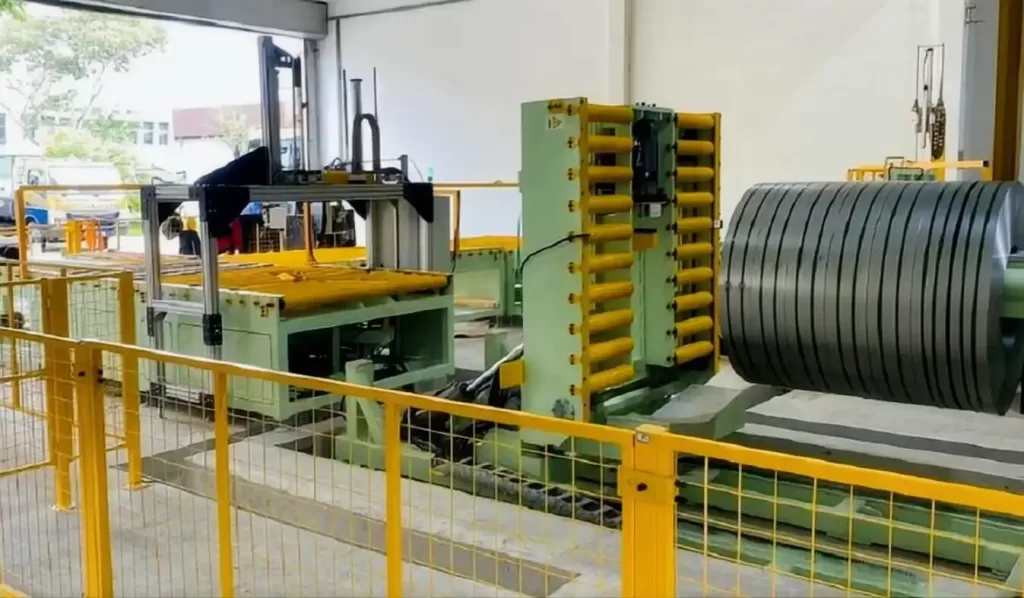
- Safety and Efficiency Combined: The Role of Automated Steel Coil Packaging Systems
- Introduction
- 1. The Importance of Automation in Steel Coil Packaging
- 2. Key Components of an Automated Steel Coil Packaging System
- 3. Safety Benefits of Automated Steel Coil Packaging
- 4. Enhanced Efficiency and Productivity in Packaging Operations
- 5. Cost Savings Through Reduced Labor and Maintenance
- 6. Advanced Technology for Improved Quality Control
- 7. Flexibility and Customization to Meet Unique Production Needs
- 8. The Role of Smart Sensors and IoT in Modern Packaging Systems
- 9. Reduced Environmental Impact through Optimized Resource Usage
- 10. Improving Workplace Safety and Compliance with Regulatory Standards
- 11. Evaluating the Return on Investment (ROI) of Automated Systems
- Conclusion
Introduction
In today’s competitive manufacturing landscape, automating steel coil packaging has become a necessity rather than a luxury. With industries prioritizing not only speed and cost-effectiveness but also workplace safety, the adoption of automated steel coil packaging systems has skyrocketed. These systems, designed to streamline the handling, wrapping, and storing of steel coils, have revolutionized the way companies operate, offering numerous benefits that enhance overall productivity and safety.
While traditional packaging systems required significant manual intervention, today’s automated systems leverage advanced robotics, smart sensors, and integrated control systems to reduce the risk of accidents and errors. But what exactly makes these systems so essential in modern steel coil packaging? How do they contribute to both safety and efficiency, and what features should businesses look for when investing in them? This article dives deep into the transformative role of automated steel coil packaging systems, unpacking their benefits, technology, and applications.
1. The Importance of Automation in Steel Coil Packaging
Automation in steel coil packaging is not just about speeding up operations; it’s about ensuring consistency, minimizing downtime, and enhancing safety standards. Steel coils are heavy, often weighing several tons, and manually packaging or moving them can lead to severe safety hazards. Automated systems mitigate these risks by taking over complex, repetitive tasks and enabling a smoother, error-free packaging process.
Beyond safety, automation also offers measurable improvements in efficiency. Automated packaging systems are often faster and more accurate than manual operations, ensuring that every coil is uniformly wrapped and prepared for shipping without delays. Additionally, these systems can be configured to perform various tasks, such as labeling, stacking, and wrapping, in a single cycle, saving both time and resources.
