Pick an Orbital Wrapping Machine That's Simple and Safe
When it comes to industrial packaging, choosing the right orbital wrapping machine is critical not only for operational efficiency but fundamentally for the safety and well-being of your workforce. Manually wrapping large, heavy, or irregularly shaped products is often slow and poses significant ergonomic risks, potentially leading to costly injuries and operational delays. The ideal orbital wrapping machine simplifies the packaging workflow while integrating robust safety features to protect operators.
This guide delves into the essential factors for selecting an orbital wrapping machine that balances simplicity with safety. We'll explore features contributing to ease of use and the safety mechanisms crucial for minimizing workplace hazards. A well-chosen machine boosts productivity and significantly reduces risk, representing a sound investment for any manufacturing or distribution operation.
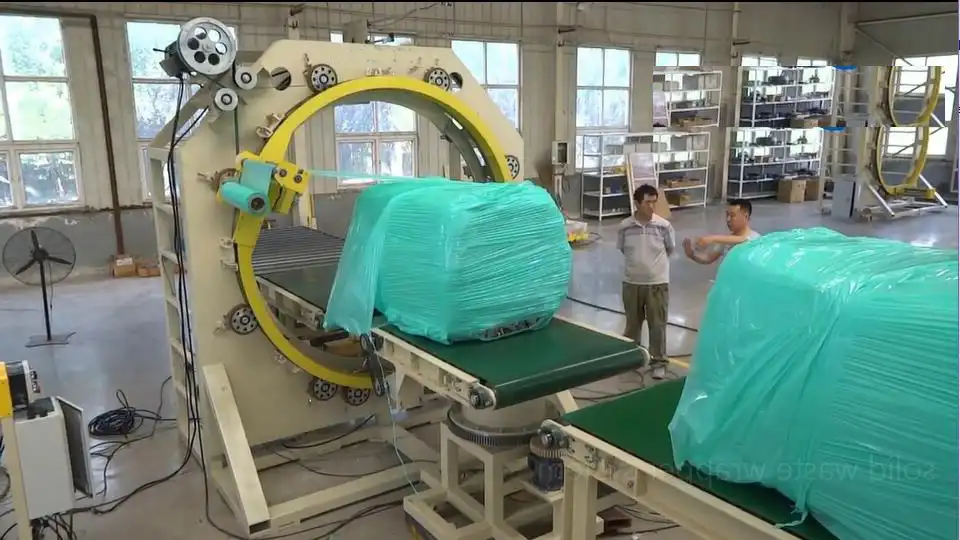
1. Prioritizing Safety in Orbital Wrapping Machine Selection
Safety must be the foremost consideration when evaluating orbital wrapping machinery. Workplace injuries can lead to significant downtime, disrupt operations, and incur substantial direct and indirect costs, including medical expenses and potential increases in insurance premiums. Packaging environments, particularly those involving manual handling of heavy loads, repetitive motions like bending and stretching, or monotonous tasks, are prone to accidents. An effective orbital wrapping machine mitigates many of these risks by automating the wrapping process and incorporating essential safety measures.
A. Preventing Injuries Associated with Manual Wrapping
Manual stretch wrapping exposes workers to numerous hazards. Frequent lifting and maneuvering of heavy products, adopting awkward postures (bending, twisting, reaching), and performing repetitive motions significantly increase the risk of musculoskeletal disorders (MSDs). According to the Occupational Safety and Health Administration (OSHA), MSDs are among the most frequently reported causes of lost work time. Automation via orbital wrappers dramatically reduces these physical demands, safeguarding employees from strains and long-term injuries.
B. Understanding the True Cost of Workplace Injuries
Beyond the immediate human impact, workplace injuries impose a heavy financial burden. Costs extend beyond medical treatment and lost wages to include decreased productivity, potential regulatory fines, and damage to employee morale. Investing in a safe orbital wrapping machine is a proactive measure to mitigate these financial and operational risks, fostering a safer and more productive work environment.
2. Identifying Common Risks in Manual Wrapping Processes
Businesses still relying on manual wrapping methods must acknowledge the inherent ergonomic challenges and injury risks.
A. Handling Heavy or Awkward Loads
Manually moving and rotating heavy or bulky items for wrapping places considerable strain on workers' backs, shoulders, and legs, even with proper lifting techniques. An automated orbital wrapping machine eliminates this manual handling requirement for the wrapping phase, managing heavy items safely and consistently.
