Problems in the Coil Packing Line and How to Avoid Them
In modern manufacturing, the coil packing line plays a crucial role in ensuring the integrity and quality of coiled products, such as wires, cables, and metal sheets. A well-functioning coil packing line maintains product safety during transport and storage, reduces waste, and upholds the company's reputation. Despite the adoption of automation in these processes, several issues frequently arise in coil packing that can lead to product damage, wasted resources, and operational inefficiencies. Identifying these common problems and implementing strategies to avoid them is essential for optimizing productivity and maintaining high-quality standards.
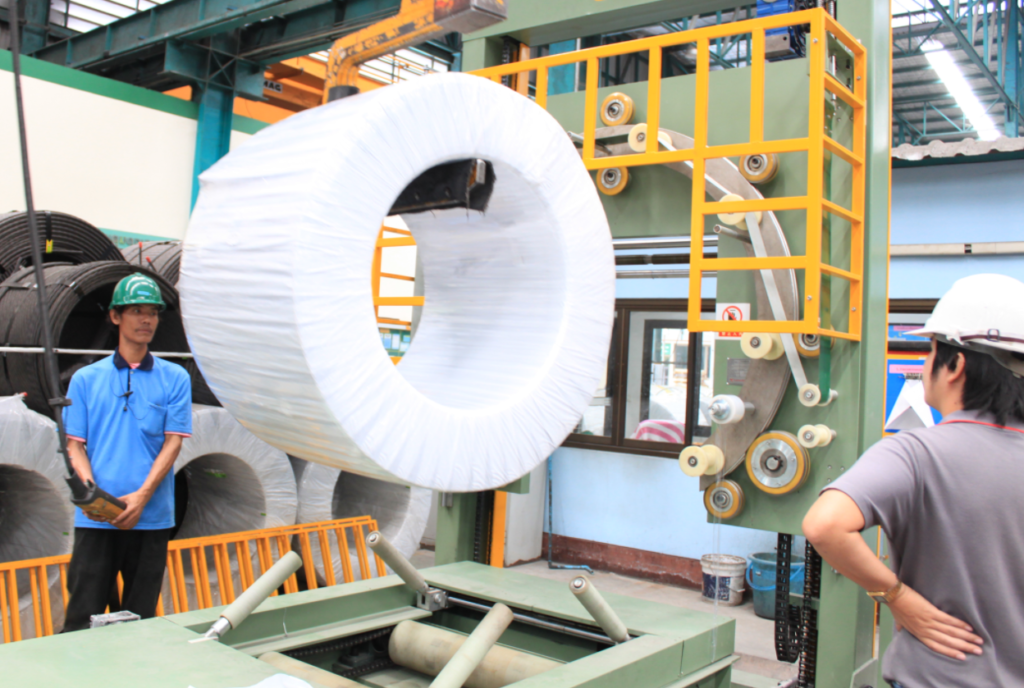
This article will discuss the common issues encountered in coil packing lines, analyze the causes, and propose targeted solutions to improve both the quality of packaging and the efficiency of production.
1. Misalignment and Overlapping of Coils
1.1 Problem Description
Coils may become misaligned or overlap during the packing process due to conveyor vibrations, inaccurate control of mechanical arms, or insufficiently spaced product handling. Misaligned or overlapping coils can lead to several complications, including:
- Increased friction between coils, which can damage the product’s outer surface.
- Inefficient use of packaging materials, leading to increased costs.
- Reduced stability during transport, which raises the risk of shifting or damage.
1.2 Causes
Misalignment often arises from inconsistencies in conveyor speed, inaccurate settings in automated handling systems, or improper initial alignment when loading the coil onto the packing line.
1.3 Solutions
To prevent coil misalignment:
- Ensure conveyor belts operate at a consistent speed, reducing the chances of coil shifting.
- Regularly calibrate and maintain automated systems to improve precision.
- Implement a check system that aligns coils correctly at the start of the line.
2. Insufficient Wrapping Tension
2.1 Problem Description
Proper wrapping tension is essential to ensure that coils are securely packaged. Insufficient tension can result in loose packaging, which not only looks unprofessional but also fails to protect the product adequately. Loose wrapping can cause coils to shift, increasing the risk of tangling or damage.
2.2 Causes
Several factors can lead to insufficient tension, including:
- Mechanical malfunctions in tension control equipment.
- Incorrect settings in wrapping machinery.
- Variations in coil size that are not accounted for in the wrapping process.
2.3 Solutions
To maintain optimal wrapping tension:
- Conduct regular maintenance and calibration of tension control mechanisms.
- Adjust wrapping machine settings to accommodate coil size variations.
- Integrate a real-time feedback system to monitor and adjust tension as necessary.
3. Inadequate Edge Protection
3.1 Problem Description
Edges of coils are often vulnerable to damage, especially during transportation. Inadequate edge protection can result in deformations, scratches, or even complete damage to the outer layers of the coil, which affects the product’s functionality and appearance.
3.2 Causes
Edge protection issues usually stem from:
- The use of insufficient protective materials around the coil’s edges.
- Improper placement of protective padding during packaging.
- A lack of standardization in edge protection procedures across batches.
3.3 Solutions
To improve edge protection:
- Use specialized padding materials designed for coil edges.
- Standardize edge protection procedures and conduct regular training for operators.
- Implement sensors to check edge protection placement before final wrapping.
4. Excessive Material Usage
4.1 Problem Description
Overuse of packaging materials not only increases costs but also contributes to waste, contradicting sustainability goals. Using excessive wrapping, padding, or securing materials can be common if the packing line is not calibrated to each coil's dimensions or specific requirements.
4.2 Causes
Material overuse often results from:
- Lack of accurate measurement systems for each coil’s dimensions.
- Inflexible packaging systems that apply a one-size-fits-all approach.
- Poorly configured automation software that doesn't optimize material usage.
4.3 Solutions
To minimize material waste:
- Introduce automated measurement systems that adjust material usage based on each coil’s size.
- Update software algorithms to dynamically assess and apply the right amount of materials.
- Implement a continuous improvement process to regularly assess material use and make adjustments.
5. Inconsistent Labeling and Marking
5.1 Problem Description
Clear and accurate labeling is essential for tracking and logistics. Inconsistent or incorrect labeling can lead to identification issues, resulting in shipping delays or errors and impacting inventory management.
5.2 Causes
Labeling issues may arise due to:
- Printer malfunctions or ink supply issues.
- Errors in automated labeling software or data input.
- Failure to inspect labels for accuracy and readability.
5.3 Solutions
To ensure accurate labeling:
- Schedule regular maintenance and calibration for printing and labeling equipment.
- Integrate quality control checks for label readability and accuracy.
- Implement automated scanning systems to verify each label before final packing.
Conclusion
Addressing common problems in the coil packing line is crucial for maintaining product quality, reducing costs, and ensuring operational efficiency. By focusing on issues such as coil alignment, wrapping tension, edge protection, material usage, and labeling, manufacturers can minimize damage, waste, and errors, ultimately enhancing their product quality and market reputation. Employing regular maintenance, automated monitoring systems, and standardizing procedures are effective ways to avoid these problems and improve the overall performance of the coil packing line.