By reducing the need for manual intervention, automated systems also lower the risk of human error, which is a leading cause of workplace accidents and product damage. With a well-designed automated packaging solution, businesses can safeguard their workforce while improving operational efficiency—a win-win situation.
2. Key Components of an Automated Steel Coil Packaging System
Understanding the structure and components of automated steel coil packaging systems is essential for appreciating their capabilities. These systems generally consist of several main components, each playing a critical role in achieving smooth, secure packaging. The most common components include:
- Coil Handling Equipment: Responsible for lifting, rotating, and positioning coils, these machines eliminate the need for manual handling, reducing strain on workers and minimizing injury risks. Coil handling equipment is often designed to accommodate coils of various sizes, offering flexibility across different production requirements.
- Wrapping Machines: Wrapping machines ensure that coils are securely packaged, preventing potential damages during transit. With adjustable wrapping tension and multiple wrapping patterns, these machines cater to different coil sizes and protection requirements, ensuring that each product is ready for transport.
- Control Systems: Equipped with smart technology, control systems manage the entire operation, coordinating each component and ensuring they work in sync. These systems often feature user-friendly interfaces that allow operators to monitor and adjust the packaging process as needed, making it easier to detect and resolve issues in real-time.
- Safety Sensors and Alarms: Safety is a core component of automated systems, and safety sensors play a critical role in maintaining accident-free operations. These sensors can detect irregularities such as coil misalignment or equipment malfunction, alerting operators before a minor issue escalates into a major problem.
Each of these components is designed with both efficiency and safety in mind, enabling manufacturers to handle high-volume coil packaging while reducing the risk of mishaps.
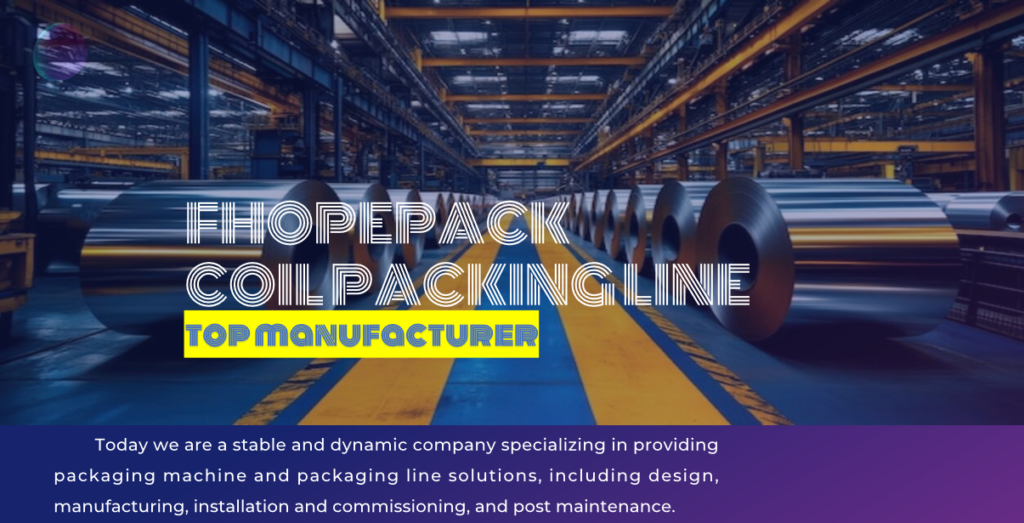
3. Safety Benefits of Automated Steel Coil Packaging
One of the most significant advantages of automated steel coil packaging systems is the improvement in workplace safety. Handling steel coils manually can be risky, with injuries ranging from strains and sprains to more severe incidents caused by coil slippage or equipment malfunction. Automated systems mitigate these risks by reducing the need for human interaction with heavy, potentially hazardous materials.
Automated systems come equipped with safety features like emergency stop buttons, safety guards, and fail-safes that prevent accidents and protect workers. In addition, by eliminating manual handling, these systems reduce repetitive strain injuries and lower the chances of human error. Safety sensors, such as proximity detectors and overload sensors, further enhance protection, ensuring that coils are packaged securely and without incident.