B. Working in Awkward Postures
Stretching high, bending low, or twisting repeatedly to apply film manually forces workers into ergonomically unsound positions. This is particularly problematic with large or irregularly shaped products. Over time, these postures can lead to chronic pain and debilitating injuries.
C. Performing Repetitive Motions
The repetitive nature of hand-wrapping—pulling film, walking around the load—can cause repetitive strain injuries (RSIs), such as tendonitis or carpal tunnel syndrome. These conditions affect wrists, elbows, and shoulders, impairing a worker's ability to perform tasks and potentially leading to long-term disability if not addressed.
3. How Orbital Wrapping Machines Enhance Workplace Safety
Modern orbital wrapping machines directly address and eliminate many hazards associated with manual wrapping, creating a significantly safer operational environment.
A. Automation Eliminates Hazardous Manual Tasks
By automating the core wrapping process, these machines remove the need for operators to manually lift heavy film rolls, bend, stretch, or walk backward around loads. The machine consistently applies the film with minimal physical input from the operator, drastically reducing exposure to ergonomic risks.
B. Reducing Physical Strain and Fatigue
Orbital wrappers bear the physical burden of tensioning and applying stretch film. Operators are primarily responsible for initiating the cycle and overseeing the process, rather than exerting significant physical effort. This reduction in physical demand minimizes fatigue and dramatically lowers the incidence of MSDs.
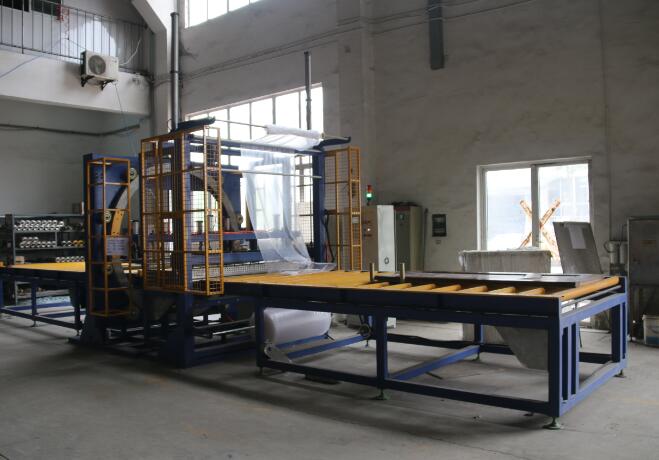
4. Essential Safety Features in Modern Wrapping Machines
When evaluating an orbital wrapping machine, prioritize models equipped with comprehensive safety features designed to protect operators during operation and maintenance.
A. Safety Sensors, Light Curtains, and Guarding
Look for machines equipped with:
- Safety Sensors/Light Curtains: These detect intrusions into the machine's operating envelope. If an operator or object breaks the light beam or enters a monitored zone, the machine immediately stops, preventing contact with moving parts.
- Physical Guarding: Interlocked perimeter guards or cages prevent access to potentially hazardous areas (like the rotating ring or film carriage) during operation. Opening a gate typically triggers an immediate machine stop.
B. Emergency Stop Buttons (E-Stops)
Clearly marked and easily accessible emergency stop buttons are crucial. These allow operators to halt all machine motion instantly in case of a malfunction, entanglement, or other unforeseen emergency, preventing or mitigating injury. Multiple E-stops should be strategically located around the machine.
C. Controlled Film Tension and Safe Film Carriage Design
- Automatic Film Tension Control: Systems that automatically regulate film tension prevent over-stretching (which can cause film breaks, potentially snapping back at operators) or under-stretching (leading to unstable loads). Consistent, controlled tension ensures load stability and operator safety.
- Safe Film Loading/Threading: The film carriage design should facilitate safe and easy loading of heavy film rolls. Features like ergonomic roll loading heights and simplified film threading paths minimize strain and potential pinch points.
5. The Significance of a Simple and User-Friendly Interface
Beyond physical safety features, operational simplicity is key to preventing errors and ensuring the machine is used correctly and efficiently.
A. Intuitive Control Panels
A machine with a straightforward control panel, often featuring a touchscreen interface (HMI), is essential. Look for:
- Clear Labels and Graphics: Functions should be clearly identified.
- Logical Menu Navigation: Adjusting parameters or selecting programs should be intuitive.
- Diagnostic Feedback: Clear error messages and troubleshooting guidance help operators resolve issues quickly and safely.
