Automated Panel Shrinking and Packaging: Optimizing Efficiency and Protection
Panel shrinking and packaging machines are crucial components in modern manufacturing, ensuring the safe and efficient handling of materials like EPS boards, sandwich panels, and MDF boards. This guide will explore the mechanics, benefits, and technical considerations of automated panel shrinking machines, specifically focusing on how they enhance productivity and minimize costs.
This automatic panel shrinking machine streamlines the process of bundling and packing various types of boards. It bundles boards of uniform size, seals, and wraps them, often on multiple sides, to provide comprehensive protection. The wrapped bundles are then placed on pallets, ready for storage and shipping.

Key Features and Technical Specifications
Automated panel shrinking machines offer a range of features designed to optimize performance and flexibility:
- Board Size Variability: Capable of handling boards ranging from 600x1200mm to 3200x20000mm, with thicknesses from 10mm to 100mm. This adaptability allows for use across diverse product lines.
- Adjustable Bundling: Utilizes adjustable straps and stretch film to accommodate boards of different dimensions, ensuring consistent bundle sizes. The tension of the straps is generally controlled by a pneumatic system, offering precise adjustment.
- Sealing and Wrapping Options: Provides options for side sealing, partial wrapping, and full wrapping, tailored to specific product requirements. Some advanced machines use servo-driven film dispensers for ultra-precise wrapping control.
- Sealing Mechanism: Employs hot melt adhesive for sealing and stretch film for wrapping, offering secure and durable packaging. The hot melt adhesive system typically includes a temperature controller maintaining adhesive viscosity and bond strength.
- Control System: Features a PLC (Programmable Logic Controller) to automate sequencing, tension control, and cutting operations. These systems often incorporate HMI (Human Machine Interface) touchscreens for intuitive parameter adjustments and diagnostics.
- Safety Features: Equipped with safety mechanisms such as light curtains, emergency stop buttons, and overload sensors to prevent injuries. Light curtains typically use infrared beams to detect obstructions, and emergency buttons are hard-wired to immediately halt machine operation.
- Construction: Designed with robust materials and construction to withstand continuous operation in manufacturing environments. Frame materials are often high-strength steel profiles, and moving components are equipped with durable bearings and linear guides.
- Bundle Settings: Allows for adjustable settings to control the number of boards per bundle and the tightness of the bundle, optimizing bundle size and stability. The formula to approximate bundle tightness would be:
Bundle Tightness Index = (Bundle Circumference / Number of Boards) / Board Thickness
This index helps in optimizing the tightness for different dimensions of boards.
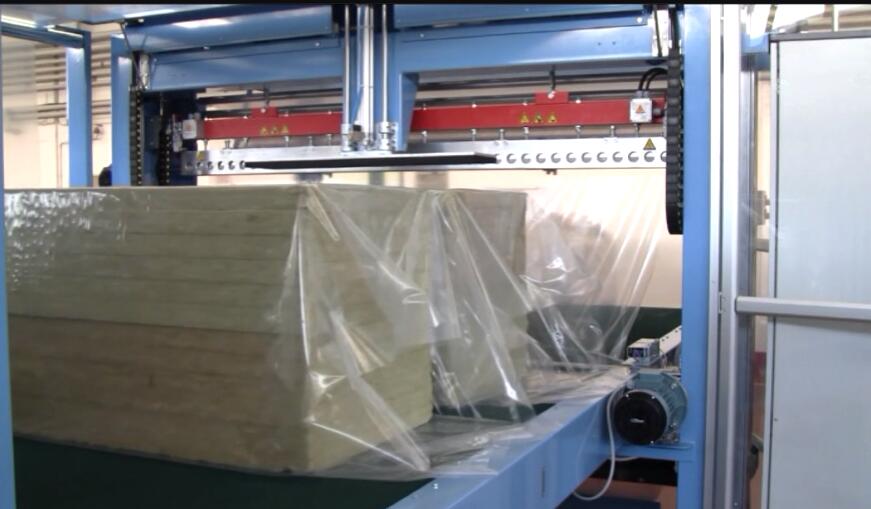
Benefits of Automation
Implementing an automated panel shrinking machine offers numerous advantages:
- Increased Throughput: Automates and accelerates the bundling and packing process, significantly surpassing the output of manual operations. Some high-speed lines can process over 50 tons of boards per day.
- Consistent Quality: Ensures uniform bundle size, quality, and reliable shrinkage, guaranteeing safe storage and transportation. Servo-controlled film tensioners maintain consistent film application, reducing material waste and improving package aesthetics.
- Improved Safety: Reduces the risk of workplace injuries by eliminating manual handling of hot melt adhesives and sharp board edges. Enclosed machine designs and safety interlocks further minimize potential hazards.
- Cost Reduction: Optimizes the use of adhesives, straps, and stretch film, minimizing material costs. Programmable logic controllers precisely control material consumption, and real-time monitoring can identify areas for further optimization.
- Waste Reduction: Minimizes product damage during bundling and transportation, decreasing waste and associated costs. Proper tension and wrapping techniques prevent board shifting and edge damage.
- Reduced Labor Costs: Requires only one operator to monitor multiple machines, decreasing labor expenses. Integrated diagnostic systems and remote monitoring capabilities further reduce downtime and maintenance costs.
- Enhanced Productivity: Boosts overall production volume and profitability while lowering operating costs. Increased throughput translates to faster order fulfillment and improved customer satisfaction.
- Customization: Provides bespoke bundling solutions tailored to specific customer requirements for diverse board types. Flexible machine configurations and software options allow for adapting to changing production demands.
- Brand Enhancement: Promotes a positive brand image through high-quality, damage-free products, and timely deliveries. Professional packaging reinforces product quality and contributes to customer loyalty.
Machine Mechanics and Functional Implementation
The operational efficiency of panel shrinking machines arises from a combination of mechanical and digital systems working in concert.
- Infeed Conveyor System: The board is propelled to the wrapping part through an infeed which contains a conveyor system driven by a variable speed motor. This regulates throughput.
- Wrapping Module: This module uses a stretch film dispenser with the servomotor managing the constant film wrapping on the group of boards. The tension control of the film is important to sustain the package integrity and is regulated by the programmable logic controller.
- Sealing Mechanism: The hot melt adhesive system is responsible for sealing. It is a closed-loop configuration that keeps track of temperature to maintain the viscosity levels while sustaining the ideal bond strength.
- Cutting System: Integrated into the machine is an automatic cutting device that uses either a hot wire or a mechanical blade to cut out the stretch film after the wrapping. Servo or pneumatic devices usually drive the system for clean cuts to enhance the packing appearance.
- Outfeed and Palletizing: Bundled wrapped boards are propelled from one wrapping station to an output where an automated palletizing system will ensure that boards are positioned strategically onto the pallet for storage and shipping.
Conclusion
Automated panel shrinking machines represent a vital investment for manufacturers seeking to optimize resources, minimize costs, improve product quality, and prioritize workplace safety. By automating the bundling and packing process, these machines deliver a tangible return on investment and contribute to a more efficient and profitable operation. Such a solution is essential for businesses striving for high performance, strong partnerships, and sustained profitability.