For businesses, the integration of automated systems means fewer workplace accidents, which can reduce downtime and the associated costs of injury claims and equipment repairs. Enhanced safety also leads to better employee morale and retention, as workers feel secure operating in a safe, well-regulated environment.
4. Enhanced Efficiency and Productivity in Packaging Operations
Automated steel coil packaging systems are designed to perform tasks more quickly and accurately than manual operations, resulting in substantial improvements in efficiency. By eliminating the need for manual intervention at multiple stages, these systems can handle high volumes of coils in less time, allowing businesses to meet tight deadlines and improve their output capacity.
Productivity gains from automation stem from several factors. First, automated systems work continuously without the fatigue or variability associated with human labor. This consistency reduces errors and optimizes cycle times, ensuring each coil is packaged to exact specifications. Second, these systems can be programmed to perform a series of operations in one go, including wrapping, labeling, and loading, streamlining the entire packaging process. The result is a highly efficient operation that enhances throughput while minimizing idle time and manual adjustments.
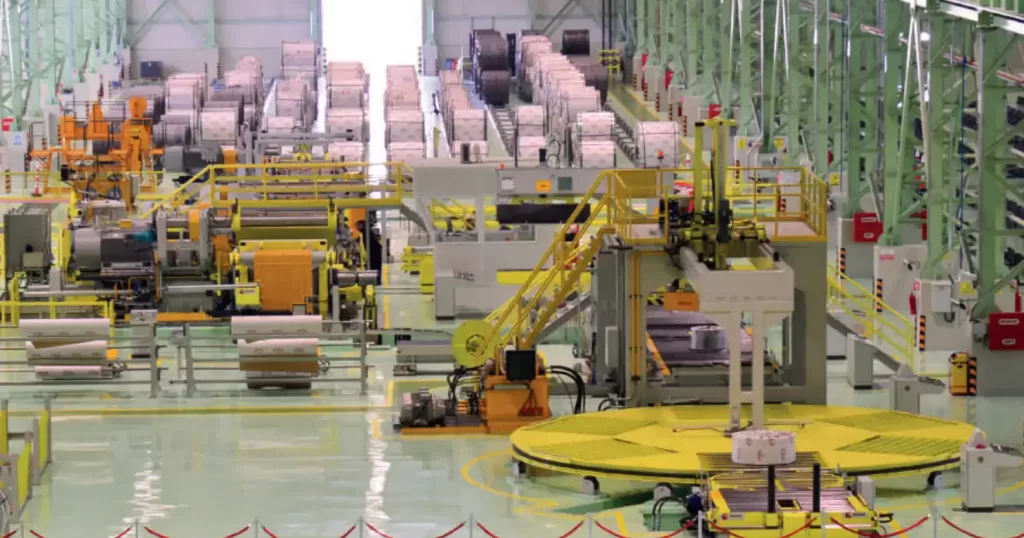
5. Cost Savings Through Reduced Labor and Maintenance
Another significant benefit of automated steel coil packaging systems is the potential for cost savings. While the initial investment in automation may seem substantial, the return on investment becomes evident through reduced labor costs and lower maintenance expenses over time. Automated systems take on repetitive and physically demanding tasks, reducing the need for a large manual workforce and allowing skilled workers to focus on more complex or strategic roles.
Additionally, automation minimizes wear and tear on equipment, as machines operate within optimal conditions set by the control systems, thereby reducing the frequency of repairs and extending the lifespan of each component. These systems also offer predictive maintenance capabilities, identifying minor issues before they escalate into costly repairs. By optimizing both labor and maintenance costs, automated systems prove to be a financially viable choice for businesses focused on long-term growth.

Get Your Best Solution !
6. Advanced Technology for Improved Quality Control
Quality control is crucial in steel coil packaging, as improperly packaged coils can suffer damage in transit, leading to product loss and customer dissatisfaction. Automated systems incorporate advanced technology to maintain high-quality standards throughout the packaging process. Features such as automated thickness measurements, weight verification, and alignment checks ensure that each coil is packaged according to precise specifications.
Some systems also include real-time monitoring and data collection, allowing operators to track packaging quality metrics and adjust settings on the go. This data-driven approach to quality control enables manufacturers to maintain consistency and identify potential issues before they impact production. With automated systems, businesses can confidently deliver coils that meet high-quality standards, resulting in stronger customer relationships and fewer returns.