B. Easy Loading and Setup Procedures
The process for loading packaging materials (stretch film) should be simple, quick, and require minimal physical effort or tools. Complicated procedures increase downtime, operator frustration, and the potential for errors or unsafe workarounds. Quick-change film carriages are a valuable feature.
6. Flexibility: Adapting to Various Package Sizes and Shapes
A truly useful orbital wrapper must accommodate the range of products your facility handles. Versatility simplifies operations by reducing the need for multiple machines or complex changeovers.
A. Adjustable Parameters for Diverse Loads
Effective machines offer easily adjustable settings to handle variations in product dimensions (length, width, height) and weight. Key adjustable parameters include:
- Ring rotation speed
- Conveyor speed
- Film tension levels
- Number of wraps (top, bottom, middle)
- Film overlap percentage
B. Capability for Irregularly Shaped Items
Many industries (e.g., furniture, windows/doors, lumber, extrusions) deal with products that are long, non-uniform, or lack flat surfaces. An orbital wrapper designed to secure such items effectively—often using specialized clamping or support systems—is crucial for these applications. Ensure the machine can create a stable, protective wrap around your specific product types.
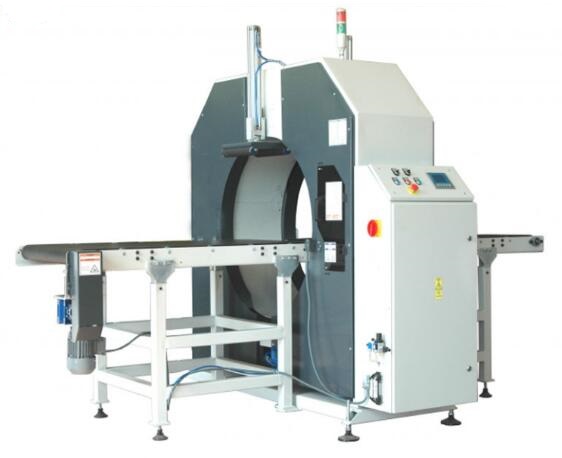
7. Why Simple Programming is Essential for Efficiency
Complex programming requirements can negate the benefits of automation, leading to errors, slow changeovers, and underutilization of the machine's capabilities.
A. Minimizing Complex Setup Requirements
Look for machines offering:
- Pre-programmed Recipes/Settings: The ability to save and recall specific wrapping parameters for different products drastically speeds up changeovers and ensures consistency.
- User-Friendly Interfaces: As mentioned earlier, intuitive controls allow operators to make necessary adjustments quickly without needing specialized programming skills or extensive training manuals.
B. Enabling Quick Adjustments and Customization
While pre-set programs are valuable, the machine should also allow for easy on-the-fly adjustments. Operators need the flexibility to fine-tune settings like film tension or wrap counts based on specific load requirements or observations, without navigating complex programming menus.
8. Operational Benefits of a Simple and Safe Wrapping Machine
Investing in an orbital wrapper that excels in both simplicity and safety yields significant operational advantages beyond injury prevention.
A. Increased Productivity and Throughput
User-friendly machines with quick setup and reliable operation minimize downtime and maximize output. Automation allows for faster wrapping cycles compared to manual methods, increasing overall packaging line throughput. Reduced operator intervention means personnel can often manage other tasks simultaneously.
B. Enhanced Packaging Consistency and Load Integrity
Automated wrapping ensures every load receives the same programmed wrap pattern and film tension. This consistency improves load containment and stability, reducing the risk of product damage during handling and transit compared to the inherent variability of manual wrapping. This can lead to fewer customer complaints and returns.
C. Reduced Workplace Stress and Improved Morale
Providing equipment that is safe and easy to use reduces physical and mental stress on employees. Knowing they are protected from common hazards and can operate the machinery competently boosts confidence and job satisfaction, contributing to better employee retention and a more positive work culture.
Conclusion: Invest in Simplicity and Safety for Optimal Performance
When selecting an orbital wrapping machine, prioritize both simplicity of operation and robust safety features. The ideal machine automates demanding and hazardous wrapping tasks, significantly reducing the risk of workplace injuries while boosting overall productivity. Look for intuitive controls, essential safety mechanisms like sensors and guarding, easy material handling, and the flexibility to accommodate your specific product range. Simple programming and adjustable settings ensure the machine remains efficient across various tasks.
Ultimately, investing in an orbital wrapping machine designed with both the operator and the operation in mind saves time, reduces costs associated with injuries and inefficiencies, and fosters a safer, more productive work environment.