7. Flexibility and Customization to Meet Unique Production Needs
One of the most appealing aspects of modern automated steel coil packaging systems is their flexibility and customization options. Businesses often deal with a variety of coil sizes, shapes, and material types, each requiring specific packaging methods to ensure safe transport and storage. Automated systems are designed to accommodate these varying requirements, providing options for customizable wrapping patterns, adjustable tension controls, and tailored coil handling mechanisms.
Advanced models also offer modular designs that allow manufacturers to add or modify components based on changing production demands. This scalability ensures that as businesses grow, their packaging systems can evolve to meet new challenges without the need for extensive reinvestment. This adaptability makes automated systems a smart choice for companies looking to maintain operational flexibility and stay competitive in a dynamic market.
8. The Role of Smart Sensors and IoT in Modern Packaging Systems
The rise of the Internet of Things (IoT) has revolutionized the way manufacturers approach automation, and steel coil packaging is no exception. Modern automated systems are equipped with smart sensors and IoT capabilities that allow real-time monitoring, predictive maintenance, and improved process control. These sensors collect data on various aspects of the packaging process, including coil alignment, machine wear, and environmental conditions.
With IoT integration, operators can access this data remotely, enabling them to oversee packaging operations from any location. The data collected by these sensors can also be analyzed to improve process efficiency, reduce waste, and enhance product quality. This level of connectivity brings significant advantages in terms of both productivity and operational transparency, empowering manufacturers to make data-driven decisions that positively impact their bottom line.
9. Reduced Environmental Impact through Optimized Resource Usage
Sustainability is becoming increasingly important in the manufacturing sector, and automated steel coil packaging systems can contribute to a business’s environmental goals. By using precise amounts of packaging materials and minimizing waste, automated systems reduce the environmental footprint of packaging operations. Features like adjustable wrapping tension allow manufacturers to use just the right amount of materials needed to secure each coil, avoiding excess plastic or metal banding.
In addition, some systems are designed to work efficiently with recyclable or biodegradable materials, making it easier for companies to adopt eco-friendly practices. With fewer resources consumed and waste minimized, automated packaging aligns with sustainable manufacturing practices, making it an ideal solution for companies committed to reducing their environmental impact.
10. Improving Workplace Safety and Compliance with Regulatory Standards
Safety regulations in industrial environments are stringent, and compliance is critical to avoid fines and protect workers. Automated steel coil packaging systems are engineered with safety and compliance in mind, incorporating features that ensure adherence to local and international safety standards. These systems typically include safety barriers, emergency stop buttons, and clear operational guidelines to safeguard operators.
Additionally, automated systems reduce the likelihood of injuries related to manual handling, lifting, and repetitive strain, which are common in manual packaging setups. Compliance with safety standards is not only a legal obligation but also a way to foster a safer workplace culture, which in turn leads to higher employee satisfaction and productivity. Automated systems thus serve as a comprehensive solution for companies aiming to enhance safety and meet regulatory requirements.
11. Evaluating the Return on Investment (ROI) of Automated Systems
Investing in an automated steel coil packaging system is a major decision, and understanding the potential return on investment (ROI) is essential. By reducing labor costs, minimizing downtime, and improving product quality, these systems often pay for themselves within a few years. Calculating ROI involves considering factors like reduced accident rates, maintenance savings, and increased productivity, all of which contribute to a stronger bottom line.
Manufacturers can also measure the impact of automation on customer satisfaction and retention, as high-quality packaging leads to fewer damaged products and improved brand reputation. With a clear understanding of the financial benefits, businesses can make informed decisions about integrating automated systems into their operations, recognizing both short-term gains and long-term value.
Conclusion
Incorporating automated steel coil packaging systems into production lines offers a dual advantage: enhanced safety and operational efficiency. These systems, equipped with advanced technology and robust safety features, reduce the risks associated with manual coil handling while significantly boosting productivity. By lowering labor and maintenance costs, improving quality control, and supporting sustainability goals, automation provides a competitive edge in today’s manufacturing industry.
For businesses seeking to modernize their operations, investing in automated packaging systems is a strategic choice that not only safeguards employees but also strengthens the overall production process. As technology continues to evolve, automated systems will only become more sophisticated, ensuring that manufacturers remain agile, efficient, and ahead of the curve in an ever-competitive marketplace.

Get Your Best Solution !